I say 'infill'.... :roll:
I got an old stanley 110 in a job lot a while back. I think it's a stanley 110 at least. It was in a bit of a state. While a lot of the other bits went into the rust bucket and got cleaned up for some reason I chucked this one on the desk next to my pc and there it sat for a while. Then one night, some months back, I found I found a well known thread (I won't name it because it doesn't deserve to be dragged down in any sense to be associated with anything I can manage) on here about making a proper infill plane. About two hours later and full of the naive hope of the beginner, immune to the rough edges of experience I glanced down. My eyes settled on the 110.
The rest is obvious I suppose.
Yeeeees. I can hear you laughing at the back...
Onwards and upwards.
After a dip and a clean.
Now, here was my first mistake. I set about undercoating and painting it although I only actually wanted a tiny section above the mouth to be painted eventually. Bear with me.
Live and learn. :|
I started cutting the wooden bits. To save time I cut them from a 5" block of mahogany on my top of the range Evolution chop saw. I then spent about a day trying to get the cuts squared off.... Lesson learned, again. You can hide a few mm out of square on a window sill. Not when the wood has to be cut this accurately. So the chop saw was shouted at and demoted and lost all shore leave. That'll teach me for not having more faith in my handsawing abilities.
Measuring the angle from the mouth to bed the wood in correctly was done by wizardry and jiggerypokery. And a little bit of luck.
I cut the rear bit off to fit then drilled holes by hand with forstner bits (thankyou Benjamin!), the plan is 1, they will provide stability for the gluing of the handles and 2, i'm possibly planning on laying in a thread and a brass screw of some variety. To hold stuff in place, but also for looks and razzle dazzle. 8)
Tons more work to do and loads of ways that I might still mess everything up.
So. The real reason for posting.
I had a sudden thought that I need to get the blade now before I do any more work trying to fettle it all up. That way I can work with real error margins.
I think its a 1 5/8" blade. I was planning on a QS workshop Heaven blade originally. But it seems that's not available. Hock, Clifton and Veritas all do the right dimension blades. But of course they are all super pricey. Any ideas? I'm mostly after an off the shelf solution though perhaps cutting down a thicker wood iron is not out of the question.
Also and more importantly (in fact the whole reason for this post), I want to shape a brass lever cap to wedge under the bar to secure the iron. (I'm nowhere near being able to drill pivot pins etc). Would the lever cap/screw be man enough to hold the iron in place without some form of wedging? Chip breaker? If it's a 3mm blade? I think I might be able to shape the lever cap to act as a chipbreaker. Any ideas?!?
I'd be grateful for any knowledge you can throw this way.
Cheers as always
Chris
I got an old stanley 110 in a job lot a while back. I think it's a stanley 110 at least. It was in a bit of a state. While a lot of the other bits went into the rust bucket and got cleaned up for some reason I chucked this one on the desk next to my pc and there it sat for a while. Then one night, some months back, I found I found a well known thread (I won't name it because it doesn't deserve to be dragged down in any sense to be associated with anything I can manage) on here about making a proper infill plane. About two hours later and full of the naive hope of the beginner, immune to the rough edges of experience I glanced down. My eyes settled on the 110.
The rest is obvious I suppose.
Yeeeees. I can hear you laughing at the back...
Onwards and upwards.
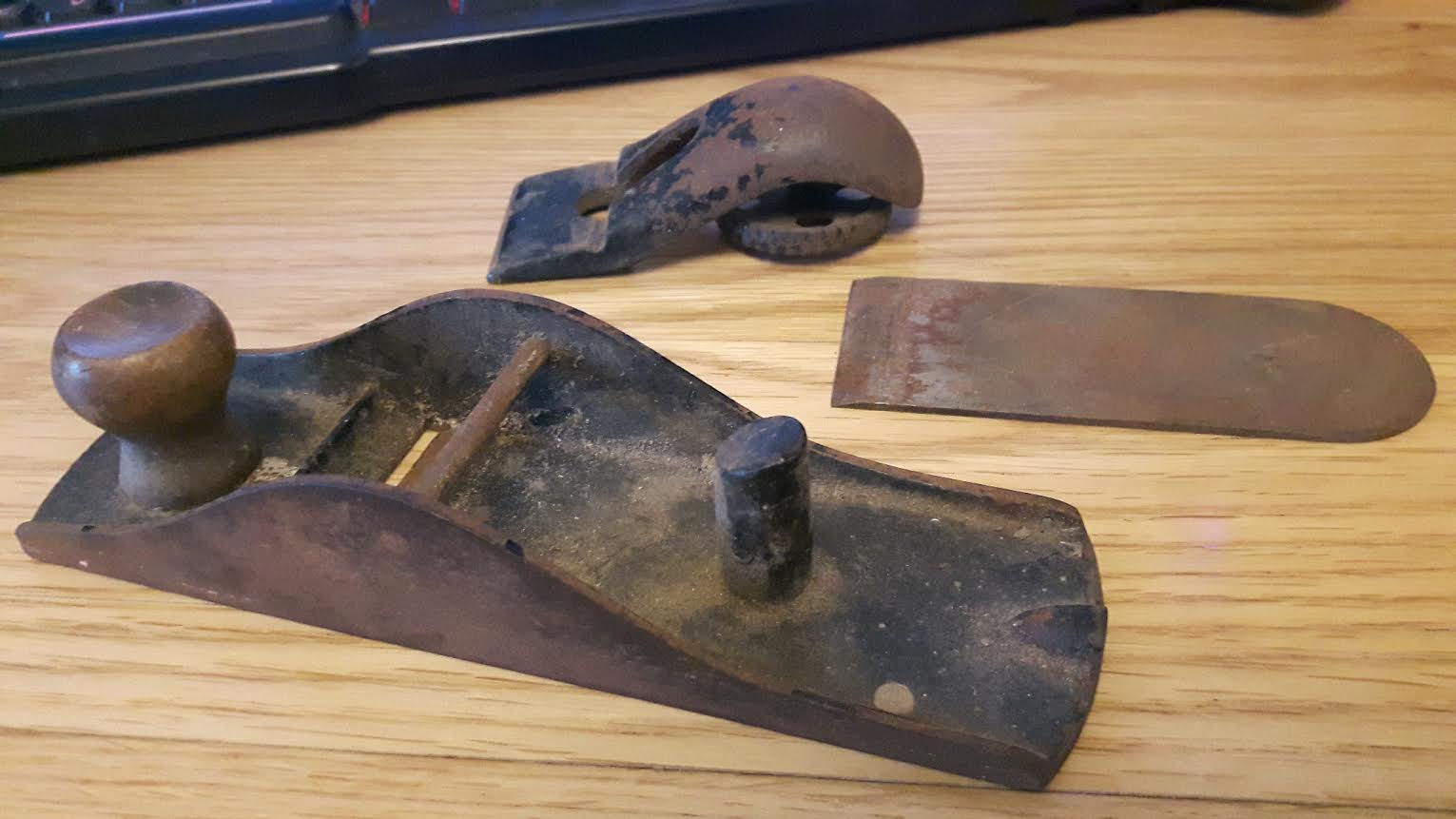
After a dip and a clean.
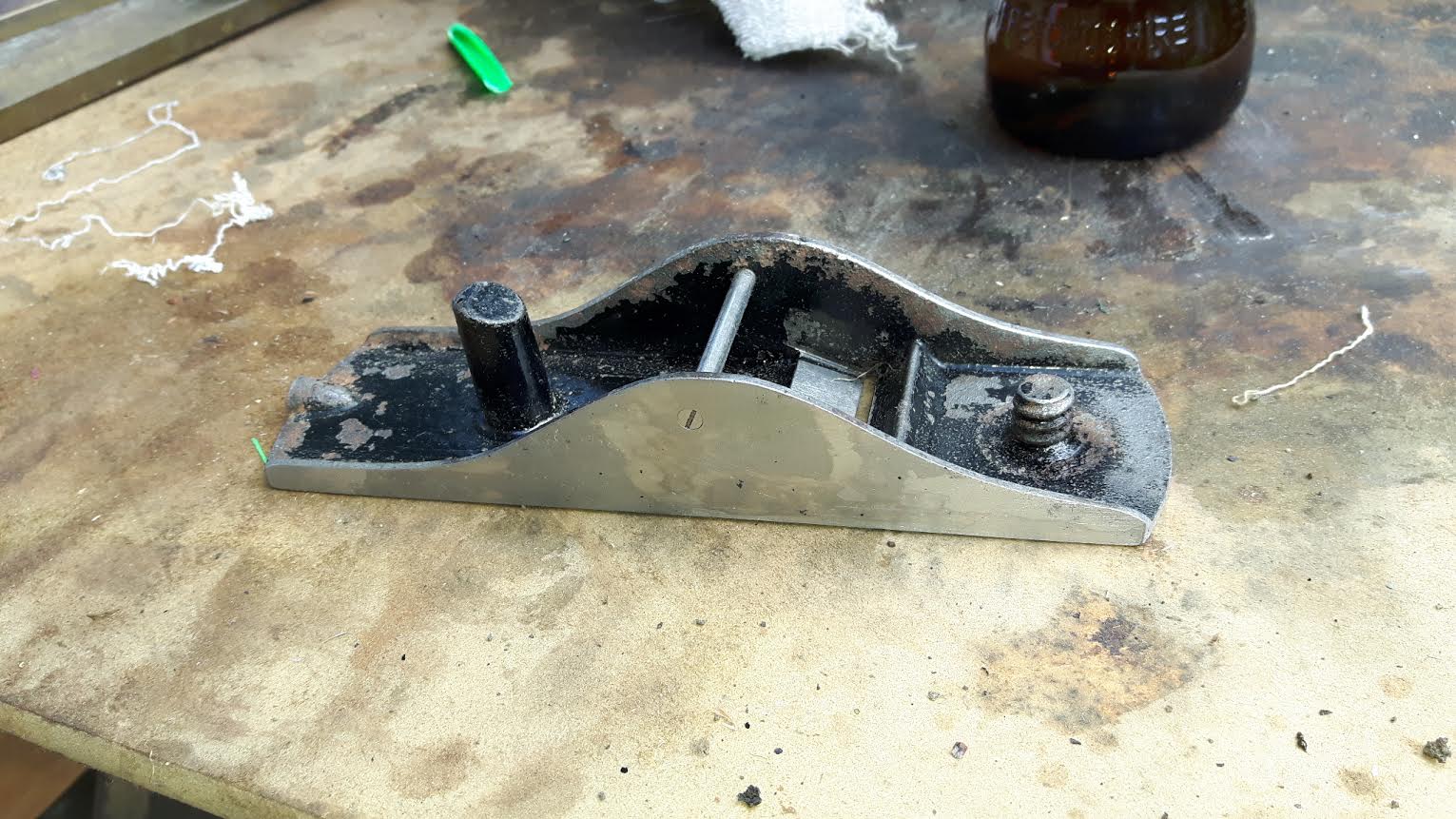
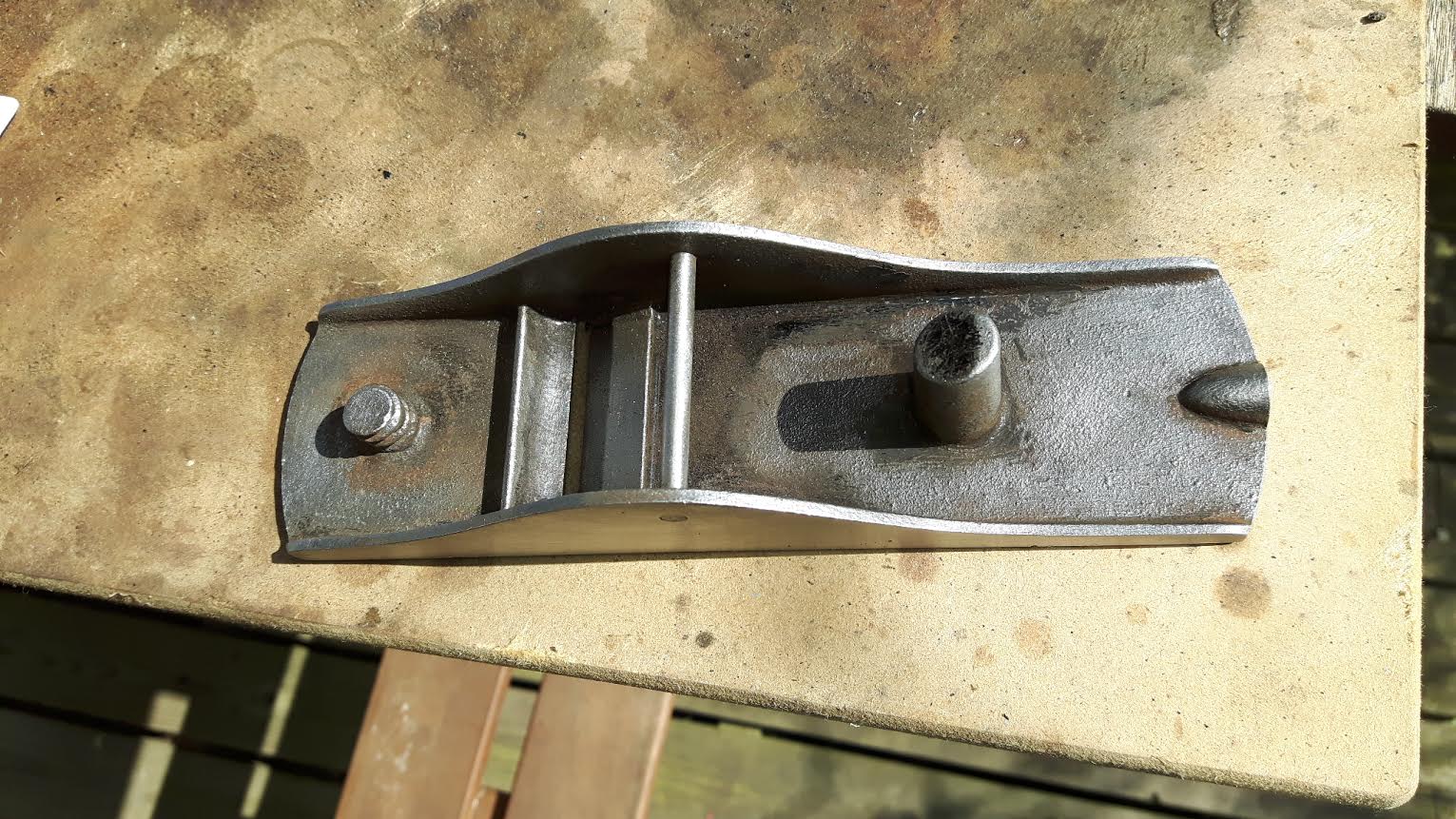
Now, here was my first mistake. I set about undercoating and painting it although I only actually wanted a tiny section above the mouth to be painted eventually. Bear with me.
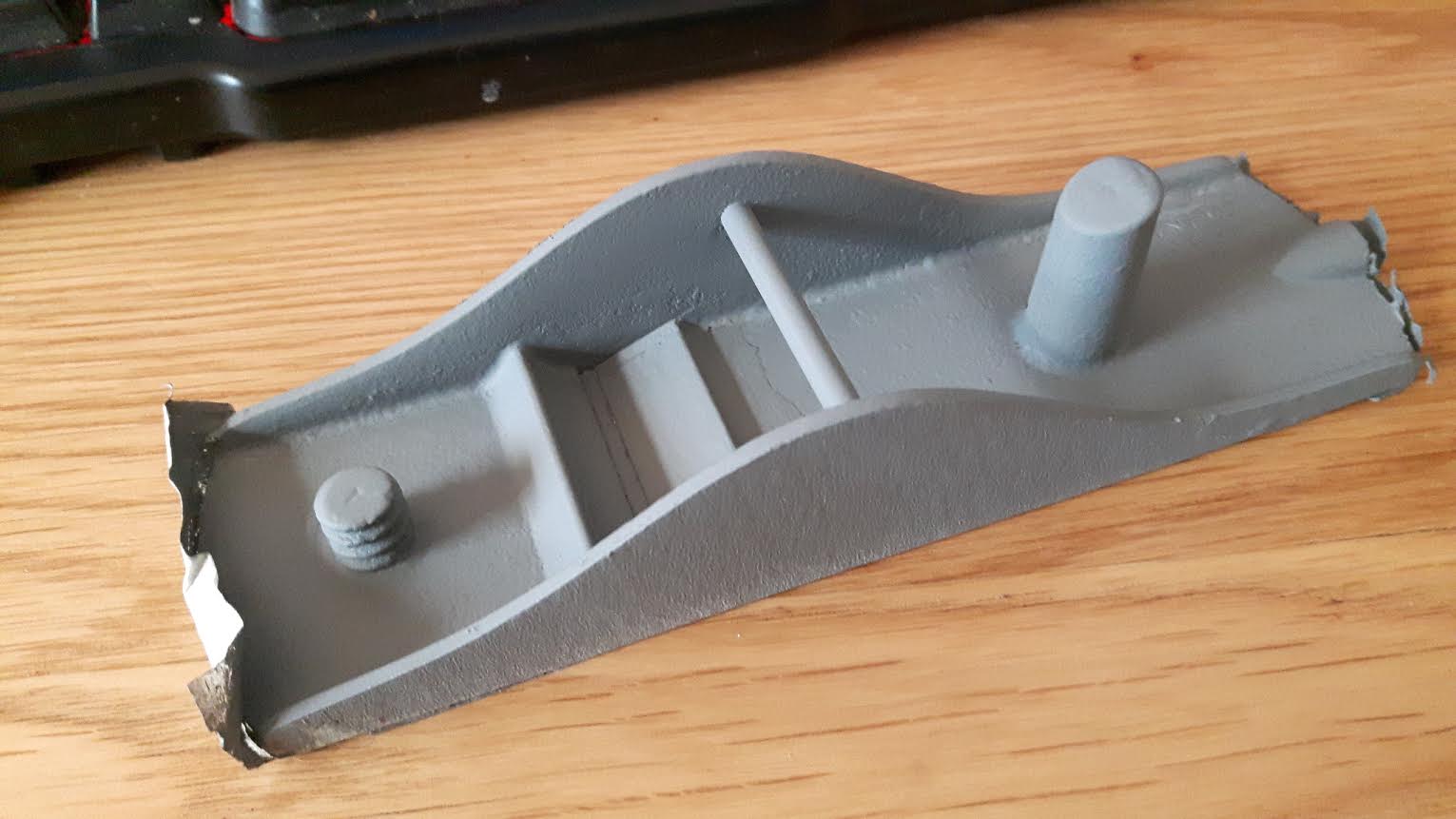
Live and learn. :|
I started cutting the wooden bits. To save time I cut them from a 5" block of mahogany on my top of the range Evolution chop saw. I then spent about a day trying to get the cuts squared off.... Lesson learned, again. You can hide a few mm out of square on a window sill. Not when the wood has to be cut this accurately. So the chop saw was shouted at and demoted and lost all shore leave. That'll teach me for not having more faith in my handsawing abilities.
Measuring the angle from the mouth to bed the wood in correctly was done by wizardry and jiggerypokery. And a little bit of luck.
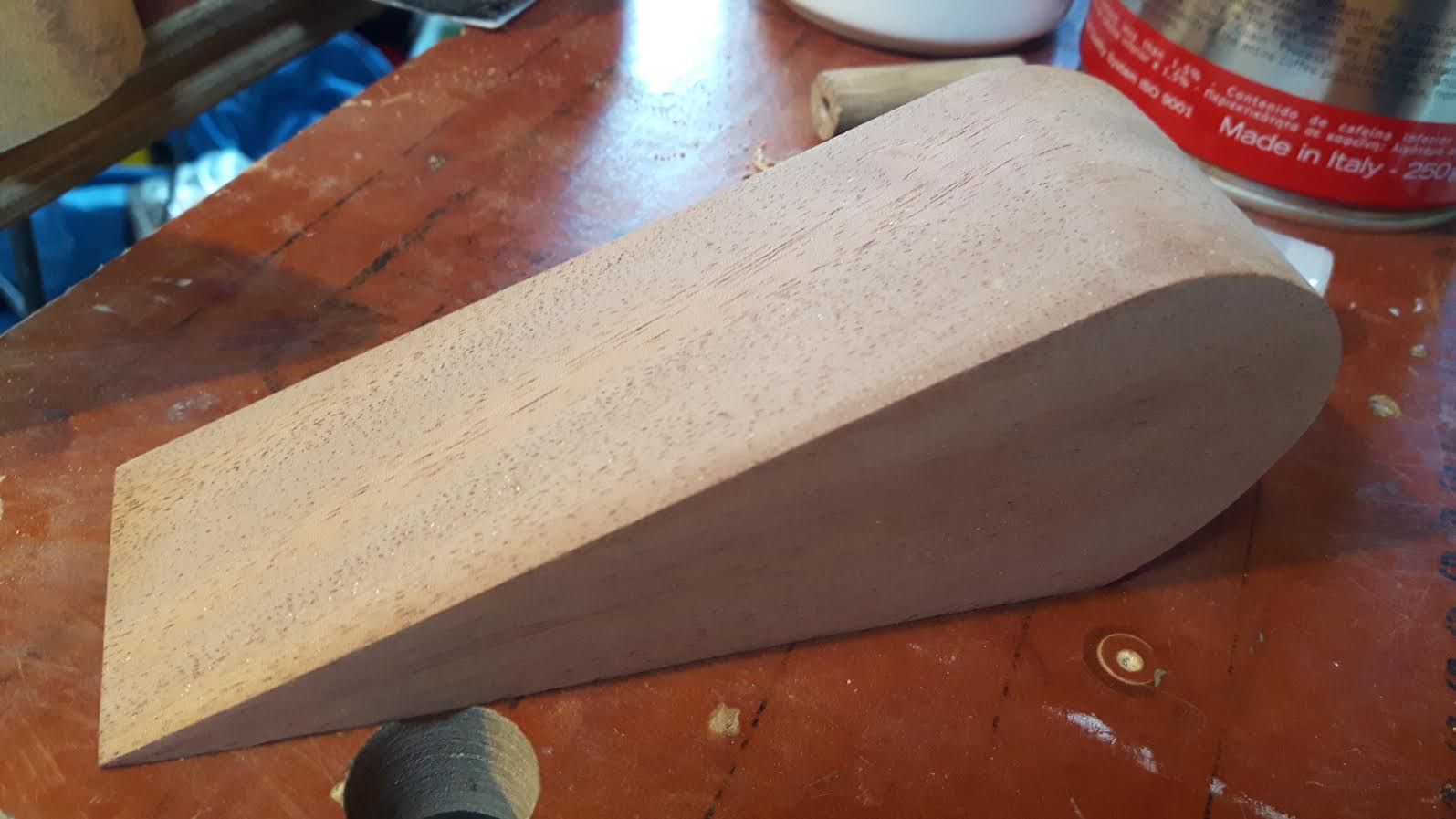
I cut the rear bit off to fit then drilled holes by hand with forstner bits (thankyou Benjamin!), the plan is 1, they will provide stability for the gluing of the handles and 2, i'm possibly planning on laying in a thread and a brass screw of some variety. To hold stuff in place, but also for looks and razzle dazzle. 8)
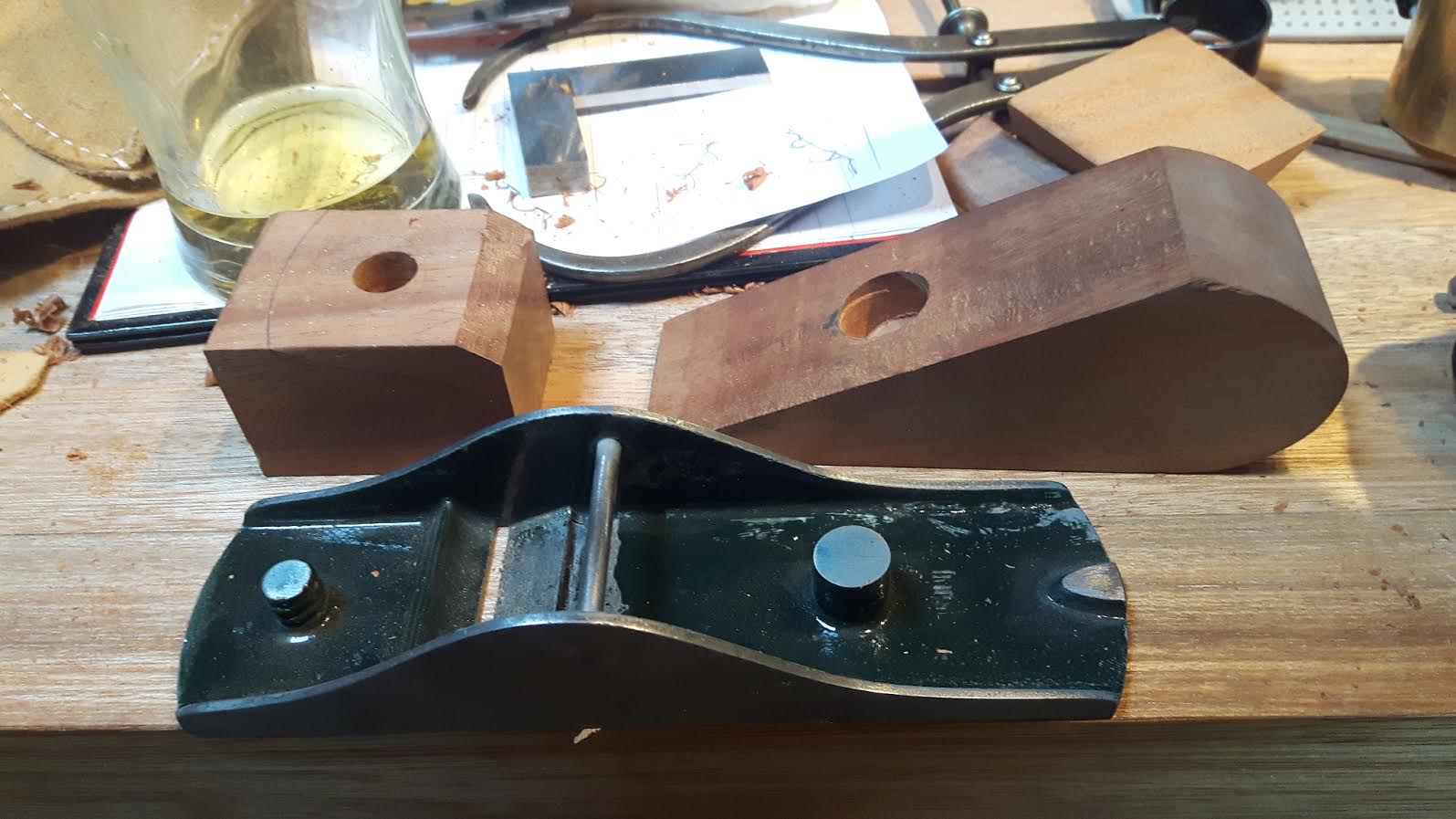
Tons more work to do and loads of ways that I might still mess everything up.
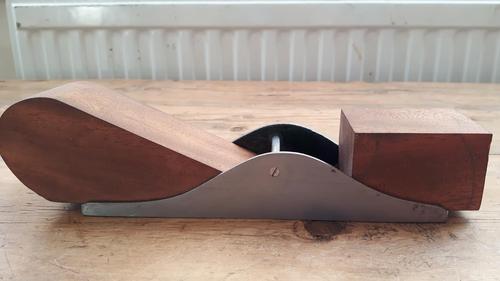
So. The real reason for posting.
I had a sudden thought that I need to get the blade now before I do any more work trying to fettle it all up. That way I can work with real error margins.
I think its a 1 5/8" blade. I was planning on a QS workshop Heaven blade originally. But it seems that's not available. Hock, Clifton and Veritas all do the right dimension blades. But of course they are all super pricey. Any ideas? I'm mostly after an off the shelf solution though perhaps cutting down a thicker wood iron is not out of the question.
Also and more importantly (in fact the whole reason for this post), I want to shape a brass lever cap to wedge under the bar to secure the iron. (I'm nowhere near being able to drill pivot pins etc). Would the lever cap/screw be man enough to hold the iron in place without some form of wedging? Chip breaker? If it's a 3mm blade? I think I might be able to shape the lever cap to act as a chipbreaker. Any ideas?!?
I'd be grateful for any knowledge you can throw this way.
Cheers as always
Chris