Chip shop
Established Member
I have to replace some skirting in a friends gaff. It's only a couple of yards that were terminated by a fitted unit during the original build.
The profile is one I haven't come across before:
I don't want to have knives ground for the spindle as they'd never get used again, and I don't have any blanks to grind my self.
I could do with fitting tomorrow as I have to go over to patch some floor board.
So the question is; how would you lot do it?
Cheers,
Ed
The profile is one I haven't come across before:
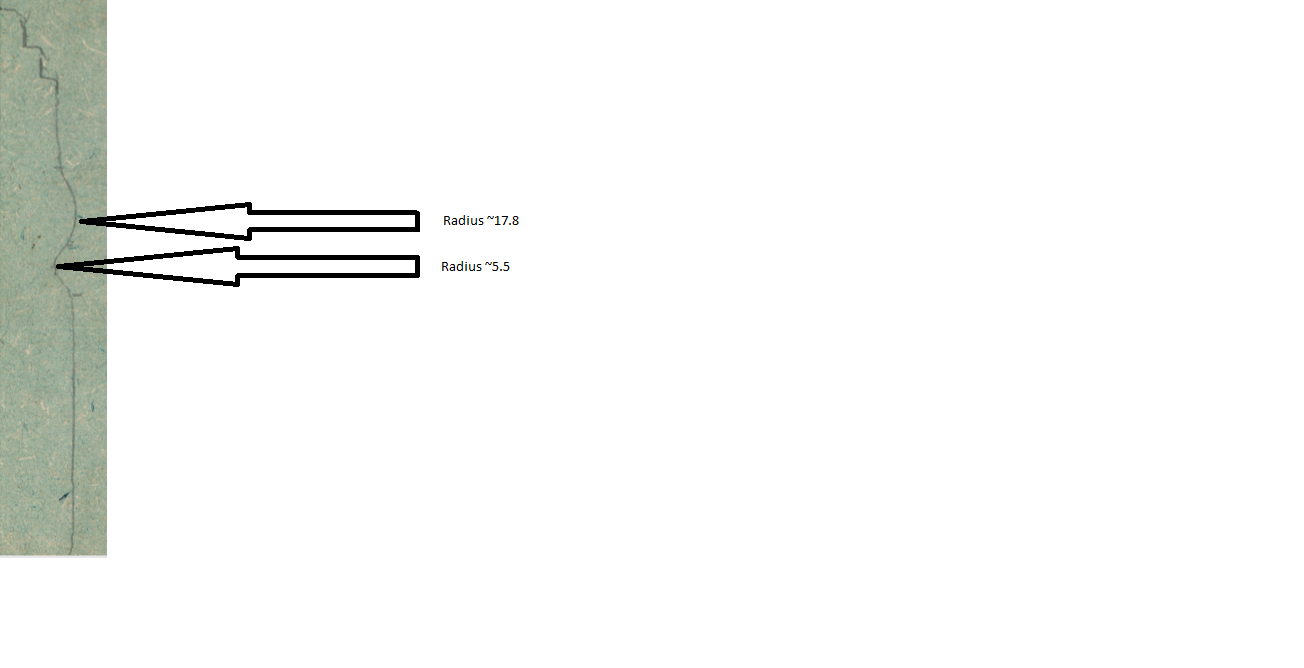
I don't want to have knives ground for the spindle as they'd never get used again, and I don't have any blanks to grind my self.
I could do with fitting tomorrow as I have to go over to patch some floor board.
So the question is; how would you lot do it?
Cheers,
Ed