Paul Chapman
Established Member
adrian":10mkpzi5 said:What is the Eclipse modification?
Unmodified on the left, modified on the right
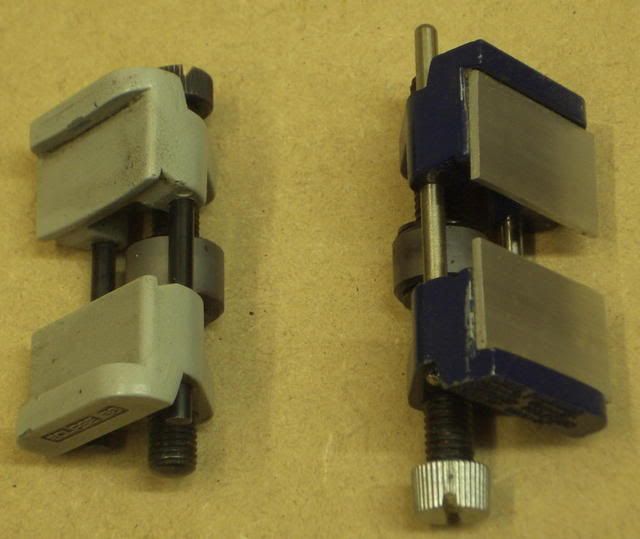
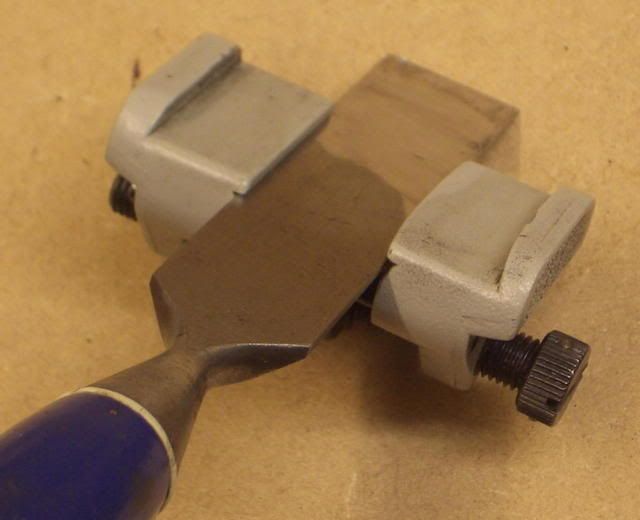
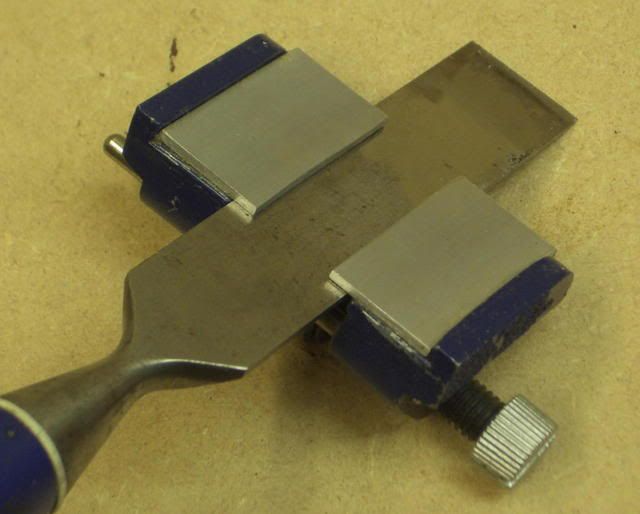
Simply glue (Araldite) or screw some thin metal on so that the chisel can register from the flat side.
With the unmodified guide, the chisel fits into grooves each side and some chisels don't fit the grooves very well.
Cheers :wink:
Paul