profchris
Established Member
Now I'm into finishing, which means there is very little to show by way of photos. But I thought my process might be of interest, if only because (having tried most of the other possibilities) I think it's about the simplest possible for an amateur (other than simply spraying clear automotive lacquer from a rattle can, with which some can achieve rather good results, but at which I'm a complete failure!).
My finish of choice is clear shellac, bought ready-mixed (Liberon is your only brand here, though the cheaper hardware store brown ready mixes work quite well too). I'm not French polishing, but rather brushing it on. So I suppose my finish is spirit varnish.
Once everything is scraped or sanded as well as I can I wipe on two thin coats with a paper towel, leaving an hour or two between them. This avoids end grain areas like the heel absorbing more finish than the rest and thus becoming darker.
Then I start on the neck, masking off the body and fingerboard.
The reason for doing them separately is that it's impossible to brush into the neck/body join without getting finish on the other side of the join, with the result that a visible build-up of extra finish occurs either side of the join. This way the only bit which gets double treatment is the join itself, and that helps fill any gaps.
I use a flat, fine hair artist's brush, and apply the finish in a single coat, working from heel to headstock. It begins to dry immediately, so you mustn't go back and re-coat any bits you missed - catch them next time! After about 8 hours I can take any nibs off with P1000 paper on a cork block, sanding very lightly indeed, and then re-coat. No more than two coats a day.
Here is the neck after three coats, and I reckon one more will do it.
I'm happy with a fairly thick film of finish on the neck, because I don't want it to be so thin that it wears quickly away through playing. This mahogany has small pores and not too many of them, so I've left the pores unfilled. It gives a decent look, and helps stop the neck feeling too sticky when playing (a really high gloss can be a problem here).
The koa headplate had some fairly large pores, so I brushed on three coats and then, using a finely set scraper, removed the finish back nearly to bare wood. This has pretty much left the pores filled with finish (for some reason I don't understand, shellac never fills up pores, but seems to settle to an even film which therefore includes pores as it builds up. But as there is finish in the bottom of the pores, once I've cut back most of them are now flat at the base).
Here is the headplate after the process and with one layer of finish brushed on top. I reckon a second coat is needed, and then there will be final shining up which I'll show later.
I like shellac because, as you can see, it really brings out the figure in the wood.
Next the body, which is a similar process to the headplate (but not quite, because we need a really thin film of finish to avoid killing the sound of the instrument).
My finish of choice is clear shellac, bought ready-mixed (Liberon is your only brand here, though the cheaper hardware store brown ready mixes work quite well too). I'm not French polishing, but rather brushing it on. So I suppose my finish is spirit varnish.
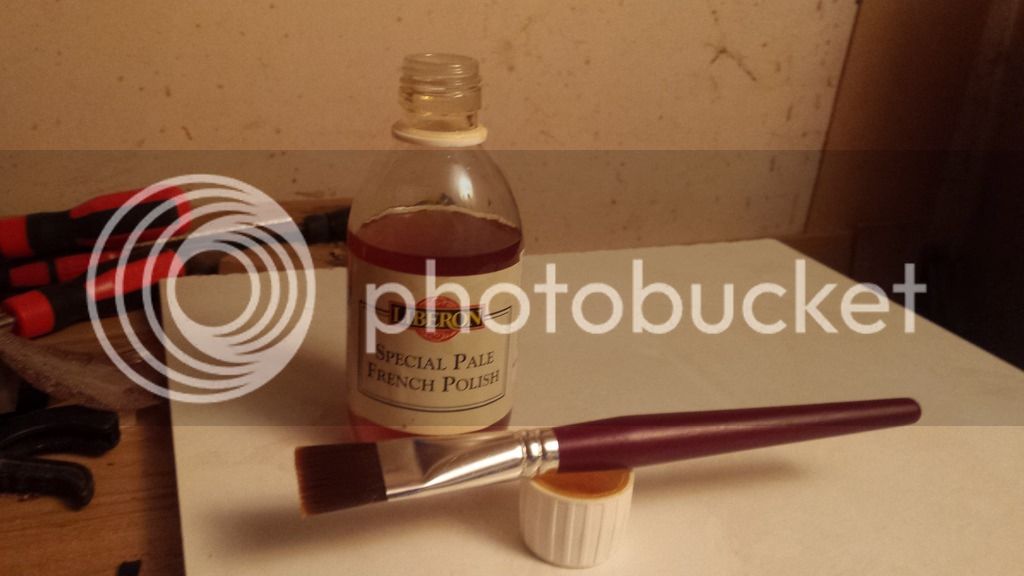
Once everything is scraped or sanded as well as I can I wipe on two thin coats with a paper towel, leaving an hour or two between them. This avoids end grain areas like the heel absorbing more finish than the rest and thus becoming darker.
Then I start on the neck, masking off the body and fingerboard.
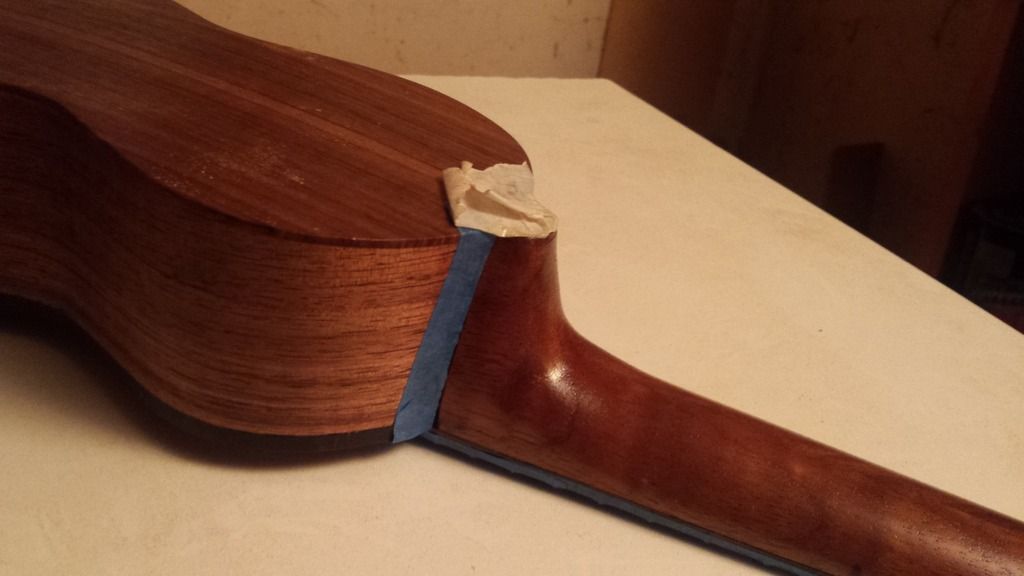
The reason for doing them separately is that it's impossible to brush into the neck/body join without getting finish on the other side of the join, with the result that a visible build-up of extra finish occurs either side of the join. This way the only bit which gets double treatment is the join itself, and that helps fill any gaps.
I use a flat, fine hair artist's brush, and apply the finish in a single coat, working from heel to headstock. It begins to dry immediately, so you mustn't go back and re-coat any bits you missed - catch them next time! After about 8 hours I can take any nibs off with P1000 paper on a cork block, sanding very lightly indeed, and then re-coat. No more than two coats a day.
Here is the neck after three coats, and I reckon one more will do it.
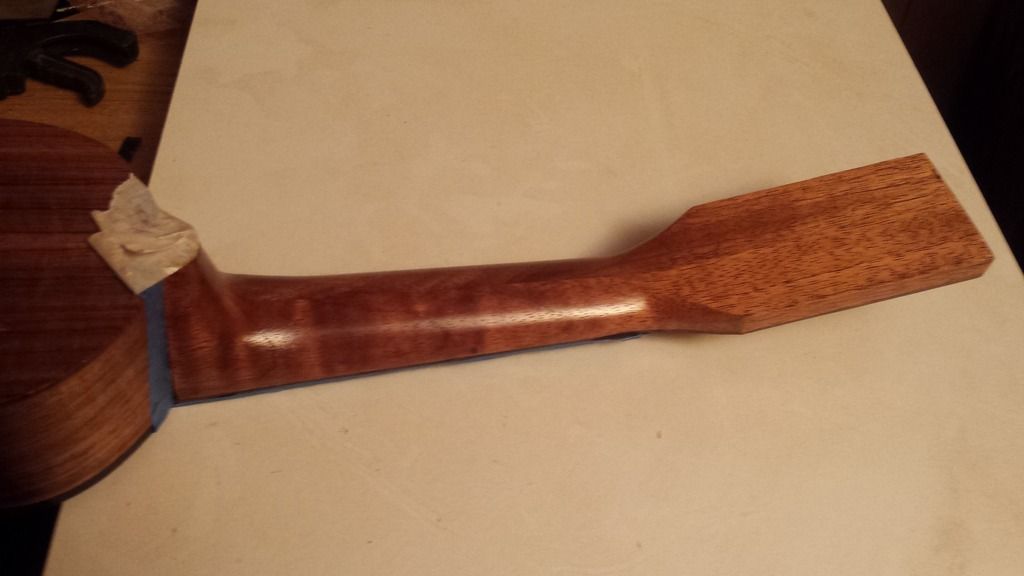
I'm happy with a fairly thick film of finish on the neck, because I don't want it to be so thin that it wears quickly away through playing. This mahogany has small pores and not too many of them, so I've left the pores unfilled. It gives a decent look, and helps stop the neck feeling too sticky when playing (a really high gloss can be a problem here).
The koa headplate had some fairly large pores, so I brushed on three coats and then, using a finely set scraper, removed the finish back nearly to bare wood. This has pretty much left the pores filled with finish (for some reason I don't understand, shellac never fills up pores, but seems to settle to an even film which therefore includes pores as it builds up. But as there is finish in the bottom of the pores, once I've cut back most of them are now flat at the base).
Here is the headplate after the process and with one layer of finish brushed on top. I reckon a second coat is needed, and then there will be final shining up which I'll show later.
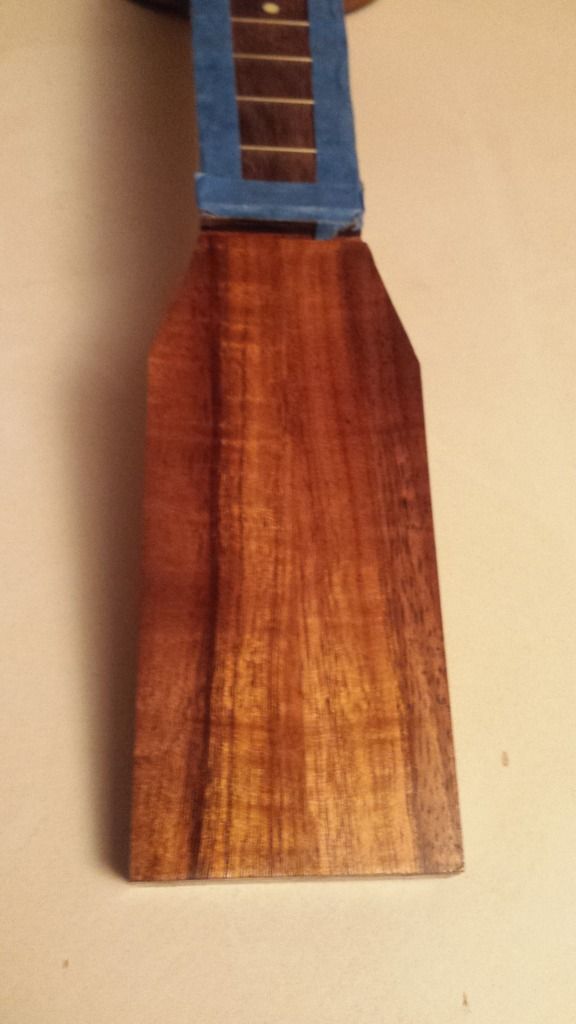
I like shellac because, as you can see, it really brings out the figure in the wood.
Next the body, which is a similar process to the headplate (but not quite, because we need a really thin film of finish to avoid killing the sound of the instrument).