OPJ
Established Member
This weekend, I haven't spent much time out in the workshop at all although, I have made some progress on the shaping of the legs and rails.
After marking out with my template, I started cutting the legs on the bandsaw. You have to approach these as if you are cutting a cabriole leg. Once the first cut is done, you need to re-attach the offcuts so the piece is fully supported while you cut.
Even after purchasing a new vacuum extractor recently, I could see the dust raining out of the left-hand side of my saw as I cut! You can see where the mounds of it have built up, just below the bottom door. This was never an issue with the type of extraction I was using; it's in the design of this type of saw, where there's no room to get a hose under the table to extractor at source so, it ends up going round with the blade. Must look up Boz's solution again... :wink:
There's quite a lot of waste involved here, which either means I bin the lot or, add to growing collections of "usable" offcuts... Well, I can still get decent lengths of 400 x 50 x 21 (sawn) from this lot so, on the pile they go! :roll:
After all that sawing, I dragged my bobbin sander out before I looked at my spokeshaves. That 3/8"x6tpi blade I was using is on its last legs and, although I don't claim to be a 'master' at the bandsaw, the cuts were going all over the place. That's why I'm using this sander. Not to finish to the line as it requires a great amount of skill to get a consistent curve with these things! But, to remove the bulk of the waste for 'shaving later.
The sleeves that came fitted with these bobbins must be at least 120g as I find they're too fine for bulk material removal. I must invest in some coarse abrasives! Still, I spent a good twenty-minutes on this with the vacuum going and it didn't even get hot. 8)
Now, I've got to decided on my next move... The plan is to clean up one of each rail, stick the other one to it (with double-sided tape) and use that as a 'template' for a router cutter. This won't work on the legs because my longest trimming cutter is about 25mm so, I'd still have plenty to clean up by hand.
I might have to give Ray Iles a call in the morning and see where he's at with this thicker spokeshave blades I enquired about a month ago... The current blade in my old A151 'shaves will cut it but, it's difficult trying to avoid chatter.
Whatever happens, I'm sure I'll figure something out! :wink: Trouble is, I won't have much time on this in the coming week.
After marking out with my template, I started cutting the legs on the bandsaw. You have to approach these as if you are cutting a cabriole leg. Once the first cut is done, you need to re-attach the offcuts so the piece is fully supported while you cut.
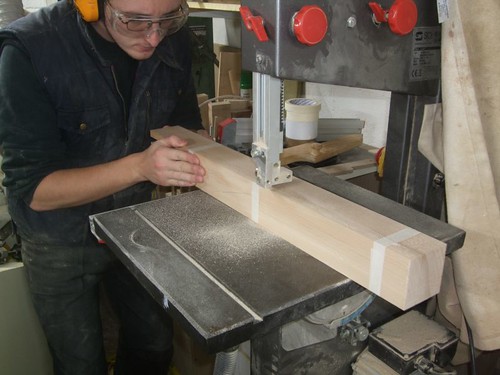
Even after purchasing a new vacuum extractor recently, I could see the dust raining out of the left-hand side of my saw as I cut! You can see where the mounds of it have built up, just below the bottom door. This was never an issue with the type of extraction I was using; it's in the design of this type of saw, where there's no room to get a hose under the table to extractor at source so, it ends up going round with the blade. Must look up Boz's solution again... :wink:
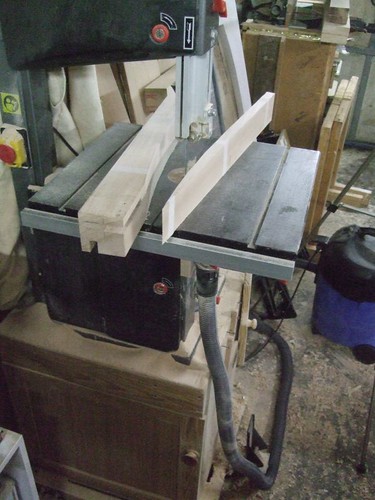
There's quite a lot of waste involved here, which either means I bin the lot or, add to growing collections of "usable" offcuts... Well, I can still get decent lengths of 400 x 50 x 21 (sawn) from this lot so, on the pile they go! :roll:
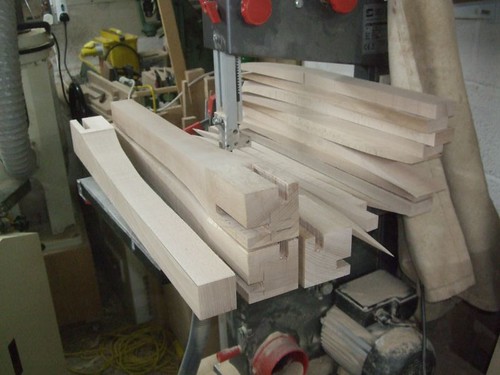
After all that sawing, I dragged my bobbin sander out before I looked at my spokeshaves. That 3/8"x6tpi blade I was using is on its last legs and, although I don't claim to be a 'master' at the bandsaw, the cuts were going all over the place. That's why I'm using this sander. Not to finish to the line as it requires a great amount of skill to get a consistent curve with these things! But, to remove the bulk of the waste for 'shaving later.
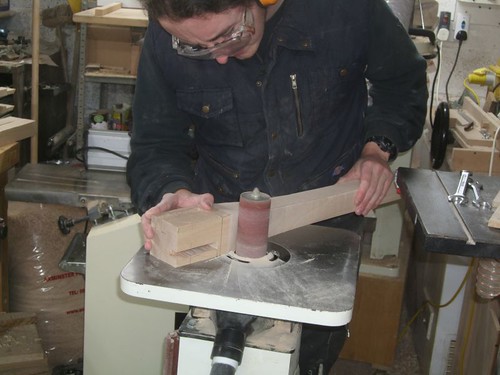
The sleeves that came fitted with these bobbins must be at least 120g as I find they're too fine for bulk material removal. I must invest in some coarse abrasives! Still, I spent a good twenty-minutes on this with the vacuum going and it didn't even get hot. 8)
Now, I've got to decided on my next move... The plan is to clean up one of each rail, stick the other one to it (with double-sided tape) and use that as a 'template' for a router cutter. This won't work on the legs because my longest trimming cutter is about 25mm so, I'd still have plenty to clean up by hand.
I might have to give Ray Iles a call in the morning and see where he's at with this thicker spokeshave blades I enquired about a month ago... The current blade in my old A151 'shaves will cut it but, it's difficult trying to avoid chatter.
Whatever happens, I'm sure I'll figure something out! :wink: Trouble is, I won't have much time on this in the coming week.