Richard T
Established Member
Thanks Jim,
7/16 X 14 .... I wonder where to look for that - I get google whacked when searching online and the only square taps I have ever seen are these I got from the boot sale a few weeks ago
- Ignore the #78, except for scale purposes. These were also the only ones the seller had ever seen and he had been carting them around for ages.
Of course, there is then the problem of finding the corresponding threaded bar. I have vaguely been thinking along the lines of finding a clamp or such, common at boot sales, that I could use as a supply, then try to find the appropriate tap ... (I plan to turn the bolt heads from brass/bronze and square rivet them on so just finding the threaded bar would be ok.) I realise this might be quite a long shot but if possible it would be far the cheapest way.
Along with all the mentioned pivot methods there is also the spring loaded method - and there is even a choice in that: blind holes or holes with shoulders and a narrower through - hole to poke things through to release the cap... so many ideas, so little brain space.
7/16 X 14 .... I wonder where to look for that - I get google whacked when searching online and the only square taps I have ever seen are these I got from the boot sale a few weeks ago
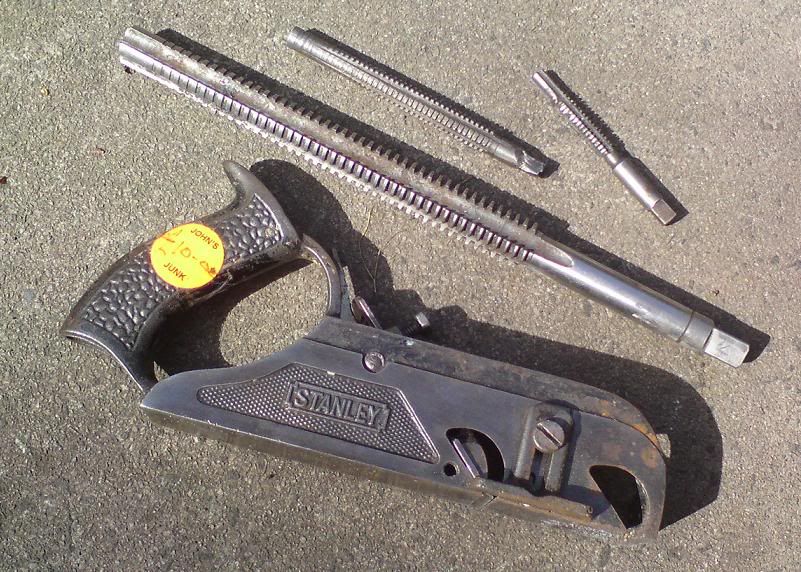
- Ignore the #78, except for scale purposes. These were also the only ones the seller had ever seen and he had been carting them around for ages.
Of course, there is then the problem of finding the corresponding threaded bar. I have vaguely been thinking along the lines of finding a clamp or such, common at boot sales, that I could use as a supply, then try to find the appropriate tap ... (I plan to turn the bolt heads from brass/bronze and square rivet them on so just finding the threaded bar would be ok.) I realise this might be quite a long shot but if possible it would be far the cheapest way.
Along with all the mentioned pivot methods there is also the spring loaded method - and there is even a choice in that: blind holes or holes with shoulders and a narrower through - hole to poke things through to release the cap... so many ideas, so little brain space.