Derek Cohen (Perth Oz)
Established Member
About a month ago I began a thread about designing and building two carver chairs to accompany the 6 bentwood chairs we have owned for the past 40 years. The chairs were purchased all those years ago along with a table, which is around 200 years old. We need a larger table, and time has come to replace it and add two more chairs.
The table planned will be a modern version of this, in Hard Maple and round Jarrah legs. The carver chairs need to match the table and blend with these chairs. Our taste is minimalist, Mid Century Danish, modern. An example of the lines I seek is this sofa table I built several years ago ...
So I started thinking about the chairs I would build, and I took inspiration from this picture ...
... and began to evolve a design along similar lines. The 8 legs were started (just need rounding) and the seats carved, and then the tenons were cut. And that is where the problem arose. I had this idea for integrated tenons into through mortices in the legs. Very few chairs are built like this, and for a good reason - you cannot control for run out in the tenons, and run out make for weak tenons. And that is what I discovered. So I stopped the build, and decided to begin again from scratch.
I started looking more carefully at the chair I had come across and had treated rather casually. It has a name: DC 09, and it was designed by the Japanese- Scandinavian duo, Kyoko Inoda and Nils Sveje, in 2011. It is built by the Miyazaki factory in Japan.
There is a challenge here - can I replicate it purely from photos? This is unlikely since one needs to examine an object in three dimensions to discover the subtleties of the design and construction. I have experience of this, having made an exact copy of Hans Wegner's "The Chair" or the "Round Chair" several years ago. What made this possible is that I own an original. One is mine and one is Wegner's ...
So the chairs I build will not be exact, but hopefully close. Actually, I am still on the fence about the arms and back and may modify this ... but will will see. We need to start with the seat. That is the key.
Help comes from two video I found ...
Some dimensions:
The doors above my bench make a place to pin details and photos ..
The seat plan was scaled and drawn using images from the videos and photos.
Two half-templates were created - the first was a straight-sided outline of the seat. The reason for this is that I planned to use loose tenon joinery, which would enable the tenons to have straight grain for maximum strength, and the mortices would be made using a Domino. These would be 30mm long x 10mm wide, in other words would use custom-made loose tenons. The straight sides would make it easier to cut the mortices ahead of shaping the seats.
The second half-template was the actual outline of the seat, and this positions the tenons.
Here the tenons are positioned ...
A little jack-planning to flatten the underside of the seat blanks ..
These are now sawn to shape ...
After this was done it became apparent just how the first shaping of the chairs differed from the DC09 design. Here is the first chair along with two legs. In the background can be seen the plan I had made for that build ...
It looks quite good, with the angles and spacings appearing correct. In fact, they are quite different from the DC09. Below is the DC09 seat below the first seat. You can see the positioning of the legs ..
Before I dominoed the mortices, the legs were mocked up to be sure of the angles. I discovered that they should be at 14 degrees and not 10 degrees, as they had been before. In the top right corner you can see a DC09 for comparison ...
Guides for 14 degrees ...
Marked and morticed ...
Tenons were made on the router table ...
All is looking right so far ...
The rule for chair backs is that thy need to allow for a lean of about 90-95 degrees. I have been thinking about this but decided to set aside this area for later. The priority is to get the seat shape correct - in three dimensions. - and its relationship with the legs (which were shaped in the first build - they are substantially correct, other than the upper ends being around 28mm against the - estimated - 40mm of the DC09. I will decide on whether to keep or replace these later). I have left the legs 1" longer in the lower half to adjust the tilt of the seat (the seat sits 18" off the ground and the ones I made previously are 19" in this respect).
I did stand the old chair along the table, and noted how low the arm rests were in reality - actually an ideal height for comfort. I do have some ideas how they may be "improved" aesthetically .... but this for later.
All advice gratefully received.
Regards from Perth
Derek
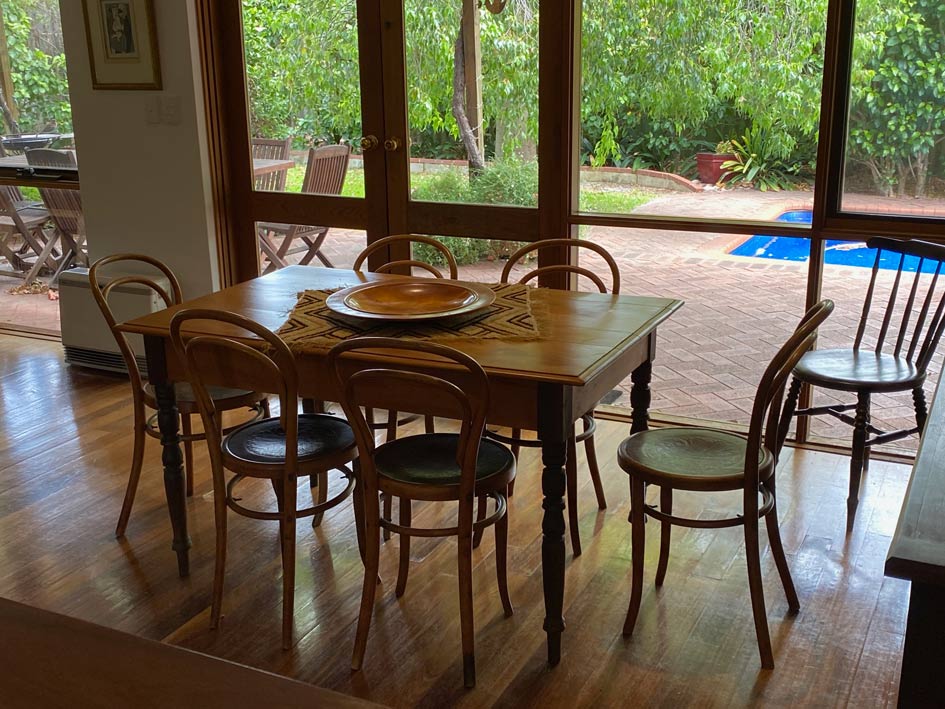
The table planned will be a modern version of this, in Hard Maple and round Jarrah legs. The carver chairs need to match the table and blend with these chairs. Our taste is minimalist, Mid Century Danish, modern. An example of the lines I seek is this sofa table I built several years ago ...
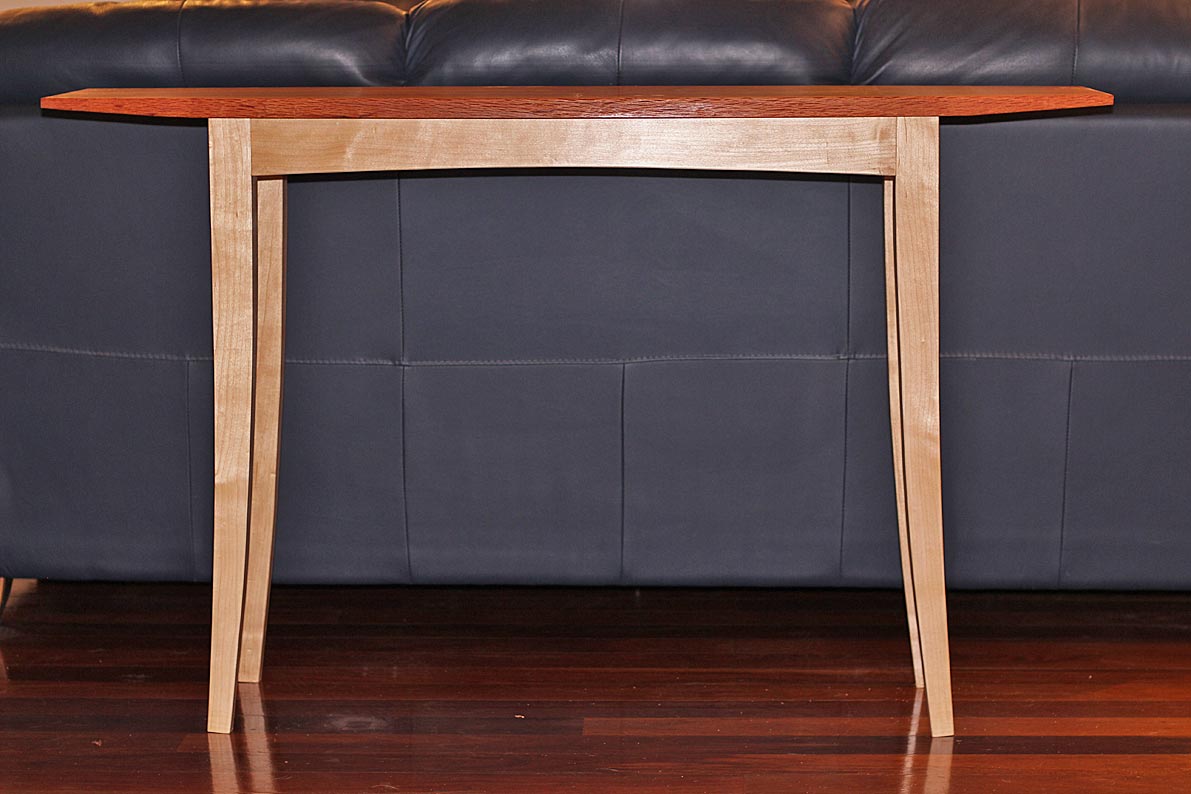
So I started thinking about the chairs I would build, and I took inspiration from this picture ...
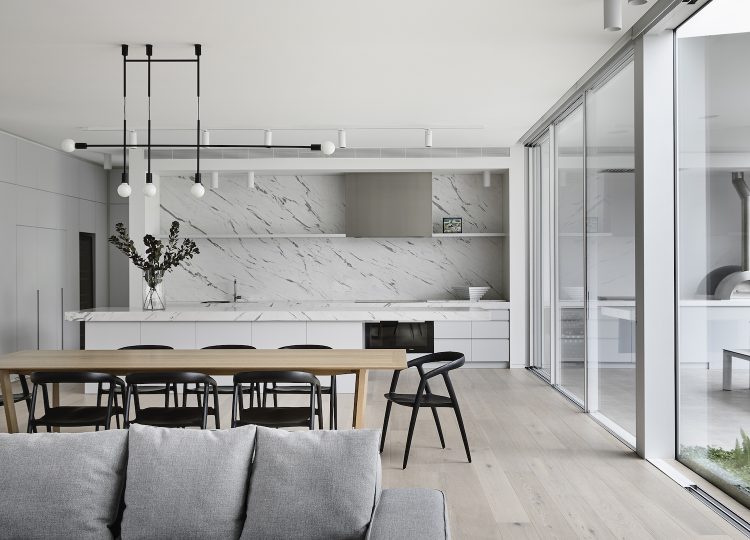
... and began to evolve a design along similar lines. The 8 legs were started (just need rounding) and the seats carved, and then the tenons were cut. And that is where the problem arose. I had this idea for integrated tenons into through mortices in the legs. Very few chairs are built like this, and for a good reason - you cannot control for run out in the tenons, and run out make for weak tenons. And that is what I discovered. So I stopped the build, and decided to begin again from scratch.
I started looking more carefully at the chair I had come across and had treated rather casually. It has a name: DC 09, and it was designed by the Japanese- Scandinavian duo, Kyoko Inoda and Nils Sveje, in 2011. It is built by the Miyazaki factory in Japan.
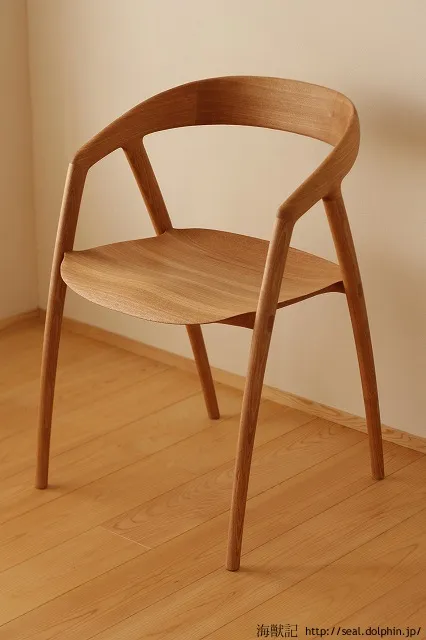
There is a challenge here - can I replicate it purely from photos? This is unlikely since one needs to examine an object in three dimensions to discover the subtleties of the design and construction. I have experience of this, having made an exact copy of Hans Wegner's "The Chair" or the "Round Chair" several years ago. What made this possible is that I own an original. One is mine and one is Wegner's ...
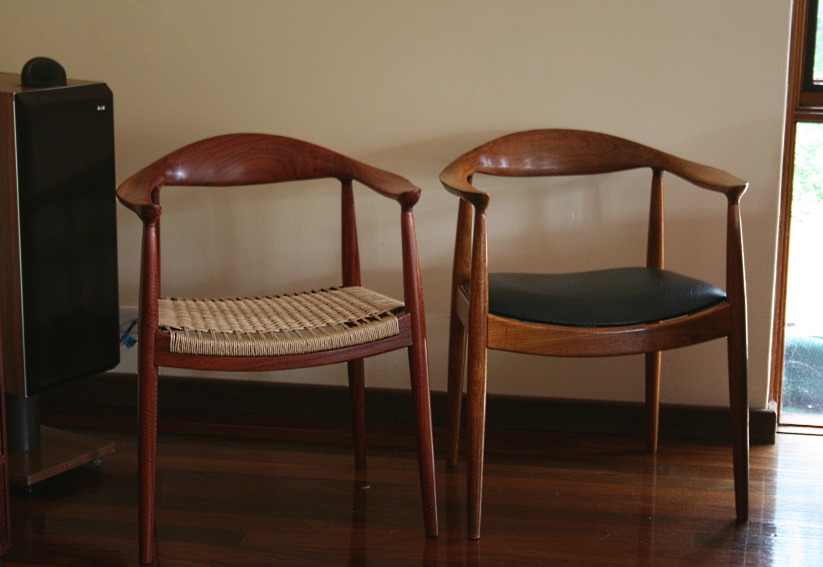
So the chairs I build will not be exact, but hopefully close. Actually, I am still on the fence about the arms and back and may modify this ... but will will see. We need to start with the seat. That is the key.
Help comes from two video I found ...
Some dimensions:
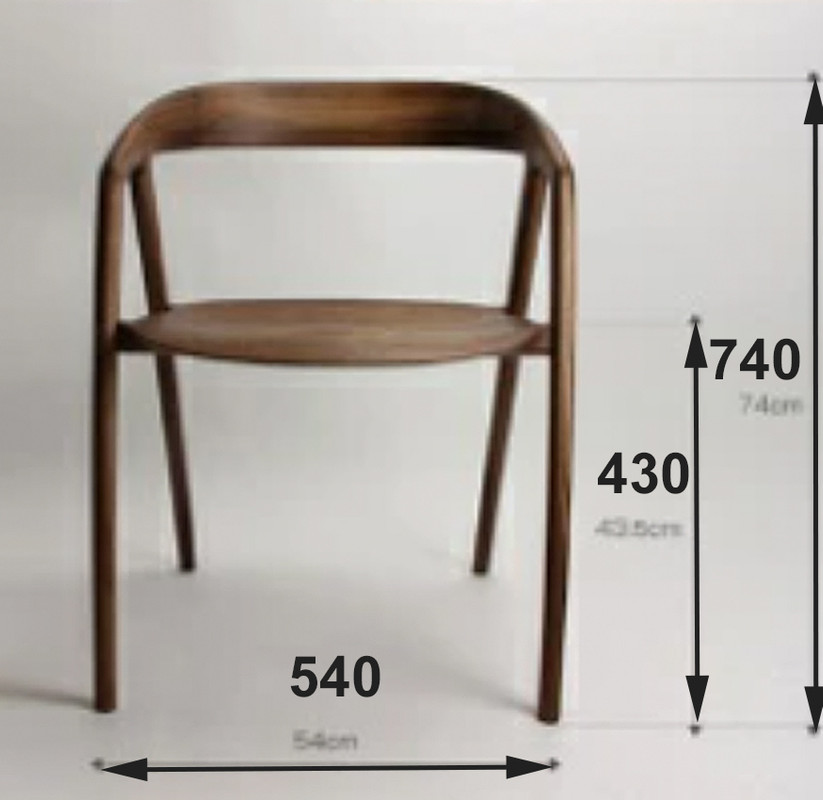
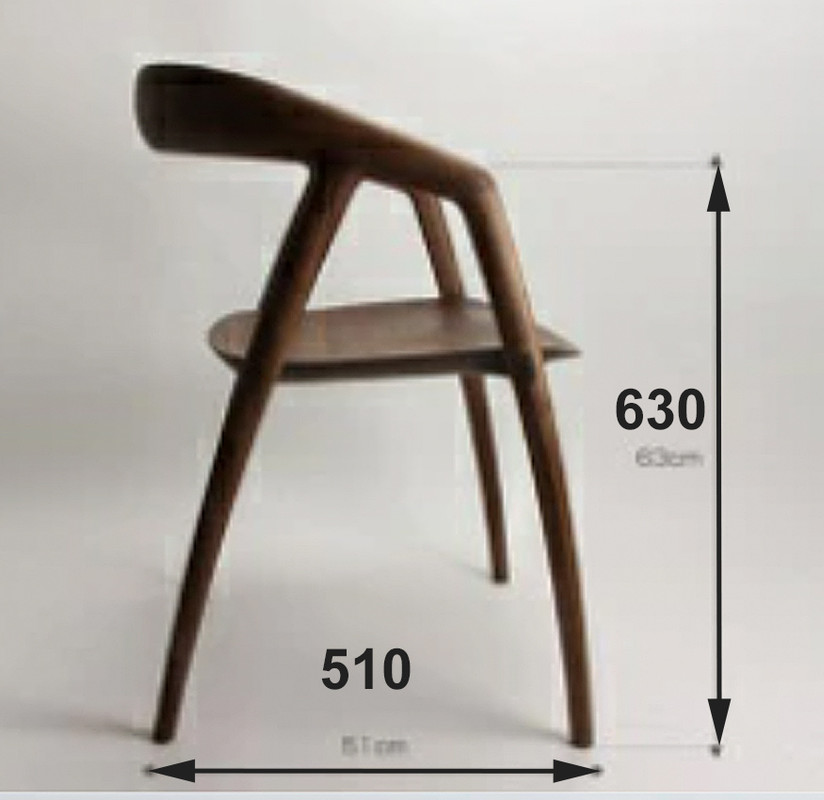
The doors above my bench make a place to pin details and photos ..
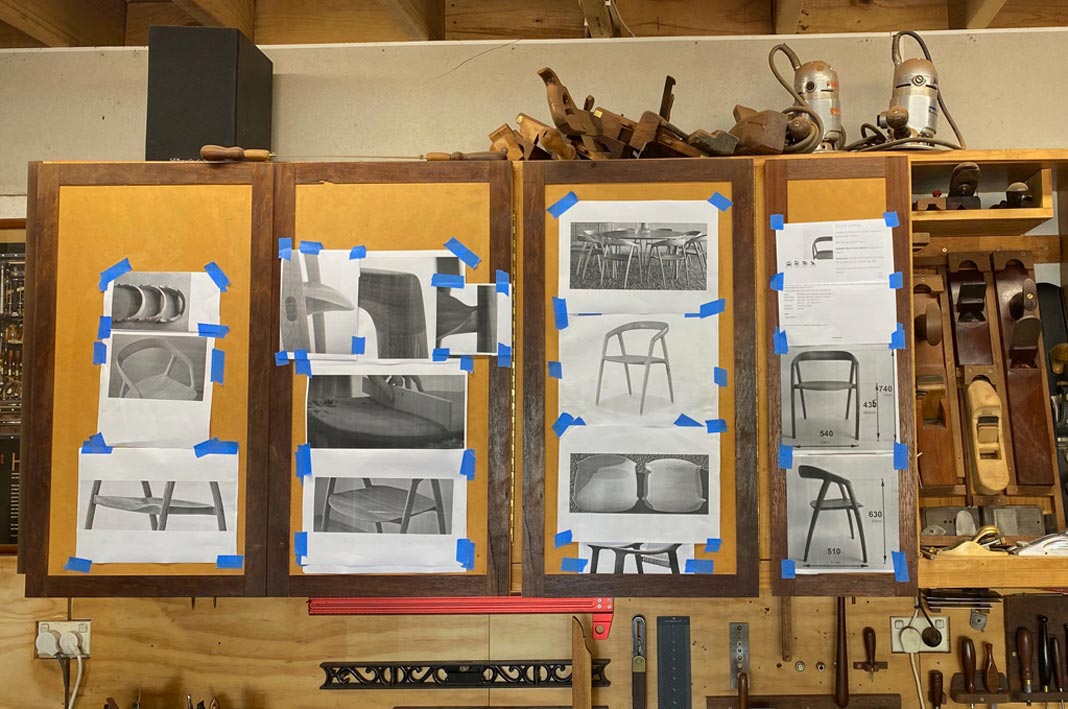
The seat plan was scaled and drawn using images from the videos and photos.
Two half-templates were created - the first was a straight-sided outline of the seat. The reason for this is that I planned to use loose tenon joinery, which would enable the tenons to have straight grain for maximum strength, and the mortices would be made using a Domino. These would be 30mm long x 10mm wide, in other words would use custom-made loose tenons. The straight sides would make it easier to cut the mortices ahead of shaping the seats.
The second half-template was the actual outline of the seat, and this positions the tenons.
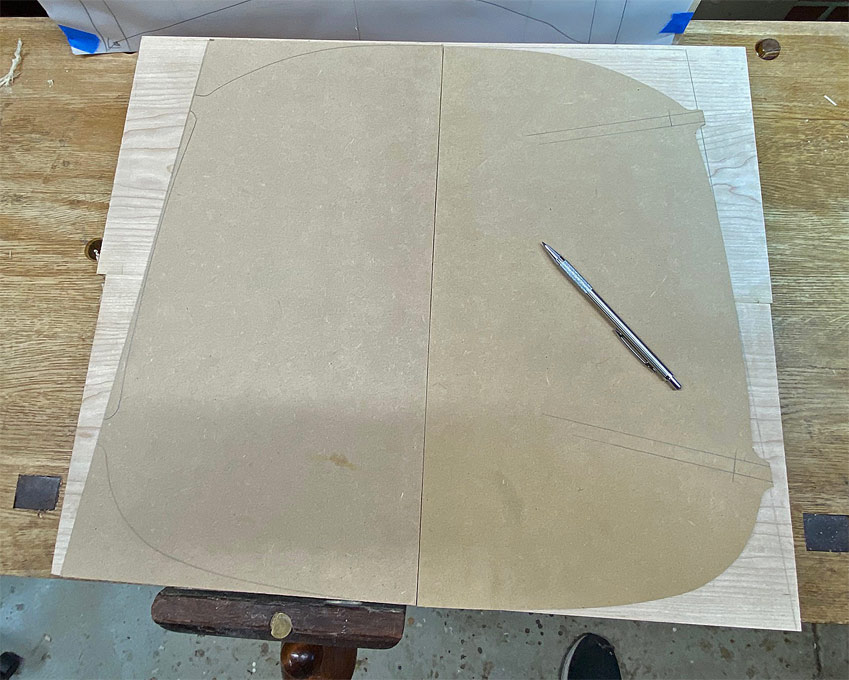
Here the tenons are positioned ...
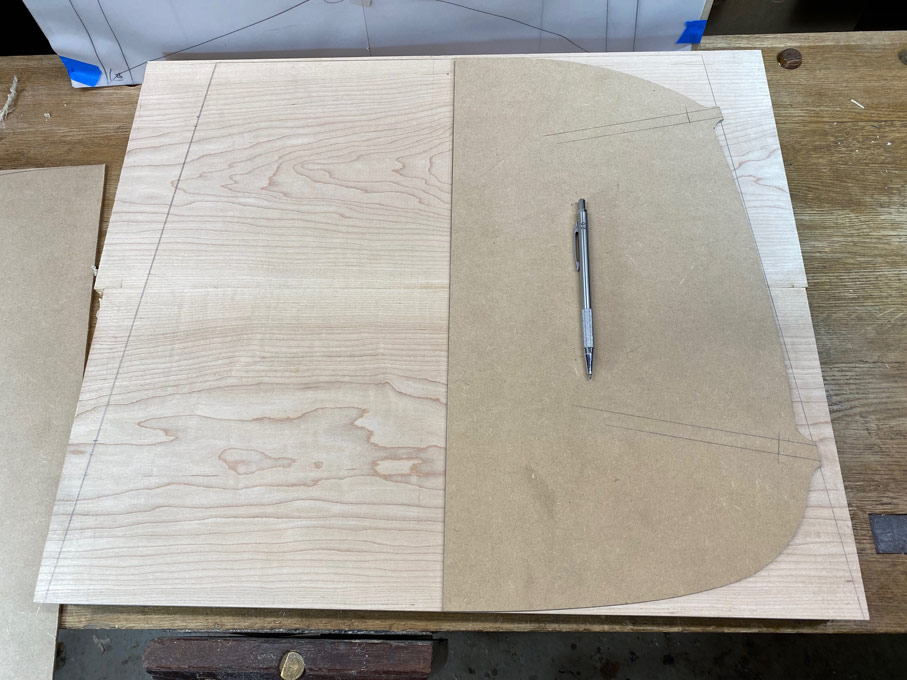
A little jack-planning to flatten the underside of the seat blanks ..
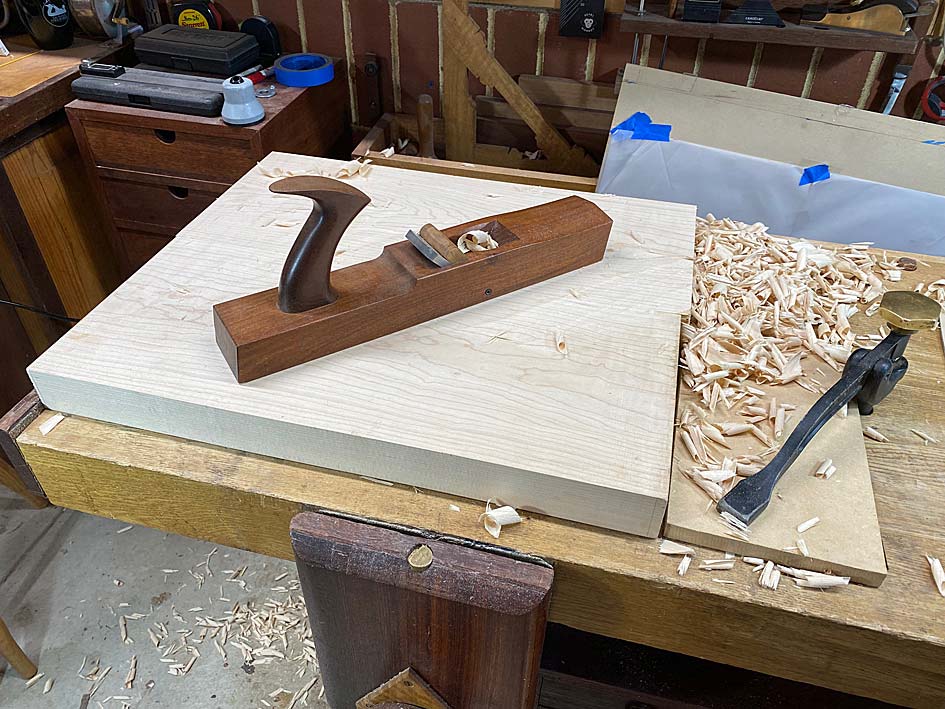
These are now sawn to shape ...
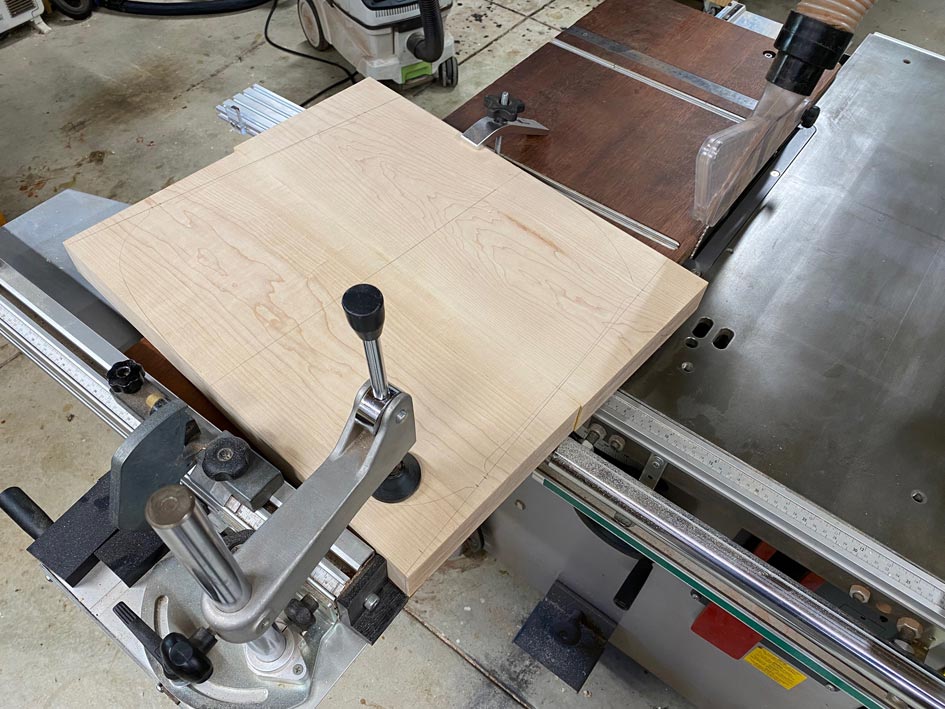
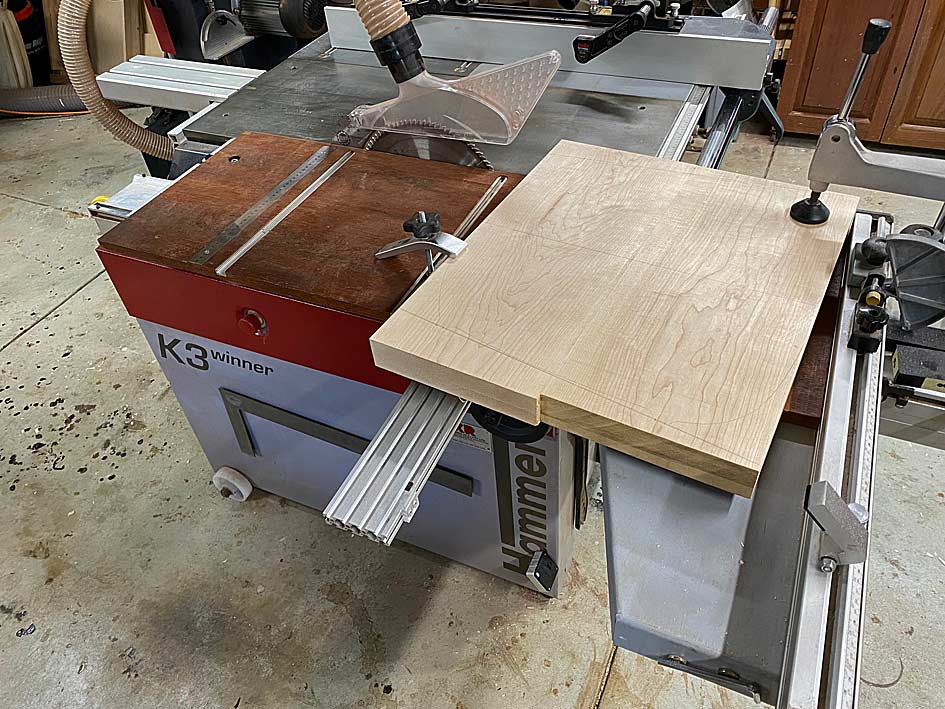
After this was done it became apparent just how the first shaping of the chairs differed from the DC09 design. Here is the first chair along with two legs. In the background can be seen the plan I had made for that build ...
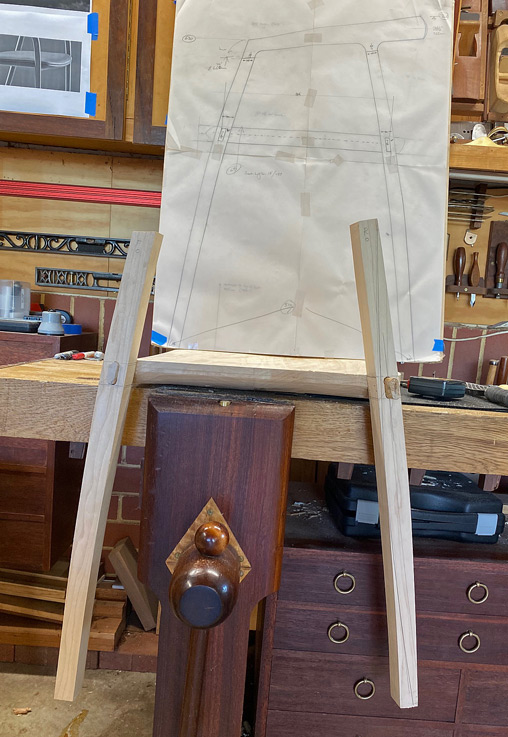
It looks quite good, with the angles and spacings appearing correct. In fact, they are quite different from the DC09. Below is the DC09 seat below the first seat. You can see the positioning of the legs ..
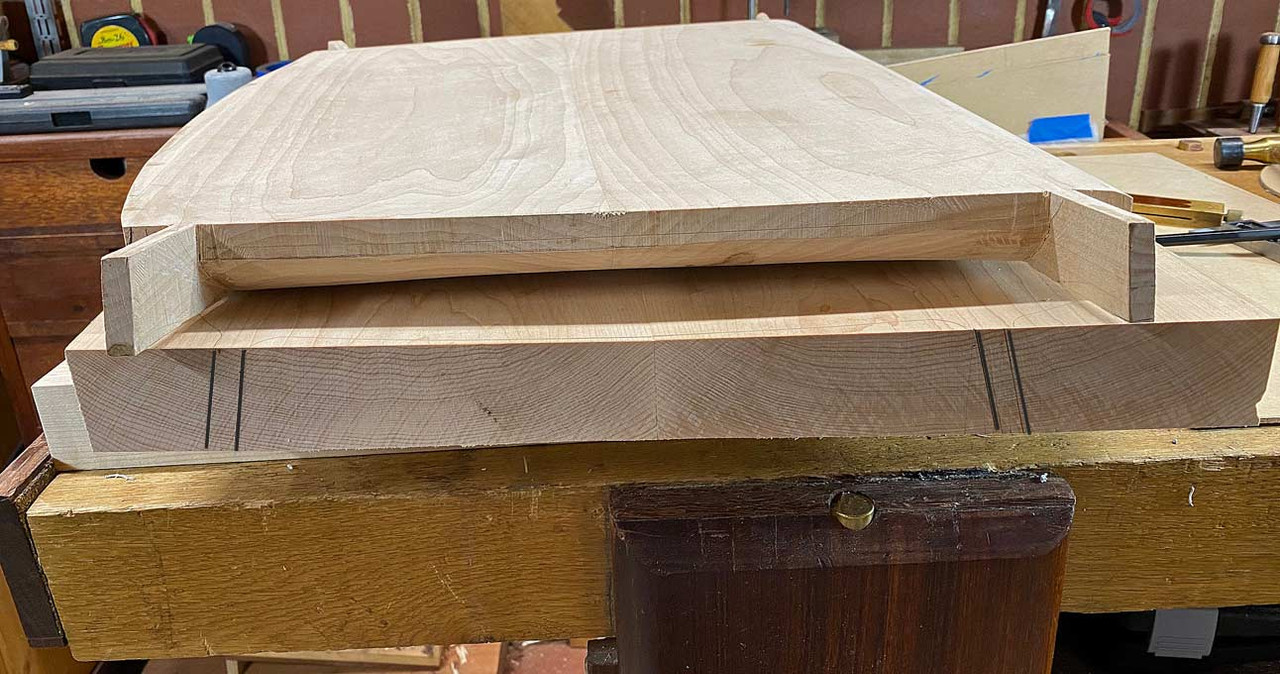
Before I dominoed the mortices, the legs were mocked up to be sure of the angles. I discovered that they should be at 14 degrees and not 10 degrees, as they had been before. In the top right corner you can see a DC09 for comparison ...
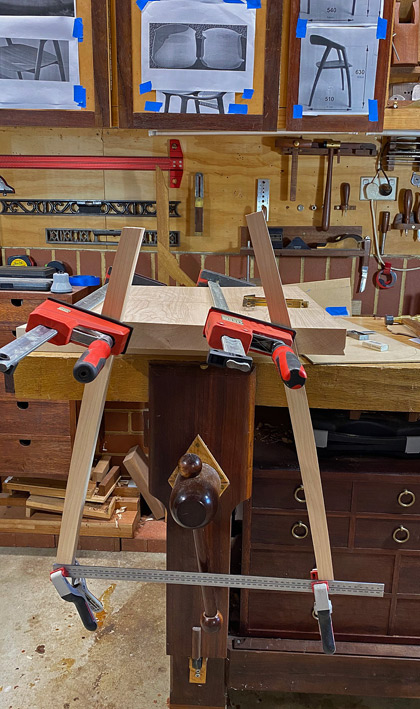
Guides for 14 degrees ...
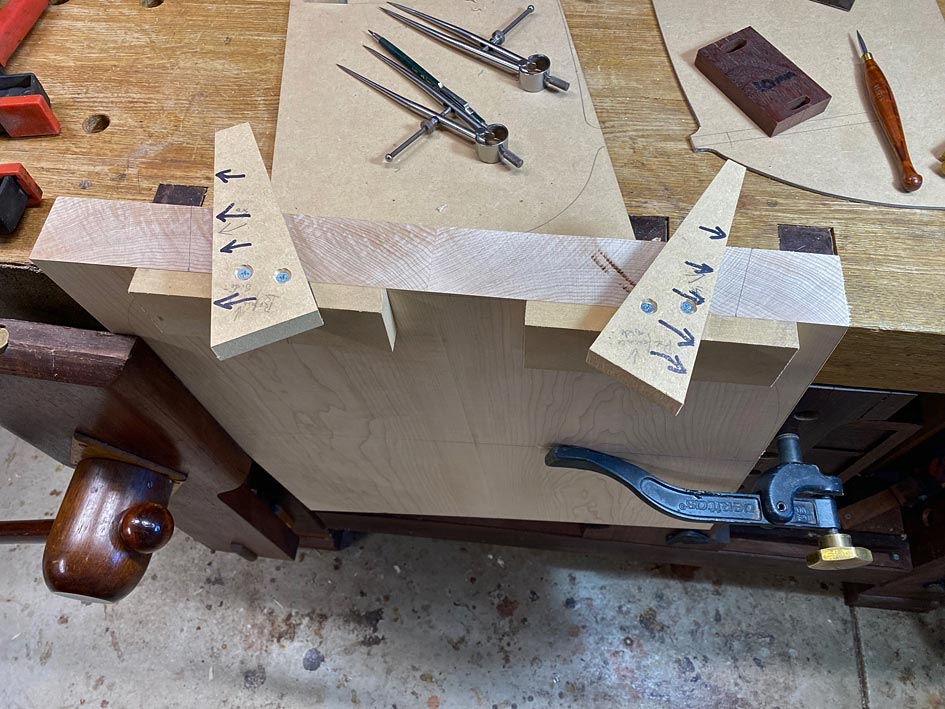
Marked and morticed ...
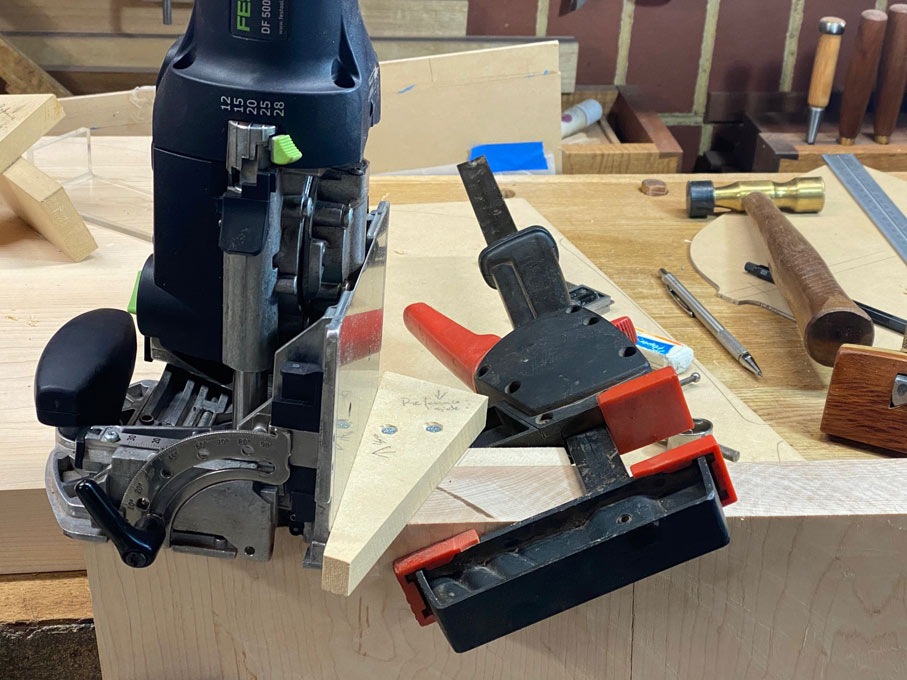
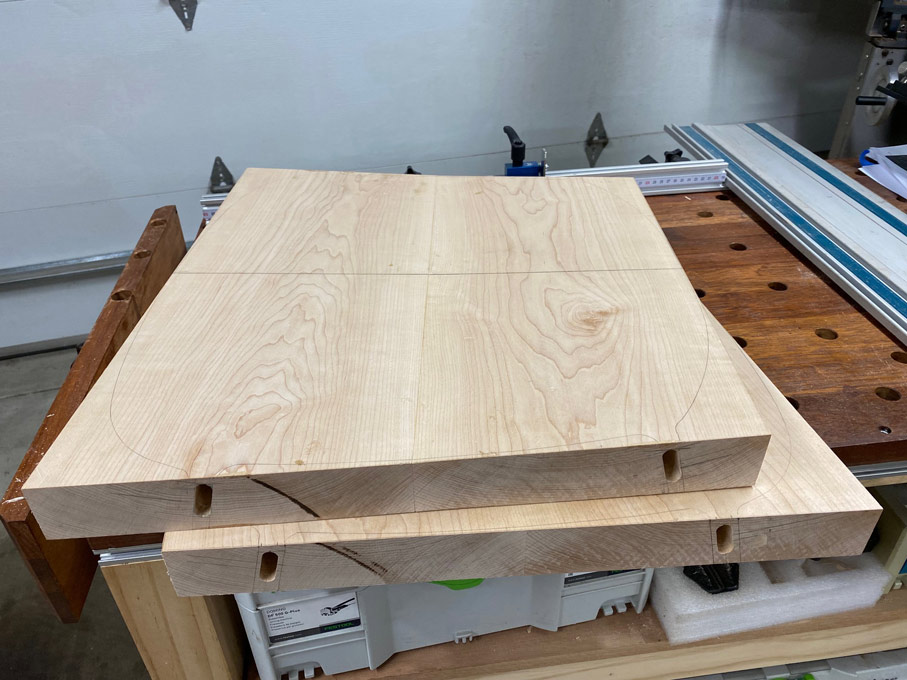
Tenons were made on the router table ...
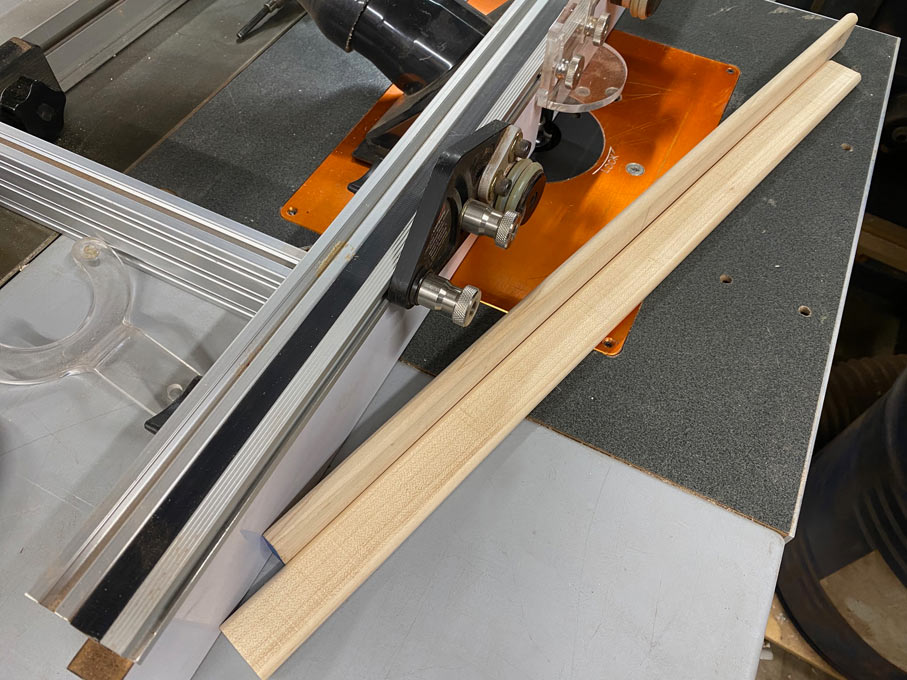
All is looking right so far ...
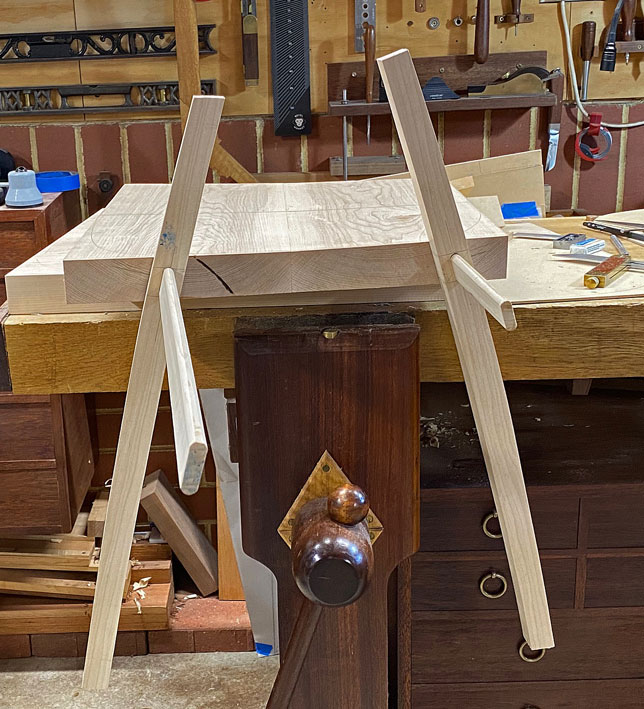
The rule for chair backs is that thy need to allow for a lean of about 90-95 degrees. I have been thinking about this but decided to set aside this area for later. The priority is to get the seat shape correct - in three dimensions. - and its relationship with the legs (which were shaped in the first build - they are substantially correct, other than the upper ends being around 28mm against the - estimated - 40mm of the DC09. I will decide on whether to keep or replace these later). I have left the legs 1" longer in the lower half to adjust the tilt of the seat (the seat sits 18" off the ground and the ones I made previously are 19" in this respect).
I did stand the old chair along the table, and noted how low the arm rests were in reality - actually an ideal height for comfort. I do have some ideas how they may be "improved" aesthetically .... but this for later.
All advice gratefully received.
Regards from Perth
Derek
Last edited: