I picked up a couple of bronze castings a while back. I did a bit on the bullnose then put it down for a while busy with real life. Lots of work on the house done, I decided to use my karma points to spend some time doing the shed up a bit. Racking and lights, a massive tidy up and a new 'metalworking bench' made out of my old table from my mums when I was a kid and all of a sudden I was cracking on with the little bullnose again. But now I was sat by a window with a fag on the go, pint of cider at hand and just a minute on the wireless. Top shout. Lovely.
Off we go then. Lots of pics. Be warned. There will be a test at the end.
What did the tiny dog say?
A little ruff probably covers it...
Still, on with trying to get a fair reference surface. Started with the sole.
Roughed out the top, the ears (ears!? horns? no idea). and the bed. The bed's fairly tricky it's a bit cramped and also, probably more pertinent, I'm a bit clueless.
By this point I was getting fancy and knocked up a bit of wood to hold the body to do the sides. I improved it a bit later with some dog hole type dowel improvised clamps. Actually it works really well. Turn the body over, move the dowell to a different hole. Simple stuff but effective. Yes, the Mark 1 bendy nail was a bit lazy, you got me there.
Some stubborn casting pitting and I was smashing it to bits with a turnip. Grrrrr.
One of the things I've found is you have to prepare to leave off before it happens if you see what I mean. Now I'm a semi-professional plane maker(...) I know all about scratch patterns. Judging when to leave off and go up a grade on the files so you take just enough off but not too much with the next cut is a dark art. Not so vital at this stage but we're getting there.
You can see the pitting at the back, there's one on the exact same spot on the other side. Taking off a fair bit of metal either side just to get these two spots out I (briefly) considered drilling a hole and interference fitting some copper rod. At one point tbh, if I'd had some copper rod and a decent accurate pillar drill I'd have done it and called it a design feature.
Anyhoo.
I knew the curved bit above the bed was not square across it's face. It's marked out in red sharpie in an earlier photo. I hadn't realised how much it was out, a good 2 or 3 mm, a huge amount by any decent standards. Doesn't look too bad from here.
When getting on to the nervy stages of opening the mouth there was a big discrepancy. In a plane that's only really useful square that's not good. Still. Spotted and remedied.
I got a bit worried at this point how I was going to approach the mouth and not wreck the work I'd done on the bed. With silent thanks once more to Andy T and the promise of a pint bought at some point, I dug out the lil' Eclipse. :wink:
Loads more to do, the sides need sorting and I haven't even approached the infil but its going ok.
So, as promised. Test time! Woop.
Q1. I'm aiming for a narrow mouth. How vital that it's very narrow for a bullnose?
Q2. I'm wondering about brazing a very thin plate of o1 plate to the sole. Never brazed much but chicken before. Is it feasible, favourable , advisable or would an expert planemaker like me who just pretends to be an silly person be better off leaving the sole bronze?
Q3. Taking into account your answer to Q2, is there a definite reason for doing so?
Cheers guys, sorry for the long post, hope I didn't bore you to death. As always I am very glad and thankful of any expertise you can pass my way.
Cheers as always.
Chris.
Off we go then. Lots of pics. Be warned. There will be a test at the end.
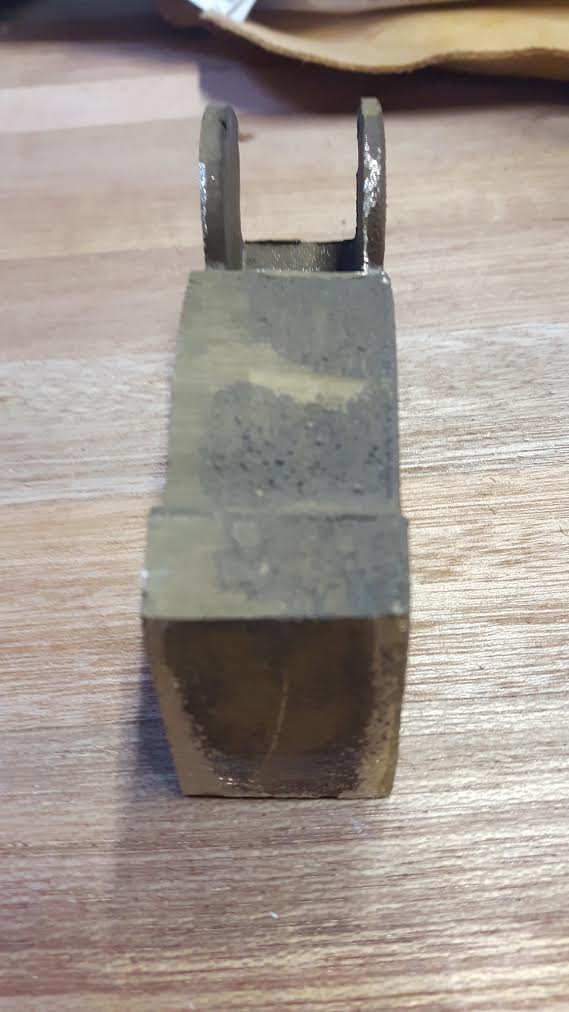
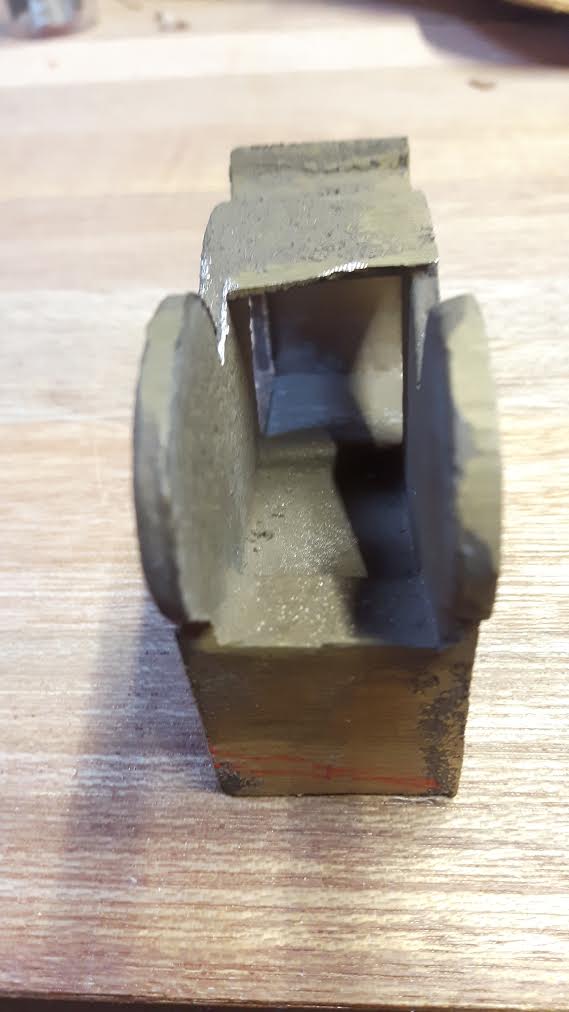
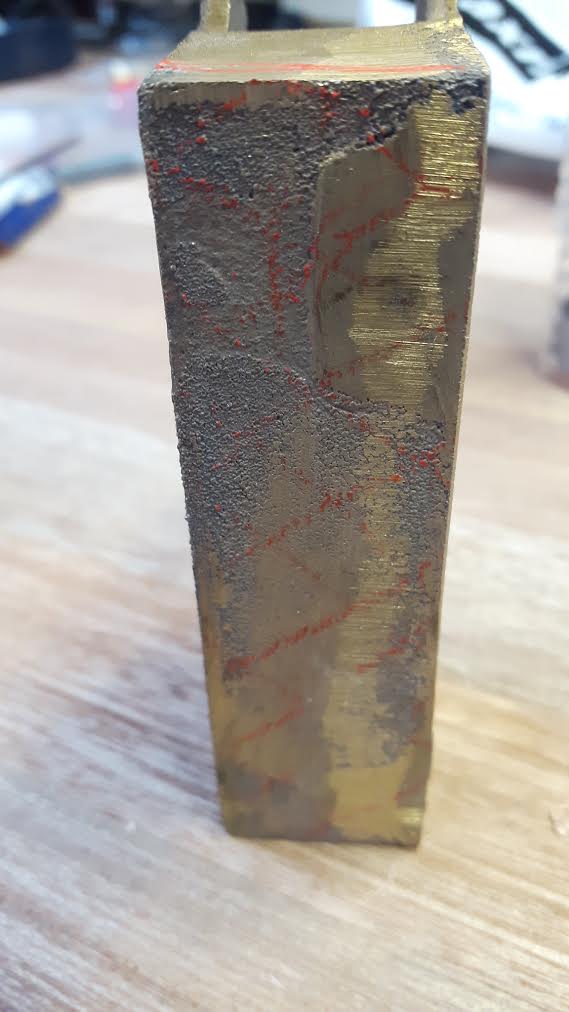
What did the tiny dog say?
A little ruff probably covers it...
Still, on with trying to get a fair reference surface. Started with the sole.
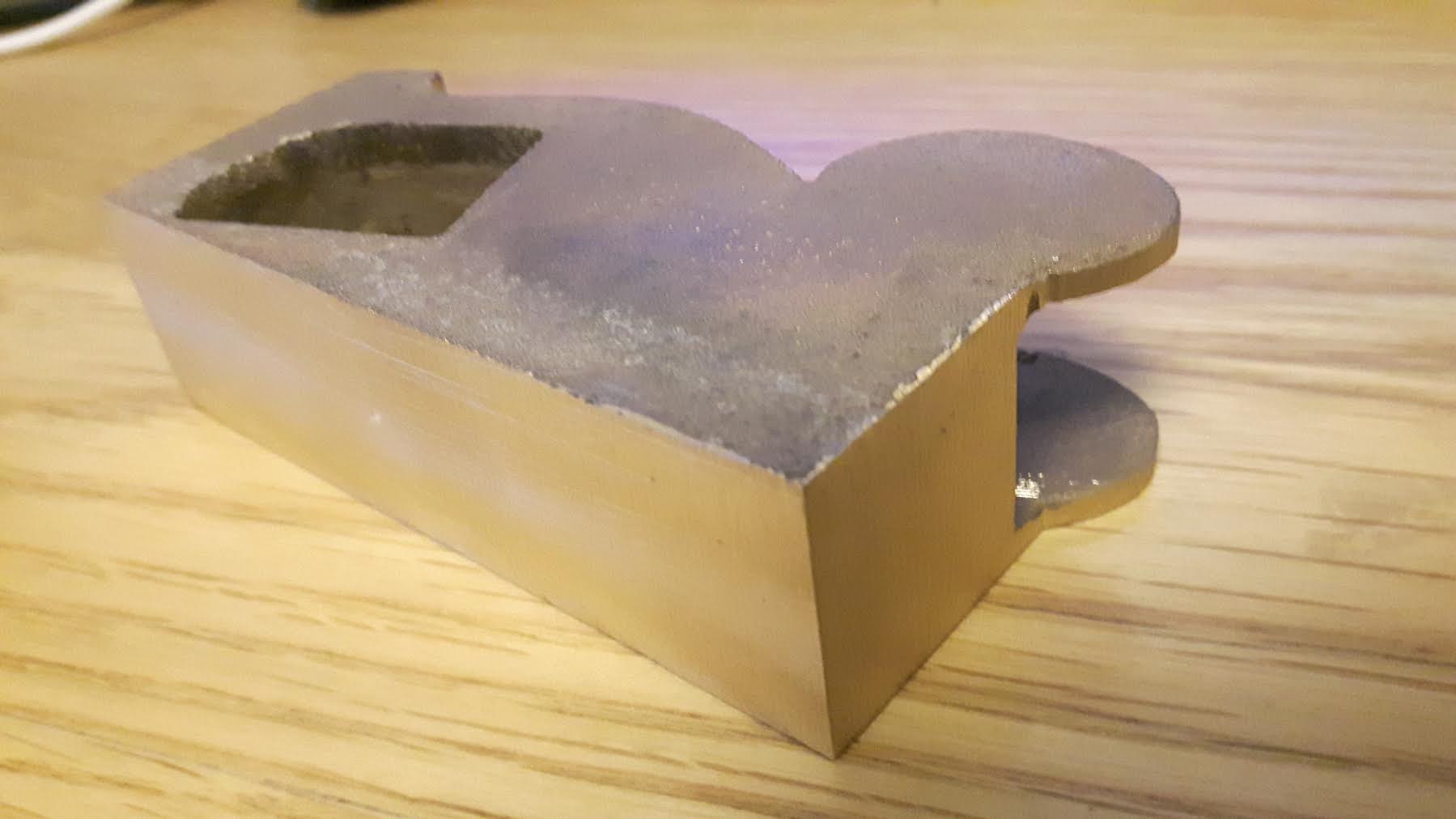
Roughed out the top, the ears (ears!? horns? no idea). and the bed. The bed's fairly tricky it's a bit cramped and also, probably more pertinent, I'm a bit clueless.
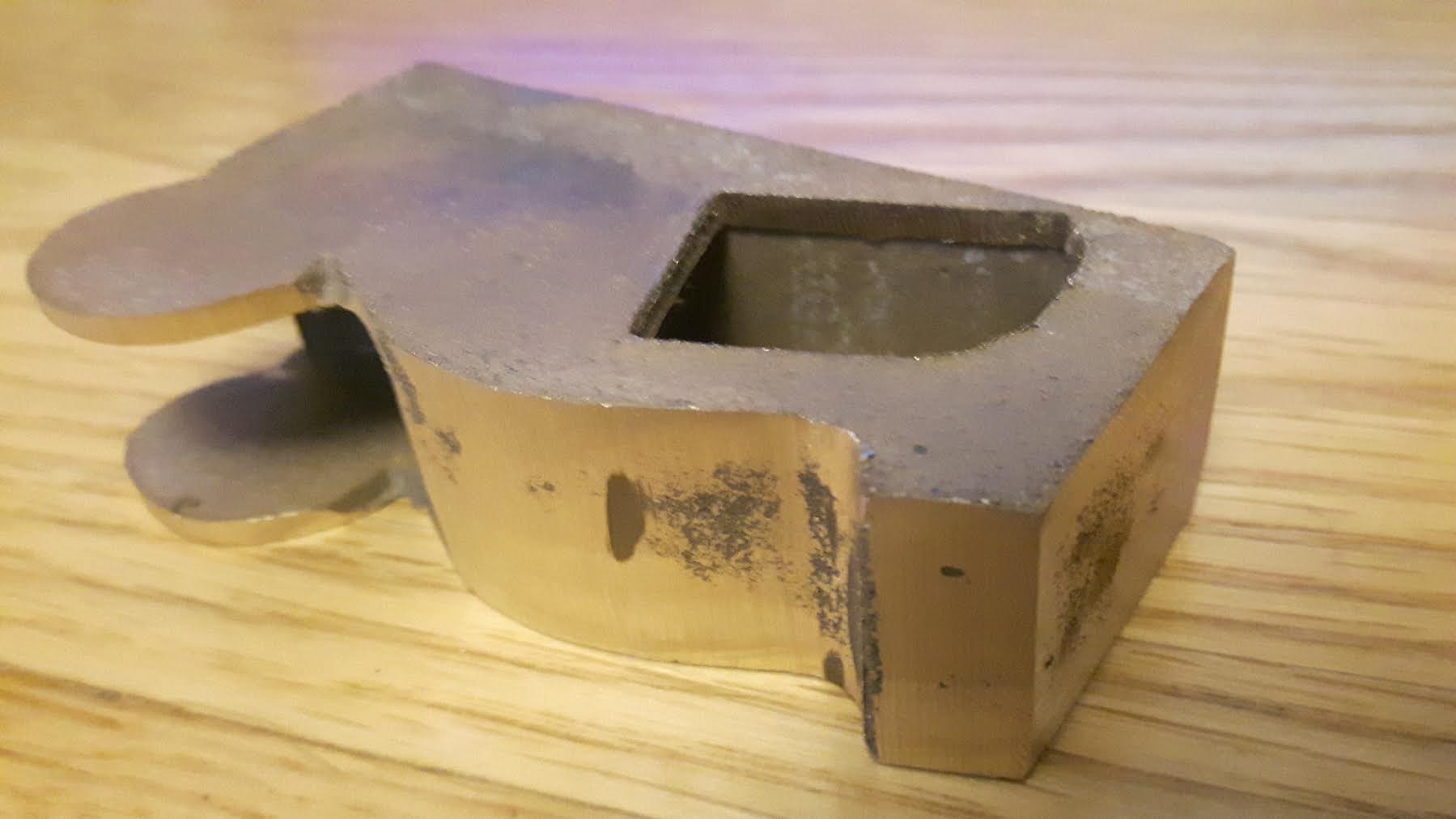
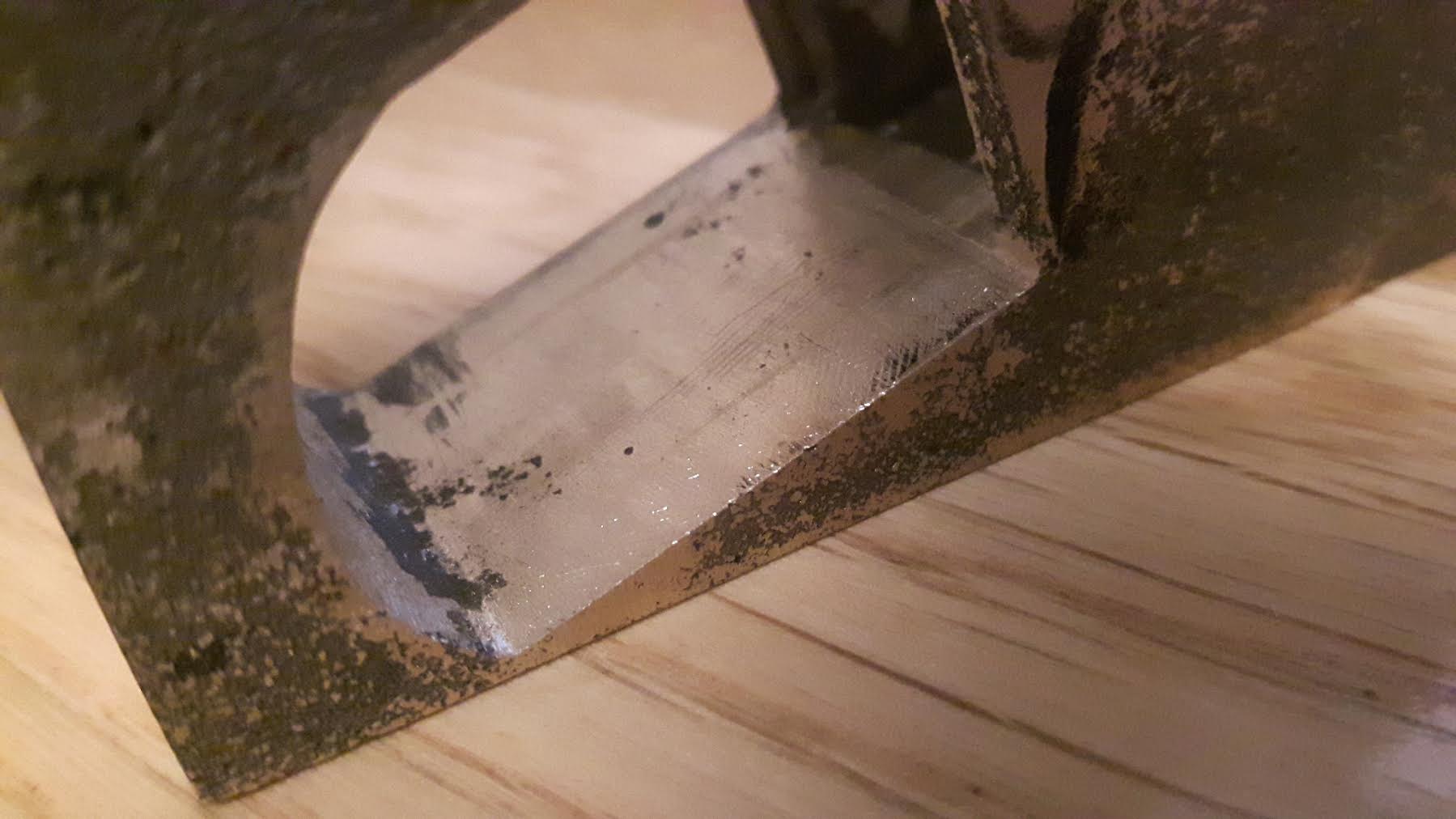
By this point I was getting fancy and knocked up a bit of wood to hold the body to do the sides. I improved it a bit later with some dog hole type dowel improvised clamps. Actually it works really well. Turn the body over, move the dowell to a different hole. Simple stuff but effective. Yes, the Mark 1 bendy nail was a bit lazy, you got me there.
Some stubborn casting pitting and I was smashing it to bits with a turnip. Grrrrr.
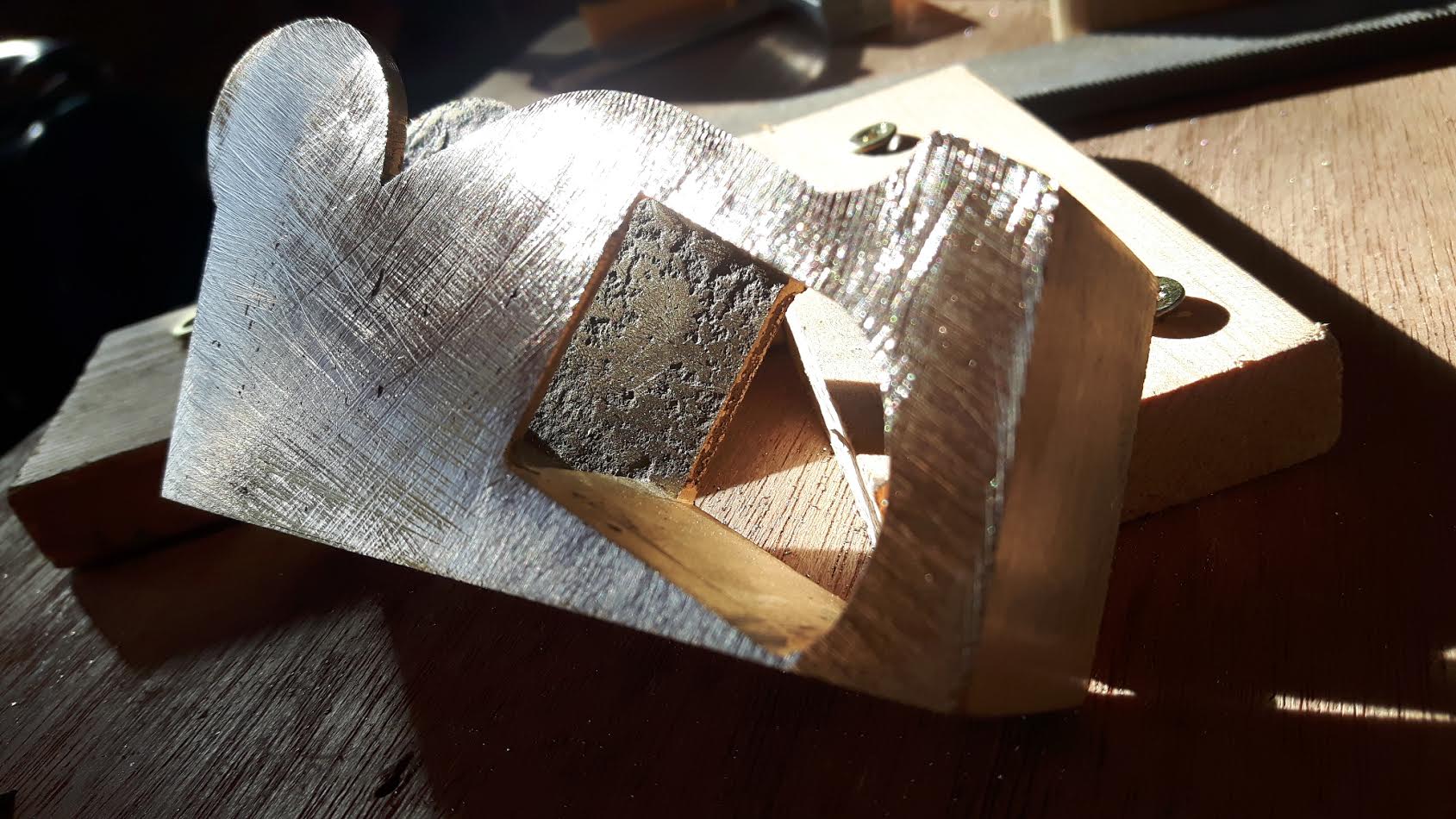
One of the things I've found is you have to prepare to leave off before it happens if you see what I mean. Now I'm a semi-professional plane maker(...) I know all about scratch patterns. Judging when to leave off and go up a grade on the files so you take just enough off but not too much with the next cut is a dark art. Not so vital at this stage but we're getting there.
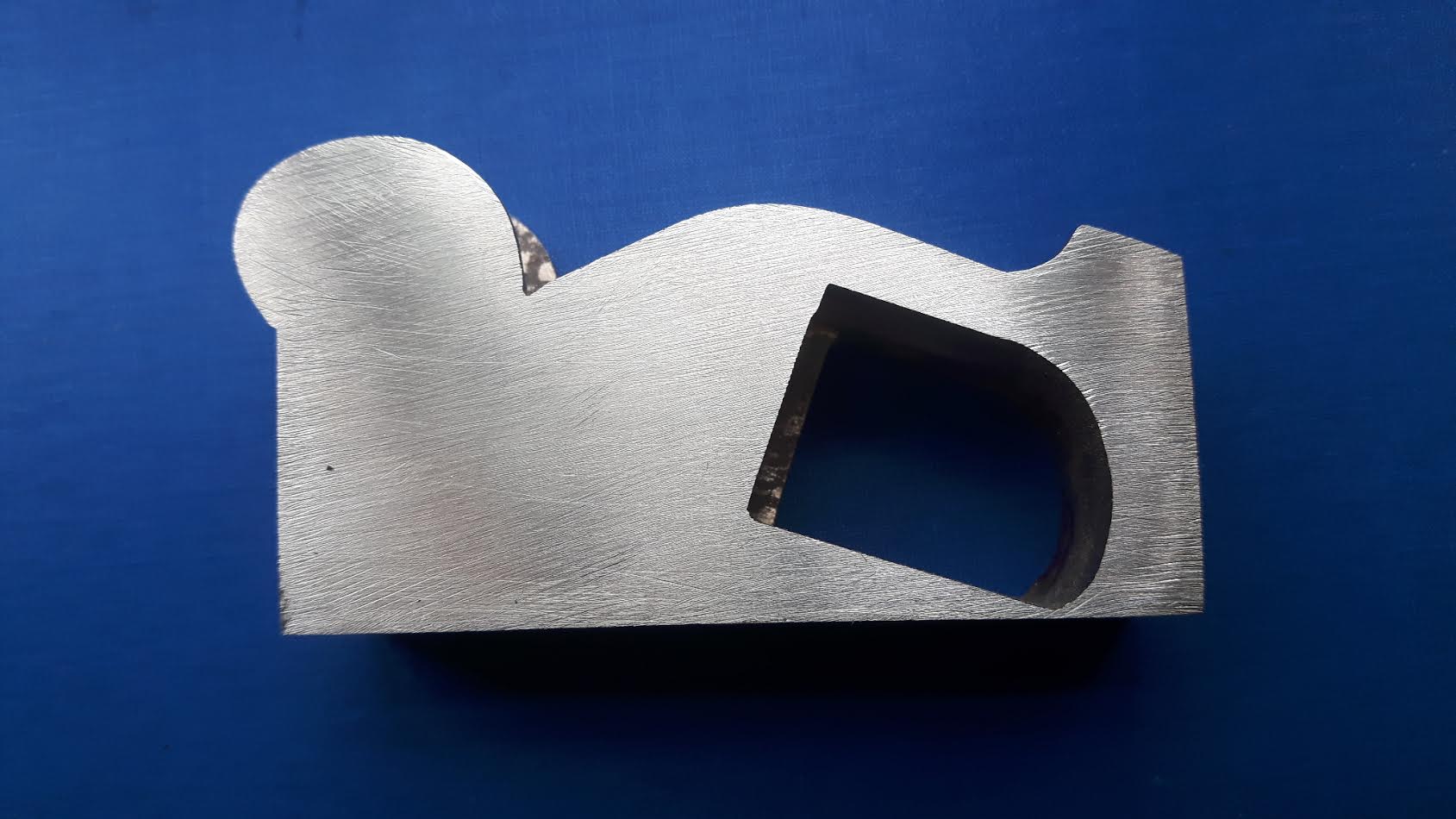
You can see the pitting at the back, there's one on the exact same spot on the other side. Taking off a fair bit of metal either side just to get these two spots out I (briefly) considered drilling a hole and interference fitting some copper rod. At one point tbh, if I'd had some copper rod and a decent accurate pillar drill I'd have done it and called it a design feature.
Anyhoo.
I knew the curved bit above the bed was not square across it's face. It's marked out in red sharpie in an earlier photo. I hadn't realised how much it was out, a good 2 or 3 mm, a huge amount by any decent standards. Doesn't look too bad from here.
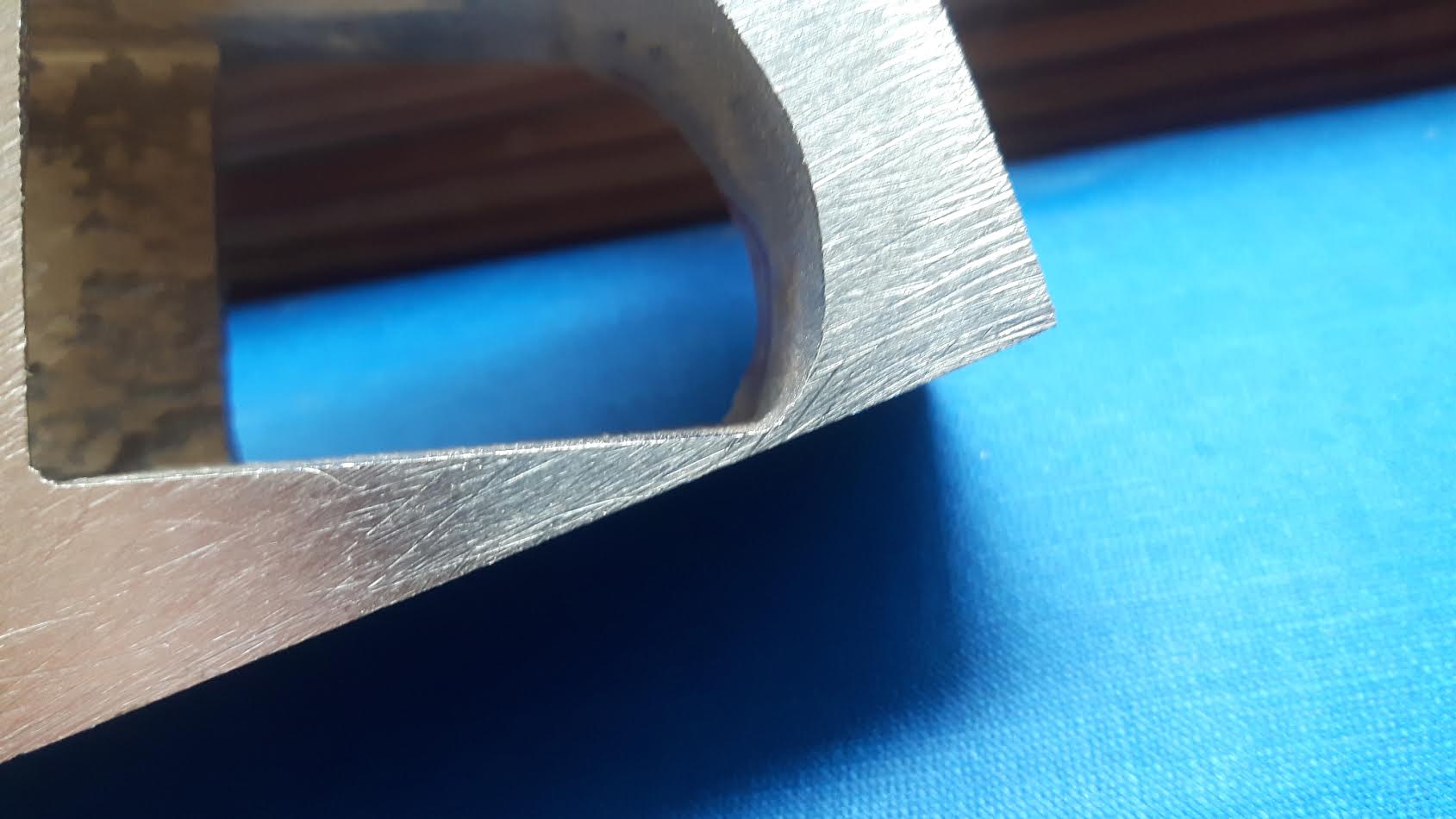
When getting on to the nervy stages of opening the mouth there was a big discrepancy. In a plane that's only really useful square that's not good. Still. Spotted and remedied.
I got a bit worried at this point how I was going to approach the mouth and not wreck the work I'd done on the bed. With silent thanks once more to Andy T and the promise of a pint bought at some point, I dug out the lil' Eclipse. :wink:
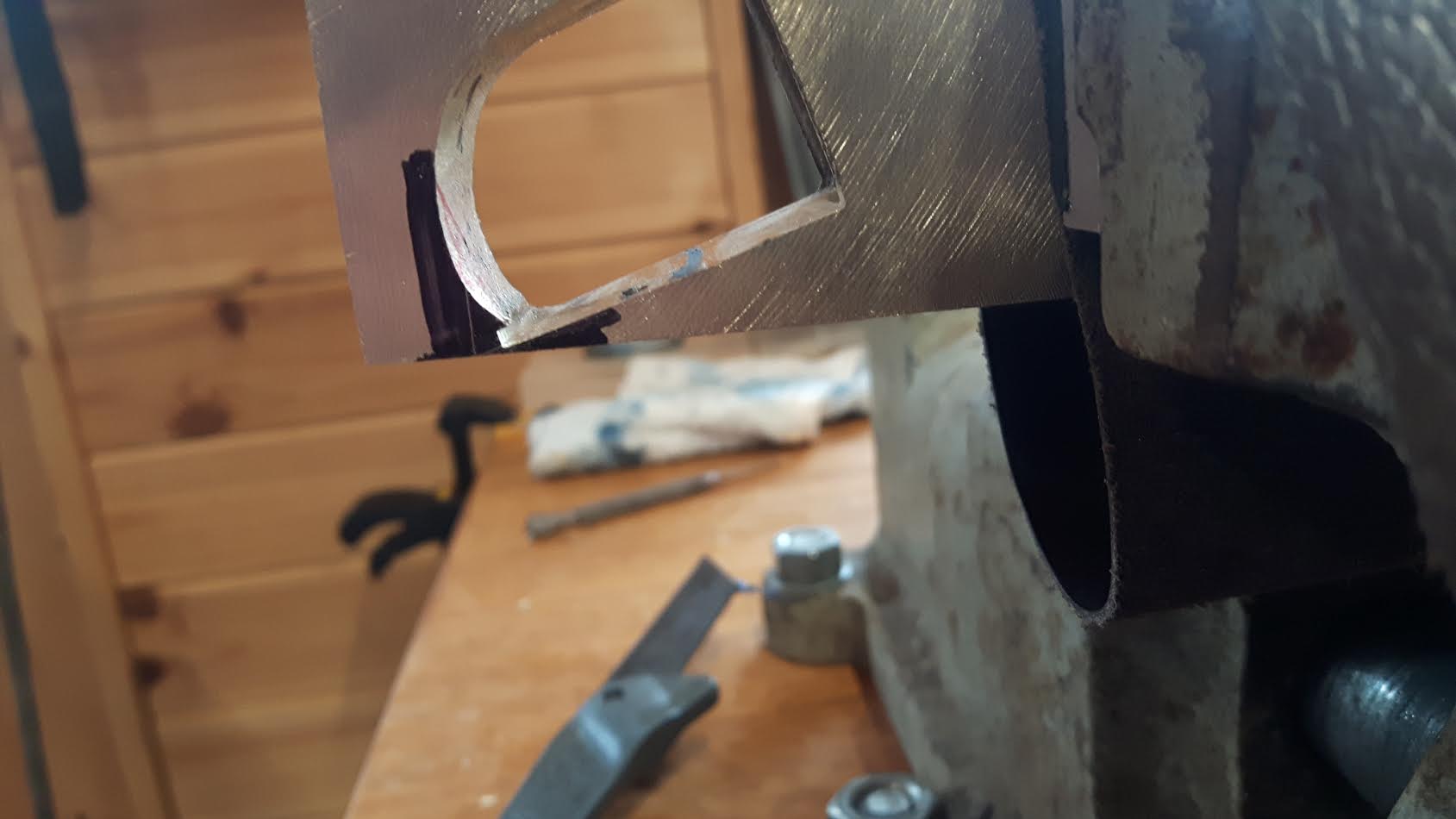
Loads more to do, the sides need sorting and I haven't even approached the infil but its going ok.
So, as promised. Test time! Woop.
Q1. I'm aiming for a narrow mouth. How vital that it's very narrow for a bullnose?
Q2. I'm wondering about brazing a very thin plate of o1 plate to the sole. Never brazed much but chicken before. Is it feasible, favourable , advisable or would an expert planemaker like me who just pretends to be an silly person be better off leaving the sole bronze?
Q3. Taking into account your answer to Q2, is there a definite reason for doing so?
Cheers guys, sorry for the long post, hope I didn't bore you to death. As always I am very glad and thankful of any expertise you can pass my way.
Cheers as always.
Chris.