swagman
Established Member
Last week when I was sorting through some of my earlier made backsaws, and took some new photo's.
18 inch tooth line; handle wood is American Black Walnut.
16 inch tooth line; handle wood is Tasmanian Tiger Myrtle.
18 inch tooth line, with a D8 style extension of the saw plates heel.
The slot for along the bottom rail was cut to a depth of 5mm using 40mm slitting blade mounted to a router table. Note; the top mounting flange on the slitting saw holder I use has an OD of 30mm.
For cutting the slot around the cheek line and spine mortise I normally use a 50mm slitting blade to achieve an initial slot depth of 10mm. The remaining depth of cut was completed using a backsaw of matching kerf width. (tooth set removed)
These type of slitting blades are designed to be run at low speed to minimize vibration. The greater the OD of the slitting blade, the greater the potential for vibration to occur. Personally I prefer not to exceed an OD of 50mm. Excessive vibration will result in the slot turning out oversize.
The following shows the type of 1/2 shank holder I use. The graduated steps allows the user a greater choice of inner bore sizes that are common within the range of slitting blades available.
https://encrypted-tbn0.gstatic.com/imag ... 1syzPHTczh
The gauge of saw plate used on backsaws can vary in thickness from 0.015, 0.018, 0.020. 0.025, to 0.032 on large mitre box saws. As the backsaws depth and length are further increased, the saw maker should also incrementally increase the gauge of saw plate used. By doing so, his actions will mitigate the potential of heat distortion below the unsupported spine.
As I am working with both side and end grain to round over the saw handles profiles, I avoid the use of routers, preferring instead to use a variety of dedicated hand rasps. The following is one of those dedicated rasps sold by Logier in France. http://www.hand-stitched-rasp-riffler.c ... -rasp.html
Further smoothing work is carried out using a range of sandpaper grit cut into thin strips for ease of use. Coats of Amber or Garnet Shellac are then included between each change in sandpaper grit, to effectively fill in, and generate a depth in top coat thickness over the handle woods face, side and end grains.
The Shellac I use is de-waxed, and is sold in flake form, ready for mixing with Denatured Alcohol. (100% Methylated Spirits).
18 inch tooth line; handle wood is American Black Walnut.
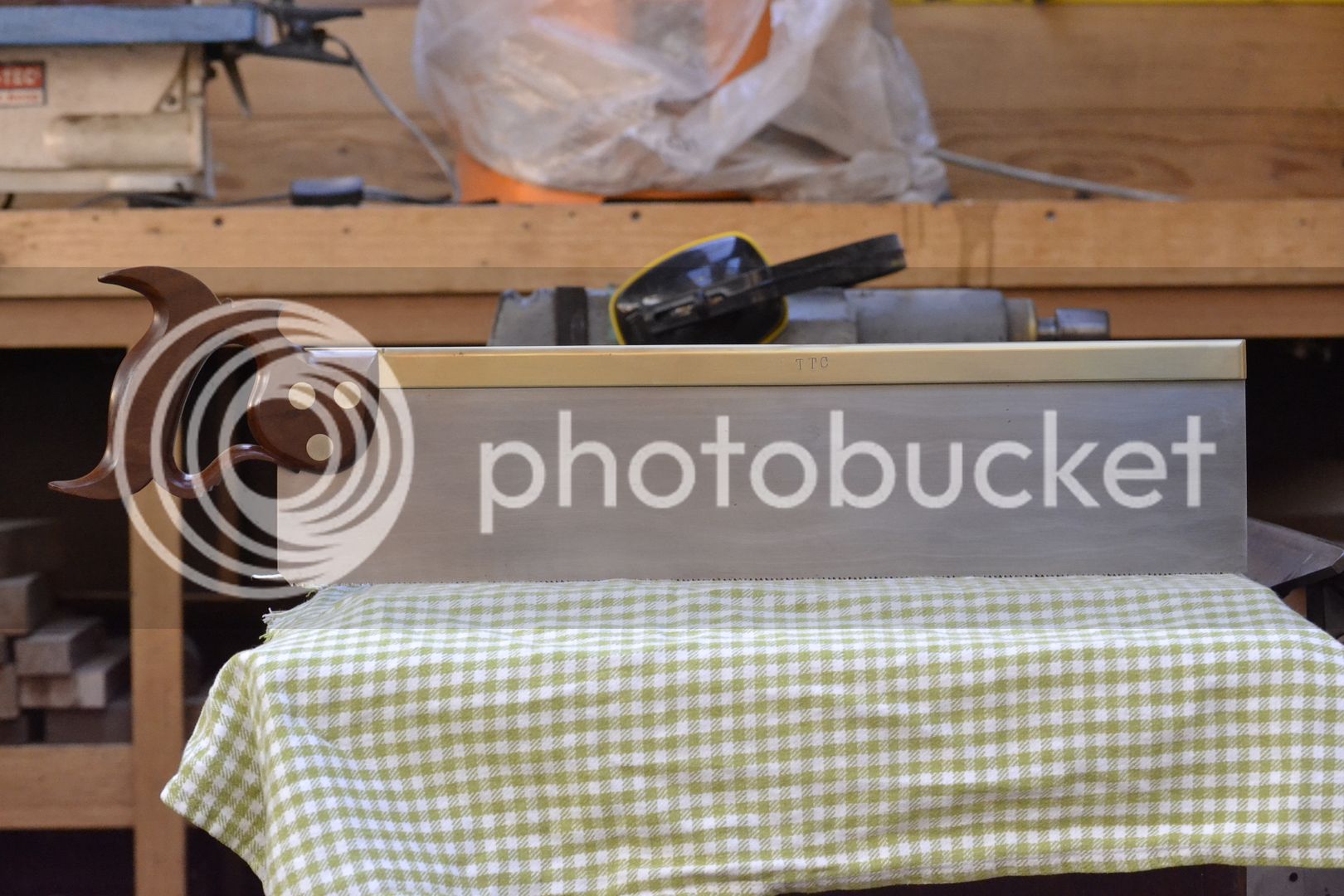
16 inch tooth line; handle wood is Tasmanian Tiger Myrtle.
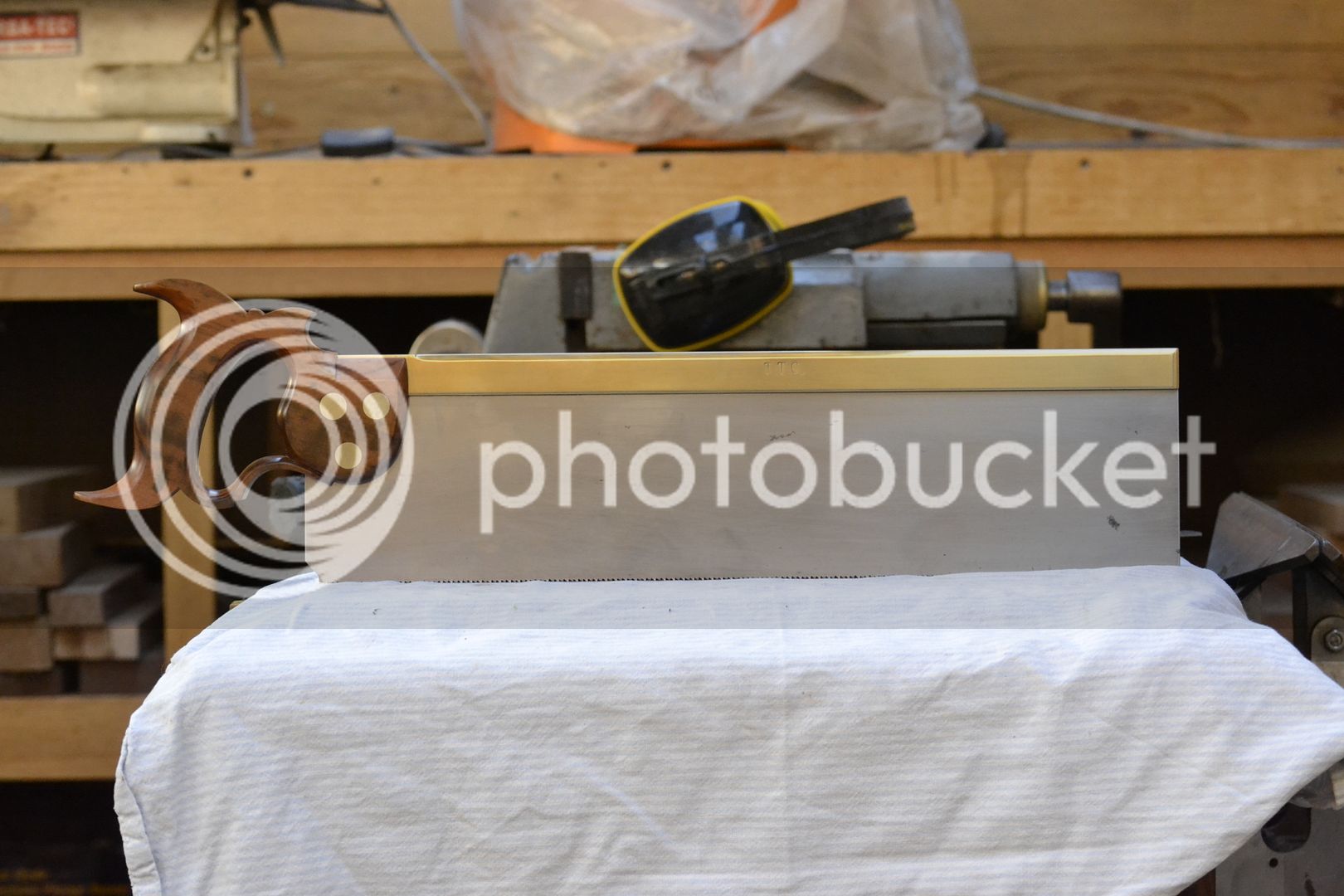
18 inch tooth line, with a D8 style extension of the saw plates heel.
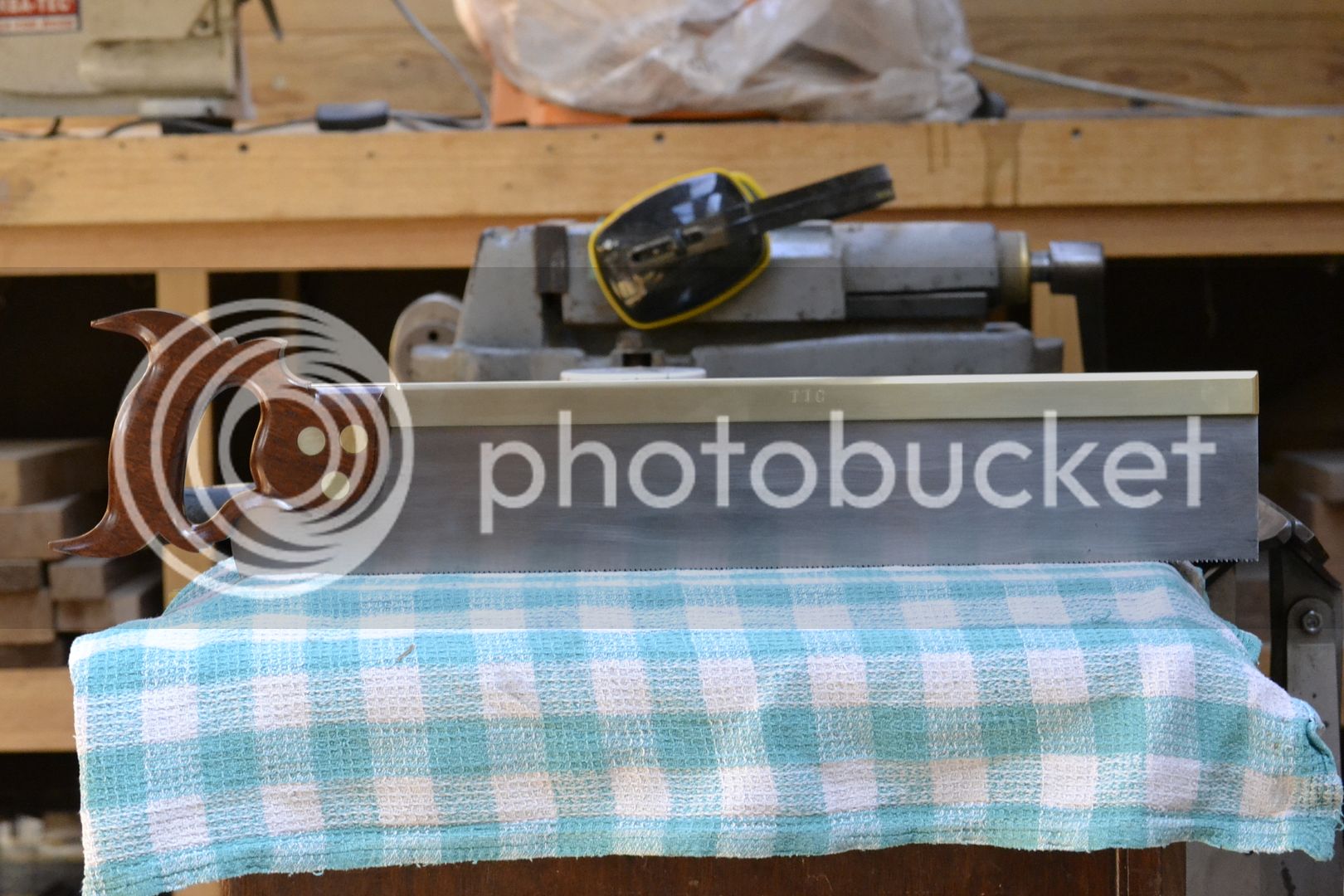
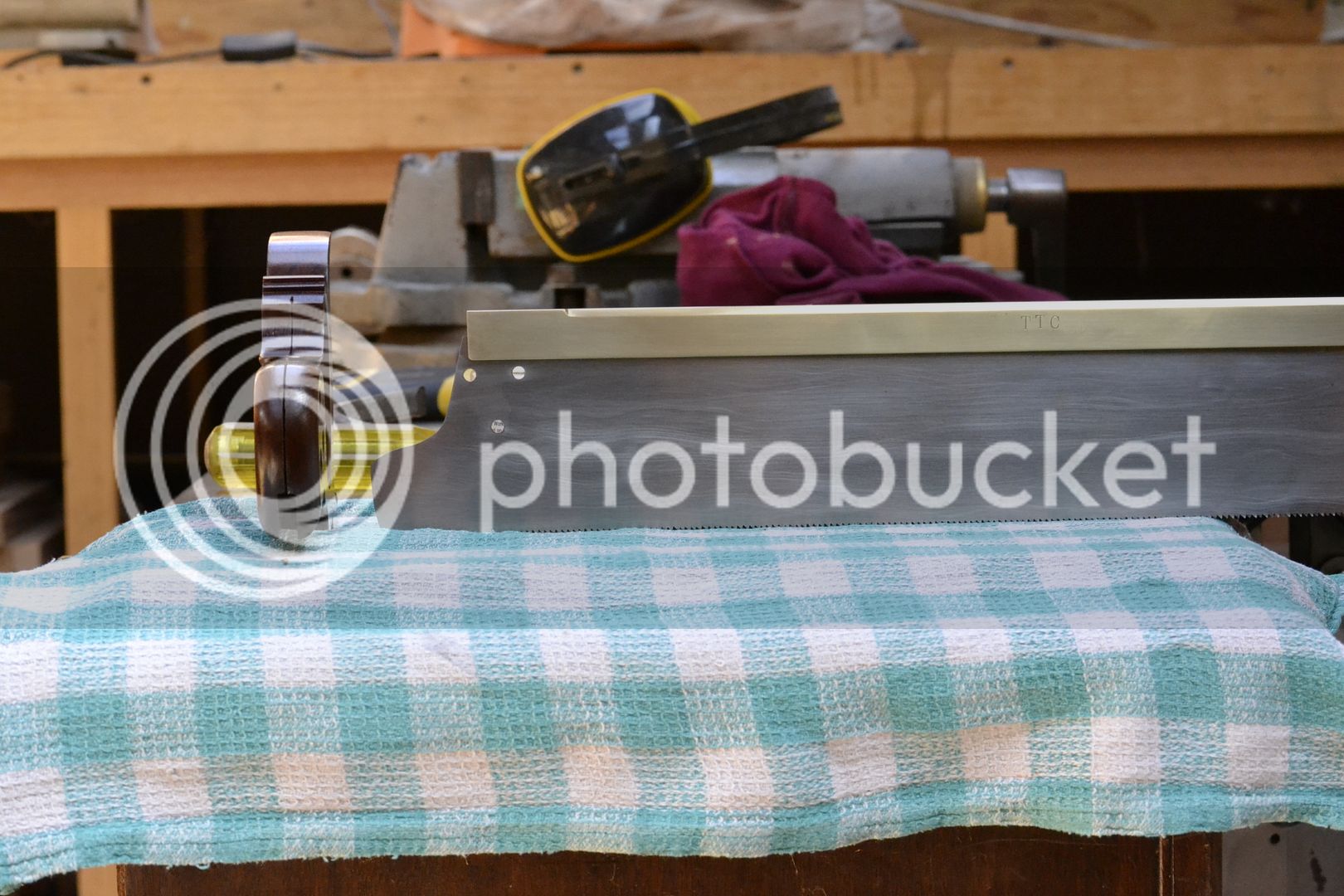
The slot for along the bottom rail was cut to a depth of 5mm using 40mm slitting blade mounted to a router table. Note; the top mounting flange on the slitting saw holder I use has an OD of 30mm.
For cutting the slot around the cheek line and spine mortise I normally use a 50mm slitting blade to achieve an initial slot depth of 10mm. The remaining depth of cut was completed using a backsaw of matching kerf width. (tooth set removed)
These type of slitting blades are designed to be run at low speed to minimize vibration. The greater the OD of the slitting blade, the greater the potential for vibration to occur. Personally I prefer not to exceed an OD of 50mm. Excessive vibration will result in the slot turning out oversize.
The following shows the type of 1/2 shank holder I use. The graduated steps allows the user a greater choice of inner bore sizes that are common within the range of slitting blades available.
https://encrypted-tbn0.gstatic.com/imag ... 1syzPHTczh
The gauge of saw plate used on backsaws can vary in thickness from 0.015, 0.018, 0.020. 0.025, to 0.032 on large mitre box saws. As the backsaws depth and length are further increased, the saw maker should also incrementally increase the gauge of saw plate used. By doing so, his actions will mitigate the potential of heat distortion below the unsupported spine.
As I am working with both side and end grain to round over the saw handles profiles, I avoid the use of routers, preferring instead to use a variety of dedicated hand rasps. The following is one of those dedicated rasps sold by Logier in France. http://www.hand-stitched-rasp-riffler.c ... -rasp.html
Further smoothing work is carried out using a range of sandpaper grit cut into thin strips for ease of use. Coats of Amber or Garnet Shellac are then included between each change in sandpaper grit, to effectively fill in, and generate a depth in top coat thickness over the handle woods face, side and end grains.
The Shellac I use is de-waxed, and is sold in flake form, ready for mixing with Denatured Alcohol. (100% Methylated Spirits).