swagman
Established Member
Received this 2nd hand natural sharpening stone from the U.K this morning.
Under all that old oil and grime there are features that indicate its most likely crystaline novaculite in structure, an oil stone, either Washita or Arkansas.
The same stone after being flattened reveals much more of the stones natural features.
During the flattening process, indications are, its a hard stone, slow slurry releasing, most likely pointing to its identity as being Arkansas.
To validate that fact, requires some mathematics to work out the stones specific gravity. (SG)
Weight of the stone = 515 grams.
Mass ( 20.1 cm x 4.7cm x 2.3cm) = 217.28 cm3
515/ 217.28 = 2.37 g/cm3
SG = 2.37.
Using the following site as a reference; http://www.danswhetstone.com/stone_grades_101.htm.
It identifies the stone as being within the Hard Arkansas range of 2.30 - 2.45 SG / 800 - 1000 grit.
Stewie;
Under all that old oil and grime there are features that indicate its most likely crystaline novaculite in structure, an oil stone, either Washita or Arkansas.
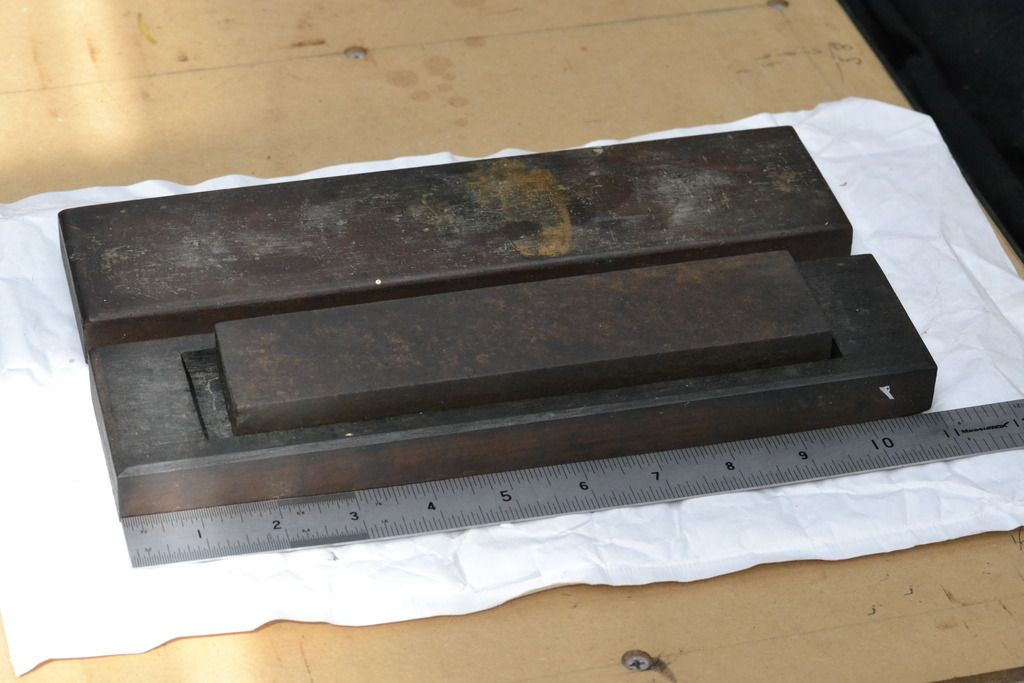
The same stone after being flattened reveals much more of the stones natural features.
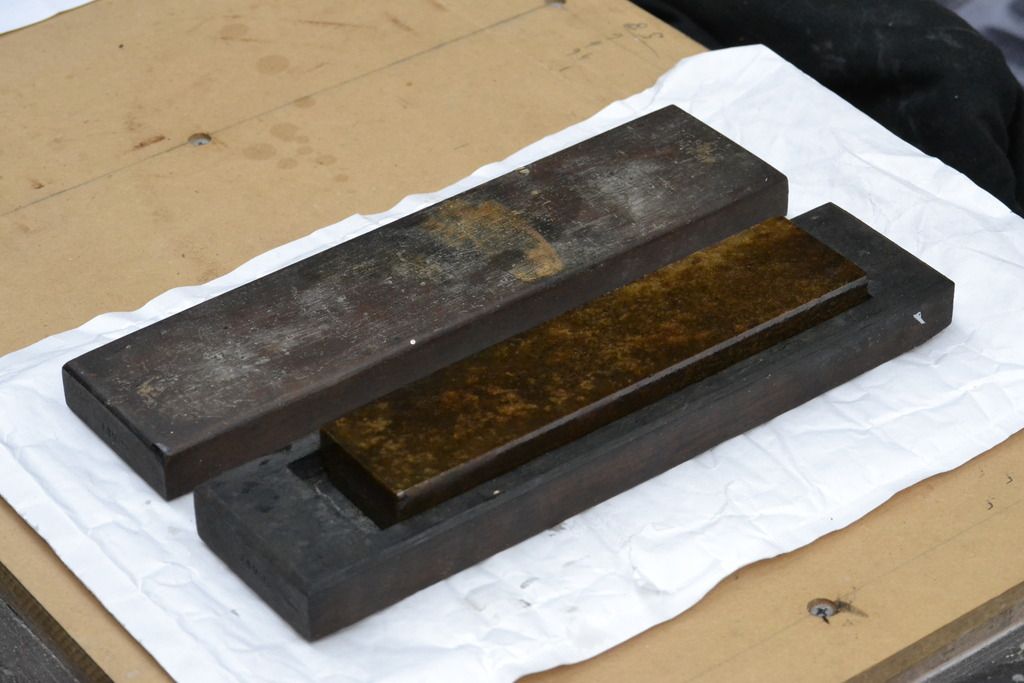
During the flattening process, indications are, its a hard stone, slow slurry releasing, most likely pointing to its identity as being Arkansas.
To validate that fact, requires some mathematics to work out the stones specific gravity. (SG)
Weight of the stone = 515 grams.
Mass ( 20.1 cm x 4.7cm x 2.3cm) = 217.28 cm3
515/ 217.28 = 2.37 g/cm3
SG = 2.37.
Using the following site as a reference; http://www.danswhetstone.com/stone_grades_101.htm.
It identifies the stone as being within the Hard Arkansas range of 2.30 - 2.45 SG / 800 - 1000 grit.
Stewie;