Hi folks
SWMBO has dictated that our new dining table MUST be completed before I can make a start on my competition entry....
I had a trip to the timber merchants with Brad today, and came back with this little lot:
I haven't done a "proper" sketch - I have the picture in my head, and you will see it progress over the next few days. I should have this finished by Sunday. Fingers crossed.
Anyway, the timber is a mixture of 1", 1 1/2" and 2" American Oak. We checked with the timber yard, who cofirmed that moisture content is between 9-11 %. So i'm happy to get on with machining straight away - no acclimatising for this little lot....
These 4 pieces will form the rails. I will be putting a cross rail underneath the table top between the two long rails, joined with through wedged mortices. The joints between rails and legs will be pinned mortice and tenon joints
The timber was nice and flat - no twist or cupping/bowing. So I passed it straight through the thicknesser. I then edge jointed each piece by hand
The Veritas twin screw vice is great at this sort of stuff - the piece in the vice is 6' long and it held it more than securely enough to joint the edge.
I then set the table saw for ripping to width - mainly to remove the small amount of sapwood present.
Treated the Metabo to a new Freud combi blade. Wish I hadn't bothered - it doesn't perform nearly as well as the one supplied with the saw, and the dust extraction has gone AWOL. :evil:
Anyway, onwards and upwards as they say.....
Ripped to width the rails were put to one side, and I turned my attention to the legs.
These pieces of 1 1/2" stock are to form the legs. I first crosscut the pieces to length
I was being a little lazy here - the stock was too long to be put on the saw for all crosscutting, so I did the first cut by hand on the bench, and the second on the table saw.
Once all pieces were thicknessed, jointed, ripped to width etc I ended up with 4 sets of these
Each leg will consist of 3 pieces laminated together. Therefore each glue surface was hand planed to remove twist, snipe, cupping/bowing etc. Ended up with all pieces planed and ready for clamping
I only managed to get two glued up - ran out of bloody clamps....
And that's as far as I got today. Tomorrow - glue up the other two legs and cut all four to size. Cut the mortice and tenon joints on rails and legs. Hopefully get the cross rail piece done.
Now it's time for one of these
Total time spent on project today - 6 hours
Cheers
Karl
SWMBO has dictated that our new dining table MUST be completed before I can make a start on my competition entry....
I had a trip to the timber merchants with Brad today, and came back with this little lot:
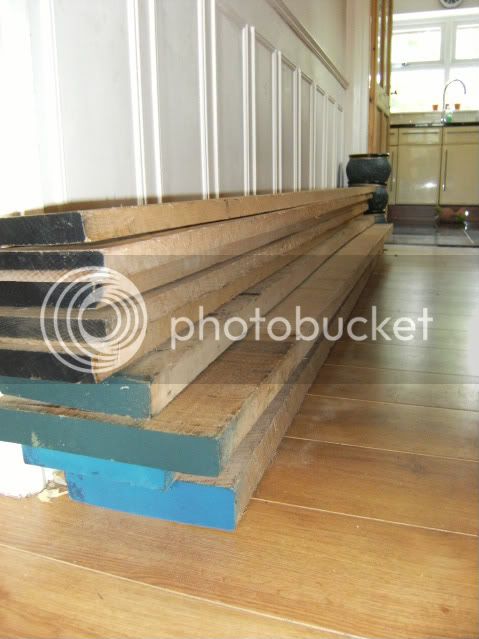
I haven't done a "proper" sketch - I have the picture in my head, and you will see it progress over the next few days. I should have this finished by Sunday. Fingers crossed.
Anyway, the timber is a mixture of 1", 1 1/2" and 2" American Oak. We checked with the timber yard, who cofirmed that moisture content is between 9-11 %. So i'm happy to get on with machining straight away - no acclimatising for this little lot....
These 4 pieces will form the rails. I will be putting a cross rail underneath the table top between the two long rails, joined with through wedged mortices. The joints between rails and legs will be pinned mortice and tenon joints
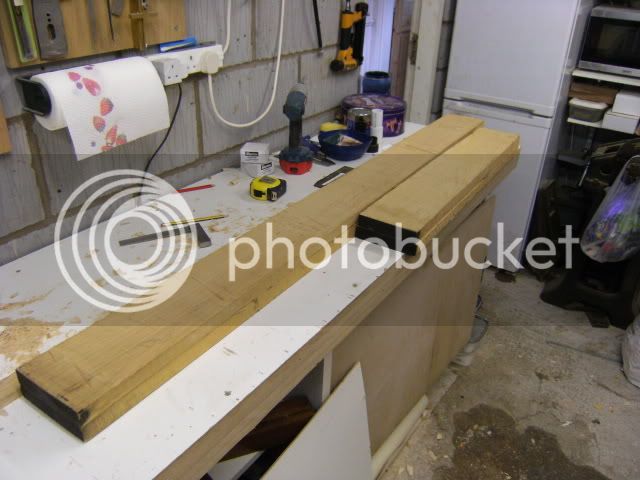
The timber was nice and flat - no twist or cupping/bowing. So I passed it straight through the thicknesser. I then edge jointed each piece by hand
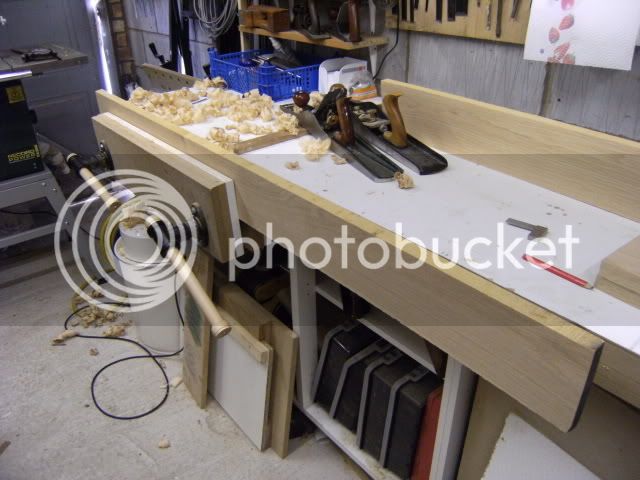
The Veritas twin screw vice is great at this sort of stuff - the piece in the vice is 6' long and it held it more than securely enough to joint the edge.
I then set the table saw for ripping to width - mainly to remove the small amount of sapwood present.
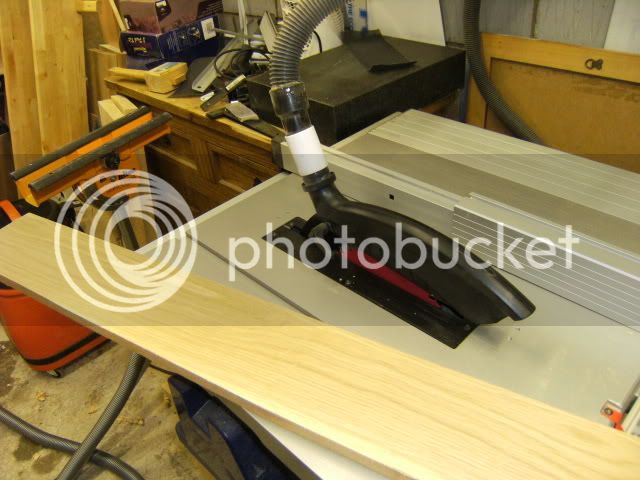
Treated the Metabo to a new Freud combi blade. Wish I hadn't bothered - it doesn't perform nearly as well as the one supplied with the saw, and the dust extraction has gone AWOL. :evil:
Anyway, onwards and upwards as they say.....
Ripped to width the rails were put to one side, and I turned my attention to the legs.
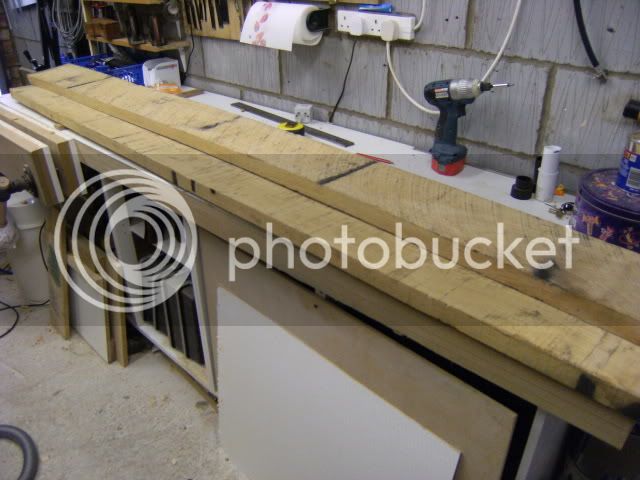
These pieces of 1 1/2" stock are to form the legs. I first crosscut the pieces to length
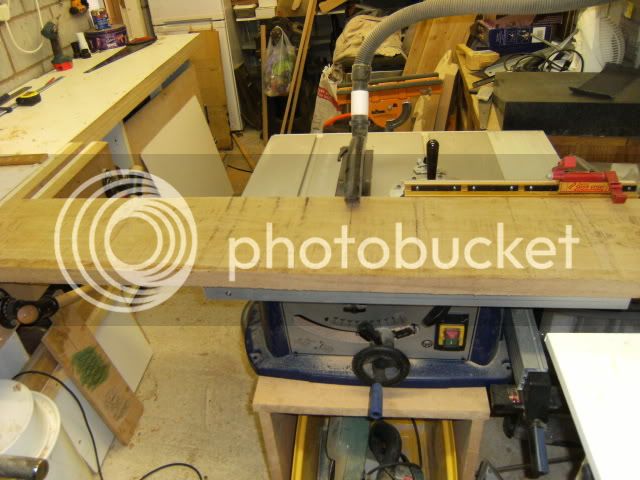
I was being a little lazy here - the stock was too long to be put on the saw for all crosscutting, so I did the first cut by hand on the bench, and the second on the table saw.
Once all pieces were thicknessed, jointed, ripped to width etc I ended up with 4 sets of these
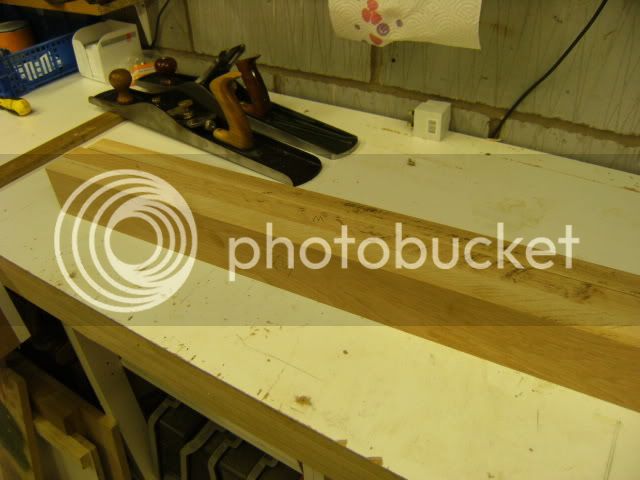
Each leg will consist of 3 pieces laminated together. Therefore each glue surface was hand planed to remove twist, snipe, cupping/bowing etc. Ended up with all pieces planed and ready for clamping
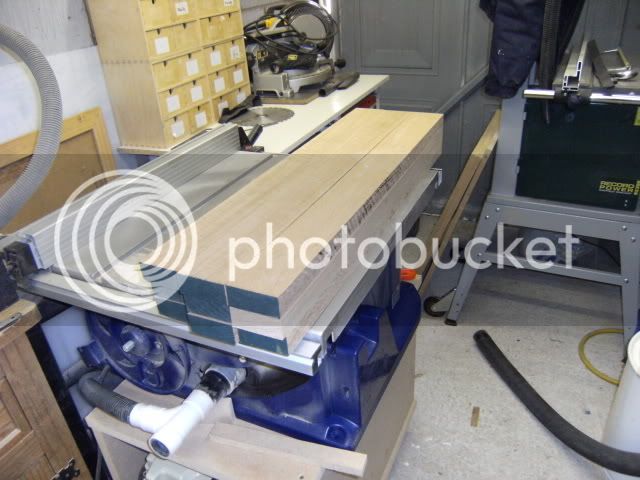
I only managed to get two glued up - ran out of bloody clamps....
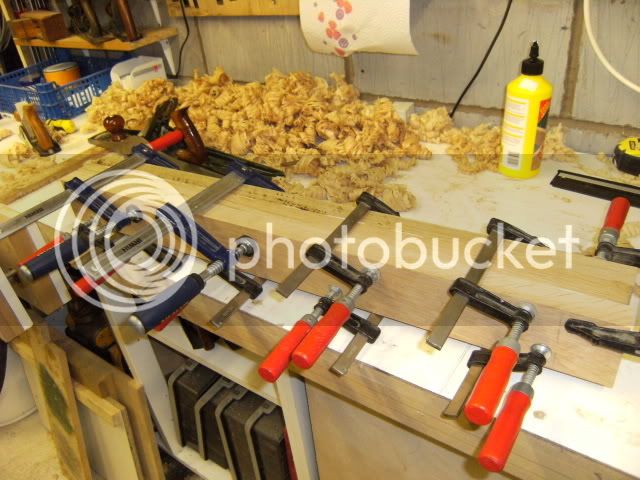
And that's as far as I got today. Tomorrow - glue up the other two legs and cut all four to size. Cut the mortice and tenon joints on rails and legs. Hopefully get the cross rail piece done.
Now it's time for one of these
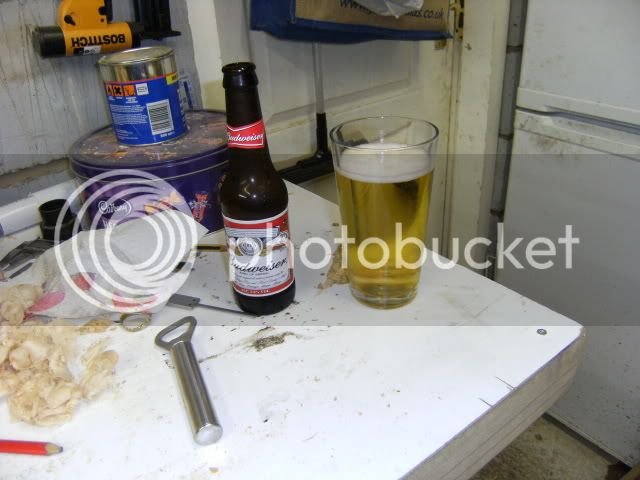
Total time spent on project today - 6 hours
Cheers
Karl