Simo
Established Member
- Joined
- 28 Mar 2009
- Messages
- 186
- Reaction score
- 118
I thought I'd post a work in progress thread to show the process of building one of my bass guitars. This one was started a couple of months back, so apologies for the amount of photos.
This will be a 33'' scale fretless, 5 string, 'piezo only' bass, fitted with a Hipshot bridge loaded with GraphTech Ghost saddles. The body wood is Black Walnut, with a Black Limba bookmatched top, Maple neck, and Ebony fingerboard. Something along these lines..
I already have a neck blank ready for this bass, so the first job to do is to plane the faces of the Black Walnut body blanks, and thickness them to the correct size. The pieces are then jointed by hand and glued together.
Once the glue has fully cured and the blank has had a final pass through the drum sander, I use a clear acrylic template to position the layout of the body shape. Then it's cut out on the bandsaw, leaving just a couple of millimetres to trim off with the router.
The Black Limba top is jointed and joined together using the 'tape tent' method. Once the glue is dry, it's sanded with a random orbit sander to remove the course drum sander marks.
After trimming the body outline on the pin router, I also route out the chamber, which is then sealed with a coat of finish.
The top, along with a piece of black veneer, are attached to the Walnut body using the vacuum bag.
After selecting a piece of Ebony for the fingerboard, I hold it down to my workbench using a couple of bench dogs and a small wedge to lock it in place. Then it's time to plane it flat, ready for slotting.
This will be a 33'' scale fretless, 5 string, 'piezo only' bass, fitted with a Hipshot bridge loaded with GraphTech Ghost saddles. The body wood is Black Walnut, with a Black Limba bookmatched top, Maple neck, and Ebony fingerboard. Something along these lines..
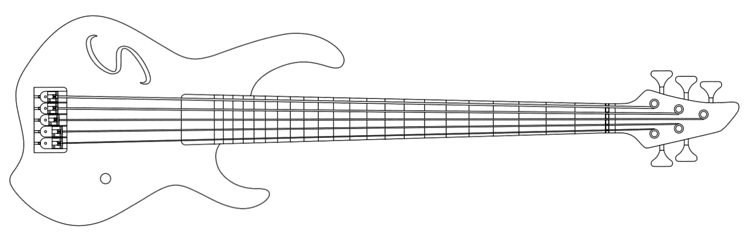
I already have a neck blank ready for this bass, so the first job to do is to plane the faces of the Black Walnut body blanks, and thickness them to the correct size. The pieces are then jointed by hand and glued together.
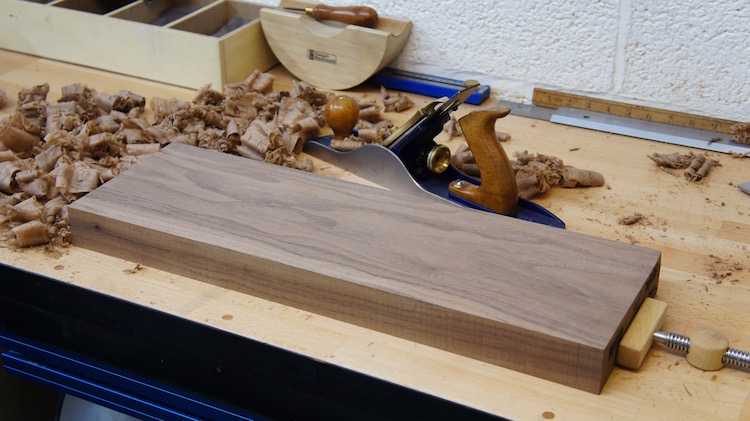
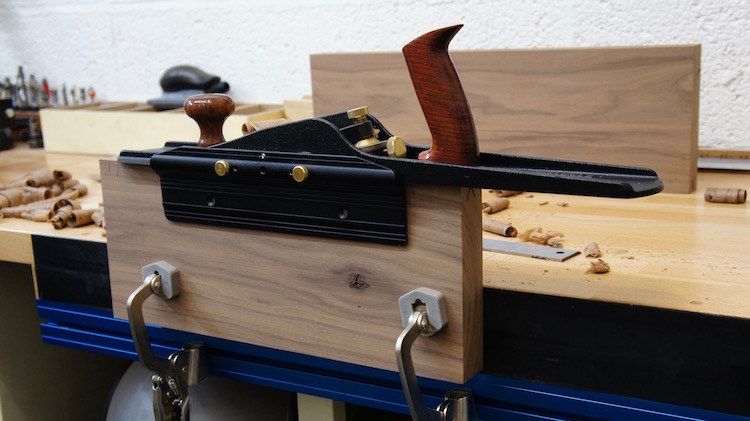
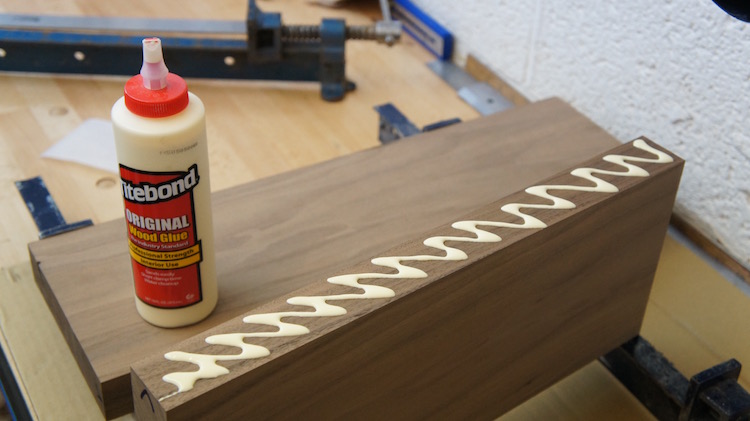
Once the glue has fully cured and the blank has had a final pass through the drum sander, I use a clear acrylic template to position the layout of the body shape. Then it's cut out on the bandsaw, leaving just a couple of millimetres to trim off with the router.
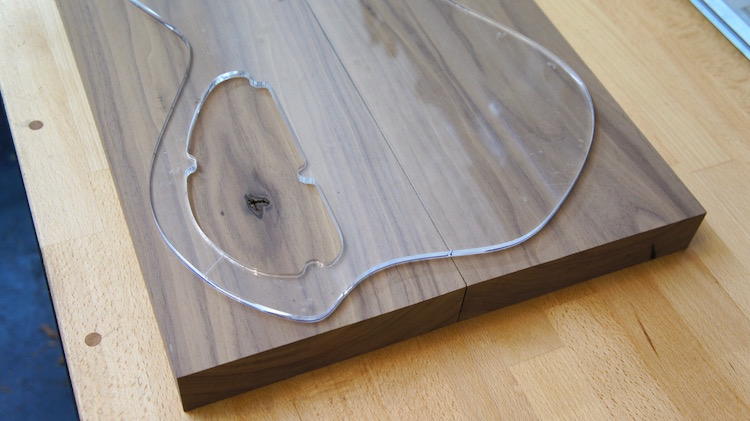
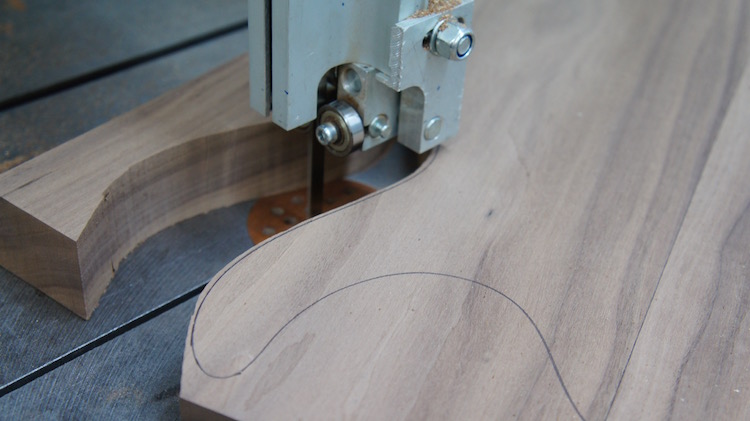
The Black Limba top is jointed and joined together using the 'tape tent' method. Once the glue is dry, it's sanded with a random orbit sander to remove the course drum sander marks.
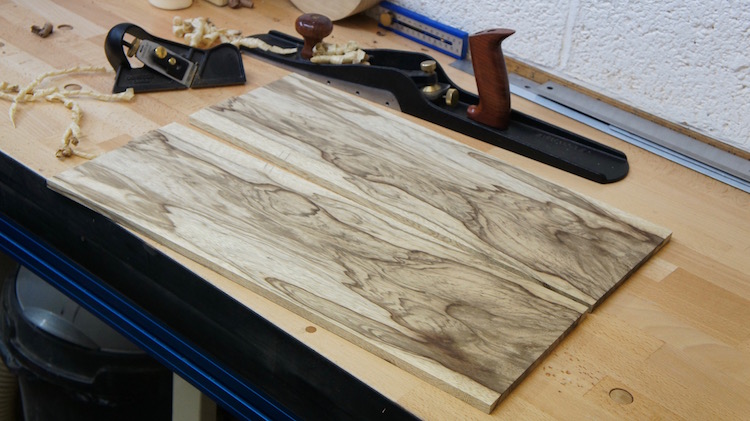
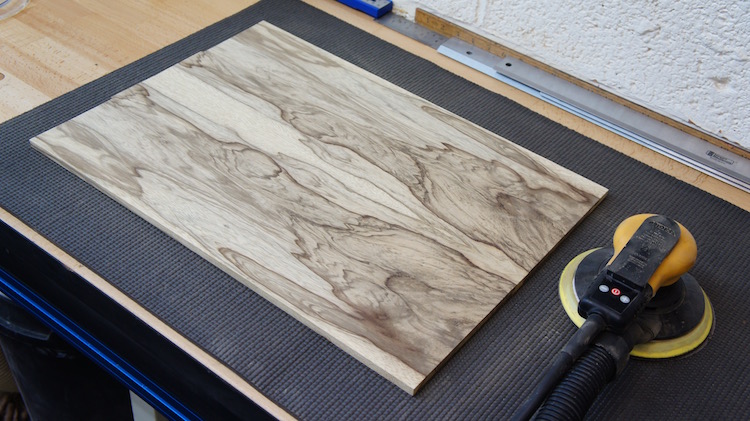
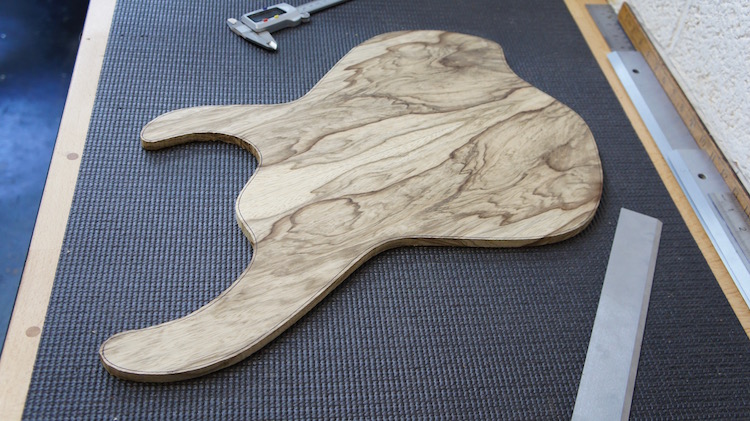
After trimming the body outline on the pin router, I also route out the chamber, which is then sealed with a coat of finish.
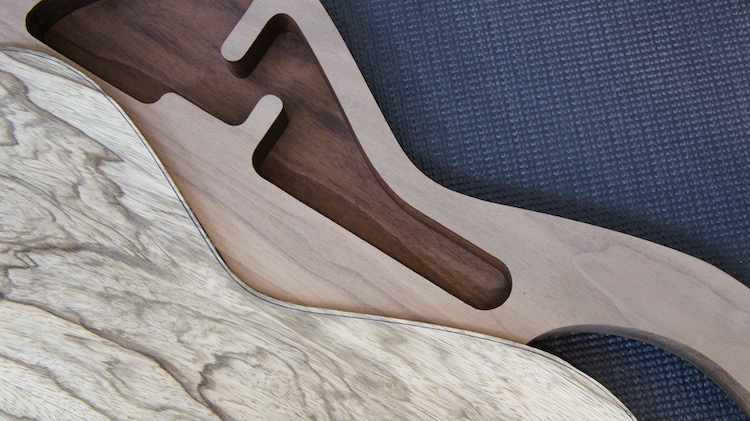
The top, along with a piece of black veneer, are attached to the Walnut body using the vacuum bag.
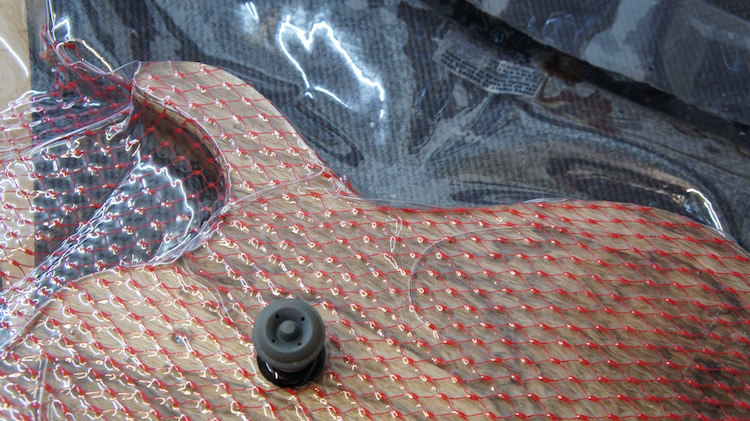
After selecting a piece of Ebony for the fingerboard, I hold it down to my workbench using a couple of bench dogs and a small wedge to lock it in place. Then it's time to plane it flat, ready for slotting.
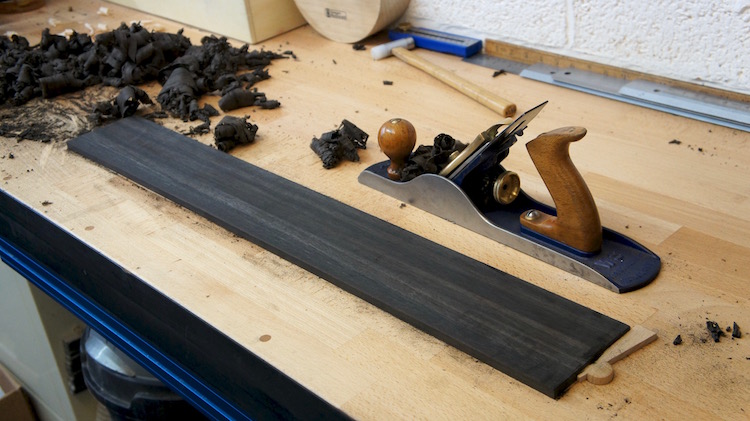