El Barto
👍
I've gotta say, this bleak winter we've had really killed my enthusiasm to be in the workshop and that is not a nice feeling. I was in there less and less, conducive to the weather, until we got that patch of sub-zero temperatures and I just gave up. I knew I wanted to be making things but at the same time I had no desire or motivation to do it ever again.
So I decided to get some sun and drove to Portugal for a couple of weeks. And it was while driving through hundreds of kilometres of olive groves and farms that I began to get that familiar stir of wanting to get my hands on some wood and do something with it. Many of the olive trees were being heavily pruned and cut back, with the branches either being left on the ground or burned. I kept an eye out for any thick looking offcuts and gathered some as I went. I hadn't thought to bring any tools with me, a shame because what better way to spend a mild evening than whittling, especially unknown woods that I'd picked up on the road? In fact at one beach I arrived at after a few miles of long dirt tracks I met another guy who was indeed doing just that, sitting on the stoop of his campervan; I was jealous. But now I know for next time and when I got home I quickly knocked up my first spoon and thankfully I thought to myself, "oh yeah, now I remember".
And since then I've been in the workshop most days, largely in part to it no longer being freezing but mostly because I want to be there. It feels great. And now I've been asked by my aunt to make some gates for my uncle's birthday. Normally when someone finds out that you are a woodworker they, at some point, ask you to make or fix something really boring. That's been my experience at least. But I was pleasantly surprised by this request. The photo is of some gates in Morocco that they loved and want to replicate - I think it could be a fun build.
As with so much old furniture, they look like they were built out of necessity using materials that were readily available and I'd like to do something similar, working with imperfections and the like. Perhaps with hazel as it grows in such abundance around here and is so flexible. Each piece could be picked based upon where it's supposed to go on the gate, curved on top etc. I'm not trying to exactly copy the photo. Anybody got any thoughts? Perhaps a more suitable wood to use?
Hope to hear some suggestions!
So I decided to get some sun and drove to Portugal for a couple of weeks. And it was while driving through hundreds of kilometres of olive groves and farms that I began to get that familiar stir of wanting to get my hands on some wood and do something with it. Many of the olive trees were being heavily pruned and cut back, with the branches either being left on the ground or burned. I kept an eye out for any thick looking offcuts and gathered some as I went. I hadn't thought to bring any tools with me, a shame because what better way to spend a mild evening than whittling, especially unknown woods that I'd picked up on the road? In fact at one beach I arrived at after a few miles of long dirt tracks I met another guy who was indeed doing just that, sitting on the stoop of his campervan; I was jealous. But now I know for next time and when I got home I quickly knocked up my first spoon and thankfully I thought to myself, "oh yeah, now I remember".
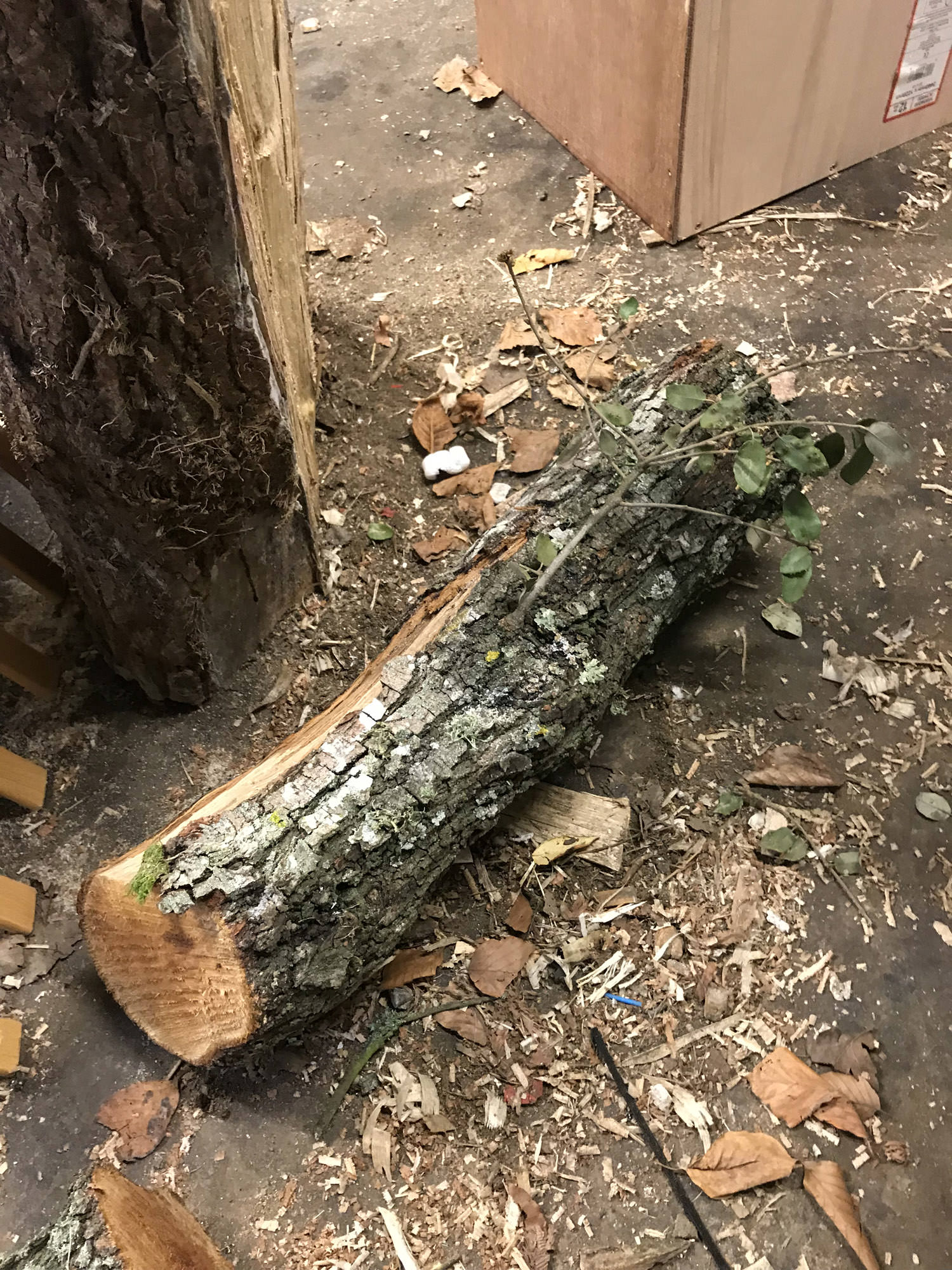
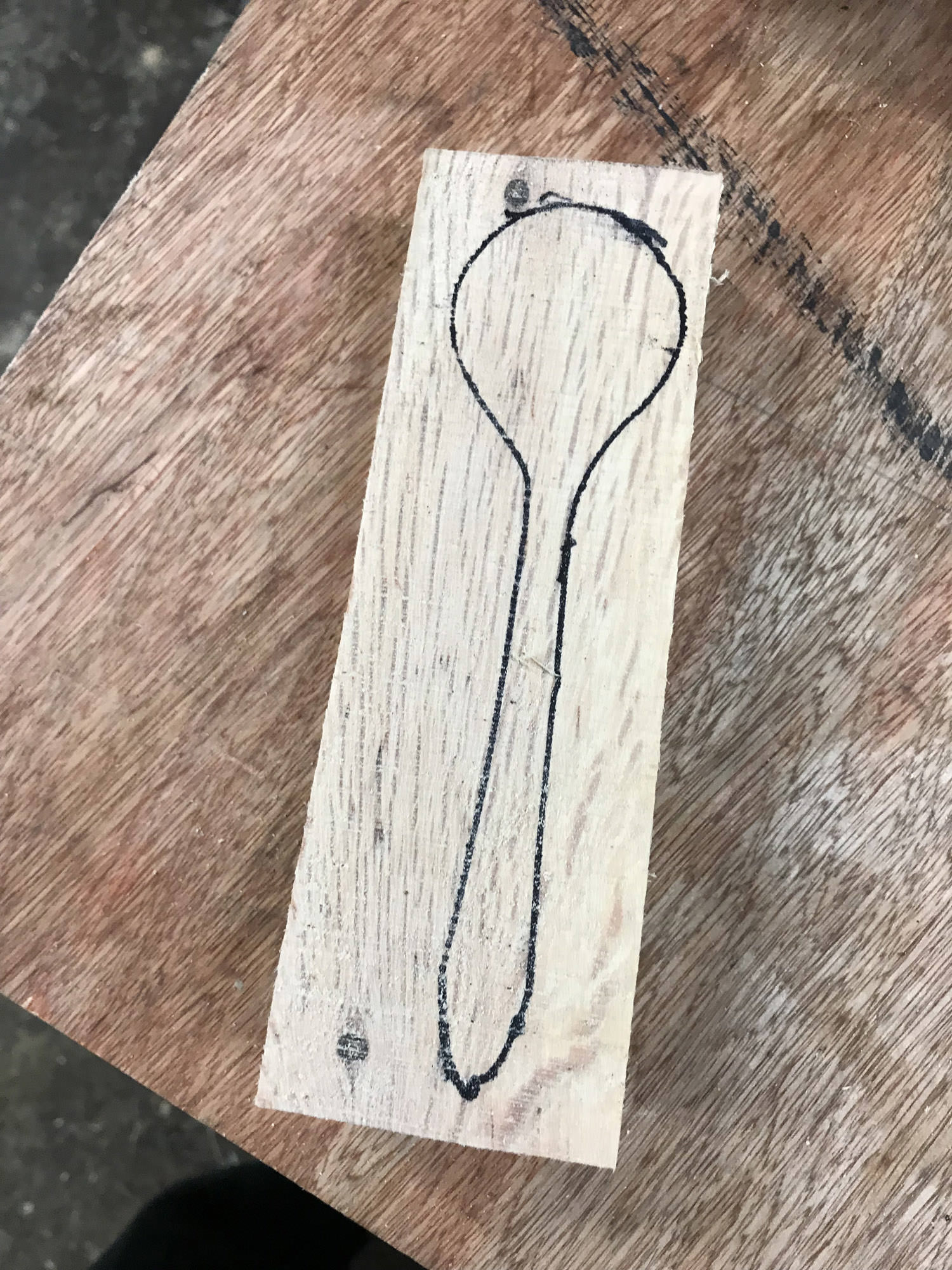
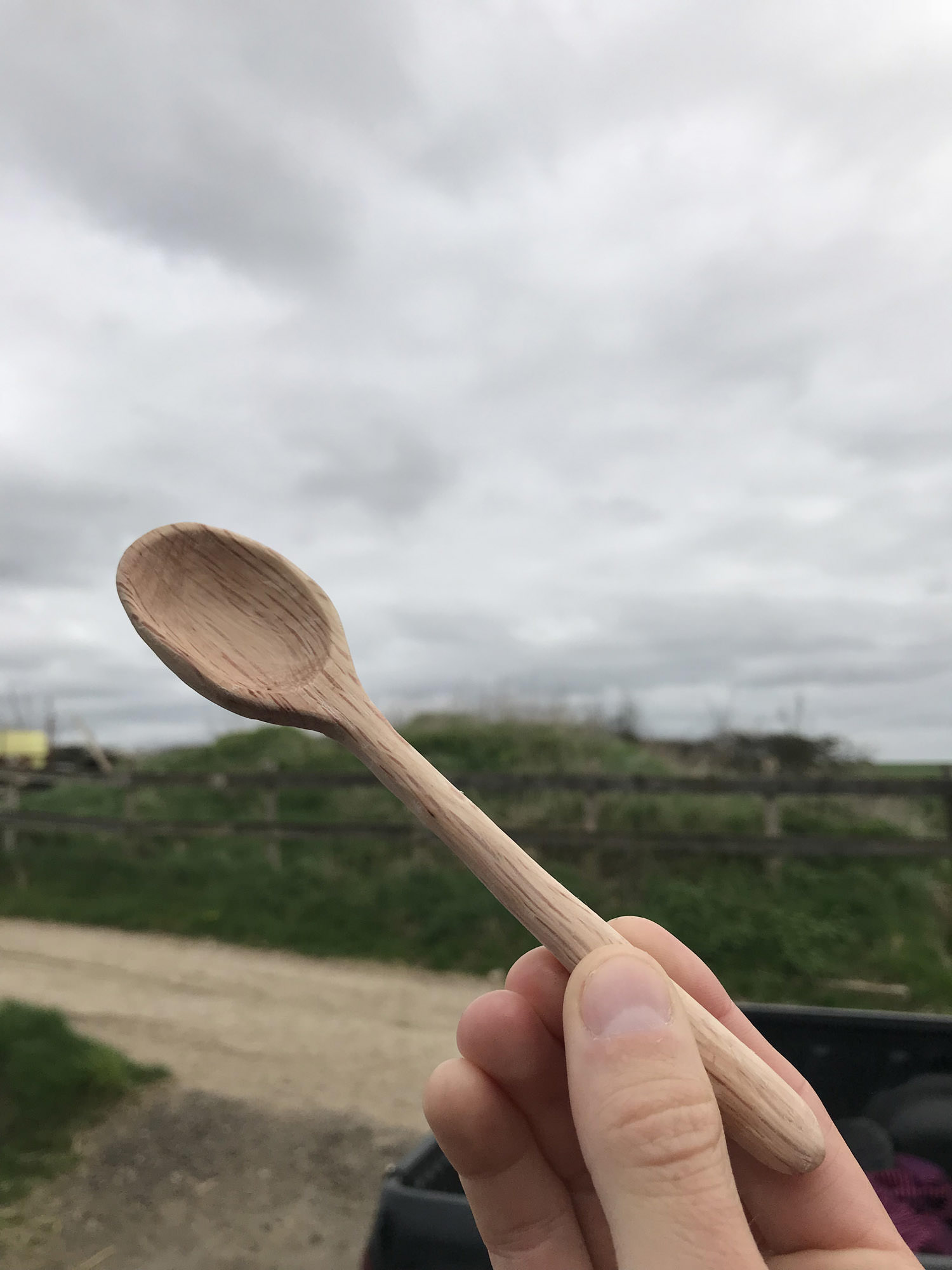
And since then I've been in the workshop most days, largely in part to it no longer being freezing but mostly because I want to be there. It feels great. And now I've been asked by my aunt to make some gates for my uncle's birthday. Normally when someone finds out that you are a woodworker they, at some point, ask you to make or fix something really boring. That's been my experience at least. But I was pleasantly surprised by this request. The photo is of some gates in Morocco that they loved and want to replicate - I think it could be a fun build.
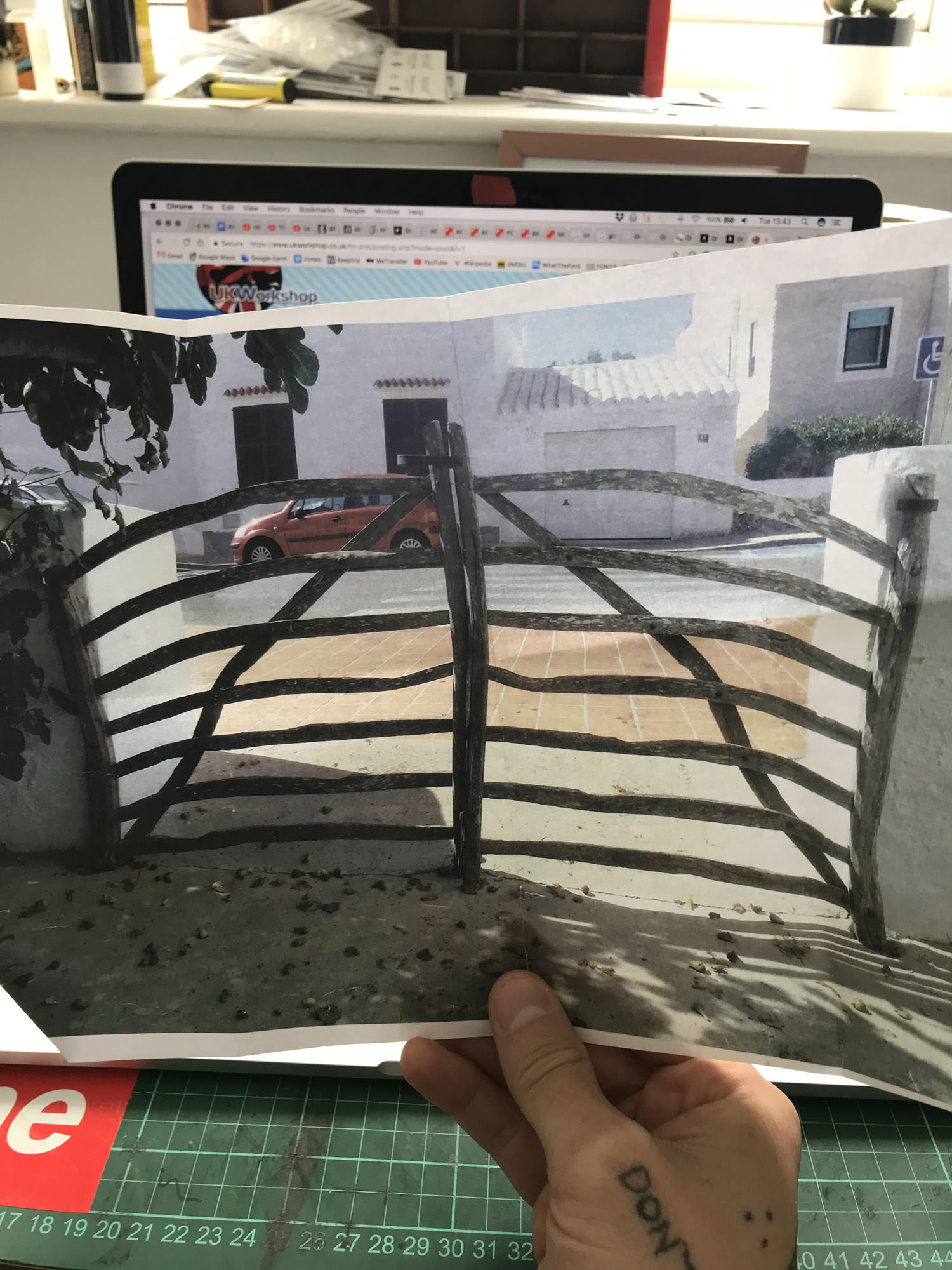
As with so much old furniture, they look like they were built out of necessity using materials that were readily available and I'd like to do something similar, working with imperfections and the like. Perhaps with hazel as it grows in such abundance around here and is so flexible. Each piece could be picked based upon where it's supposed to go on the gate, curved on top etc. I'm not trying to exactly copy the photo. Anybody got any thoughts? Perhaps a more suitable wood to use?
Hope to hear some suggestions!