I passed my Axminster standalone thicknesser onto Alan (Mailee). So there I was, browsing through Ebay, looking for a benchtop thicknesser, when up popped a little tempter. Bit grubby looking, but it arrived today and i'm well chuffed !
12" 3 knife cutterblock assembly.
Rise and fall handle with locking tommy bar arrangement - the rise and fall on the table is sweet!
Rollers in the table too
Side cover
Which, when removed, reveals this lot - you can't really see from the picture, but the motor is huge!
Starter switch and isolator - a quick inspection of the wiring confirms it's single phase
Here you can see the "W" logo
Which is noticeably absent from the cutterblock cover
And finally, the inspection plate
1951 model
Can't wait to get my tool box back from site and start taking it apart.
Cheers
Karl
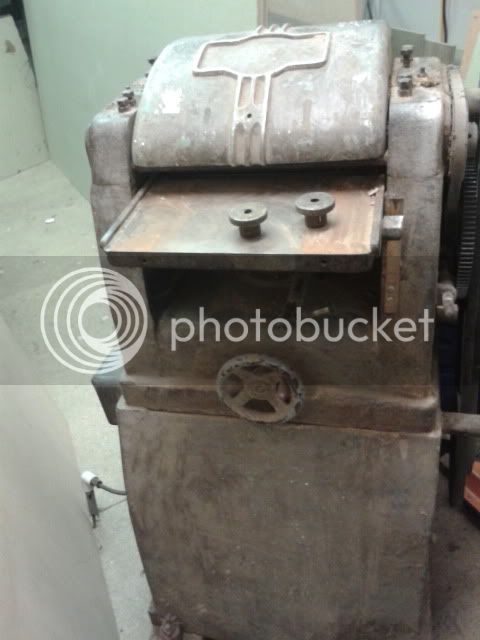
12" 3 knife cutterblock assembly.
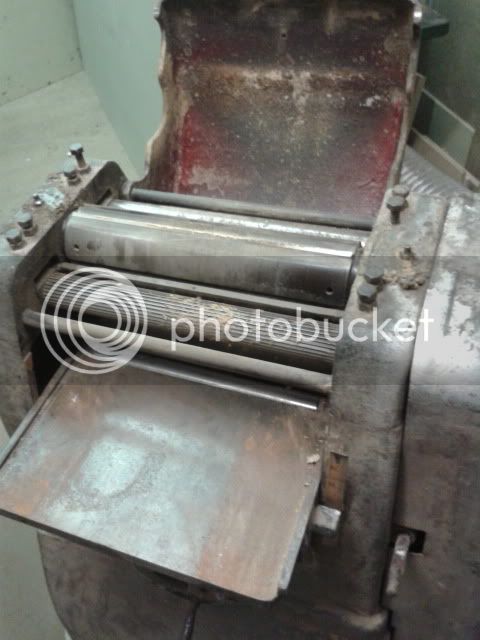
Rise and fall handle with locking tommy bar arrangement - the rise and fall on the table is sweet!
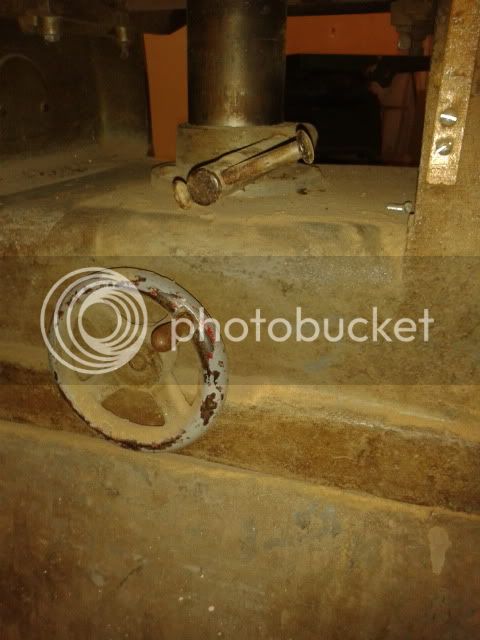
Rollers in the table too
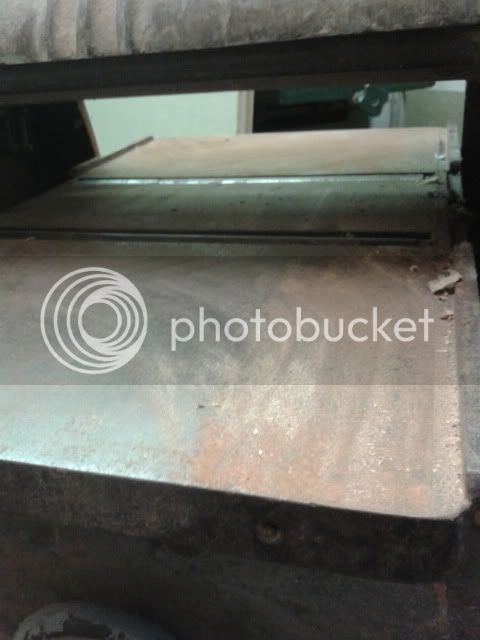
Side cover
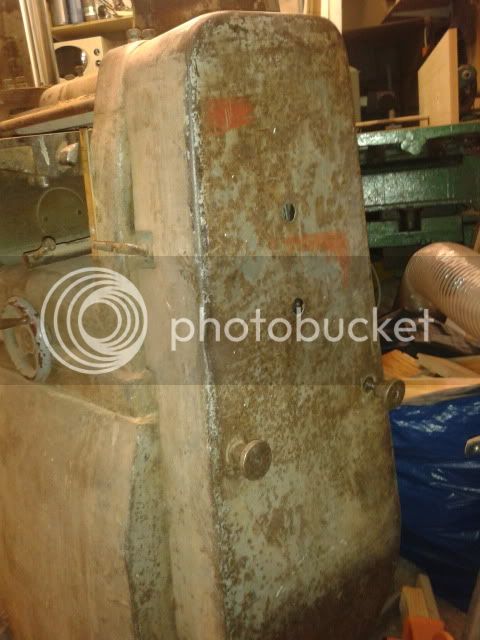
Which, when removed, reveals this lot - you can't really see from the picture, but the motor is huge!
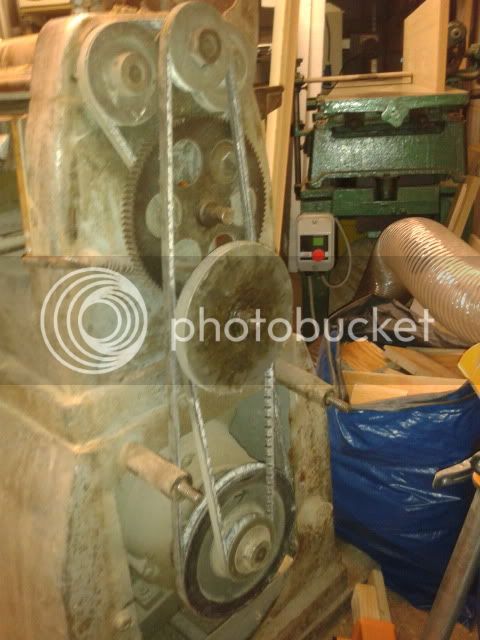
Starter switch and isolator - a quick inspection of the wiring confirms it's single phase
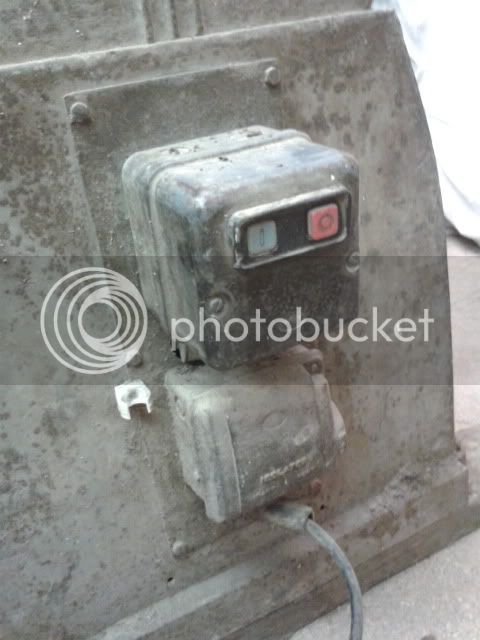
Here you can see the "W" logo
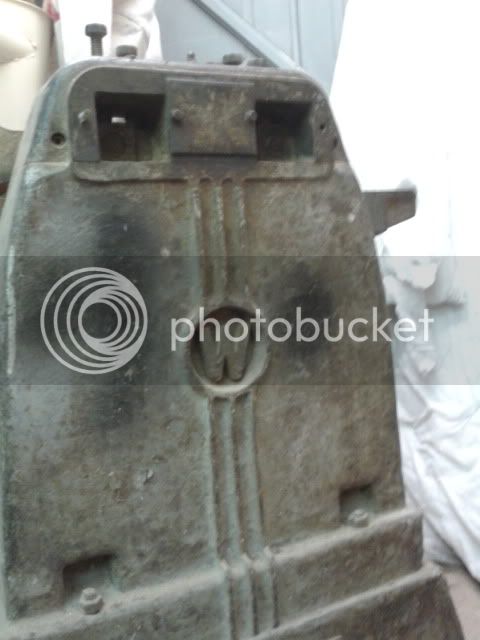
Which is noticeably absent from the cutterblock cover
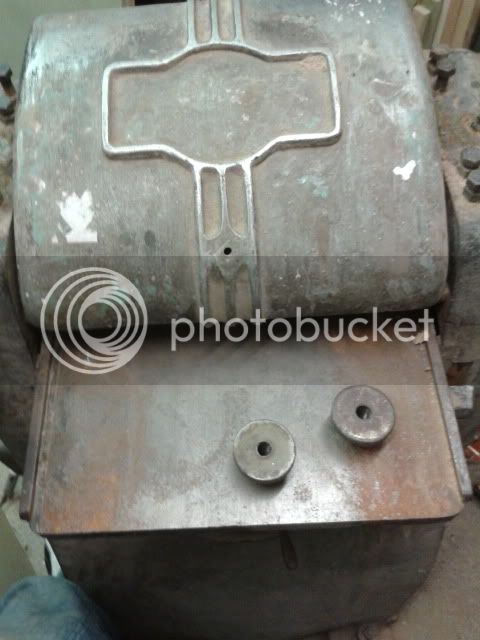
And finally, the inspection plate
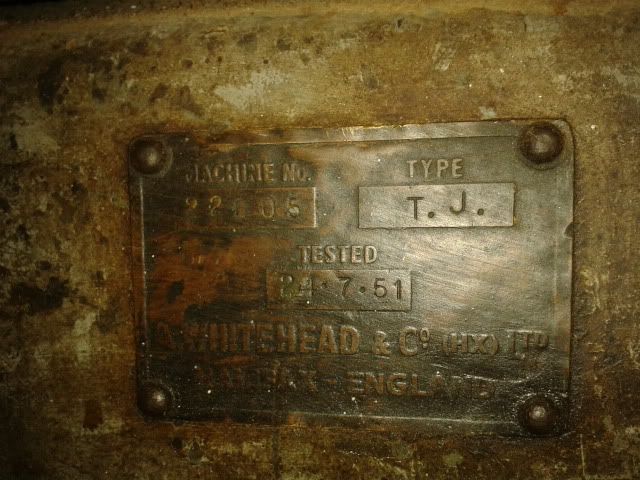
1951 model
Can't wait to get my tool box back from site and start taking it apart.
Cheers
Karl