Moved in this hulk:
The bolt which secures the chisel in position, unfortunately seized and subsequently sheered on attempting to free it. The remainder of the bolt has been drilled out, the residue of the threads removed with a tap, and a replacement (and spare) set-screw of the appropriate size (5/16th Whitworth) has been sourced.
Machine has been stripped, wire brushed, cleaned and coated with a thin coat of light oil.
Threads on arm have been cleared with 7/16ths Whitworth tap.
Ways on the table have been thoroughly cleaned, all ways have been lubricated using light oil (debatable as to whether way-lube would be beneficial or cause excessive buildup of sawdust).
Damaged wiring to motor removed, motor has been stripped, all dust and chips removed, and the bearings checked, top bearing cover found to not be attached, needs 2 × 0BA 2" machine screws. sourced.
Chisel and auger sharpened, fitted and adjusted.
New depth stop machined from ½"O/D steel pipe from metalwork scrap bin.
Chisel collet has significant damage, still serviceable as is but replacement best course of action long term.
Auger collet has burr on bottom, could damage chisel holder assembly bearing surface during maintainance if not addressed.
Z-axis travel rack missing tooth, has been replaced with two set screws, long term brazed-in replacement sensible.
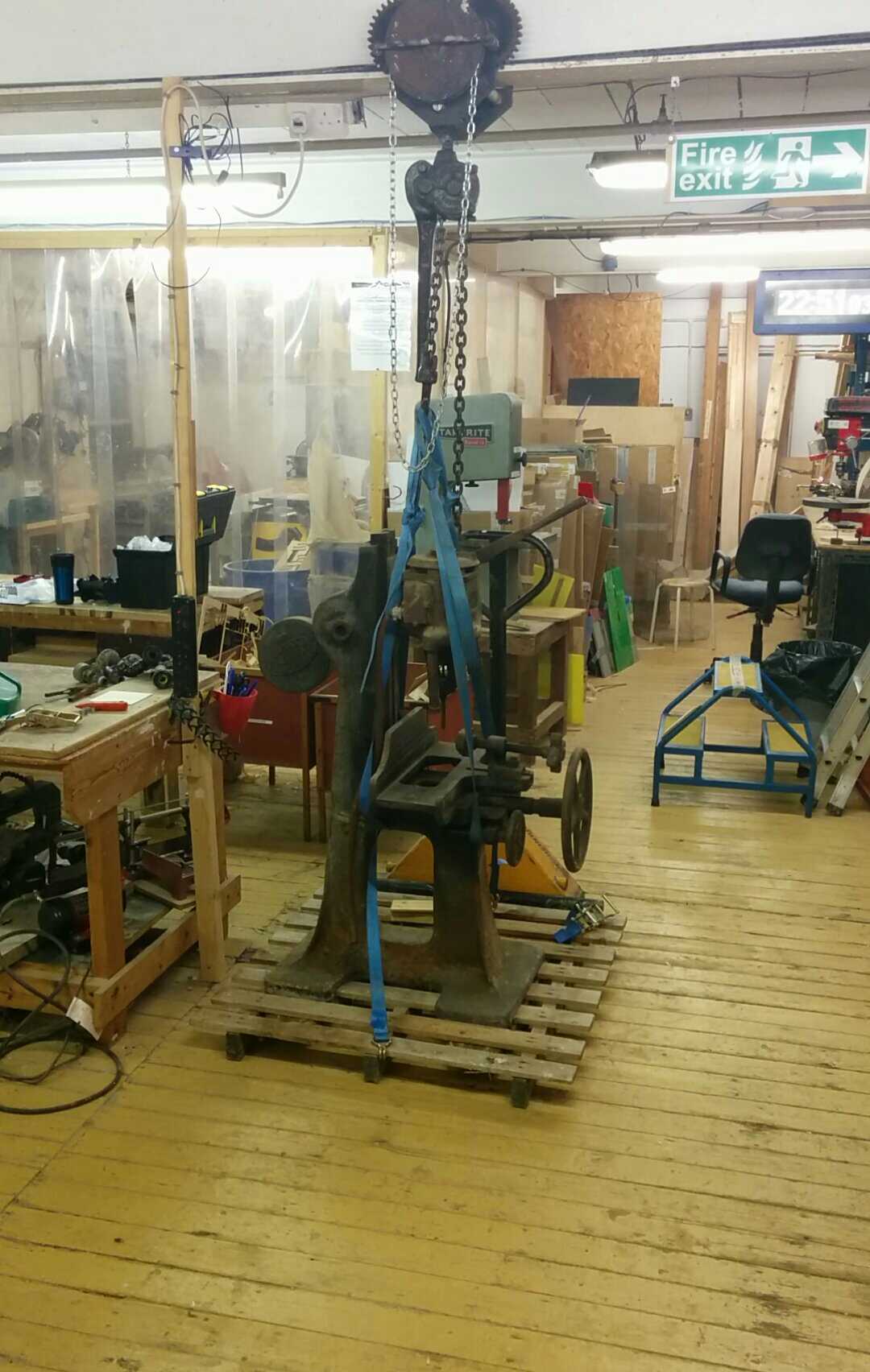
The bolt which secures the chisel in position, unfortunately seized and subsequently sheered on attempting to free it. The remainder of the bolt has been drilled out, the residue of the threads removed with a tap, and a replacement (and spare) set-screw of the appropriate size (5/16th Whitworth) has been sourced.
Machine has been stripped, wire brushed, cleaned and coated with a thin coat of light oil.
Threads on arm have been cleared with 7/16ths Whitworth tap.
Ways on the table have been thoroughly cleaned, all ways have been lubricated using light oil (debatable as to whether way-lube would be beneficial or cause excessive buildup of sawdust).
Damaged wiring to motor removed, motor has been stripped, all dust and chips removed, and the bearings checked, top bearing cover found to not be attached, needs 2 × 0BA 2" machine screws. sourced.
Chisel and auger sharpened, fitted and adjusted.
New depth stop machined from ½"O/D steel pipe from metalwork scrap bin.
Chisel collet has significant damage, still serviceable as is but replacement best course of action long term.
Auger collet has burr on bottom, could damage chisel holder assembly bearing surface during maintainance if not addressed.
Z-axis travel rack missing tooth, has been replaced with two set screws, long term brazed-in replacement sensible.