- Joined
- 19 Mar 2007
- Messages
- 5,295
- Reaction score
- 411
Has anyone else tried turning ply? This is my second and last attempt. The ply that I used to get from Severn Ply in Stonehouse Glos was excelent quality and I decided to see what it was like to turn. It was very dusty and dulled tools quicker that you could say. Well, I had a brain wave a short while back and decided to glue 4 bits of 1 inch French ply together and turn a 12 inch by 4 inch deep bowl! I cut the ply so the bottom was a 4 inch circular piece with a 5 inch ring, 2 inches wide i.e. a 3 inch hole in the middle, glued on to that. Next 2 rings stuck onto that to finish up with a 12 inch-ish top ring. I hot glued a piece of pine to the top of the second smallest ring and hot glued a wooden faceplate chuck to the middle. Much easier to do than trype out believe me!
I mounted the assembly on the chuck and turned the bottom to take my expanding jaw chuck and turned the outside of the bowl. Once done and sanded it was sealed with a Liberon hard wax stick.
The whole lot was then turned, after belting the faceplate chuck out with a cabinet makers screwdriver and big hammer cause I put enough hot glue on to make sure the blasted thing wasn't going to let go when turning! I then mounted it on my expanding chuck and turned the inside. It was an awful job because the crap French ply took the edge off of tools in just a few seconds. It was turned fairly roughly and then I thught 'sod it' and put the coarses disk on my flex drive on my power sanding drill and finished it off with that. Then it was just a case of going down through the grits and a good coat of danish oil inside to finish.
If anyone has any ideas of trying the same thing then my advise is DON'T. It's too much like hard work, it will wear your gouges down big time and it's so dusty that even if you have a Powercap light like mine then you will be able to breath, but you will spend half of your time trying to see through the dust on the faceplate!
I mounted the assembly on the chuck and turned the bottom to take my expanding jaw chuck and turned the outside of the bowl. Once done and sanded it was sealed with a Liberon hard wax stick.
The whole lot was then turned, after belting the faceplate chuck out with a cabinet makers screwdriver and big hammer cause I put enough hot glue on to make sure the blasted thing wasn't going to let go when turning! I then mounted it on my expanding chuck and turned the inside. It was an awful job because the crap French ply took the edge off of tools in just a few seconds. It was turned fairly roughly and then I thught 'sod it' and put the coarses disk on my flex drive on my power sanding drill and finished it off with that. Then it was just a case of going down through the grits and a good coat of danish oil inside to finish.
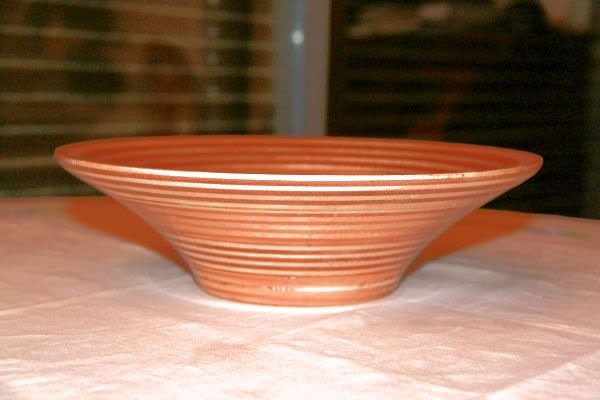
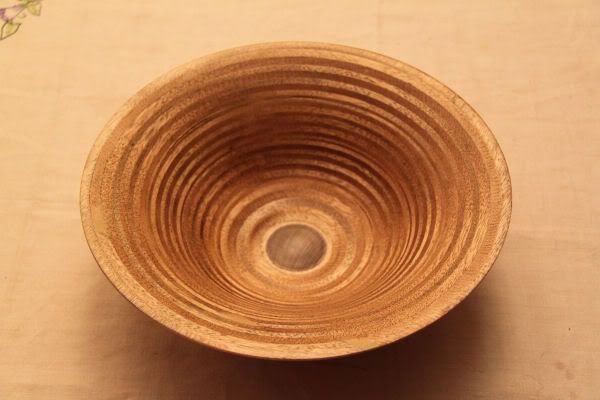
If anyone has any ideas of trying the same thing then my advise is DON'T. It's too much like hard work, it will wear your gouges down big time and it's so dusty that even if you have a Powercap light like mine then you will be able to breath, but you will spend half of your time trying to see through the dust on the faceplate!