Dr Al
Established Member
For background, the primary reason I did this project was to practice hand tool woodwork without having to worry too much about aesthetics (which are not my forte). Less significantly, I also wanted the ability to take a tool kit on holiday and be able to make small boxes and such-like. Since Carolyn has had M.E., she often needs to spend a reasonable amount of time resting and I'd go spare if I just had to sit around reading all day, so having a little project kit with me helps keep me sane.
This chest (made out of Sweet Chestnut, American Black Walnut, brass and stainless steel) gives me the ability to carry all the tools I need to make boxes and such-like, while also providing plenty of different work-holding approaches.
All the woodwork (with the exception of a few "resawing" cuts on a bandsaw) was done with hand tools. All of the metal bits were also made by me, but not with hand tools, because hand-tool metalworking is just silly
Front view:
Front open, showing the doe's feet tucked in place:
More views of the oiled drawers in place (you can also see the brass number plate in the drawers that are sticking out - the drawers are intended to be removed when the chest is being used as a workbench, so the numbers make it quick and easy to put the drawers back in the right place):
Planing stops; the little brass pins at the bottom are used to push the planing stops up and down after loosening the brass knobs:
The photo above also shows the leather lining on the vice jaw.
Back view:
Close-up of a vice screw and a wedged tenon (the knurled stainless steel knob holds the cross-bar in place; the steel screw has a small brass wear pad on the end to stop it damaging the cross-bar):
View showing the whole of the back with the anti-racking piece (which stops the chest twisting when planing stuff on the top):
Work holding:
Holding a piece in the vice for sawing (similar set-up for planing the end/edge):
Removing the middle vice screw and holding a wider piece:
The vice jaw can be completely removed and then really big pieces can be clamped to the back for sawing to length or edge planing:
or clamped to the top for sawing or chiselling or whatever:
The planing stops can be used for simple face planing:
Or for a bit more robustness, a doe's foot can be clamped to the top:
The vice can also be flipped round (so that a solid face is against the chest rather than a leather face) and then moved up and down (this photo shows the upper limit):
That allows boards to be fully constrained while still giving complete access to the top surface:
Finally (I think), there's the chest front / shooting board, which goes on top and pushes against the planing stops (this is the main reason for having three planing stops - so one is far enough over to support the shooting board near the working side)...
...which can be used for shooting ends square (with a block plane I also made, including the blade, as part of this project):
... and shooting mitres:
I mentioned that this project was mainly about learning and practising hand tool woodworking techniques. To expand on that, this was:
This chest (made out of Sweet Chestnut, American Black Walnut, brass and stainless steel) gives me the ability to carry all the tools I need to make boxes and such-like, while also providing plenty of different work-holding approaches.
All the woodwork (with the exception of a few "resawing" cuts on a bandsaw) was done with hand tools. All of the metal bits were also made by me, but not with hand tools, because hand-tool metalworking is just silly
Front view:
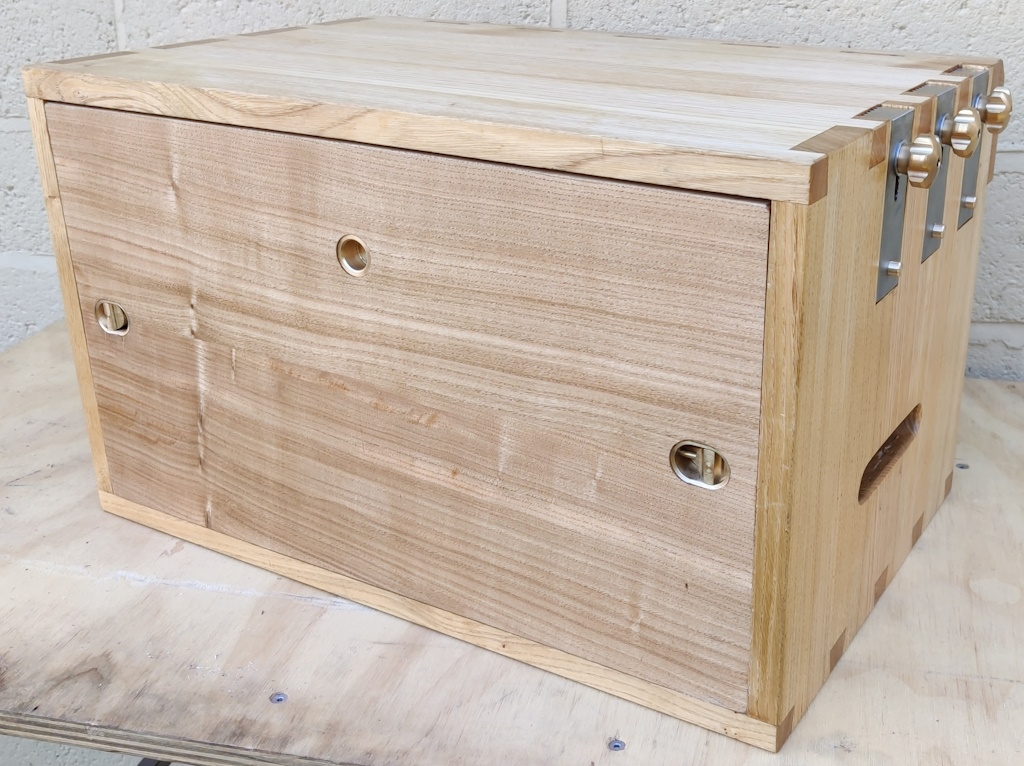
Front open, showing the doe's feet tucked in place:
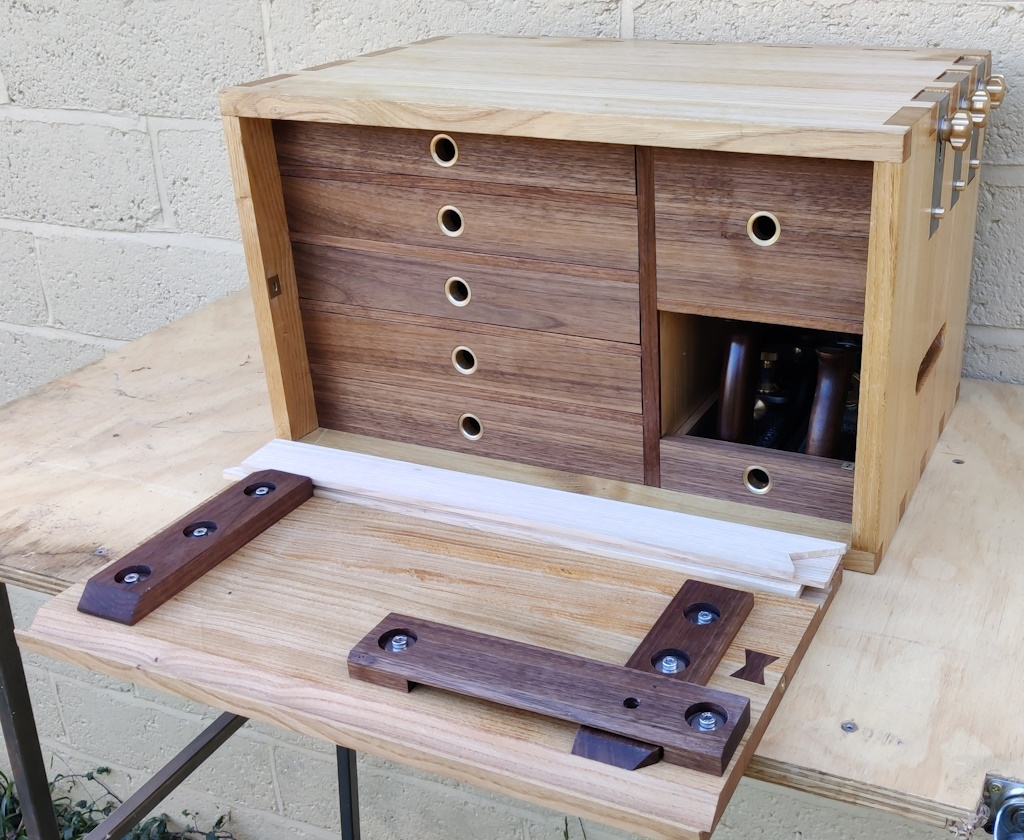
More views of the oiled drawers in place (you can also see the brass number plate in the drawers that are sticking out - the drawers are intended to be removed when the chest is being used as a workbench, so the numbers make it quick and easy to put the drawers back in the right place):
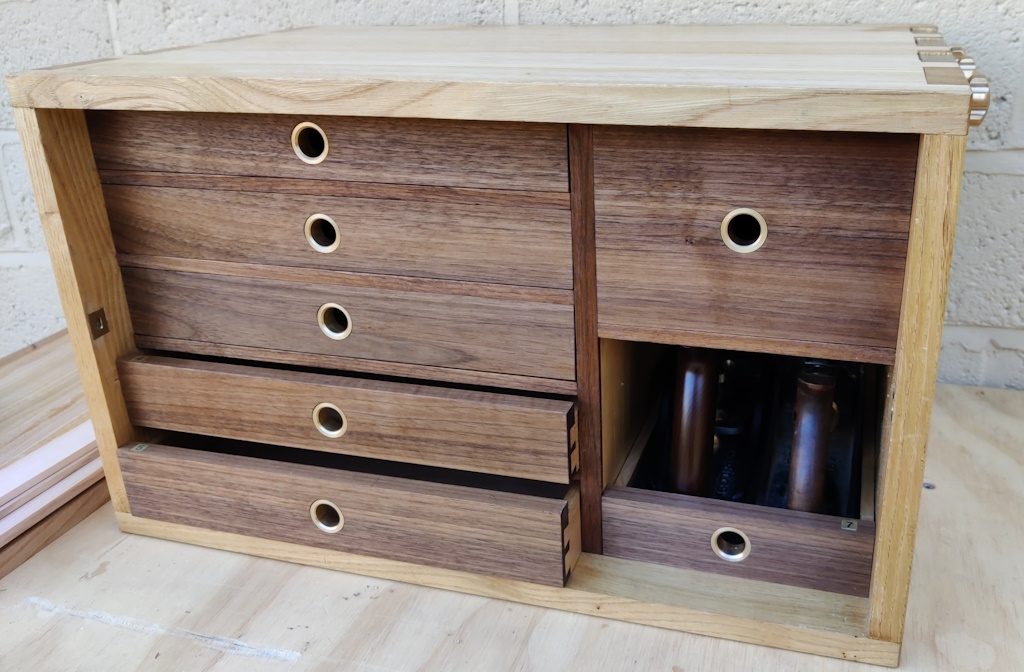
Planing stops; the little brass pins at the bottom are used to push the planing stops up and down after loosening the brass knobs:
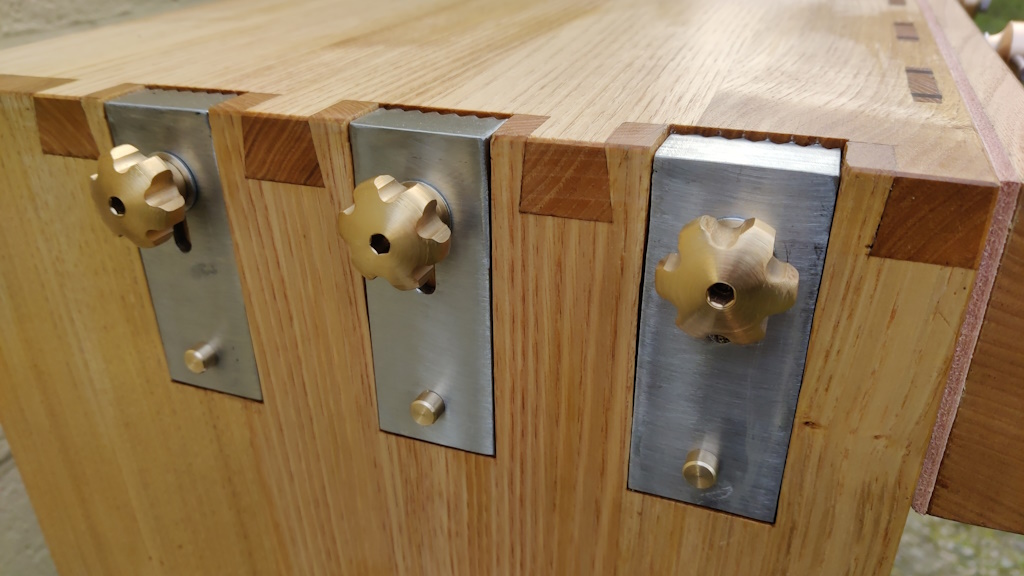
The photo above also shows the leather lining on the vice jaw.
Back view:
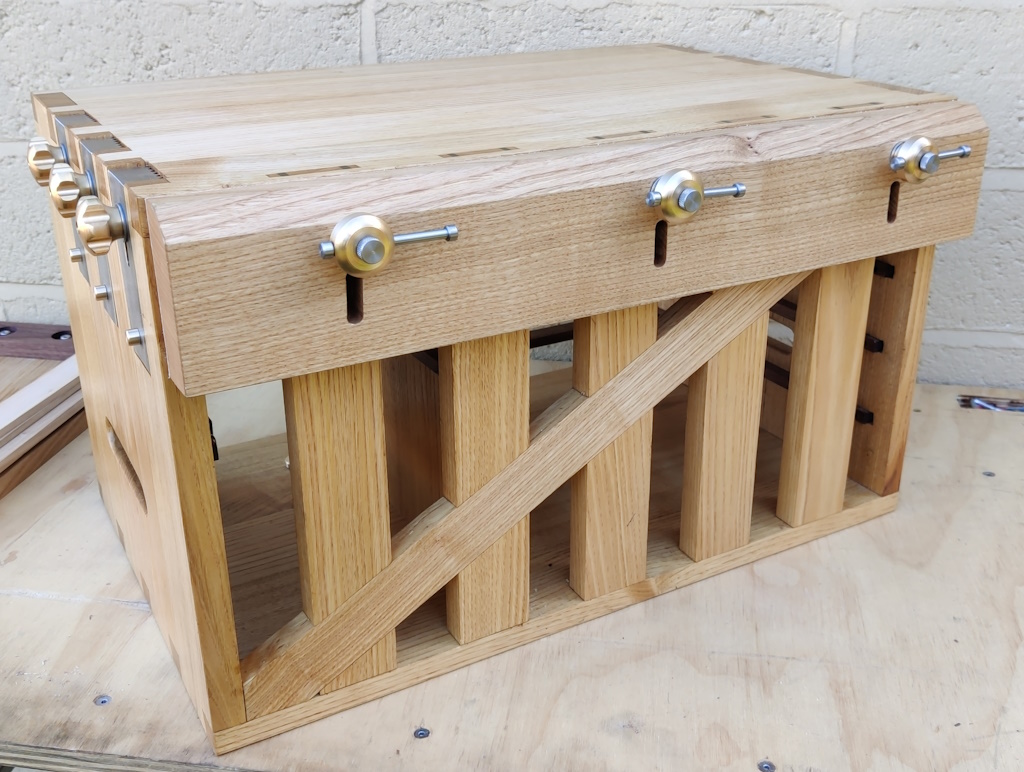
Close-up of a vice screw and a wedged tenon (the knurled stainless steel knob holds the cross-bar in place; the steel screw has a small brass wear pad on the end to stop it damaging the cross-bar):
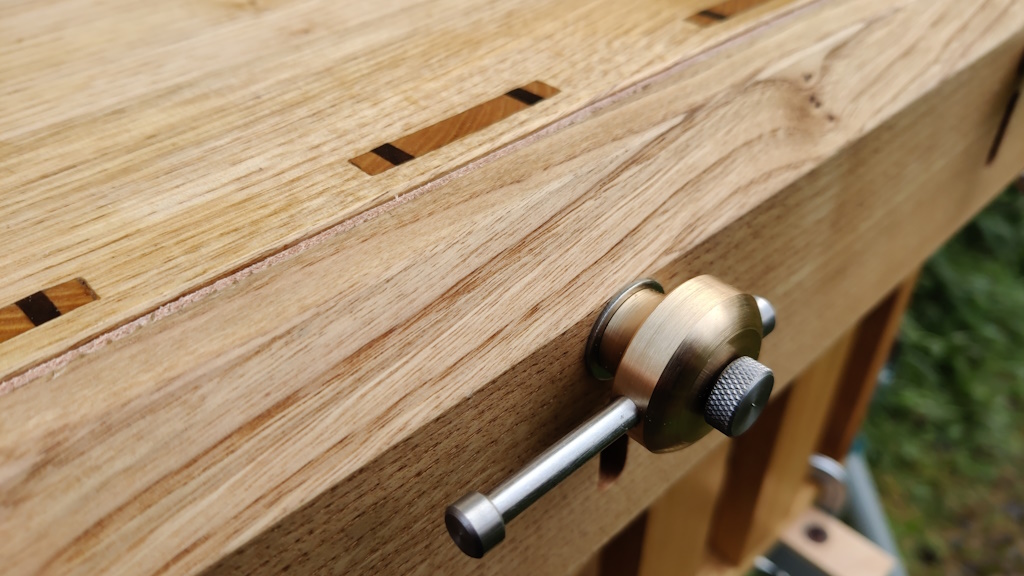
View showing the whole of the back with the anti-racking piece (which stops the chest twisting when planing stuff on the top):
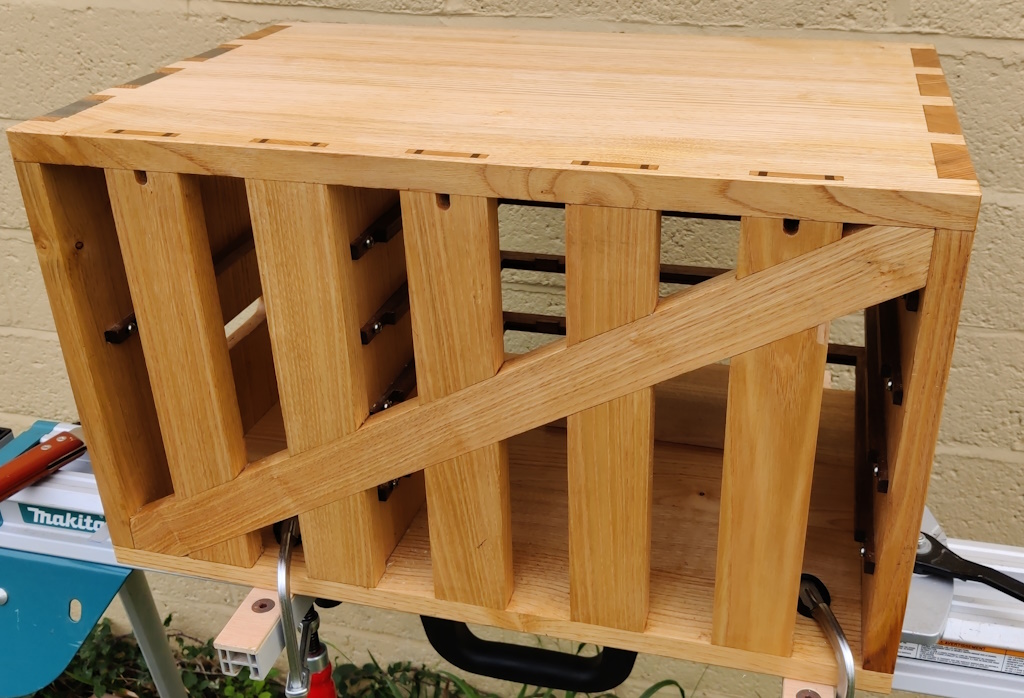
Work holding:
Holding a piece in the vice for sawing (similar set-up for planing the end/edge):
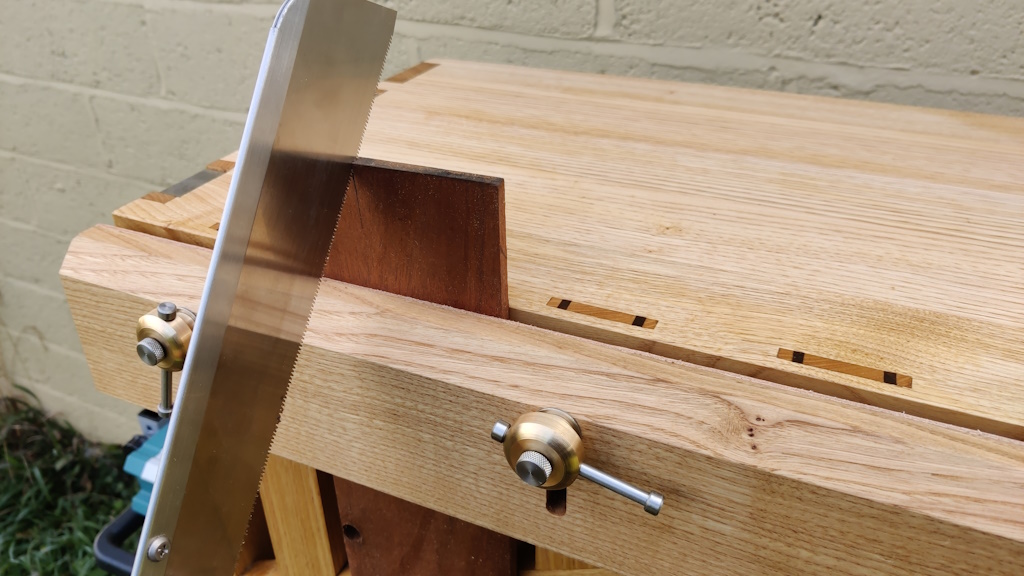
Removing the middle vice screw and holding a wider piece:
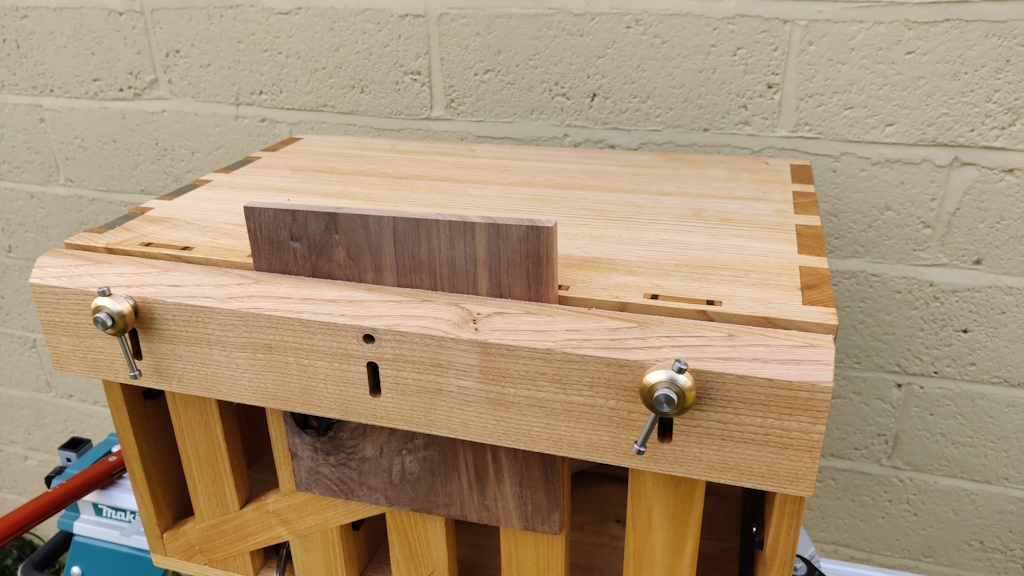
The vice jaw can be completely removed and then really big pieces can be clamped to the back for sawing to length or edge planing:
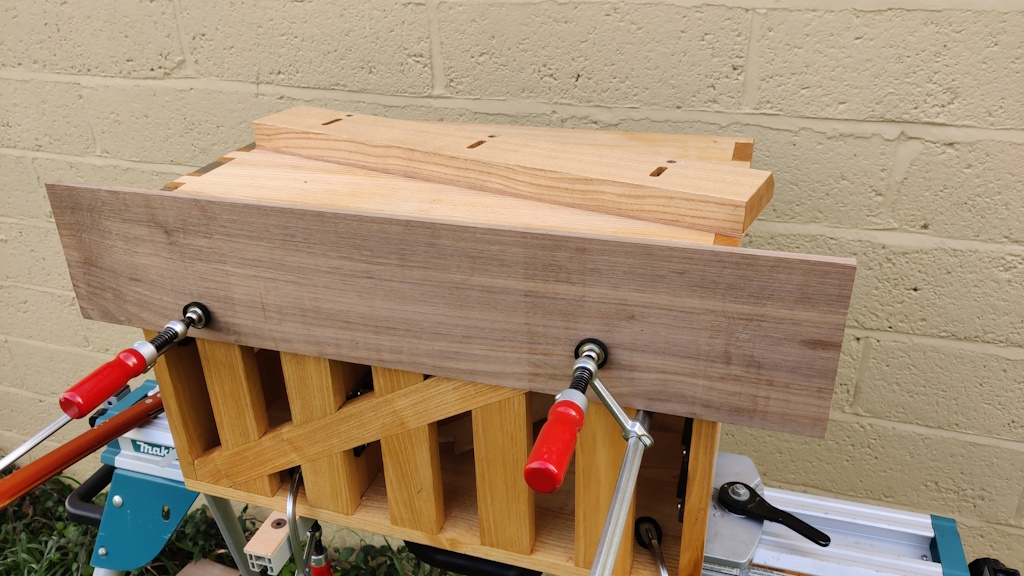
or clamped to the top for sawing or chiselling or whatever:
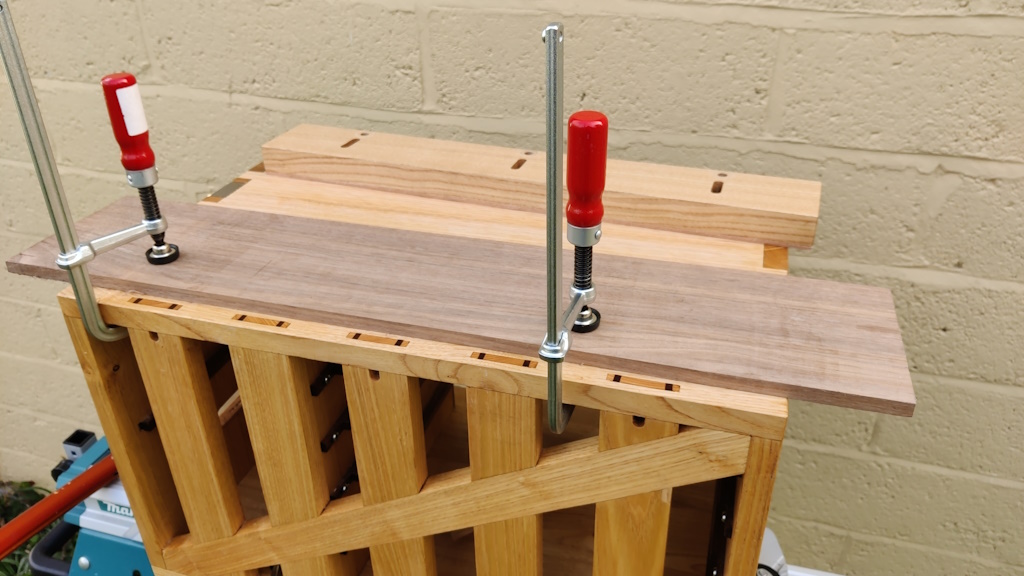
The planing stops can be used for simple face planing:
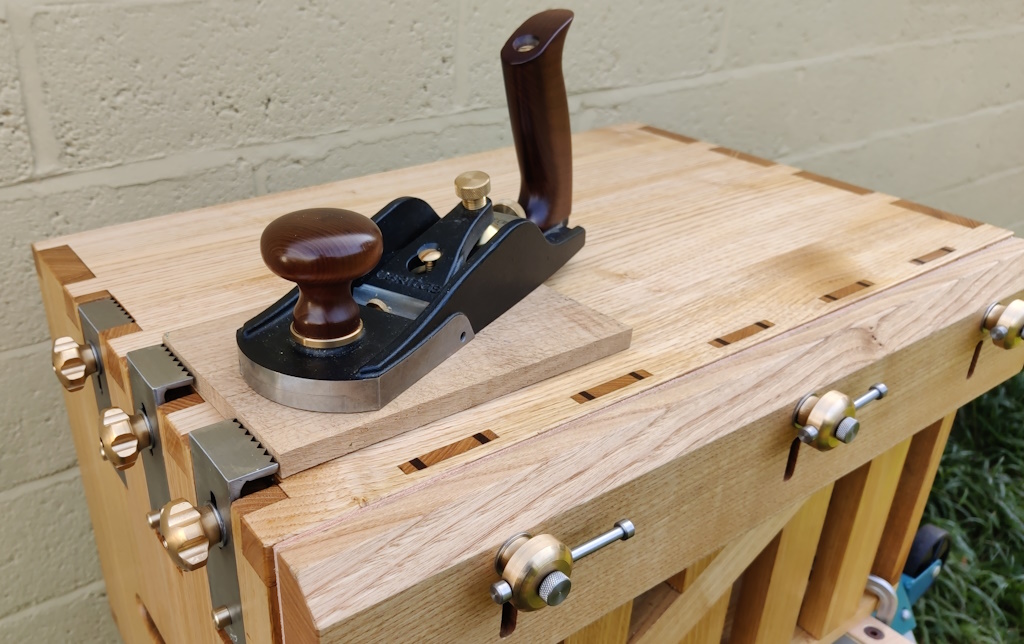
Or for a bit more robustness, a doe's foot can be clamped to the top:
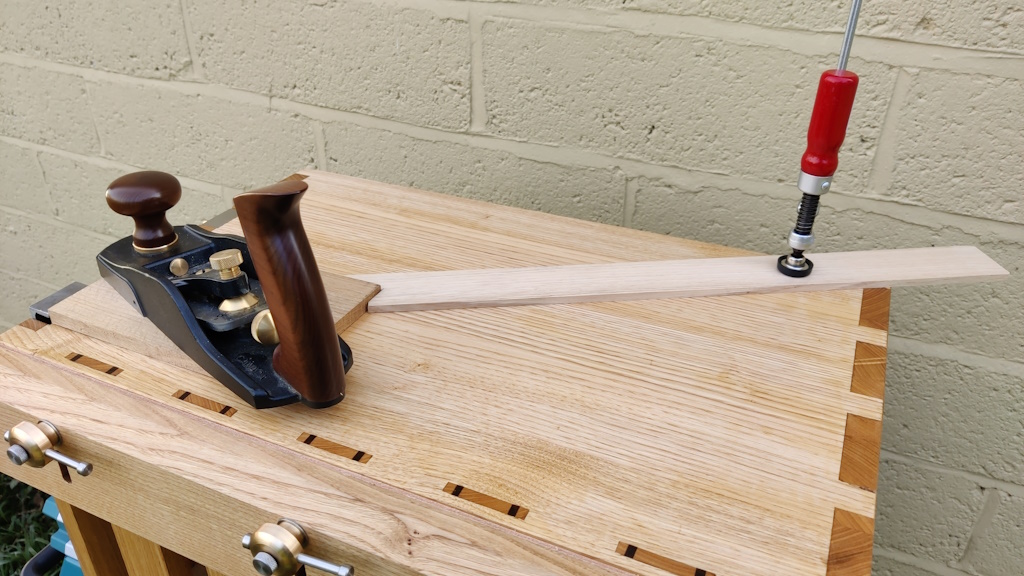
The vice can also be flipped round (so that a solid face is against the chest rather than a leather face) and then moved up and down (this photo shows the upper limit):
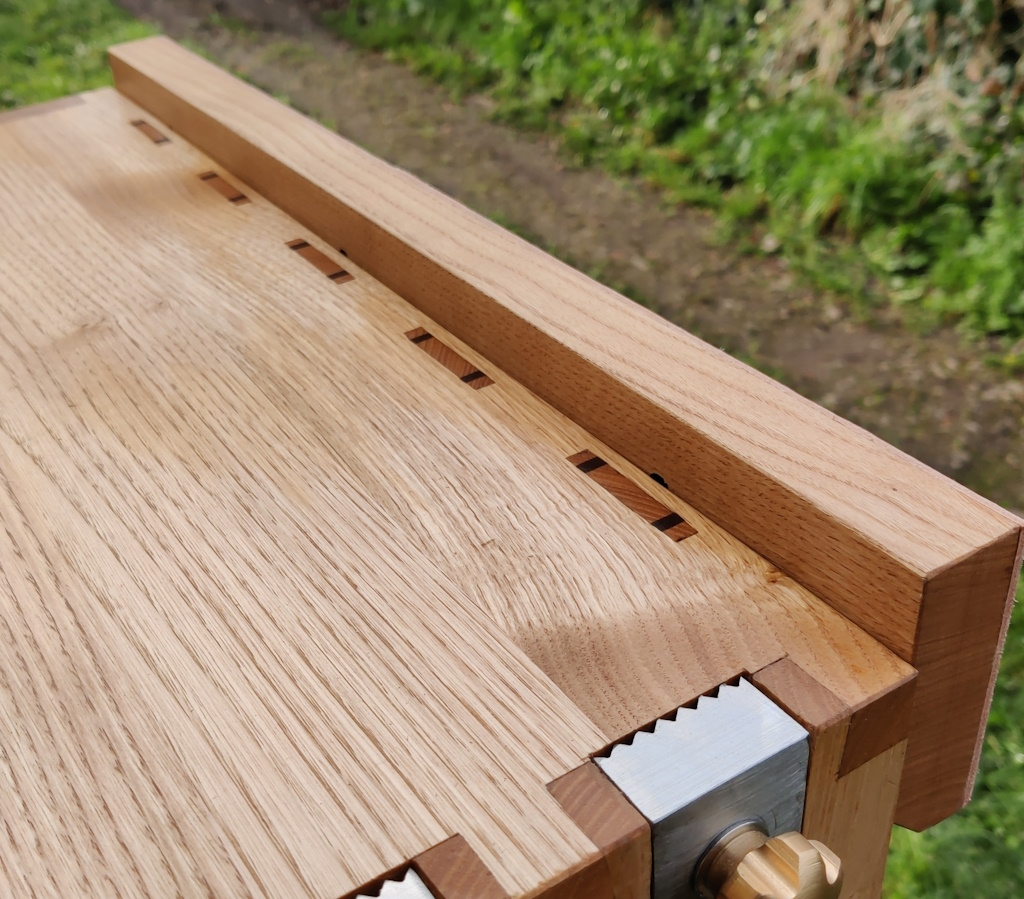
That allows boards to be fully constrained while still giving complete access to the top surface:
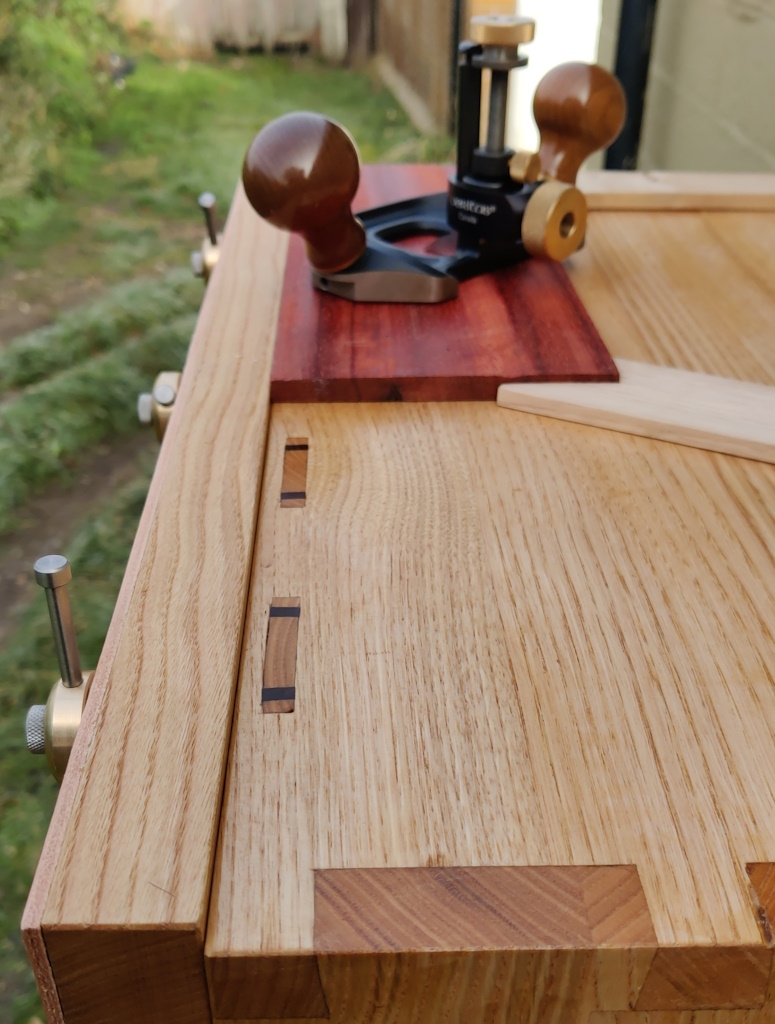
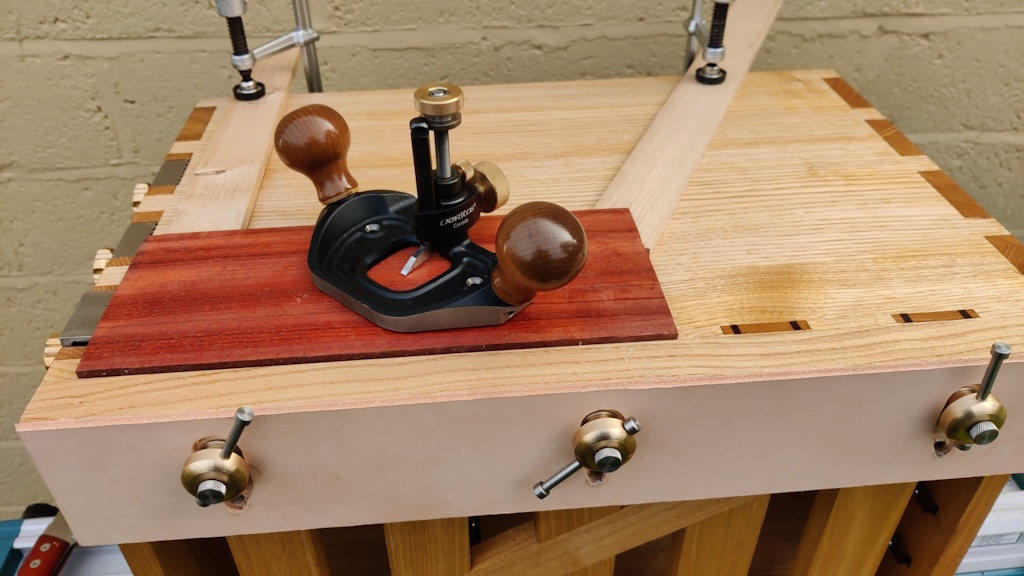
Finally (I think), there's the chest front / shooting board, which goes on top and pushes against the planing stops (this is the main reason for having three planing stops - so one is far enough over to support the shooting board near the working side)...
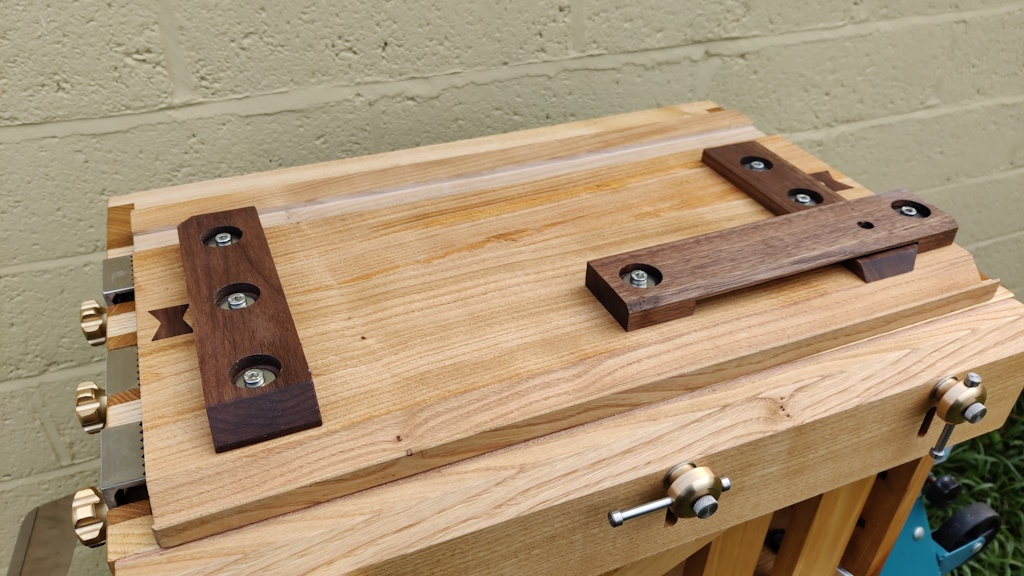
...which can be used for shooting ends square (with a block plane I also made, including the blade, as part of this project):
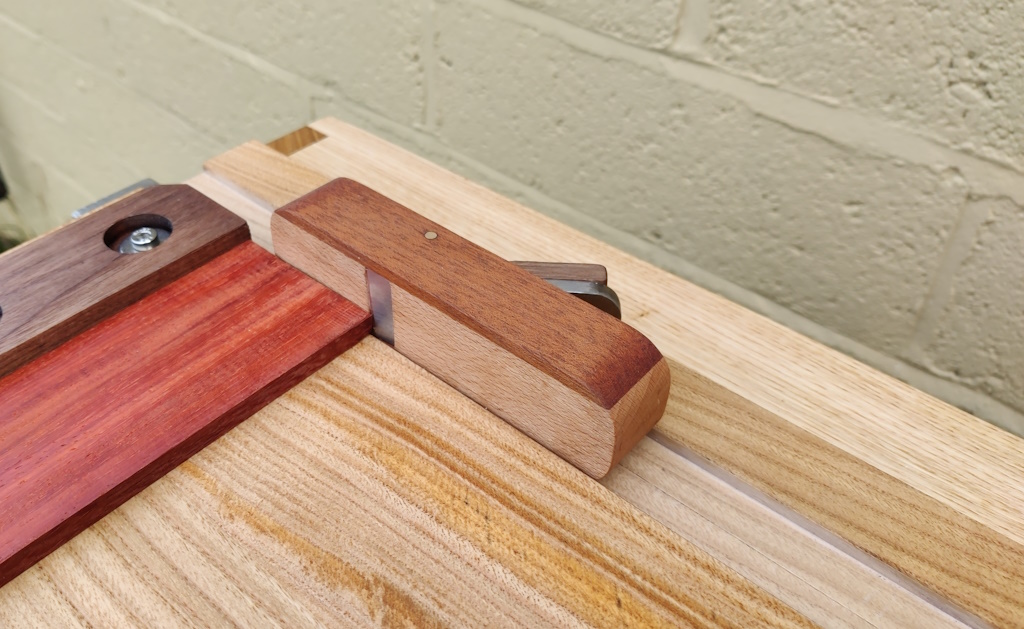
... and shooting mitres:
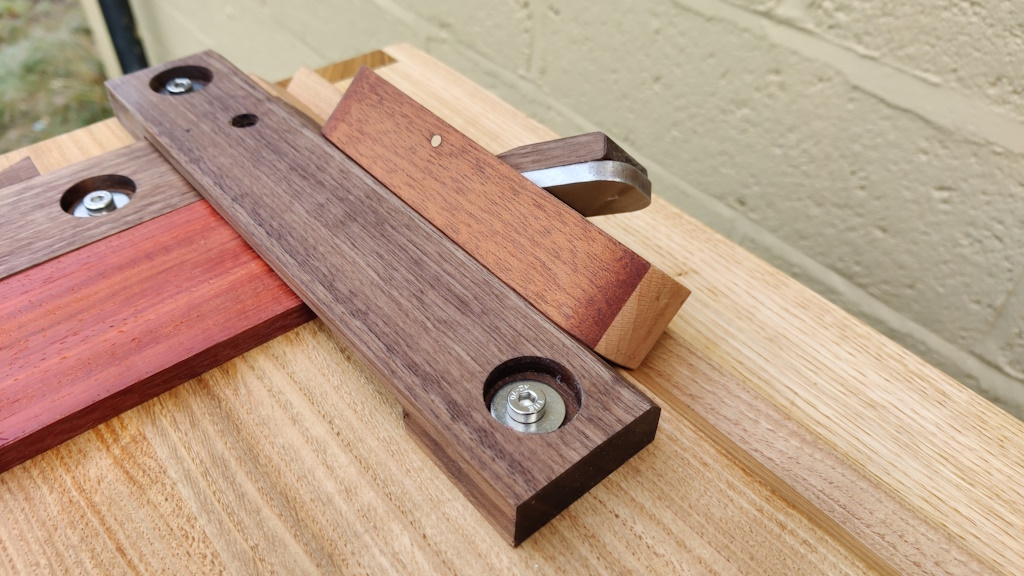
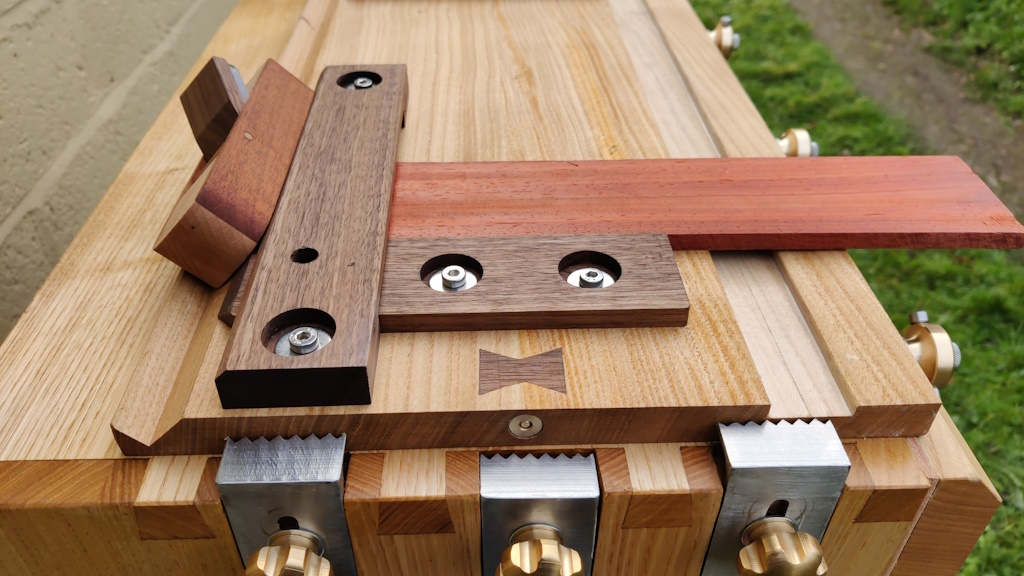
I mentioned that this project was mainly about learning and practising hand tool woodworking techniques. To expand on that, this was:
- The first project in which I've made panels from rough sawn wood by hand. In the past I've made panels, but they've involved a table saw (which I'm very happy to have now sold!) and/or thicknesser (which I've still got, but it's nice to be able to work without it, especially given the amount of snipe from my cheap-ish thicknesser). I've planed wood to size by hand in the past, but only relatively small pieces (for boxes) and this is the first time I've had to make lots of pieces of wood square edged and the same size.
- The first project where I've cut dovetails without any sort of saw guide. I've cut quite a lot of dovetails with 3D printed saw guides and I've cut a few (not very successful) dovetails without the guides on bits of scrap wood for practice, but this is the first finished project that includes guide-less dovetails. Also the first time I've cut dovetails on such thick wood: all previous ones have been on box-scale projects, so 10-ish mm thick rather than 20 mm thick.
- The first project in which I've cut housing joints (for the middle upright support and the drawer runners) - known as dadoes in America I believe.
- The first project with wedged through mortice-and-tenon joints (for the rear uprights). I used blind mortice-and-tenons on my side table, but the tenons were cut with a table saw and the fact that the mortices are blind makes them a lot easier! I'd done a few practice joints (with varying levels of success!) in offcuts, but never used them in a project.
- The first project with half-lap dovetails (for the drawer fronts). I'd done exactly one practice piece before starting this project.
- The first project with wooden drawers. Unless you count pocket-hole joined plywood boxes with ball-bearing slide runner things, I'd never made a wooden drawer before this project.
- The first project with half-lap joints (on the anti-racking diagonal piece on the back).
- The first project in which I've used protein-based glue (most joints with fish glue and some with TB hide glue).
- The first project where I've had to come up with my own way of dealing with wood movement. On previous projects I've just used well-known techniques (buttons for table tops, grooves for box bases), whereas making what is essentially a five sided box where all sides needed to be rigid took a bit more thought. Hopefully what I've done will last.
- The first time I've used a "Dutchman" / graving piece to repair a blemish. I used two different types of Dutchman: decorative butterfly ones in a contrasting wood and discrete grain matched ones.
- The first large project I've finished without sandpaper. The faces were finished with a smoothing plane without any of the dust and tedium of sanding (and I think it looks a lot better for it!). A scotchbrite pad was used for rubbing between coats of finish ("Mike's Magic Mix": equal parts pure tung oil, satin varnish & white spirit) but that's a quick job compared with sanding large surfaces.
- The first time I've tried photolithography (for etching the numbers that are inset into the top of each drawer front to help re-fit them in the right place as they're removed when the tool chest is in use).
- The biggest and most complicated hand-tool project (and woodworking project in general) I've done. I did use a bandsaw for some bits of resawing, but all the other woodwork was by hand. Metalwork was all powered, but that doesn't bother me as I hate filing and don't even aspire to being a hand-tool metalworker. Woodwork power tools are noisy and dusty, but most metalwork power tools I use aren't (angle grinders being the obvious exception). Welding the planing stops without some sort of power source would have been quite a challenge!