Derek Cohen (Perth Oz)
Established Member
Many of my projects involve bow fronts, which result in compound angle dovetails ...
I do enjoy building furniture with dovetailing challenges.
Between furniture pieces, I find time to build a new tool. This time it is the Moxon dovetail vise I have been promising myself for a while. My first and only one was built in early 2011, after Chris Schwarz helped put it on the map. I immediately modified this design, and have been making modifications since. (Link: http://www.inthewoodshop.com/ShopMadeTo ... lVise.html). This new Moxon incorporates the best ideas.
Ironically, this design is not geared for compound angles. I decided to heed my own advice and keep it as simple as possible, and cater for the 90% of the dovetailing that is likely to be done.
The width of the vise is narrower than my previous one, but capable of 450mm (17 3/4")between the screws. Most cases I built are between 350 - 450mm deep. My previous Moxon could do 560mm (22") between the screws. This is unnecessary, and just makes for a very large fixture.
Where the old Moxon used wooden screws, which I turned, this uses steel Acme screws and iron wheels ala BenchCrafted ... except that these came via Tom Bussey (thanks Tom), which amounted to a large savings. The wheels are 5" in diameter on a 3/4" screw.
The front chop is 5 1/2" high, and the Moxon is built in Jarrah ... what else do you expect!
I went a little OTT in this build, but it was fun, and I admit I did become a little carried away 
Brass inlay ...
The chop runs on bronze bushings ...
Lining the inside of the vise is rubberised cork. This makes a great non-slip (not my idea - this comes from BenchCrafted, who call it "crubber". Simply search eBay for "cork rubber").
This vise is a good height for sawing ...
There are a few innovations. The rear of the vise ...
This is a spacer, and it can be locked into the up position ...
The spacer has two functions. The first is setting the pin board (10mm) above the chop to prevent scoring the chop when transferring tails to pins with a knife (this is more of a danger with through dovetails). Also, by lifting the work, there will be light behind the pin board, and this makes it easier to align the edges.
The crubber makes a great non-slip.
The spacer may be dropped out of the way, once the height is set ...
The second use of the spacer is that it has a sliding dovetail at the top, and this allows for the use of MicroJig clamps. This would be especially useful for holding wide boards, or tail board which have developed a slight bow ...
I have used this on other fixtures, such as a morticing jig.
For aligning the tail- and pin boards, I prefer a simple wide square I made from wood ...
The spacer needs to be dropped out of the way for this ...
Once transfer is made, reverse the board and saw the pins. This is where you will recognise that the cove is not simply decoration, but allows the saw to angle and get closer to the work piece. The lower the work piece in the vise, the less vibration when sawing ...
And thats it ... the last moxon dovetail vise ...
Regards from Perth
Derek
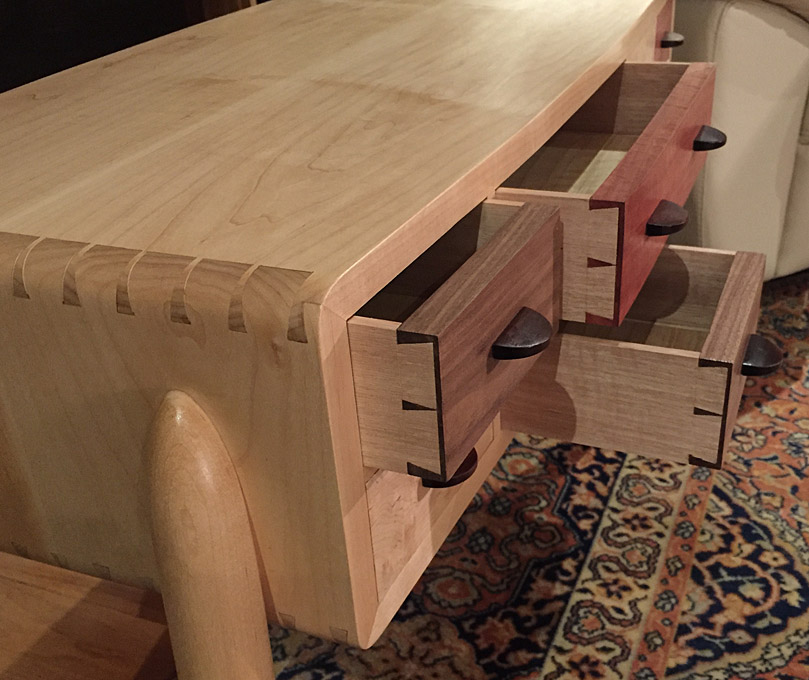
I do enjoy building furniture with dovetailing challenges.
Between furniture pieces, I find time to build a new tool. This time it is the Moxon dovetail vise I have been promising myself for a while. My first and only one was built in early 2011, after Chris Schwarz helped put it on the map. I immediately modified this design, and have been making modifications since. (Link: http://www.inthewoodshop.com/ShopMadeTo ... lVise.html). This new Moxon incorporates the best ideas.
Ironically, this design is not geared for compound angles. I decided to heed my own advice and keep it as simple as possible, and cater for the 90% of the dovetailing that is likely to be done.
The width of the vise is narrower than my previous one, but capable of 450mm (17 3/4")between the screws. Most cases I built are between 350 - 450mm deep. My previous Moxon could do 560mm (22") between the screws. This is unnecessary, and just makes for a very large fixture.
Where the old Moxon used wooden screws, which I turned, this uses steel Acme screws and iron wheels ala BenchCrafted ... except that these came via Tom Bussey (thanks Tom), which amounted to a large savings. The wheels are 5" in diameter on a 3/4" screw.
The front chop is 5 1/2" high, and the Moxon is built in Jarrah ... what else do you expect!
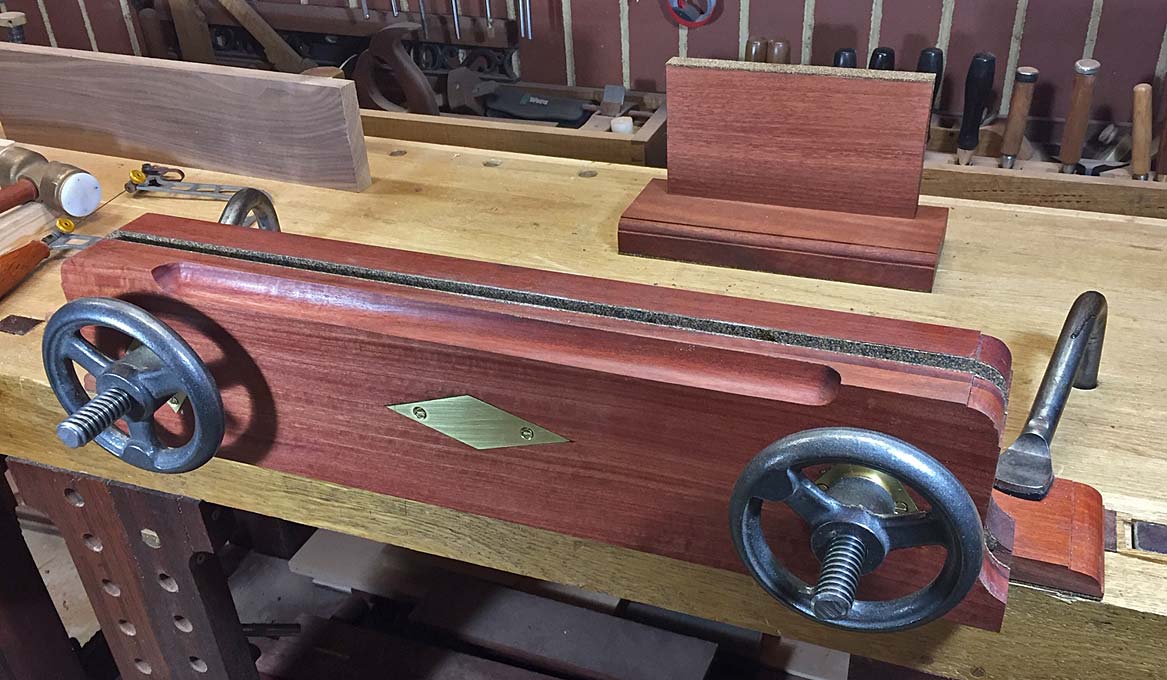
Brass inlay ...
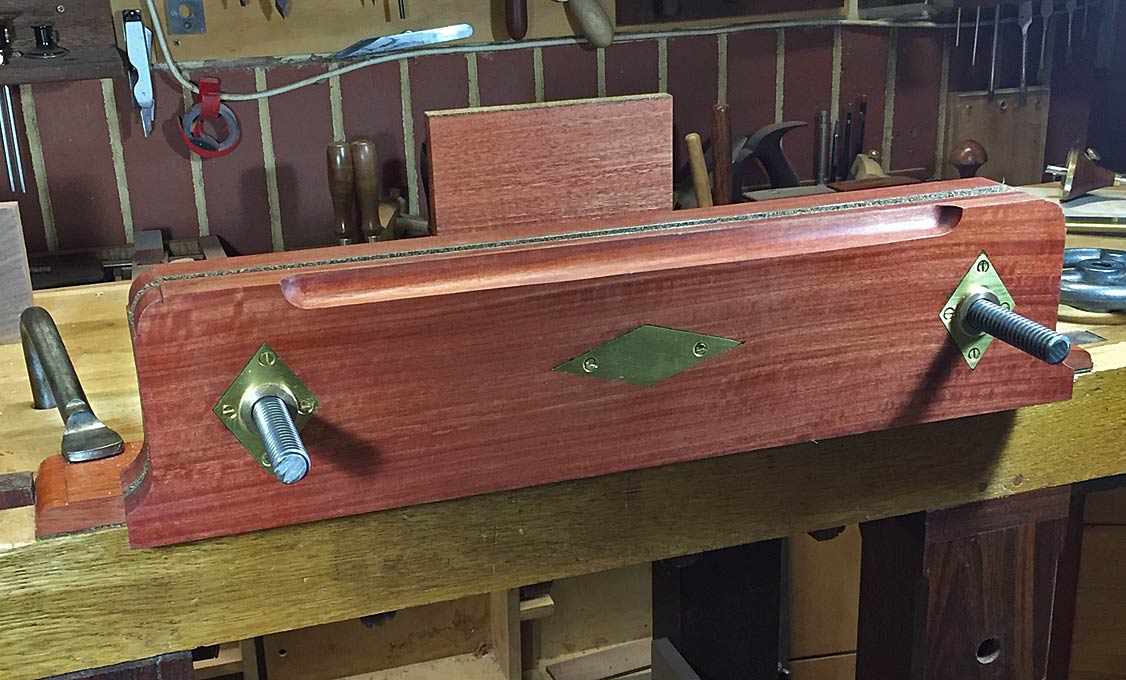
The chop runs on bronze bushings ...
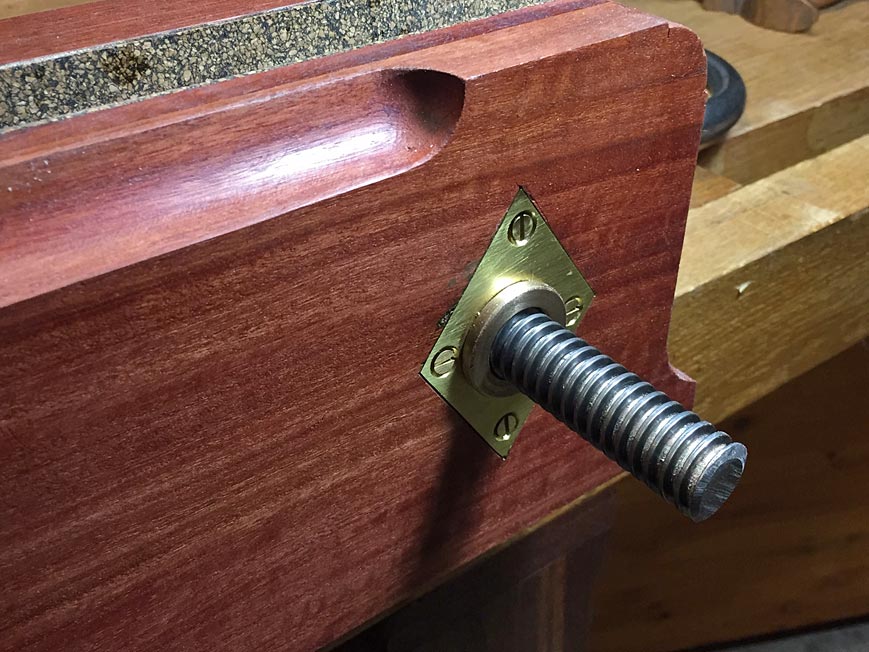
Lining the inside of the vise is rubberised cork. This makes a great non-slip (not my idea - this comes from BenchCrafted, who call it "crubber". Simply search eBay for "cork rubber").
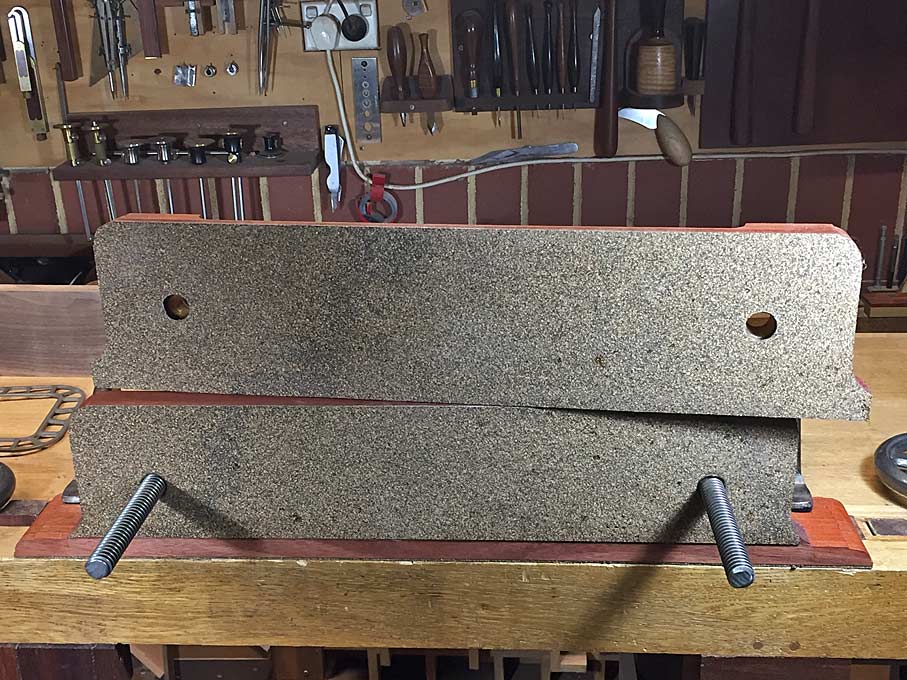
This vise is a good height for sawing ...
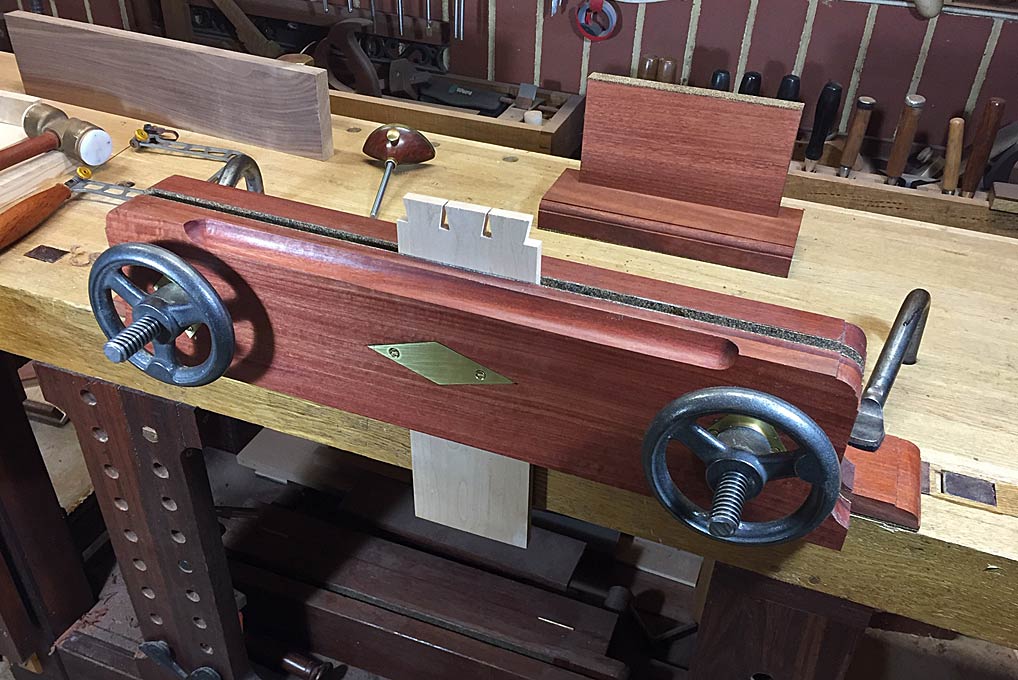
There are a few innovations. The rear of the vise ...
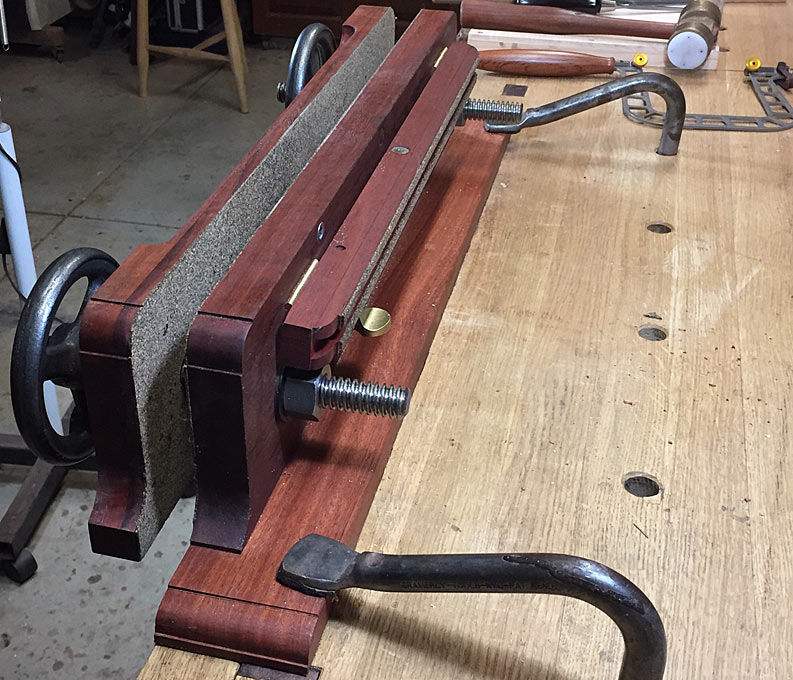
This is a spacer, and it can be locked into the up position ...
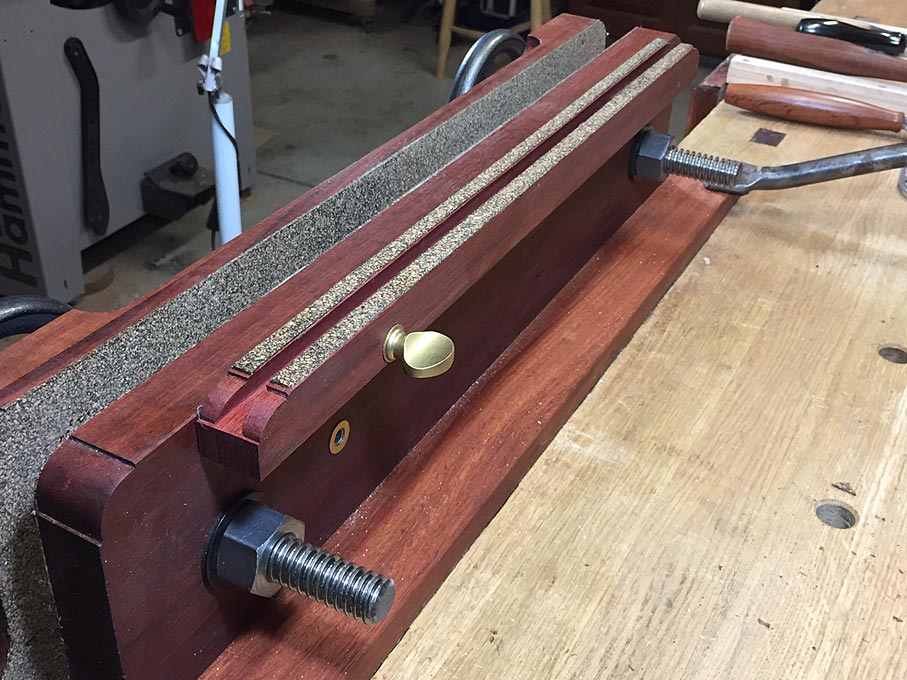
The spacer has two functions. The first is setting the pin board (10mm) above the chop to prevent scoring the chop when transferring tails to pins with a knife (this is more of a danger with through dovetails). Also, by lifting the work, there will be light behind the pin board, and this makes it easier to align the edges.
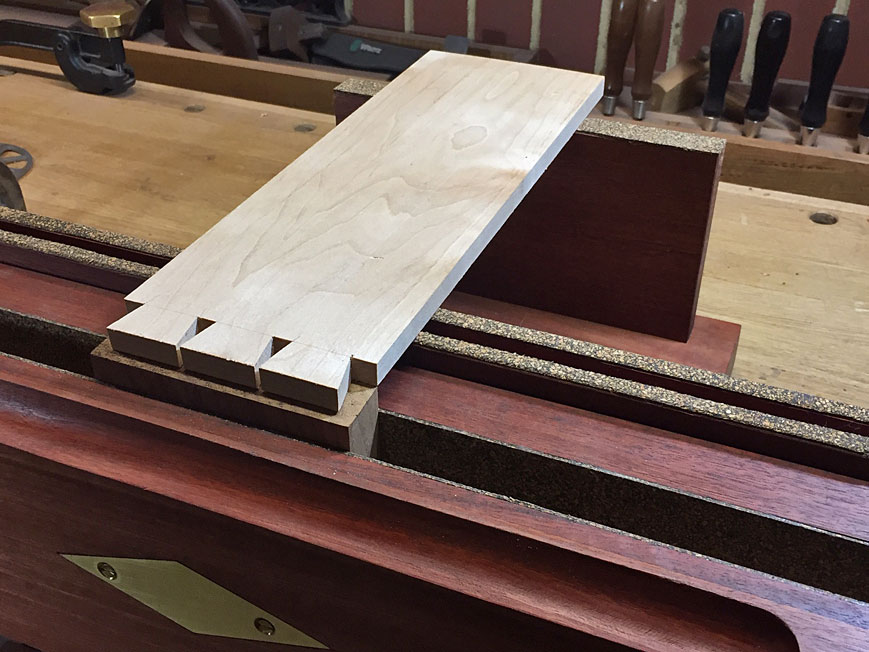
The crubber makes a great non-slip.
The spacer may be dropped out of the way, once the height is set ...
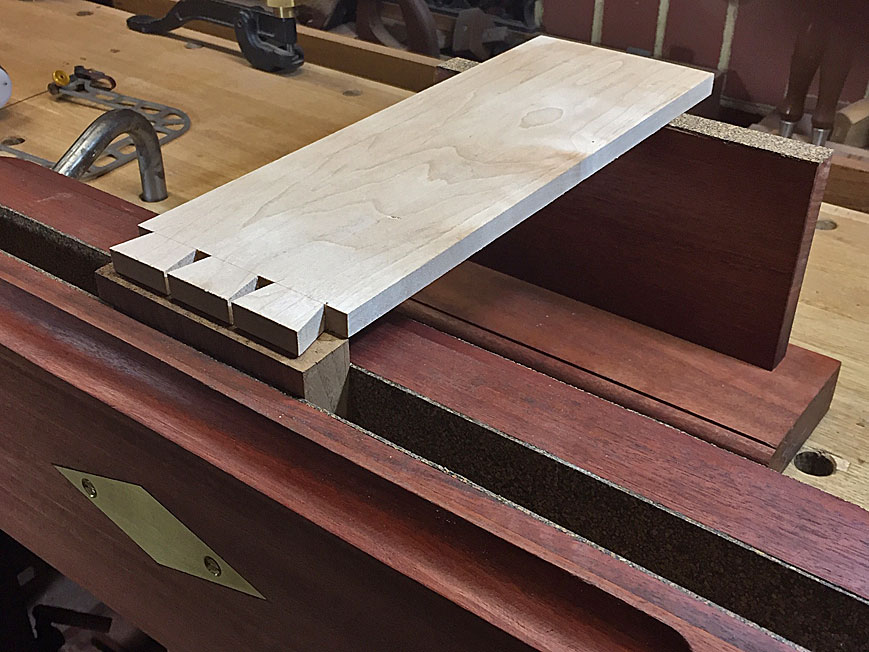
The second use of the spacer is that it has a sliding dovetail at the top, and this allows for the use of MicroJig clamps. This would be especially useful for holding wide boards, or tail board which have developed a slight bow ...
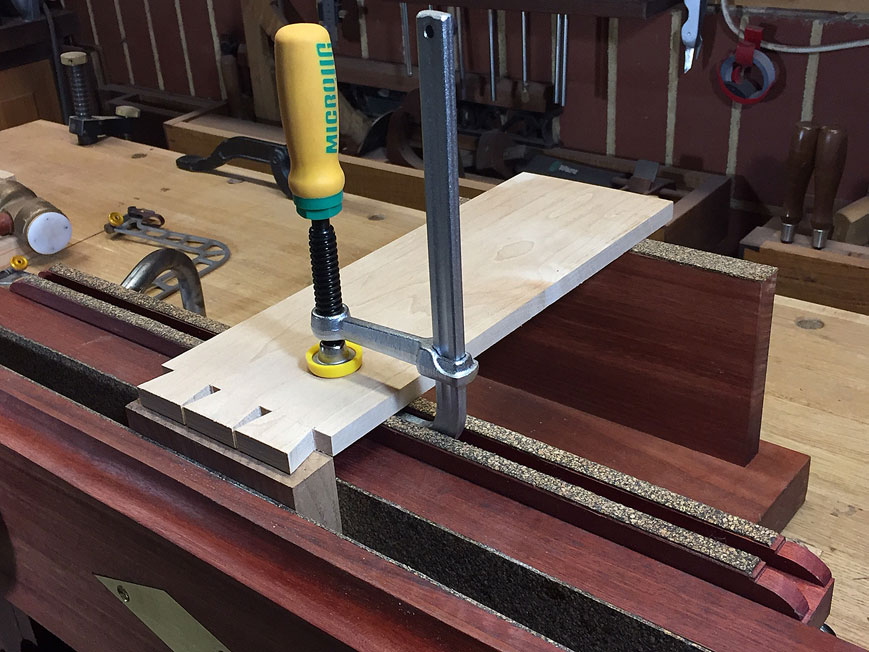
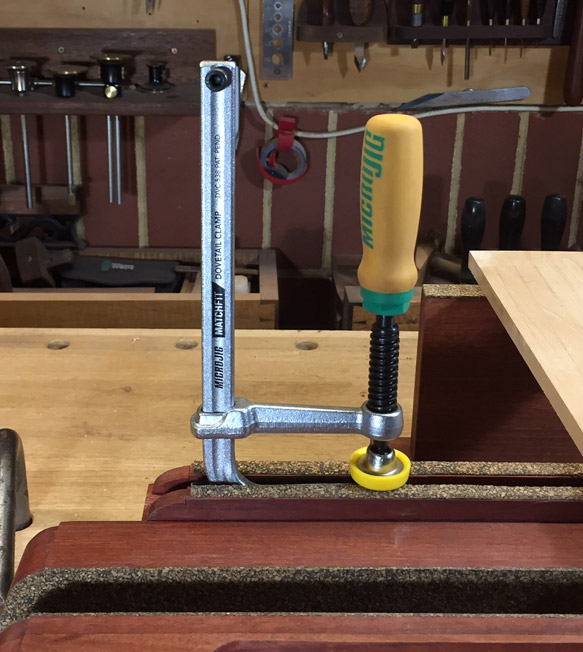
I have used this on other fixtures, such as a morticing jig.
For aligning the tail- and pin boards, I prefer a simple wide square I made from wood ...
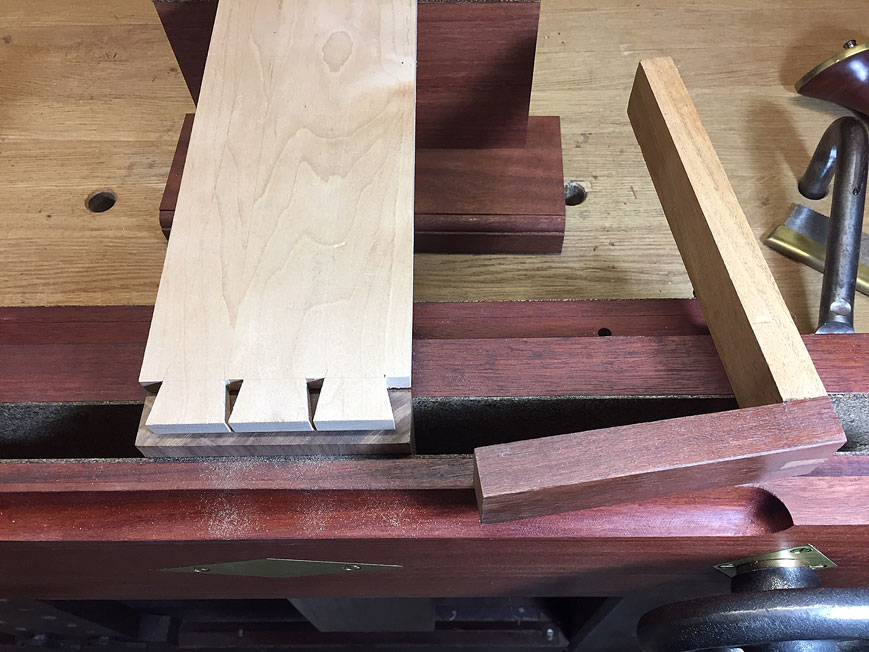
The spacer needs to be dropped out of the way for this ...
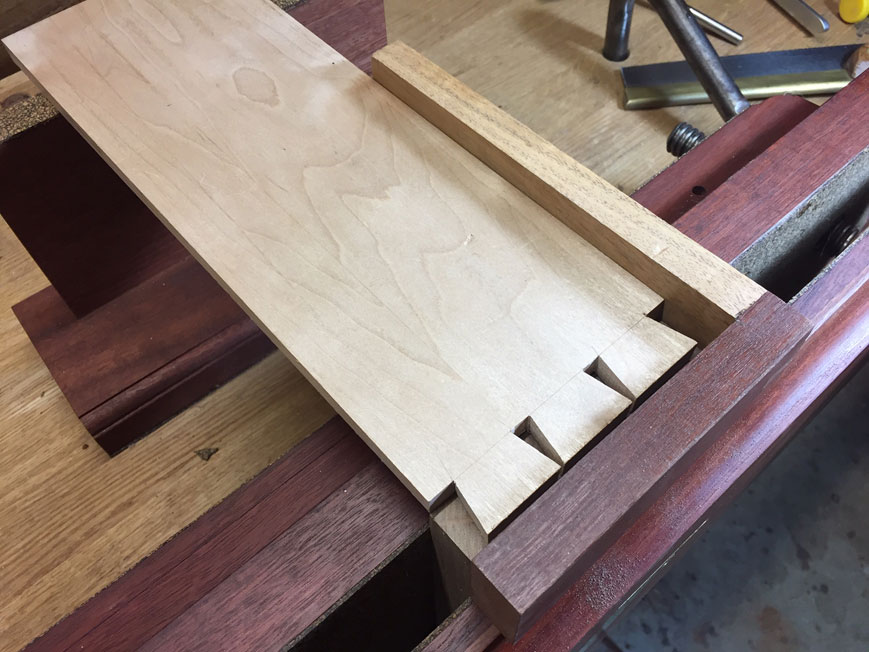
Once transfer is made, reverse the board and saw the pins. This is where you will recognise that the cove is not simply decoration, but allows the saw to angle and get closer to the work piece. The lower the work piece in the vise, the less vibration when sawing ...
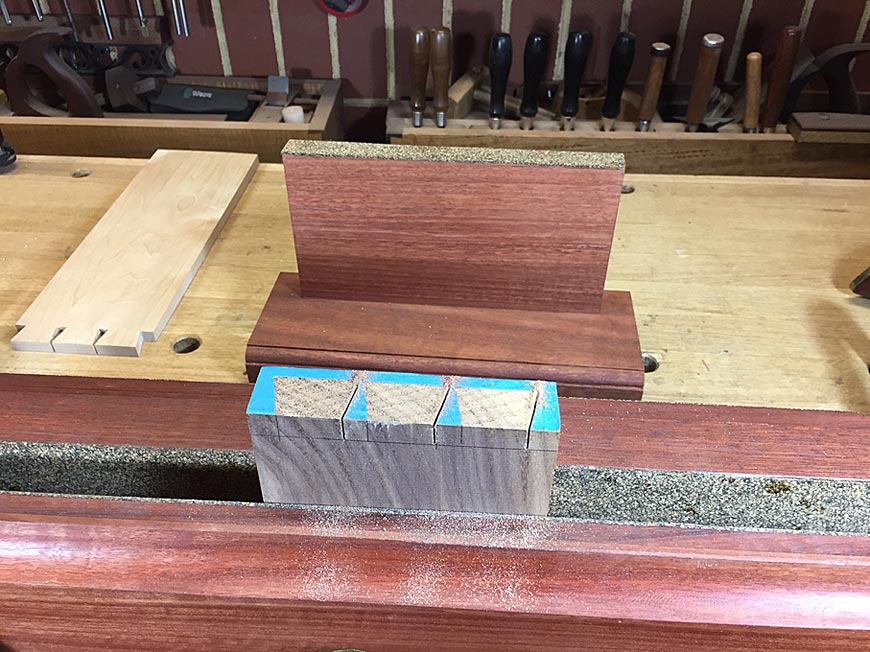
And thats it ... the last moxon dovetail vise ...
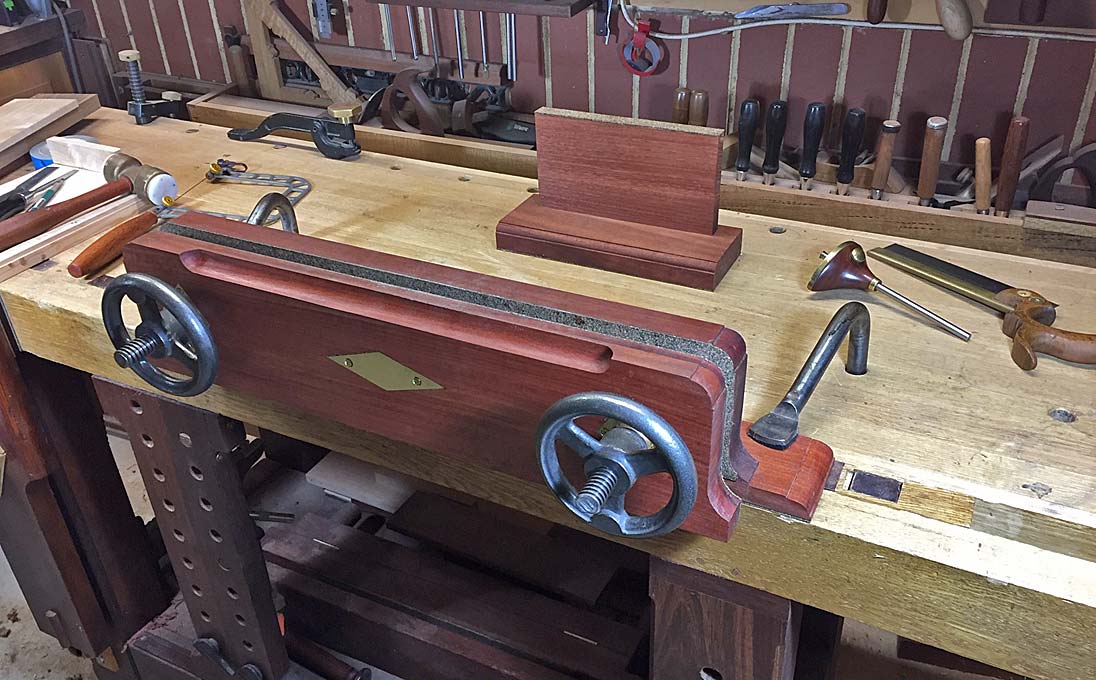
Regards from Perth
Derek