OPJ
Established Member
I'm trying to kill some time at college in between my two main projects so, with bits of brown oak left lying around, I've begun working on a small step stool. This won't be appearing in the magazine as it's taken straight from a book titled Building Small Projects so, it's not my design.
I can't think of many ways to improve it and I'd really like to have a go at some wedged tenons like this.
These are the offcuts I've chosen. It would've been nice to have gotten them from one length for grain continuity.
Here are the components after machining. I was aiming for a width of about 10", ending up with boards 240mm wide, which isn't bad, if you ask me. Because some boards weren't flat and had 'hidden dips' in them, I was only able to achieve a maximum finished thickness of 18mm, which is quite disappointing (the original design has a 1" finish; 22mm would've been nice). The boards weren't cupped at all; it's purely down to how they were cut or stacked.
Once I had all the components machined, I drew out a full size rod. I have to admit, this is something I probably wouldn't have done at home...!
I'll leave all the curved work until nearer the end so, don't worry about the rail or that badly-drawn curve on the end view! 
After the top to length on the panel saw, here, I'm setting out the mortises which will receive tenons from the two ends.
Because the legs are angled at 10°, I need to build a jig to drill the angled mortises accurately. I could just tilt the pillar drill table but, this jig will also come in handy for cutting the tenons. :wink:
This is where I'm at right now; ready to make the jig. It's Easter for the next two weeks and I'll be picking up with other things straight after. So, while I'm looking to keep you all up-to-date on how things progress, don't expect to see this one completed any time soon! Feel free to add any comments though. :wink:
These are the offcuts I've chosen. It would've been nice to have gotten them from one length for grain continuity.
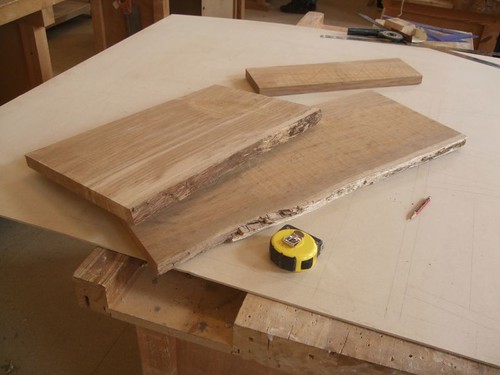
Here are the components after machining. I was aiming for a width of about 10", ending up with boards 240mm wide, which isn't bad, if you ask me. Because some boards weren't flat and had 'hidden dips' in them, I was only able to achieve a maximum finished thickness of 18mm, which is quite disappointing (the original design has a 1" finish; 22mm would've been nice). The boards weren't cupped at all; it's purely down to how they were cut or stacked.
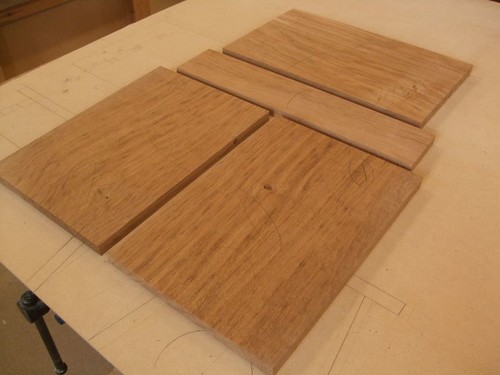
Once I had all the components machined, I drew out a full size rod. I have to admit, this is something I probably wouldn't have done at home...!
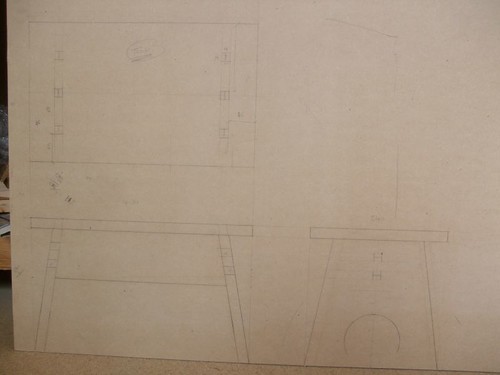
After the top to length on the panel saw, here, I'm setting out the mortises which will receive tenons from the two ends.
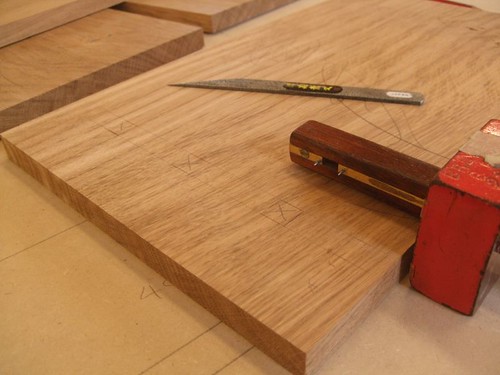
Because the legs are angled at 10°, I need to build a jig to drill the angled mortises accurately. I could just tilt the pillar drill table but, this jig will also come in handy for cutting the tenons. :wink:
This is where I'm at right now; ready to make the jig. It's Easter for the next two weeks and I'll be picking up with other things straight after. So, while I'm looking to keep you all up-to-date on how things progress, don't expect to see this one completed any time soon! Feel free to add any comments though. :wink: