devonwoody
Established Member
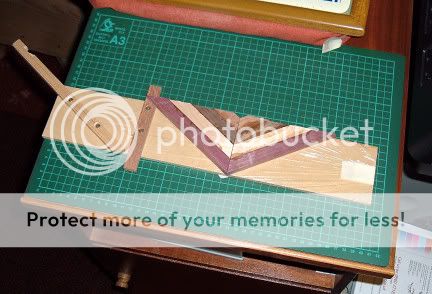
The part portion of front of the chevron box , this is the section that has got to be glued but entails 100%end grain has pictured.
devonwoody":1yxkh1e6 said:I raised the blade on my tablesaw just sufficiently to cut the third edge to size and the small panel drifted into the riving knife guard slots and gave me a bad cut.
So took the riving knife off and raised the blade well above the timber
Mike.C":2t21yz88 said:John PM sent
Cheers
Mike