A
Anonymous
Guest
Heres a few pics of some stools and a chair I have been working on recentley
This one is based on the basic irish fire side chair form, it has been distressed but as yet un stained, oiled or waxed or anything; made up from burr elm, ash, pine and recycled floorboard's
This one is a 3 legged kiddie sized chair, again based on an irish form. It has been stained with various glazes then cut back with caustic and wire wool, also un oiled or waxed as yet. Ash, with seat made of the sink cut out from my worktop off cut.
Final one is another 3 leg kiddies one that I made some while ago but wanted to work on the finish so I cut it off with custic/sugar soap etc then used red oil glaze then heated buffed up wax (as in Ian hosker's finishing book which I just got) Made from ash and old joist's
I'm trying to create an aged distressed look and texture in all my piece's but its a lot harder than it would seem to be to look convincing (I'm not trying to con people, but real old country furniture fetch's silly prices now :roll: ) I like to deliberately make some component's slightly wonky just as you get with old primitive furniture.
I got a much bigger 3 leg welsh-type chair in progress I'll post some pics in due course. I'm sourcing firewood suppliers that will save decent crooks and bends and sections from the base of the tree (= flared klismos legs) and to make up a 3 part joined arm
cheers Jonathan
:lol:
This one is based on the basic irish fire side chair form, it has been distressed but as yet un stained, oiled or waxed or anything; made up from burr elm, ash, pine and recycled floorboard's
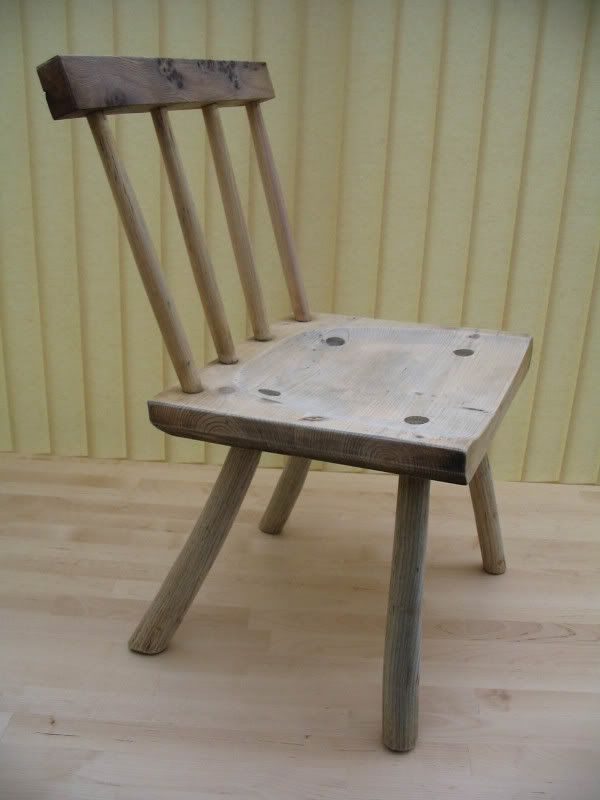
This one is a 3 legged kiddie sized chair, again based on an irish form. It has been stained with various glazes then cut back with caustic and wire wool, also un oiled or waxed as yet. Ash, with seat made of the sink cut out from my worktop off cut.
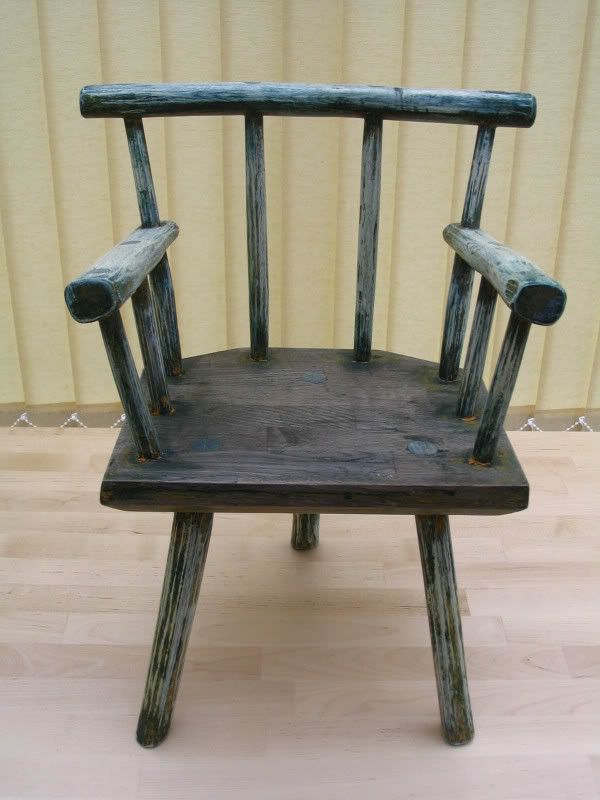
Final one is another 3 leg kiddies one that I made some while ago but wanted to work on the finish so I cut it off with custic/sugar soap etc then used red oil glaze then heated buffed up wax (as in Ian hosker's finishing book which I just got) Made from ash and old joist's
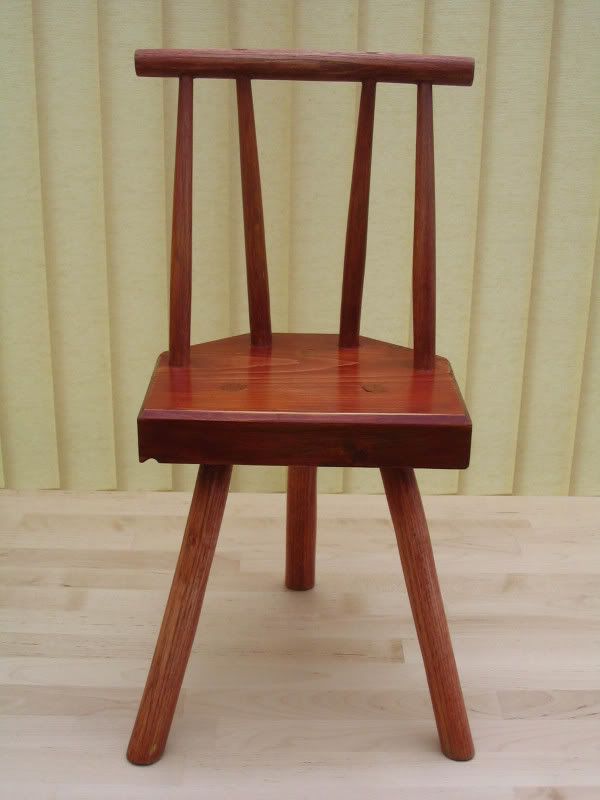
I'm trying to create an aged distressed look and texture in all my piece's but its a lot harder than it would seem to be to look convincing (I'm not trying to con people, but real old country furniture fetch's silly prices now :roll: ) I like to deliberately make some component's slightly wonky just as you get with old primitive furniture.
I got a much bigger 3 leg welsh-type chair in progress I'll post some pics in due course. I'm sourcing firewood suppliers that will save decent crooks and bends and sections from the base of the tree (= flared klismos legs) and to make up a 3 part joined arm
cheers Jonathan