Nigel Taylor
Established Member
I bought a small kiln and just had to explore some different techniques. This took a few experiments to get right but I think the resultant joint is rather nice (this brass part is roughly 25mm or 1 inch in length)
and a youtube (a bit rough) of me making this silver soldered join
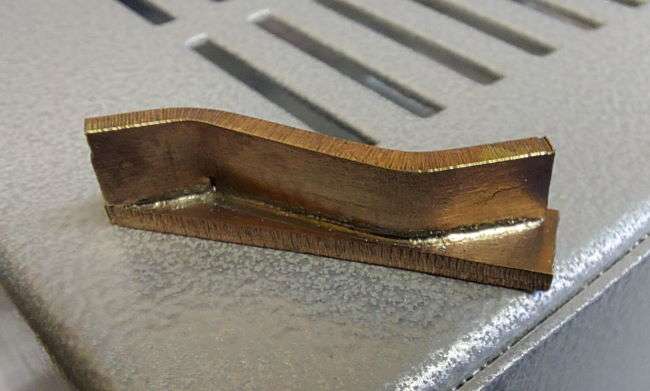
and a youtube (a bit rough) of me making this silver soldered join