I suppose I should put a post up about this, I have been asked to make a drinks cabinet round an existing small fridge, I presented my friend with a couple of options, and they decided that this design matched their existing furniture best.
I sourced the timber locally, Douglas Fir for the Top and the paneling and surprisingly (to me at least) Western Red Cedar for the framework. Having aquired it as 4m waney edged boards, I had to get it on the trestles and cut off a sufficient length (8ft) to cut a complete set of components, then take that smaller board and first establish a reference edge, then rip it down into the appropriate widths (1¾"*1¾" for the framework, 1"*11.5" for the table top segments) and cut the individual components to length. This was only achieved once I'd finished modifying the fence of the outfeed table on my RAS, and re-aliging the RAS blade square and true after the saw initially began pinching as it started to cut.
The rough sawn segments are now waiting to go to my friends house to acclimate (my house is much smaller, warmer and drier than his, unfortunately). hopefully after a week or two I'll be able to start planing them up.
I'll try to get some pictures of both the unsawn boards and cut components tomorrow.
I also have to drive over to Blanaeu Ffestiniog to collect a piece of slate riven specifically for the top at some point.
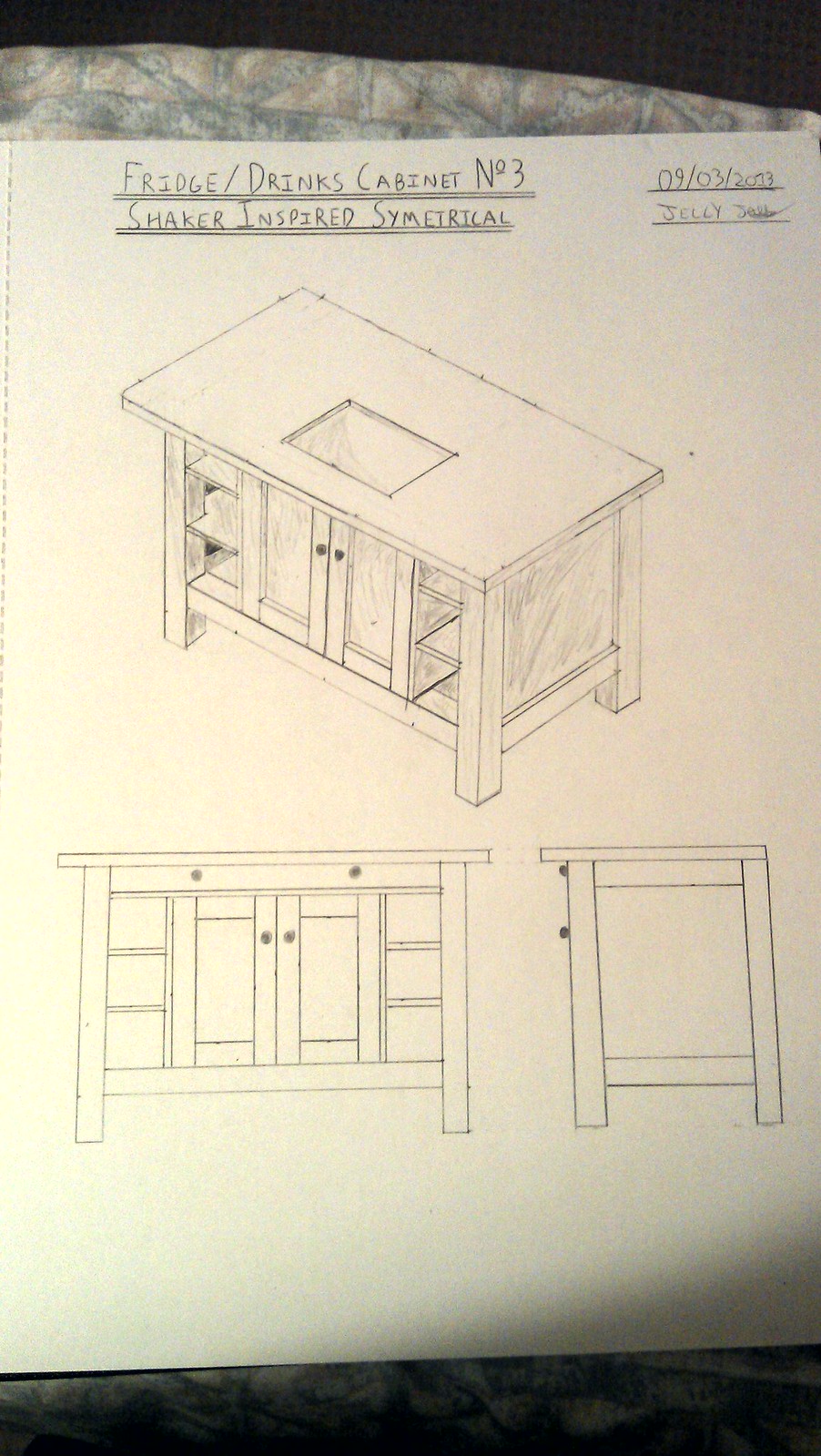
I sourced the timber locally, Douglas Fir for the Top and the paneling and surprisingly (to me at least) Western Red Cedar for the framework. Having aquired it as 4m waney edged boards, I had to get it on the trestles and cut off a sufficient length (8ft) to cut a complete set of components, then take that smaller board and first establish a reference edge, then rip it down into the appropriate widths (1¾"*1¾" for the framework, 1"*11.5" for the table top segments) and cut the individual components to length. This was only achieved once I'd finished modifying the fence of the outfeed table on my RAS, and re-aliging the RAS blade square and true after the saw initially began pinching as it started to cut.
The rough sawn segments are now waiting to go to my friends house to acclimate (my house is much smaller, warmer and drier than his, unfortunately). hopefully after a week or two I'll be able to start planing them up.
I'll try to get some pictures of both the unsawn boards and cut components tomorrow.
I also have to drive over to Blanaeu Ffestiniog to collect a piece of slate riven specifically for the top at some point.