RossJarvis
Established Member
For my next trick, I will attempt to make a scarf joint, without aid of assistants or a safety net, you people in the front three rows may wish to stand back a bit, or at least don a Mackintosh.
Once again, cut a bit of oak off the bit of oak I really really wanted to get this cut square as I’m still not brilliant at this. It seems that I can do it when not concentrating, but not when I am?!? So I found an old trick to help. First knife your mark square, then chisel into it a bit then cut on this mark;
…zzzd zzzd zzd zzd and you should have a perfectly square cut, did I? Did I b*****y!;
So I thought I’d trim the end, using a nice square block of wood as a guide (luckily I’d made one earlier);
….now we should have a nice square end. However we still actually had a b******d end so I took the block plane to it and Viola;
Time for a quick walk wi’ t’ apprentice. Boy, you need to see my nuts now, much bigger than the last time I showed you, plus the weather’s cooler now;
Back at the wood and I’ve discovered that the white pithy bits are white rot. This is a fungal thing and was in the tree when it was still standing. It appears to travel up the grain and turns the wood to fluff. I’m not sure how much is in the whole lot, but this bit of the block just fell out. The wood on either side of the ring seems sound;
…ssshhhhh shhh ssshhhh, with the plane, ooh that’s a nice shaving;
…..and we have a nice square lump of wood, just a touch of work to remove a slight slope and it’ll be great. I think I’m getting better as I haven’t had to take as much off to get this square;
As the Hampshire monsoon is upon us again, I’m taking the time to work out whether to do a Japanese scarf, or an English one. In many respects they’re identical with the odd slight difference. There are some English ones every bit as fiendish as the Japanese ones. This is the “Kanawa Tsugi” which is one option;
I’ll put some thinking tea on (Taylor’s Yorkshire today) and look up some more and get back to you if I’ve made a decision or when I’ve b******d up some more wood.
Once again, cut a bit of oak off the bit of oak I really really wanted to get this cut square as I’m still not brilliant at this. It seems that I can do it when not concentrating, but not when I am?!? So I found an old trick to help. First knife your mark square, then chisel into it a bit then cut on this mark;
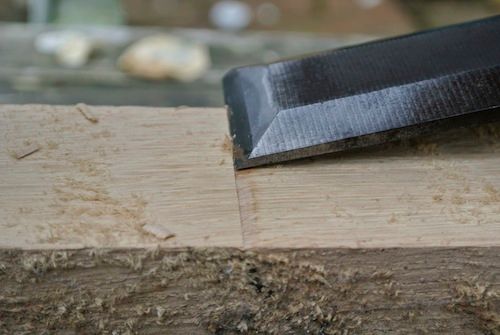
…zzzd zzzd zzd zzd and you should have a perfectly square cut, did I? Did I b*****y!;
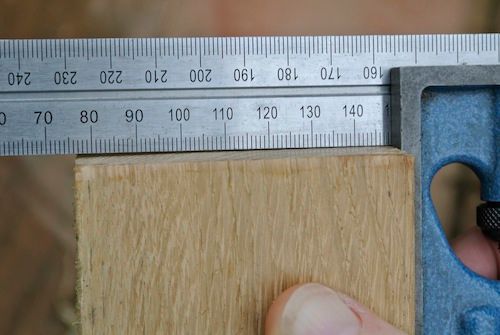
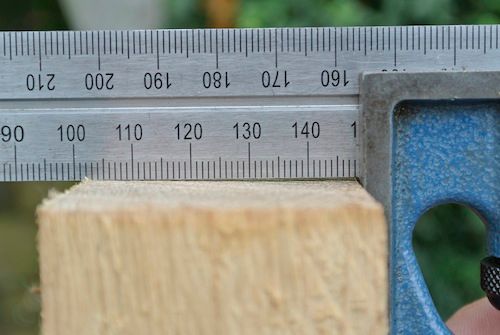
So I thought I’d trim the end, using a nice square block of wood as a guide (luckily I’d made one earlier);
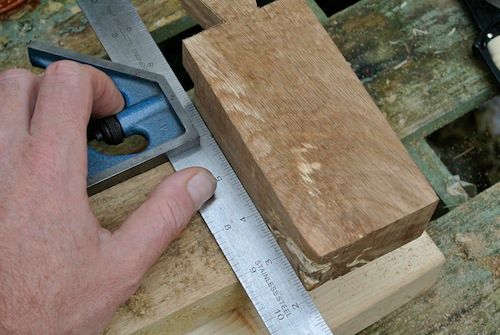
….now we should have a nice square end. However we still actually had a b******d end so I took the block plane to it and Viola;
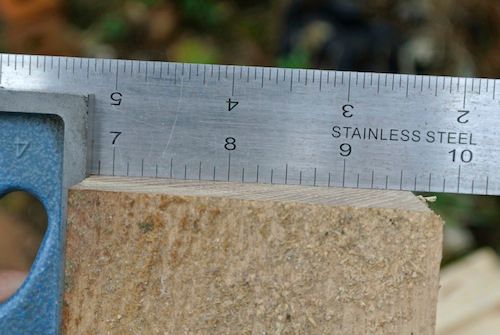
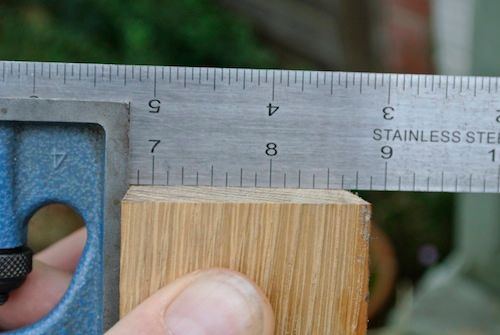
Time for a quick walk wi’ t’ apprentice. Boy, you need to see my nuts now, much bigger than the last time I showed you, plus the weather’s cooler now;

Back at the wood and I’ve discovered that the white pithy bits are white rot. This is a fungal thing and was in the tree when it was still standing. It appears to travel up the grain and turns the wood to fluff. I’m not sure how much is in the whole lot, but this bit of the block just fell out. The wood on either side of the ring seems sound;
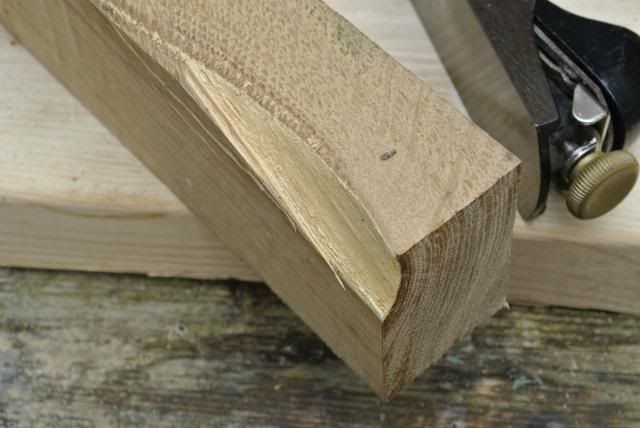
…ssshhhhh shhh ssshhhh, with the plane, ooh that’s a nice shaving;
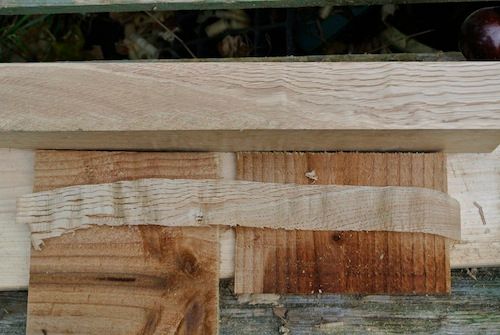
…..and we have a nice square lump of wood, just a touch of work to remove a slight slope and it’ll be great. I think I’m getting better as I haven’t had to take as much off to get this square;
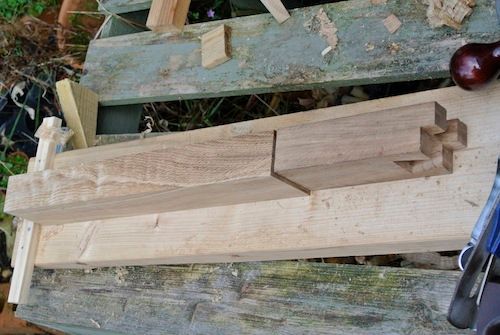
As the Hampshire monsoon is upon us again, I’m taking the time to work out whether to do a Japanese scarf, or an English one. In many respects they’re identical with the odd slight difference. There are some English ones every bit as fiendish as the Japanese ones. This is the “Kanawa Tsugi” which is one option;
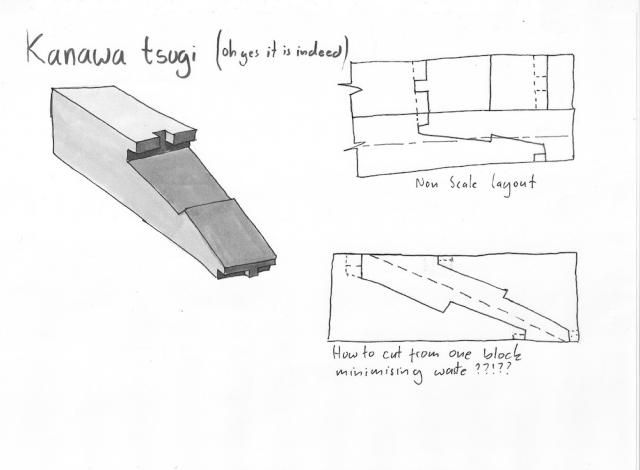
I’ll put some thinking tea on (Taylor’s Yorkshire today) and look up some more and get back to you if I’ve made a decision or when I’ve b******d up some more wood.