Sawdust=manglitter
Established Member
I’ve been keeping an eye out everywhere for a suitable bench grinder to convert to a buffer for both wood and metal. This morning I picked what I think is a cracking bargain, I bought this ridiculously heavy old cast iron Wolf 8” pedestal grinder which still works for £20!! 
So excitedly I got straight into stripping it down and to find out the spindle or thread size to try to convert it to a buffing machine. I took the right wheel off without a hitch and took off the guard etc, then I hit my first problem, the nut securing the left wheel appears to be completely stuck!!
I’ve left it soaking with wd40 in the hopes it will help, but does anyone have any tips on how best to get this nut loose without damaging the spindle (and ideally without damaging the nut)?? I assume I’m turning it the correct direction (anti clockwise, as the right wheel was clockwise).
Secondly, I have no clue at all when it comes to old imperial thread sizes. This is the exact size of the thread...
What should I be searching for as the thread size if I’m looking for a suitably sized tapered mandrel adaptor for buffing wheels/polishing mops?? I’d be surprised if I do manage to find one to fit, but I live in hope!!
Any help or tips would be greatly appreciated




So excitedly I got straight into stripping it down and to find out the spindle or thread size to try to convert it to a buffing machine. I took the right wheel off without a hitch and took off the guard etc, then I hit my first problem, the nut securing the left wheel appears to be completely stuck!!
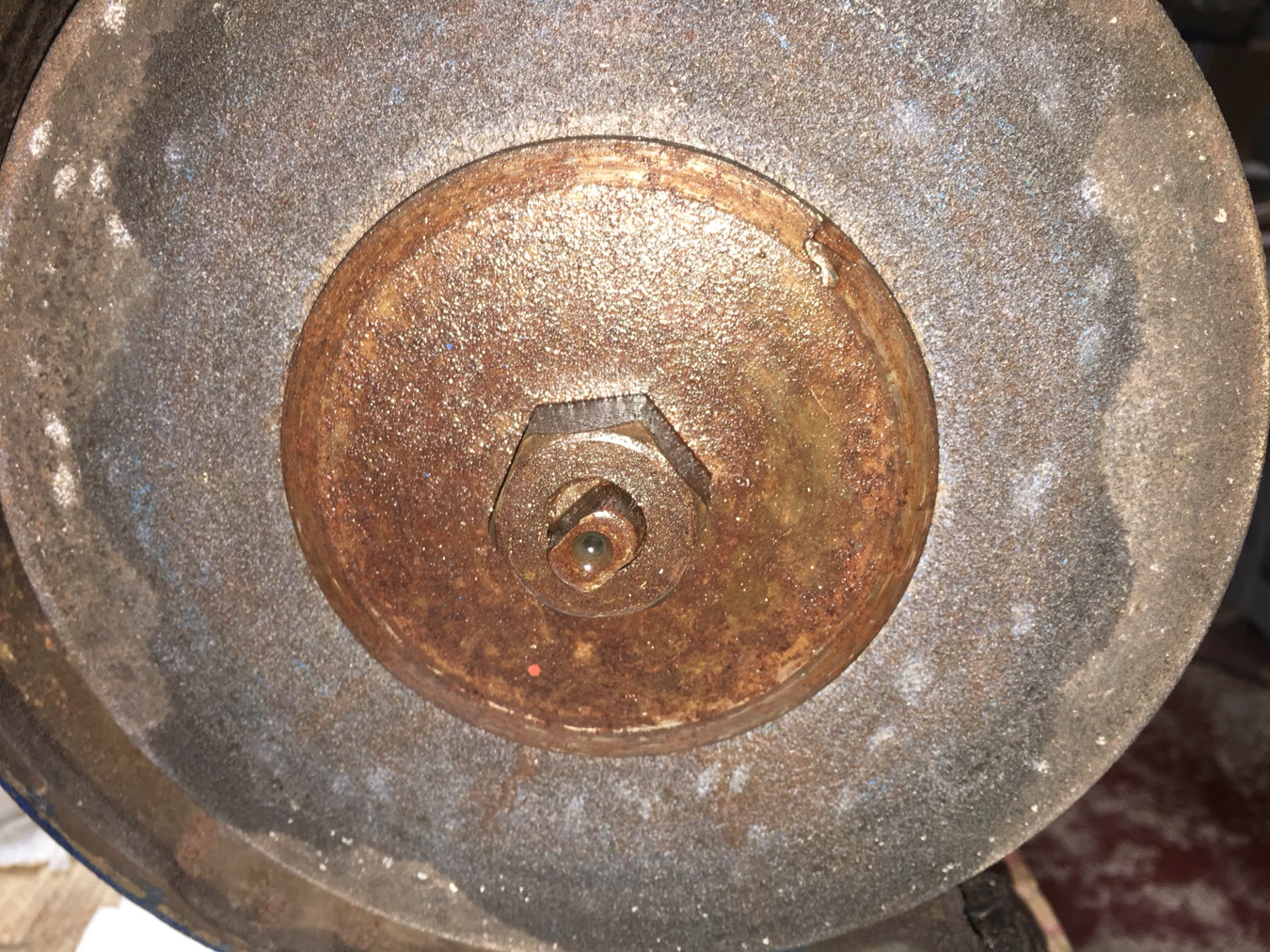
I’ve left it soaking with wd40 in the hopes it will help, but does anyone have any tips on how best to get this nut loose without damaging the spindle (and ideally without damaging the nut)?? I assume I’m turning it the correct direction (anti clockwise, as the right wheel was clockwise).
Secondly, I have no clue at all when it comes to old imperial thread sizes. This is the exact size of the thread...


What should I be searching for as the thread size if I’m looking for a suitably sized tapered mandrel adaptor for buffing wheels/polishing mops?? I’d be surprised if I do manage to find one to fit, but I live in hope!!
Any help or tips would be greatly appreciated