One or two of you may remember that for a year or two I have been dithering over organising a new workshop.
Plagued by issues over where to put it, whether to self-build or buy an instant solution, or even whether to move house for a place with some outbuildings, etc etc.
Well, I have finally cracked and ordered a new workshop, home office type building.
I just don't have the time to build the workshop myself and had to stop kidding myself otherwise, and in the cold analysis there was only ever one place to put it in our terraced garden.
Moving house was not really an option as the stamp duty alone would have amounted to more than the cost of the new workshop, base and one or two new machines I have in mind.
Here is a sneak preview of the building which will be arriving at the end of March, 20 x 16 (inc. the veranda, where I plan to put my hammock).
I now have to organise a base for the building which is at the top of the garden. My mate Dick, who runs a groundworks and civils firm is going to do the work on the base and some other work on a retained wall behind the new workshop.
I asked him to prepare for a concrete base in accordance with Mike's excellent specification. This however, will be very expensive as the concrete will have to be pumped up to the site. An alternative option he suggested is a base constructed from heavy concrete slabs, which is much easier and a cheaper option.
I am not sure if this is a good idea or not, and would value the forums opinion?
I don't want to "spoil the ship for a h'aporth of tar" as they say. Will this type of base be strong and stable enough? What method of construction should I request, specification?
Whilst searching for information I stumbled on this site;
http://www.ecobase.biz/index.html
Seems a bit wacky to me - but could this be another solution?
Look forward to receiving comments, guidance before I decide on the base.
Cheers, Tony.
Plagued by issues over where to put it, whether to self-build or buy an instant solution, or even whether to move house for a place with some outbuildings, etc etc.
Well, I have finally cracked and ordered a new workshop, home office type building.
I just don't have the time to build the workshop myself and had to stop kidding myself otherwise, and in the cold analysis there was only ever one place to put it in our terraced garden.
Moving house was not really an option as the stamp duty alone would have amounted to more than the cost of the new workshop, base and one or two new machines I have in mind.
Here is a sneak preview of the building which will be arriving at the end of March, 20 x 16 (inc. the veranda, where I plan to put my hammock).
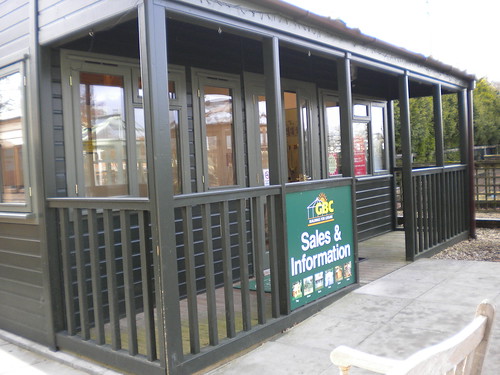
I now have to organise a base for the building which is at the top of the garden. My mate Dick, who runs a groundworks and civils firm is going to do the work on the base and some other work on a retained wall behind the new workshop.
I asked him to prepare for a concrete base in accordance with Mike's excellent specification. This however, will be very expensive as the concrete will have to be pumped up to the site. An alternative option he suggested is a base constructed from heavy concrete slabs, which is much easier and a cheaper option.
I am not sure if this is a good idea or not, and would value the forums opinion?
I don't want to "spoil the ship for a h'aporth of tar" as they say. Will this type of base be strong and stable enough? What method of construction should I request, specification?
Whilst searching for information I stumbled on this site;
http://www.ecobase.biz/index.html
Seems a bit wacky to me - but could this be another solution?
Look forward to receiving comments, guidance before I decide on the base.
Cheers, Tony.