swagman
Established Member
In the early stages of building a traditional Moving Fillister Plane. The depth stop assembly, single iron, and ancillaries were purchased from the U.K close to 5yrs ago, so its been a project that's been well overdue in getting started. Some existing slop within the mechanical movement of the depth stop had to be addressed before it was later installed. The build itself will take some time to complete as this is my 1st time attempt at this type of wooden plane design. Each stage needs to be followed up by a detailed account of the measurements taken for future reference.
A rebate needed to be formed to allow the later gluing in of a partial sole of higher janka timber. The main stock species is Tasmanian Tiger Myrtle.
A dovetailed key-way was formed to house the adjuster side wall plate.
The thread plates to secure the moving fence were keyed in before being epoxied into position.
A partial sole of higher janka Aust. Jarrah was glued in before being dressed back to final dimension.
A rebate needed to be formed to allow the later gluing in of a partial sole of higher janka timber. The main stock species is Tasmanian Tiger Myrtle.
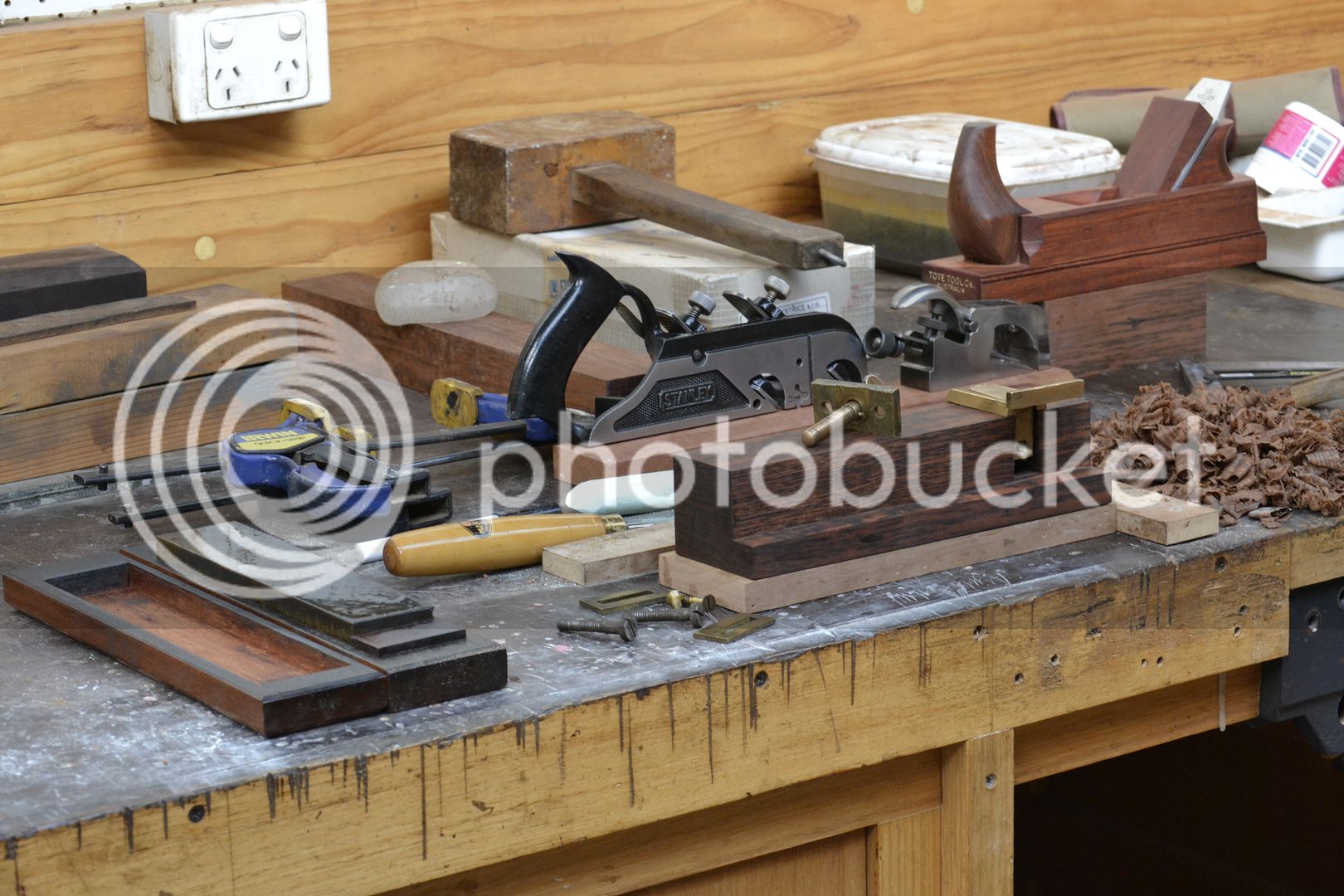
A dovetailed key-way was formed to house the adjuster side wall plate.
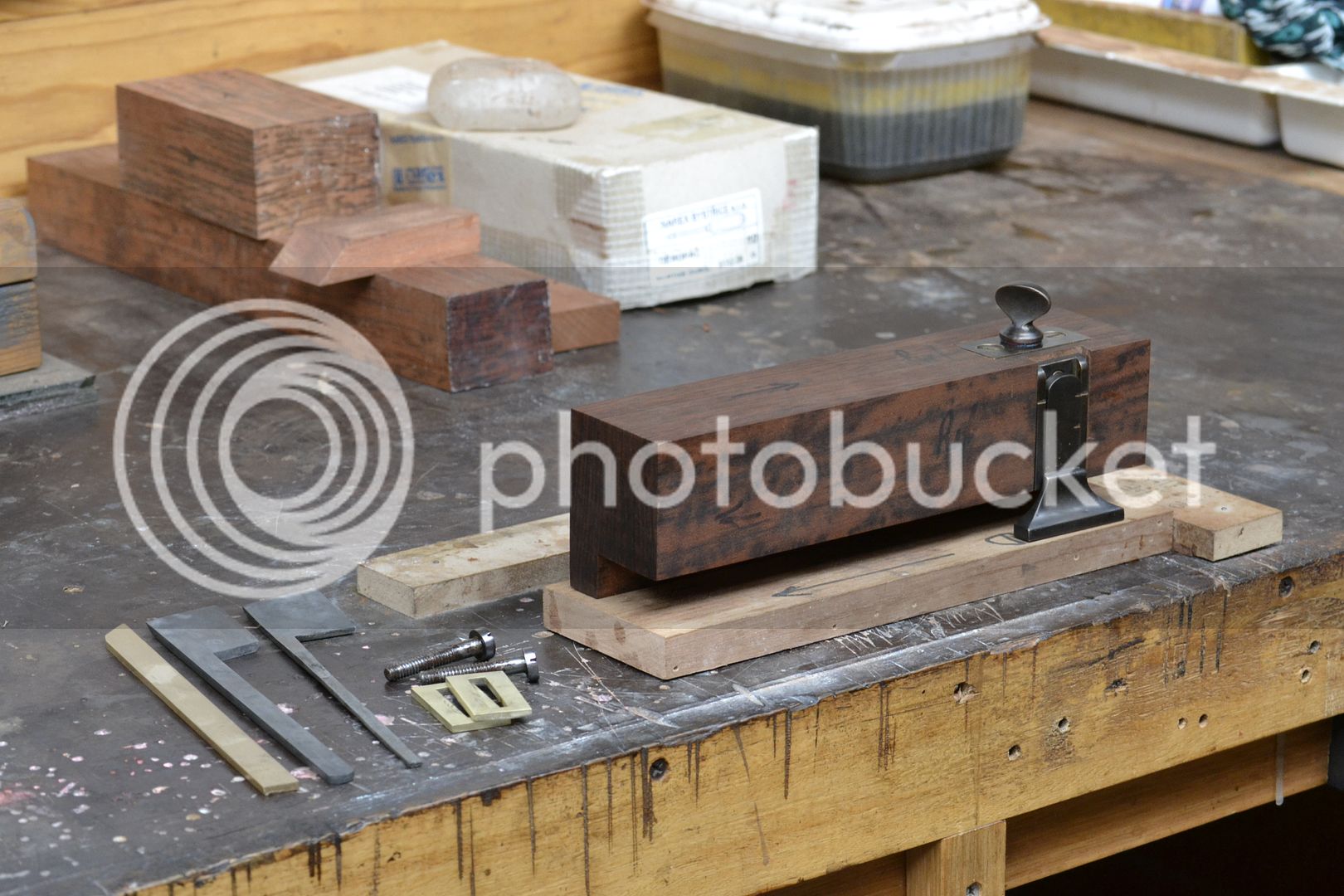
The thread plates to secure the moving fence were keyed in before being epoxied into position.
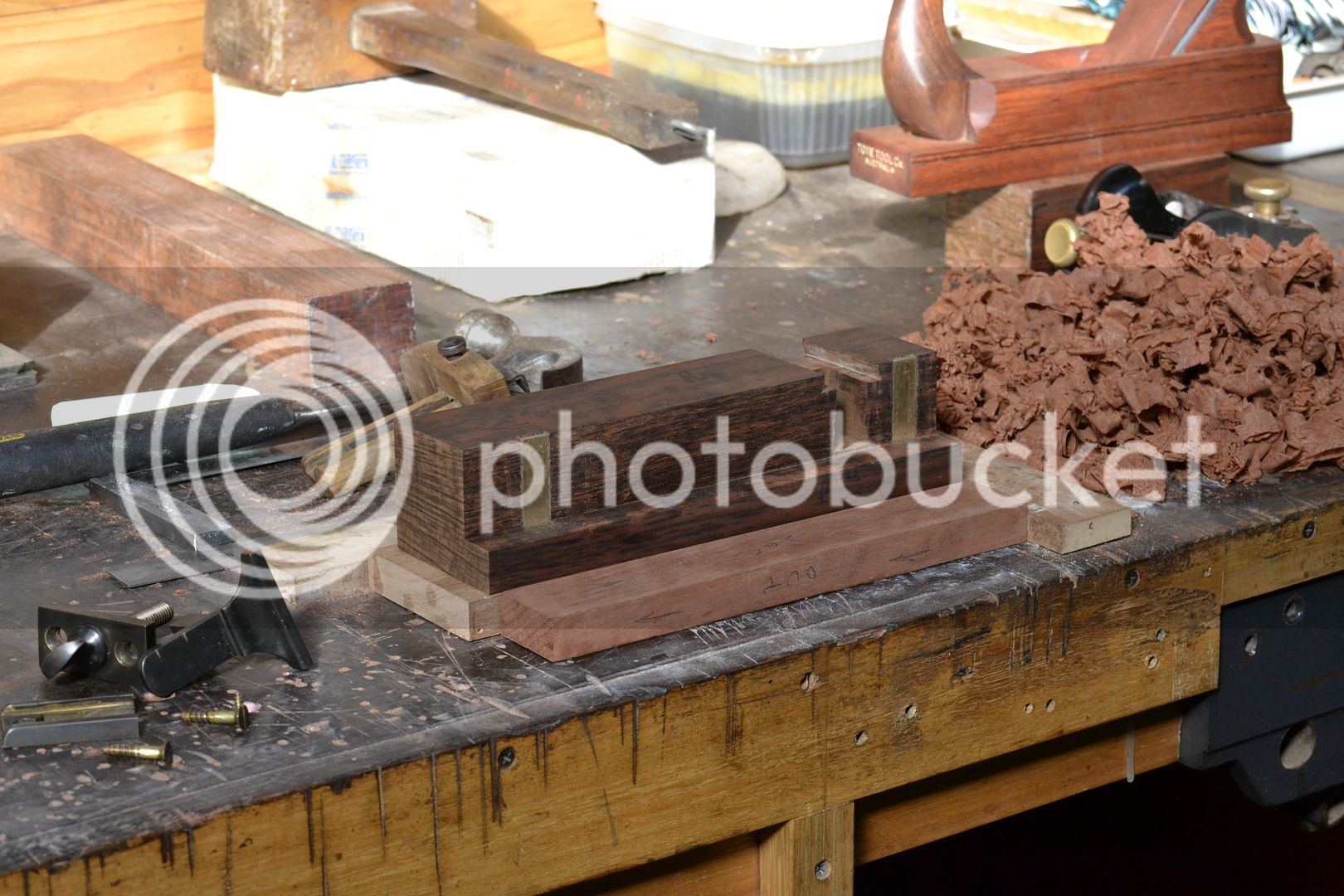
A partial sole of higher janka Aust. Jarrah was glued in before being dressed back to final dimension.
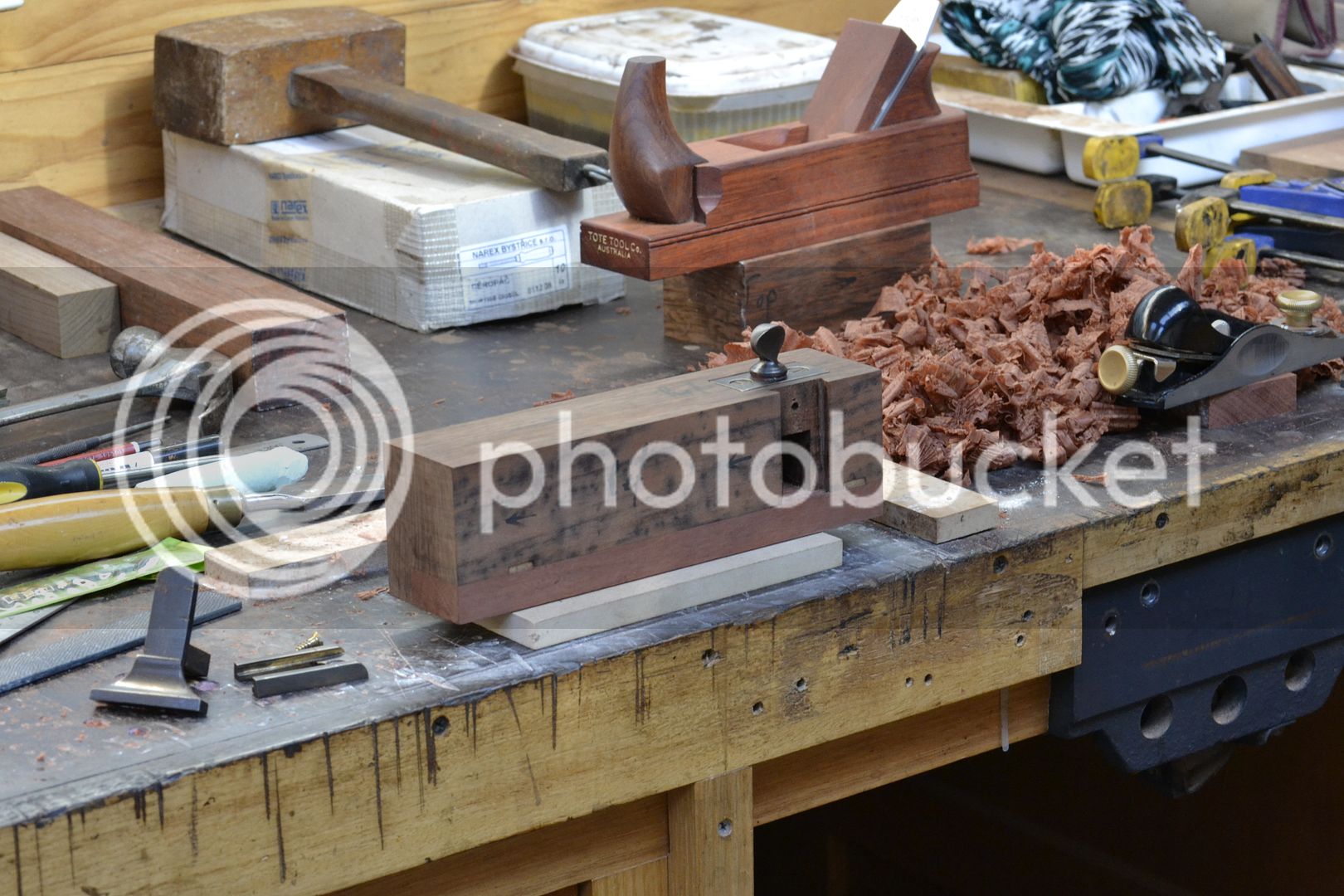
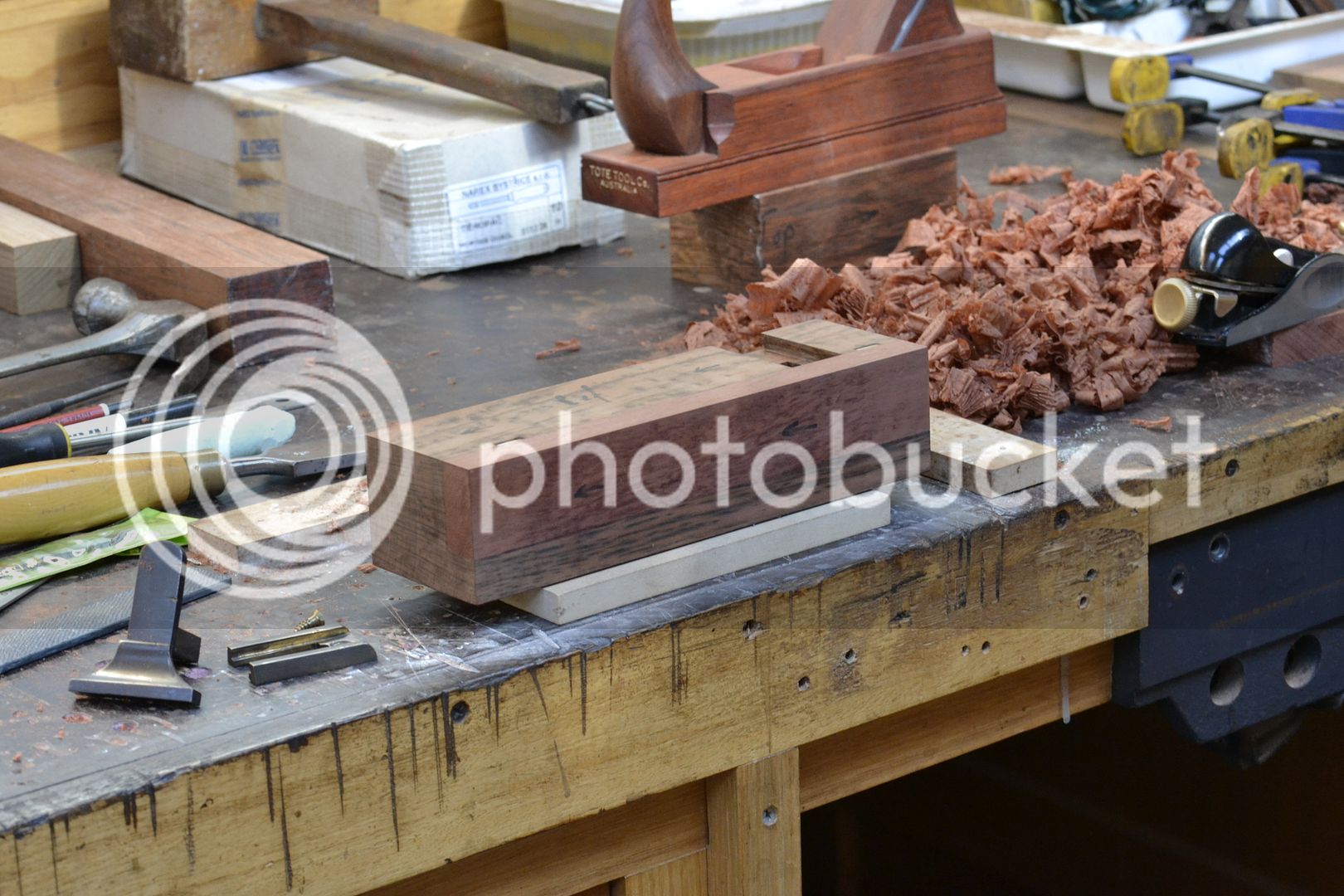