transatlantic
Boom!
Has anyone made something like this?
I would like to make one so I can cut grooves to accept 6mm ply, such as in the botton of a box.
Not sure what to use for the blade though? I was thinking of just picking up a 6mm chisel and removing the handle.
Maybe something like this :
https://www.amazon.co.uk/Bahco-414-6-B- ... B0001IX80A
or (as the wood will be easier to remove)
https://www.axminster.co.uk/axminster-r ... 6mm-103295
I did have a look at some o1 steel on ebay, but it doesn't come in the sizes I would need, so would have to cut it dow, harden it etc and it's not any cheaper really.
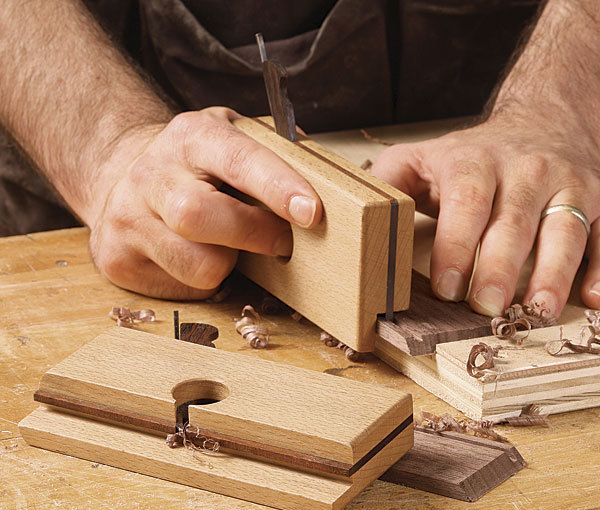
I would like to make one so I can cut grooves to accept 6mm ply, such as in the botton of a box.
Not sure what to use for the blade though? I was thinking of just picking up a 6mm chisel and removing the handle.
Maybe something like this :
https://www.amazon.co.uk/Bahco-414-6-B- ... B0001IX80A
or (as the wood will be easier to remove)
https://www.axminster.co.uk/axminster-r ... 6mm-103295
I did have a look at some o1 steel on ebay, but it doesn't come in the sizes I would need, so would have to cut it dow, harden it etc and it's not any cheaper really.