Slowly building a my first bench and I got round to wondering about the screw arrangement. I've seen on other similar threads the veritas and the Yorke ones at Axminsters. The Yorke ones seem to be the same as the Peter Schmid ones. (Czech Rep.)
Well, the thing is I'd really like to have a wheel, as seen on Escudo's lovely bench. roubo-bench-project-wip-t49024.html Seen the expensive kits and that aint happening! So I turned on the internet and duly fell down the rabbit hole.
Somewhere along the way this site was suggested for handles. https://www.berger-tools.co.uk/Standard ... andwheels/ For a 20cm odd cast wheel, with a handle £30 odd.
Searching about a bit more I found this site. http://www.abssac.co.uk/ Ooooh. Shiny. I gave 'em a quick bell to check they take tiny orders and all clear on that one.
Those brass fittings look nice!
They also seem to custom mill pretty much whatever you need. So Possibly cut a internal thread for a suitable fixing/bolt for the wheel to the thread.
Then I started getting a bit daft. I started thinking. What about the guide? Could you replace it? Would tolerances of having 2 steel rods remove racking?
http://www.abssac.co.uk/p/Splined+Shafts/83/
(They also do a bearing mounted guide on square steel.)
If you have big thick legs and used the sockets shown each side and on the leg vice, might that be enough to do away with the traditional method? Would you still have to clamp that splined bar?
Love to know your opinions on this. Price wise I guess its not the cheapest option but if it worked, we could sell it to the Americans and this time next year, we'll all be Millionaires.... :roll:
Cheers
Chris
Well, the thing is I'd really like to have a wheel, as seen on Escudo's lovely bench. roubo-bench-project-wip-t49024.html Seen the expensive kits and that aint happening! So I turned on the internet and duly fell down the rabbit hole.
Somewhere along the way this site was suggested for handles. https://www.berger-tools.co.uk/Standard ... andwheels/ For a 20cm odd cast wheel, with a handle £30 odd.
Searching about a bit more I found this site. http://www.abssac.co.uk/ Ooooh. Shiny. I gave 'em a quick bell to check they take tiny orders and all clear on that one.
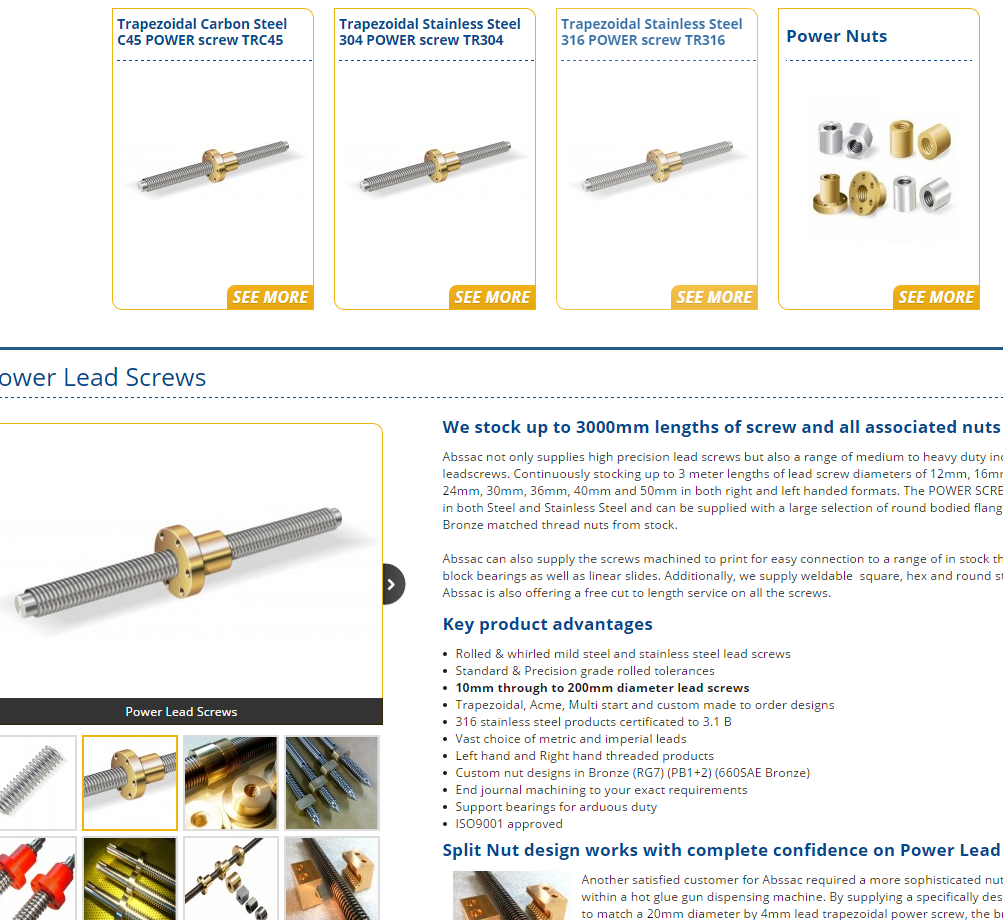
Those brass fittings look nice!
They also seem to custom mill pretty much whatever you need. So Possibly cut a internal thread for a suitable fixing/bolt for the wheel to the thread.
Then I started getting a bit daft. I started thinking. What about the guide? Could you replace it? Would tolerances of having 2 steel rods remove racking?
http://www.abssac.co.uk/p/Splined+Shafts/83/
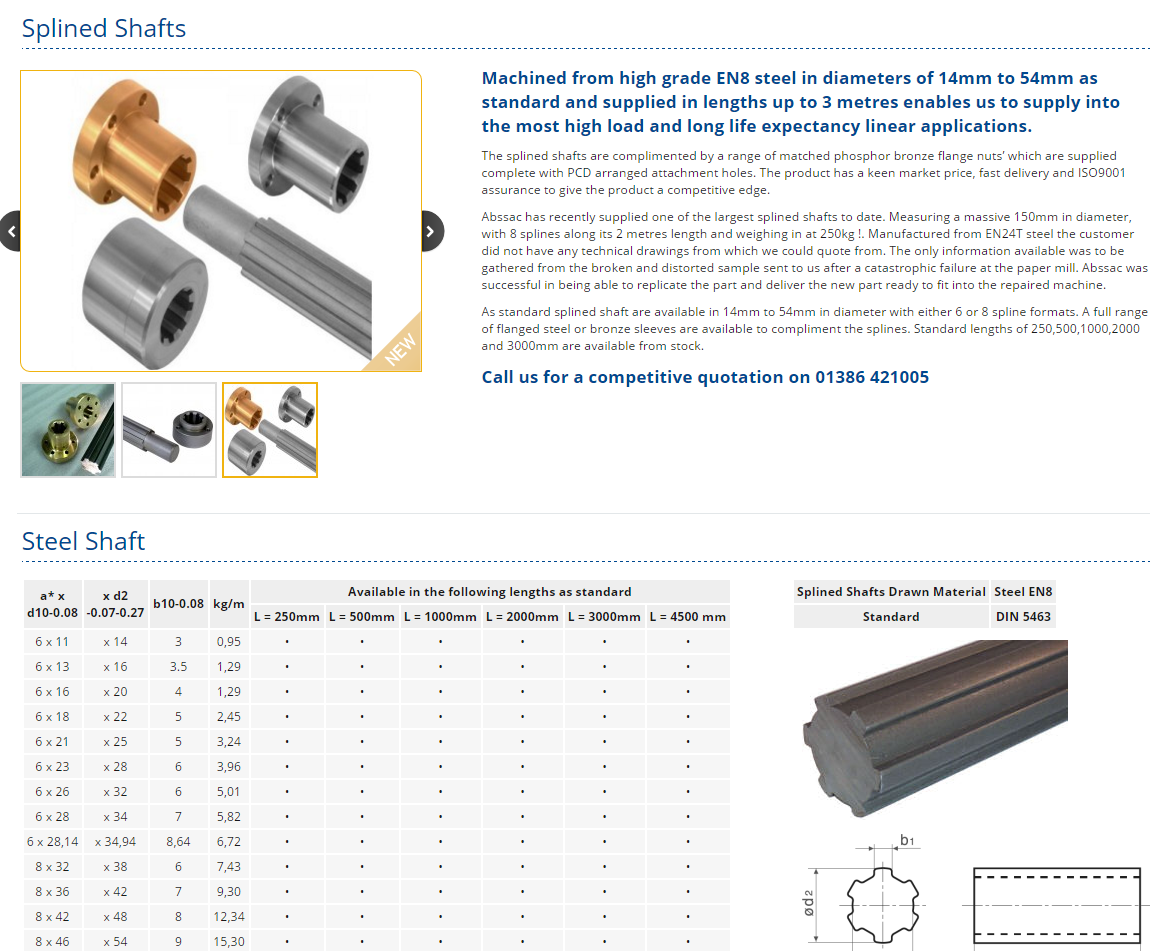
(They also do a bearing mounted guide on square steel.)
If you have big thick legs and used the sockets shown each side and on the leg vice, might that be enough to do away with the traditional method? Would you still have to clamp that splined bar?
Love to know your opinions on this. Price wise I guess its not the cheapest option but if it worked, we could sell it to the Americans and this time next year, we'll all be Millionaires.... :roll:
Cheers
Chris