So back in Nov 2009 issue 159 of F&C Mr Ley kindly showed us how to weave an oak panel - that looks nice I thought I'll do some of that sometime....
The usual Ikea-alike woven straw laundry basket has given up the ghost and the panels on the cover of the mag look like they would give a good air flow etc etc so off we go
lets see if I can remember how to post pictures
Recycled oak stock for the frame
saw it up and put it through the planer thicknesser - you will notice the fence upgrade I have added here for the woodstar PT85 as the one it comes with is only slightly less rigid than smoke. simply tapped into the deck with two M6 bolts and bolt on a square bit of wood - much much better than the original
a pile of milled stock for the uprights - not very interesting but always remember to do some extras for setting up and practice runs etc - I didn't have enough oak so used softwood - this is so important don't forget!!
so for some detail on the tenons for the cross rails - mortices done bya router cheeks of tenon cut by table saw sled (backwards and forwards and backwards and forwards and so on
we then saw down for the other bits by hand
scribe a line between cheeks - notice the reclaimed oak has some quite deep checks in it
notch for saw using chisel (read this in FWW i think)
and saw it
round off to fit routered mortice
and using rescued chisel (with new handle made by me on lathe first one i've done very pleased any excuse to show it off)
undercut the the other bit (saw this on the wood whisperer but obviously didn't pay enough attention to learn what all the bits of a tenon are called)
finally angle the edge where it meets the other tenon inside the joint using my matt black stealth plane (sorry Jimi I know it's not authentic but there's a squillion of these planes around and it was covered in rust and two quid at the boot sale - I wouldn't do it to an historically sensitive tool!)
and it fits - teaching you lot to suck eggs with all this detail I know but it might help someone so it's up
so what else needs to be done to the rails?
well we need a curve jigsawed
and routered to a template
and groove for the woven bit to go in - used my dads 050C that he's just given me as my folks have 'downsized' - funny looking thing but seems to work ok - wondering if I should make a wooden handle for it in a more traditional (and comfortable!!) shape
finally rout a matching groove in the uprights - couldn't use the plane for this as the mortices got in the way.
obviously this isn't me doing the actual machining - that would be dangerous - it's to show the 'stoat-o-matic' router lift being adjusted - I did a thread on it in jigs and tips ages ago - it works!
and dry fitted it looks like this (this is pre curves etc etc)
so onto the panels - the weavy bits (wefts and warps apparently) are 40mm wide so I can slice then off with my tablesaw which is handy. I think a bandsaw would be better but I don't have one. they come off at about 2.4mm thick and then get belt sanded at 80g and 100g and then hand sanded at 240 and they end up at about 1.8mm thick - which is quite thin. I clamped them to the bench to sand but the magazine article showed another way - each to his own.
then you clamp all the long ones to the bench (not shown) and slide in the sideways ones using a dowel to open up the long ones (i'll do some photo's when I do it properly - this was just a test) and when you un clamp it you get this
which really doesn't look like it wants to go in the frame but actually wasn't too hard - put the top and bottom in first and then the sides go in with the tenons (carefully) might need some glue with a long open time?? and it looks like this!!
Blimey - I was ever so impressed I went running into the house to show everyone how good it looked - and they'd all gone out shopping, typical!
so a couple of questions
I have many wefts and warps to sand which vibrate too much with an orbital and take too long by hand - any ideas? - I did plane one side before each strip was cut - but it still needs sanding.
and good glues that stay useable for over 30-40 minutes but don't cost too much?
will finish off and post more when I get it done - hope you like it so far
all comments as ever - good or bad - most welcome
cheers
The usual Ikea-alike woven straw laundry basket has given up the ghost and the panels on the cover of the mag look like they would give a good air flow etc etc so off we go
lets see if I can remember how to post pictures
Recycled oak stock for the frame
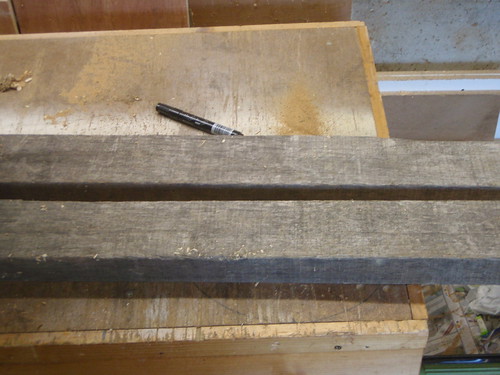
saw it up and put it through the planer thicknesser - you will notice the fence upgrade I have added here for the woodstar PT85 as the one it comes with is only slightly less rigid than smoke. simply tapped into the deck with two M6 bolts and bolt on a square bit of wood - much much better than the original
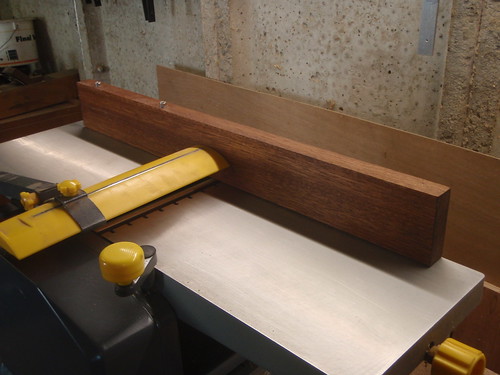
a pile of milled stock for the uprights - not very interesting but always remember to do some extras for setting up and practice runs etc - I didn't have enough oak so used softwood - this is so important don't forget!!
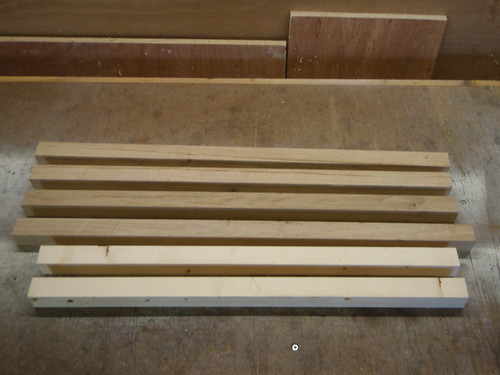
so for some detail on the tenons for the cross rails - mortices done bya router cheeks of tenon cut by table saw sled (backwards and forwards and backwards and forwards and so on
we then saw down for the other bits by hand
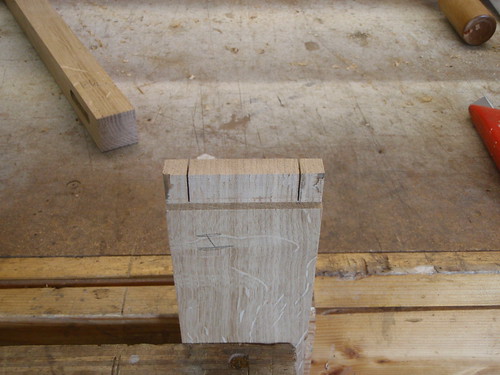
scribe a line between cheeks - notice the reclaimed oak has some quite deep checks in it
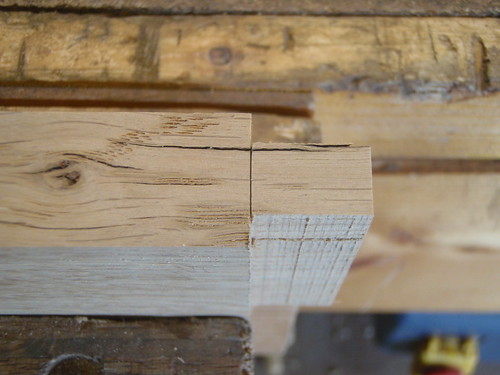
notch for saw using chisel (read this in FWW i think)
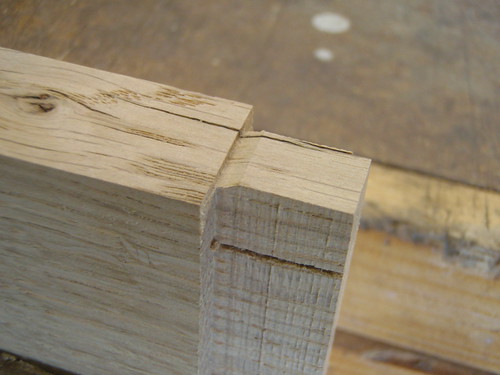
and saw it
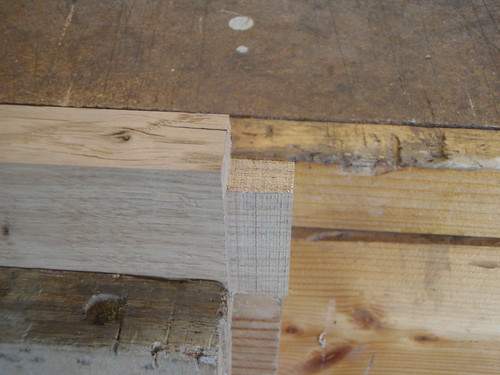
round off to fit routered mortice
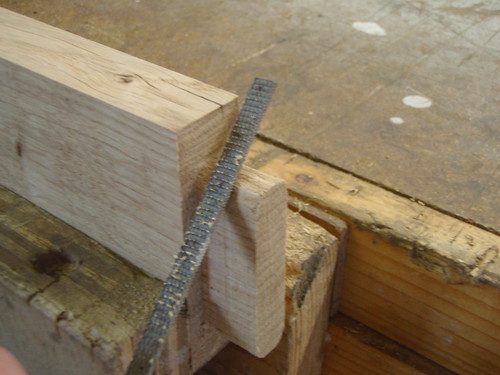
and using rescued chisel (with new handle made by me on lathe first one i've done very pleased any excuse to show it off)
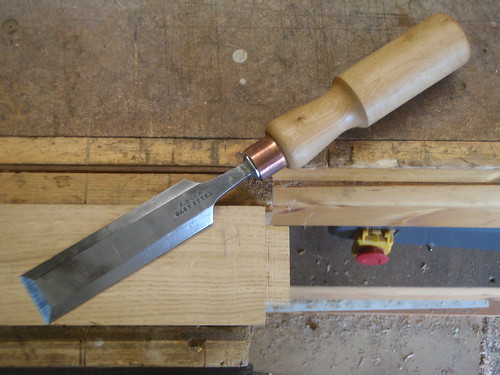
undercut the the other bit (saw this on the wood whisperer but obviously didn't pay enough attention to learn what all the bits of a tenon are called)
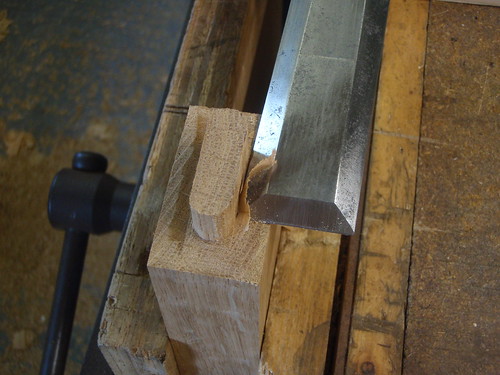
finally angle the edge where it meets the other tenon inside the joint using my matt black stealth plane (sorry Jimi I know it's not authentic but there's a squillion of these planes around and it was covered in rust and two quid at the boot sale - I wouldn't do it to an historically sensitive tool!)
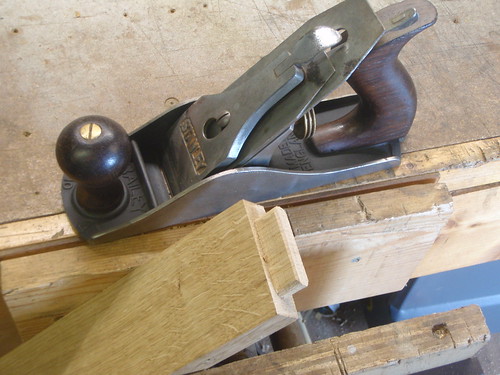
and it fits - teaching you lot to suck eggs with all this detail I know but it might help someone so it's up
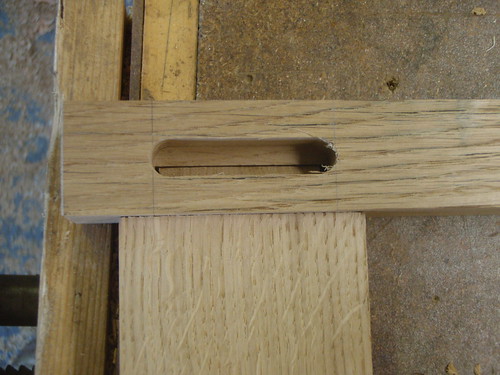
so what else needs to be done to the rails?
well we need a curve jigsawed
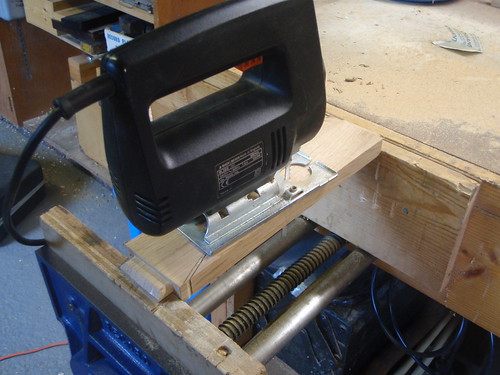
and routered to a template
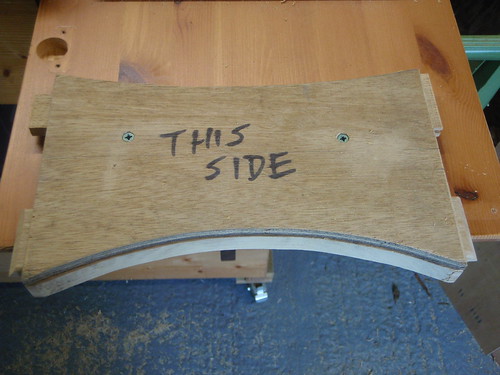
and groove for the woven bit to go in - used my dads 050C that he's just given me as my folks have 'downsized' - funny looking thing but seems to work ok - wondering if I should make a wooden handle for it in a more traditional (and comfortable!!) shape
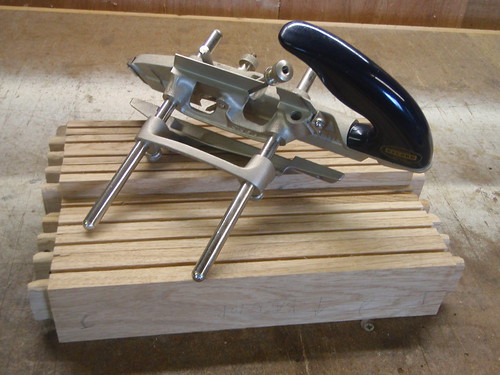
finally rout a matching groove in the uprights - couldn't use the plane for this as the mortices got in the way.
obviously this isn't me doing the actual machining - that would be dangerous - it's to show the 'stoat-o-matic' router lift being adjusted - I did a thread on it in jigs and tips ages ago - it works!
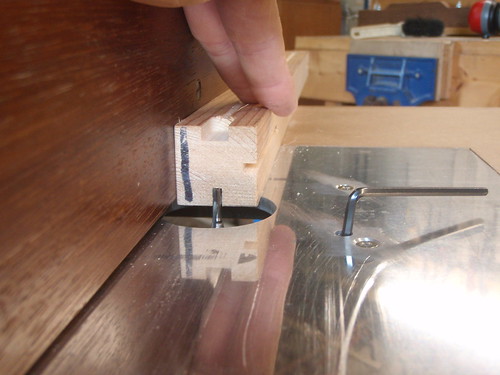
and dry fitted it looks like this (this is pre curves etc etc)
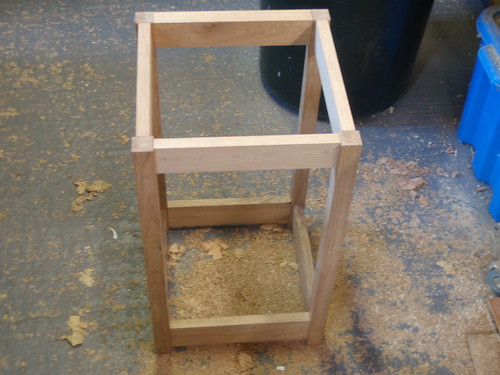
so onto the panels - the weavy bits (wefts and warps apparently) are 40mm wide so I can slice then off with my tablesaw which is handy. I think a bandsaw would be better but I don't have one. they come off at about 2.4mm thick and then get belt sanded at 80g and 100g and then hand sanded at 240 and they end up at about 1.8mm thick - which is quite thin. I clamped them to the bench to sand but the magazine article showed another way - each to his own.
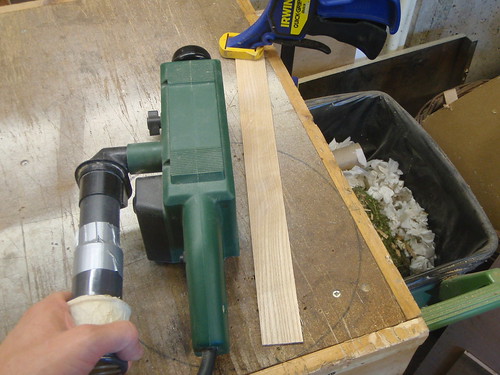
then you clamp all the long ones to the bench (not shown) and slide in the sideways ones using a dowel to open up the long ones (i'll do some photo's when I do it properly - this was just a test) and when you un clamp it you get this
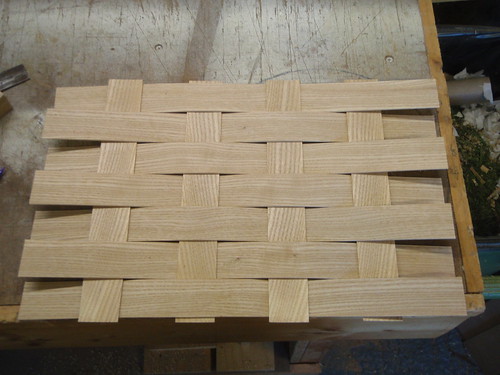
which really doesn't look like it wants to go in the frame but actually wasn't too hard - put the top and bottom in first and then the sides go in with the tenons (carefully) might need some glue with a long open time?? and it looks like this!!
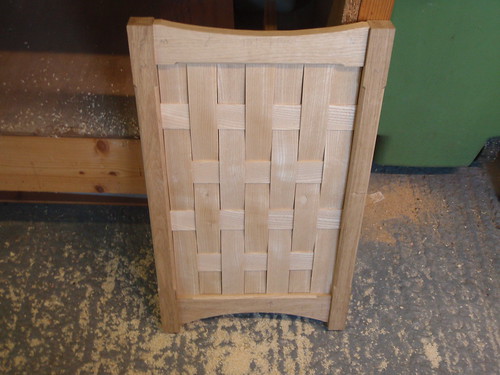
Blimey - I was ever so impressed I went running into the house to show everyone how good it looked - and they'd all gone out shopping, typical!
so a couple of questions
I have many wefts and warps to sand which vibrate too much with an orbital and take too long by hand - any ideas? - I did plane one side before each strip was cut - but it still needs sanding.
and good glues that stay useable for over 30-40 minutes but don't cost too much?
will finish off and post more when I get it done - hope you like it so far
all comments as ever - good or bad - most welcome
cheers