Keith Smith
Established Member
This project started when I was asked if I could repair a garden chair that had particular sentimental value, having been bought in Ecuador 40 years earlier. I said I could repair it and if it was too bad I’d make a copy, no problems.
When the customer brought it down it was way beyond repair but it had turned legs and spindles and I don’t turn!!
Next day Axminster had delivered me a nice new CCBL lathe.
After having a bit of a practise with softwood I started turning the oak spindles; I then discovered it’s a lot harder to turn oak that it is to turn softwood and it took me four hours to produce a spindle I was happy with. After that I sped up and by the time I was making the sixteenth I could produce one in twenty minutes.
I’m making two chairs by the way.
I should have cut the mortises in the legs before turning them but I expected to have a load of problems turning them, but in the end didn’t ruin any.
After I had finished turning I knocked the chair into its individual pieces so I could take measurements and see how it was made.
I was mostly dowelled but i was going to mortise and tenon all the joints, it had obviously been hand made as the chair was not symmetrical and I had to choose the best example of each piece and copy from that.
End of part one
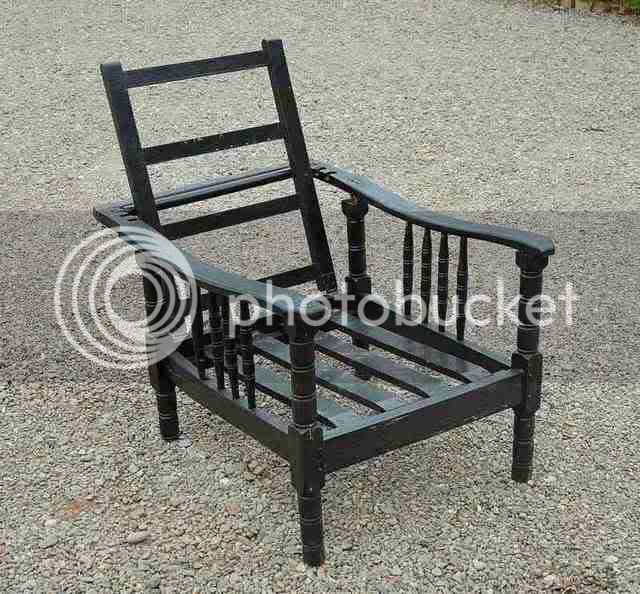
When the customer brought it down it was way beyond repair but it had turned legs and spindles and I don’t turn!!
Next day Axminster had delivered me a nice new CCBL lathe.
After having a bit of a practise with softwood I started turning the oak spindles; I then discovered it’s a lot harder to turn oak that it is to turn softwood and it took me four hours to produce a spindle I was happy with. After that I sped up and by the time I was making the sixteenth I could produce one in twenty minutes.
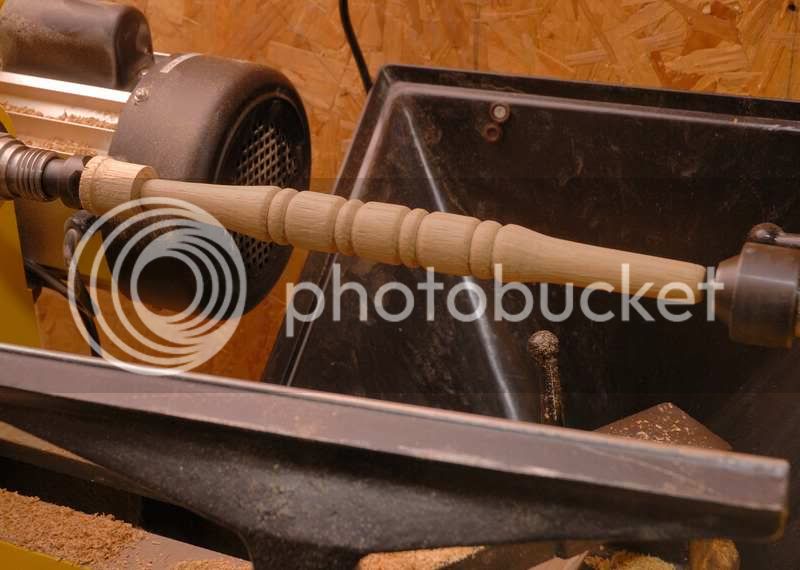
I’m making two chairs by the way.
I should have cut the mortises in the legs before turning them but I expected to have a load of problems turning them, but in the end didn’t ruin any.
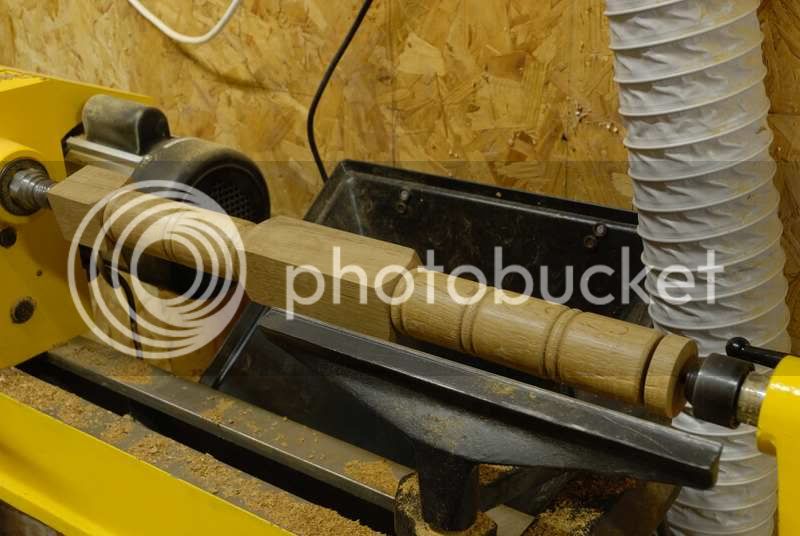
After I had finished turning I knocked the chair into its individual pieces so I could take measurements and see how it was made.
I was mostly dowelled but i was going to mortise and tenon all the joints, it had obviously been hand made as the chair was not symmetrical and I had to choose the best example of each piece and copy from that.
End of part one