At last the extraction has been "revamped" from the method posted earlier in this thread
I got a twin motor Camvac from Yandles (very helpful bunch of blokes in there, my first dealings with them and certainly not my last)
After talking through my requirements with the Yandles guys I went for a 2.5" rather than a 4" as its only servicing my TS, SCMS and router table (when its made)
I also got the blast gates and a fistful of adaptors at the same time. I thought that the Camvac pipe and fittings were a wee bit on the pricey side so opted to plumb everything in using plastic rain water pipe, reducing where neccesary to fit the machinery and blast gates. As it turned out the internal diameter of the rain pipe was a smidge bigger than the external diameter of the blast gate flanges, a decent squeeze of silicon sealant did the job admirably.
In order to keep suction to a maximum I put the blast gates as close to the extractor as possible, in my mind vacuum would be "wasted" if it were trying to suck along lengths of pipe that wern't in use (if that makes sense :roll
I also needed a way of connecting the 3 gates to the inlet hose - voila:
system works really well with massive suction. Apparently suction is lost on 90 degree bends and tees so I made my own elongated 90's by cutting the pipe at 22.5 on the scms and joining with insulation tape (all the fittings are well wound with tape)
the pipe work is all under the bench in a void which really wasn't usable, however I can see it becoming the offcuts area and general dumping ground.
I wanted to have the TS guard serviced from above so branched off the main run with some 32mm waste pipe, took it up the wall, across a rafter and dropped it with some reinforced hose. I was worried that reducing down to 32mm would reduce the suction but it works perfectly.
The hose for the connection to the SCMS was courtesy of the electrical skip at the local council tip, the adapter on the bench top is from the dust collection bag off of a bosch electric plane.
There is a third outlet for the router table but as thats not been built yet its redundant at the mo.
Vinny
I got a twin motor Camvac from Yandles (very helpful bunch of blokes in there, my first dealings with them and certainly not my last)
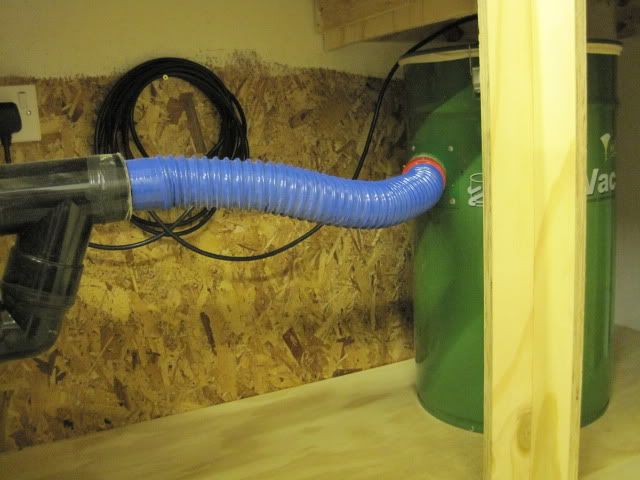
After talking through my requirements with the Yandles guys I went for a 2.5" rather than a 4" as its only servicing my TS, SCMS and router table (when its made)
I also got the blast gates and a fistful of adaptors at the same time. I thought that the Camvac pipe and fittings were a wee bit on the pricey side so opted to plumb everything in using plastic rain water pipe, reducing where neccesary to fit the machinery and blast gates. As it turned out the internal diameter of the rain pipe was a smidge bigger than the external diameter of the blast gate flanges, a decent squeeze of silicon sealant did the job admirably.
In order to keep suction to a maximum I put the blast gates as close to the extractor as possible, in my mind vacuum would be "wasted" if it were trying to suck along lengths of pipe that wern't in use (if that makes sense :roll
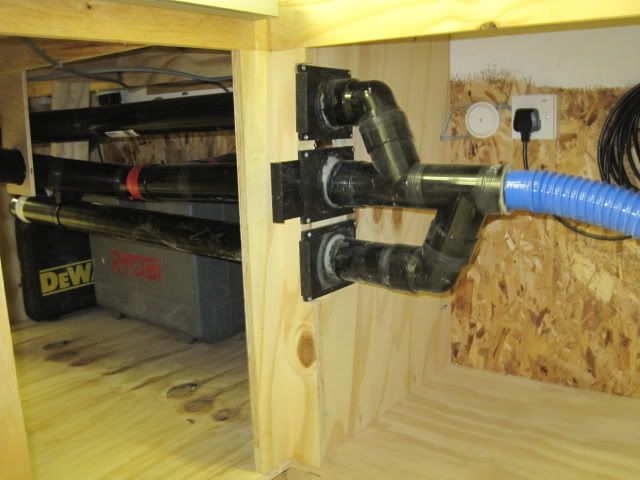
system works really well with massive suction. Apparently suction is lost on 90 degree bends and tees so I made my own elongated 90's by cutting the pipe at 22.5 on the scms and joining with insulation tape (all the fittings are well wound with tape)
the pipe work is all under the bench in a void which really wasn't usable, however I can see it becoming the offcuts area and general dumping ground.
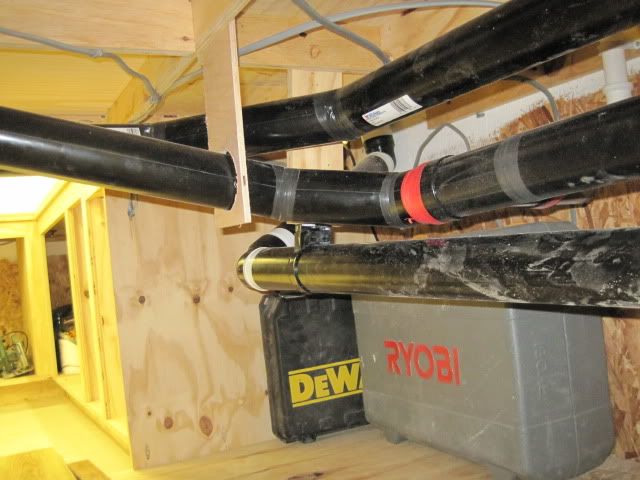
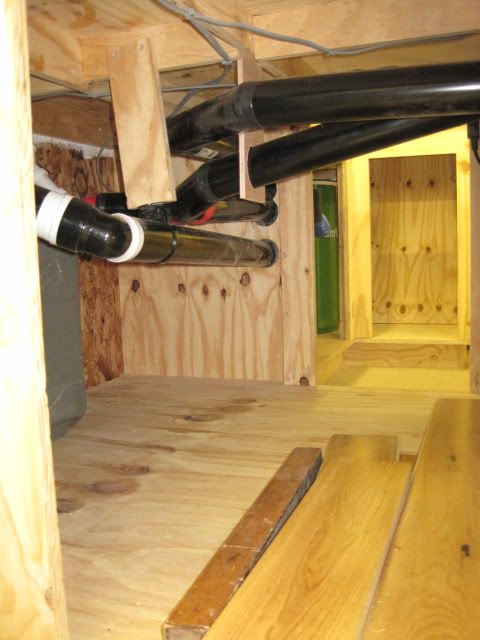
I wanted to have the TS guard serviced from above so branched off the main run with some 32mm waste pipe, took it up the wall, across a rafter and dropped it with some reinforced hose. I was worried that reducing down to 32mm would reduce the suction but it works perfectly.
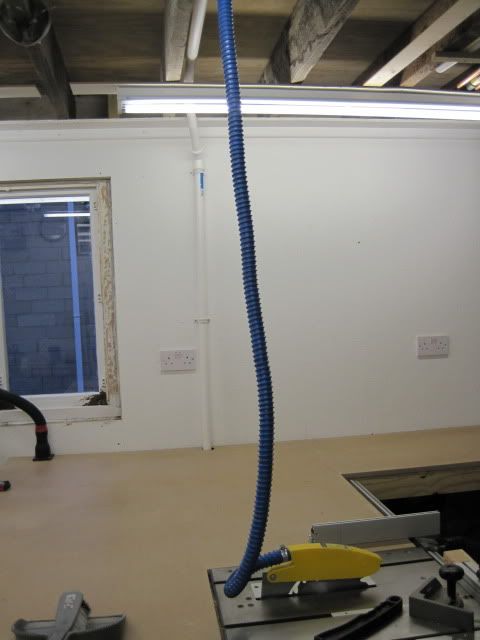
The hose for the connection to the SCMS was courtesy of the electrical skip at the local council tip, the adapter on the bench top is from the dust collection bag off of a bosch electric plane.
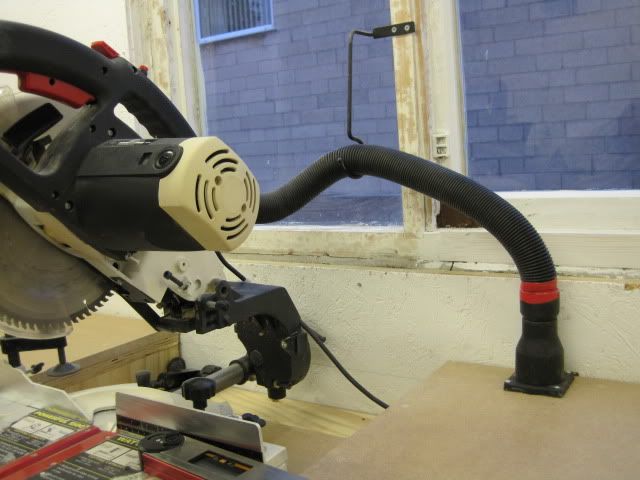
There is a third outlet for the router table but as thats not been built yet its redundant at the mo.
Vinny