woodbloke
Established Member
One of the things that came out of our very enjoyable Microbash yesterday (that Philly couldn't get to but is coming to the next one
) was the vexing question of 'Y' levers on Record and Stanley planes. There's no question that fitting a better blade, of whatever breed, makes a huge difference to the way the plane performs but, and here's the rub, they're generally much thicker than the standard offering and so the 'Y' lever barely engages on the CB. Here's a pic of Pauls' No4 which he's fitted with a 3.1mm iron and two-part chipbreaker. You can see that the top of the lever has been mangled where it's just engaging the CB:
The solution is quite straight forward and that's to silver solder a small lump of steel onto the top of the existing 'Y' lever, so here's a shot of the set up in the vice and you can see the little piece of silver solder:
Apply the heat from a gas torch and then.......DISASTER (but easily remedied Paul)......the Clifton 'Y' lever (which this is) is made from an alloy with a lower melting point than the Record 'Y' lever and the top, well....erm melted a bit. There is a quaint term that my dad used to use about describing softer mild steel but it's not for delicate ears or a mild disposition :lol: What I then did was to clean up the debris and soft-solder a piece of steel onto the top (using a large soldering iron and some 60/40 tin/lead solder) and the result is this:
This is the modified 'Y' lever shown against another one of Pauls' standard levers. When the new lever is put into the plane it no longer just catches but fully engages in the slot on the chipbreaker
,
..so a very useful and quite easy mod to do - Rob
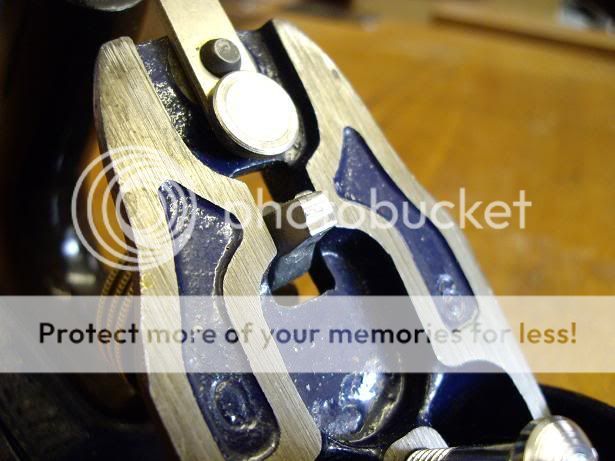
The solution is quite straight forward and that's to silver solder a small lump of steel onto the top of the existing 'Y' lever, so here's a shot of the set up in the vice and you can see the little piece of silver solder:
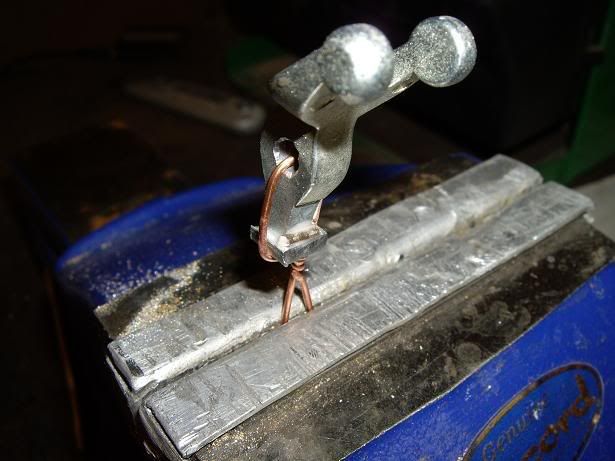
Apply the heat from a gas torch and then.......DISASTER (but easily remedied Paul)......the Clifton 'Y' lever (which this is) is made from an alloy with a lower melting point than the Record 'Y' lever and the top, well....erm melted a bit. There is a quaint term that my dad used to use about describing softer mild steel but it's not for delicate ears or a mild disposition :lol: What I then did was to clean up the debris and soft-solder a piece of steel onto the top (using a large soldering iron and some 60/40 tin/lead solder) and the result is this:
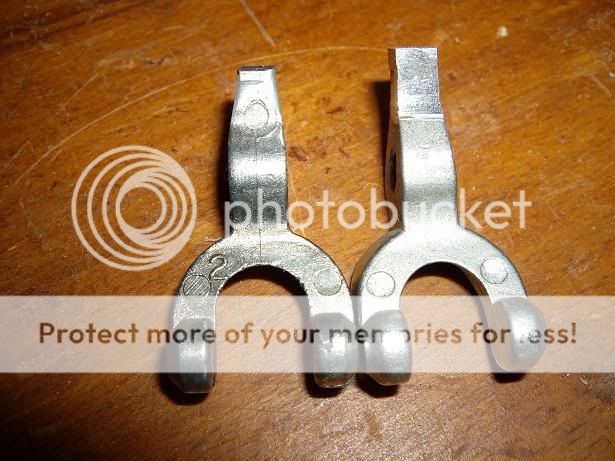
This is the modified 'Y' lever shown against another one of Pauls' standard levers. When the new lever is put into the plane it no longer just catches but fully engages in the slot on the chipbreaker
,
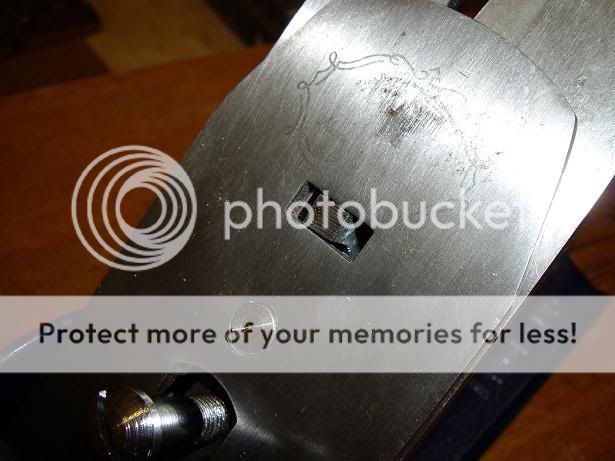
..so a very useful and quite easy mod to do - Rob