pren
Established Member
Ho there, citizens. Merry weekend to you all!
Some friends of mine are due a visit from Mr Stork soon, (the baby bringing type, not the margarine .... bringing one ...) and they asked me if I could come up with some fitted wardrobes/drawers for the nursery. They wanted somewhere to store most of their own clothes as well as the baby things.
Now, as kiddies tend to consume vast amounts of money, they really didn't have much at all in the way of a budget.
So.. after much designing and re-designing to reduce the amount of materials needed, I decided to make the drawer section as a separate 'base' unit, upon which to mount the framing for the clothes hanging/shelf section.
The whole lot will eventually be secured to the walls, with the hanging rail mounted directly to the walls. Because of this, I've decided to use 34x34mm par for the frame, which will mainly act as hinge points for the doors and half of the support for the shelves that are to run down the right hand side, from floor to cieling.
The 'base unit' has been made from 18mm chipboard which will be veneered with 4mm ply to make it less ... chipboardy ... as well as to cover the rough edging on the front.
So far:
End panels for base unit. Routed with 18x9mm housings and 9x9mm rebate for top piece.
Top and bottom panels being routed with 18mmx9mm housing and 9x9mm rebate on ends.
Dry fitting panels for drawer supports. Due to swelling at the ends of these panels, I had to plane about 1mm off in order to get them to fit :evil: It's almost as if the manufacturers of chipboard never had fine furniture making in mind! :roll: :lol:
Final dry assembly with 4mm ply placed on top. The first two bays will hold 3, 200 x 580 x 570mm drawers each (that's alot of baby socks!!) with the right hand bay being for two shelves.
MFC ripped to width for the drawer sides. This was salvaged from work as it was destined for the scrap heap.
That's all for now. Hopefully tomorrow will see most of the drawers made up and possibly some of the ply trim fixed to the front of the carcass. I also indend to fix some feet to the undersides of the two internal drawer support panels to prevent saggage.
TTFN for now.
Bryn.
Some friends of mine are due a visit from Mr Stork soon, (the baby bringing type, not the margarine .... bringing one ...) and they asked me if I could come up with some fitted wardrobes/drawers for the nursery. They wanted somewhere to store most of their own clothes as well as the baby things.
Now, as kiddies tend to consume vast amounts of money, they really didn't have much at all in the way of a budget.
So.. after much designing and re-designing to reduce the amount of materials needed, I decided to make the drawer section as a separate 'base' unit, upon which to mount the framing for the clothes hanging/shelf section.
The whole lot will eventually be secured to the walls, with the hanging rail mounted directly to the walls. Because of this, I've decided to use 34x34mm par for the frame, which will mainly act as hinge points for the doors and half of the support for the shelves that are to run down the right hand side, from floor to cieling.
The 'base unit' has been made from 18mm chipboard which will be veneered with 4mm ply to make it less ... chipboardy ... as well as to cover the rough edging on the front.
So far:
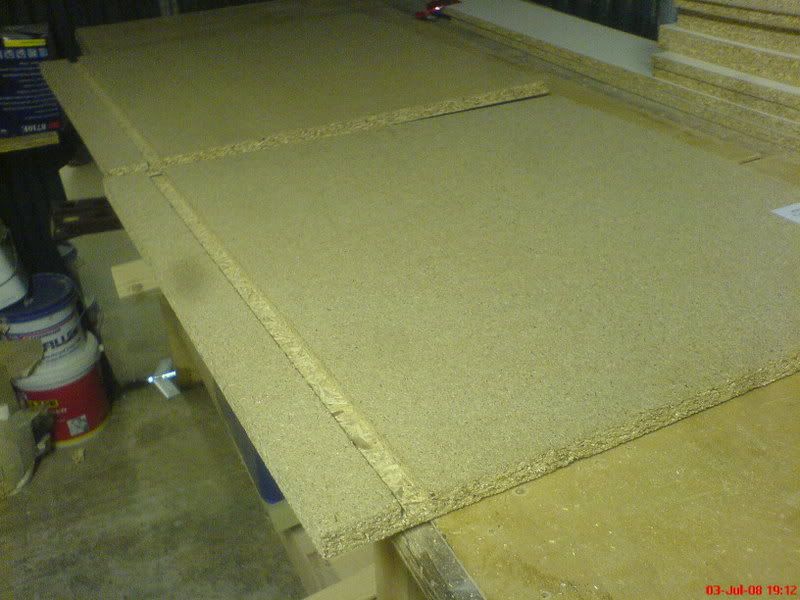
End panels for base unit. Routed with 18x9mm housings and 9x9mm rebate for top piece.
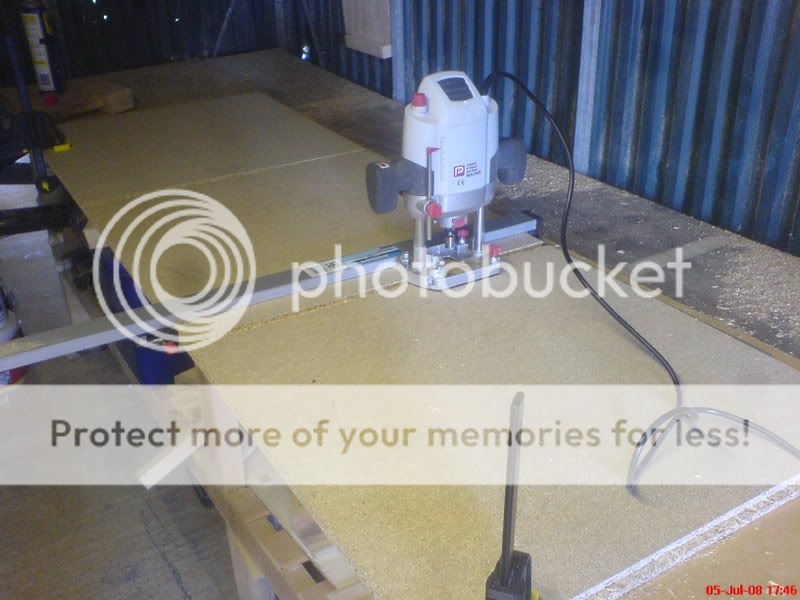
Top and bottom panels being routed with 18mmx9mm housing and 9x9mm rebate on ends.
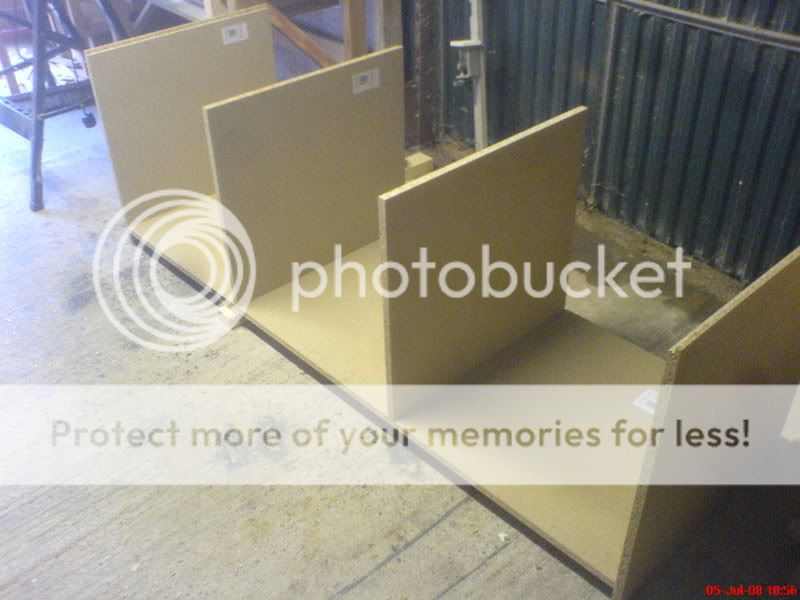
Dry fitting panels for drawer supports. Due to swelling at the ends of these panels, I had to plane about 1mm off in order to get them to fit :evil: It's almost as if the manufacturers of chipboard never had fine furniture making in mind! :roll: :lol:
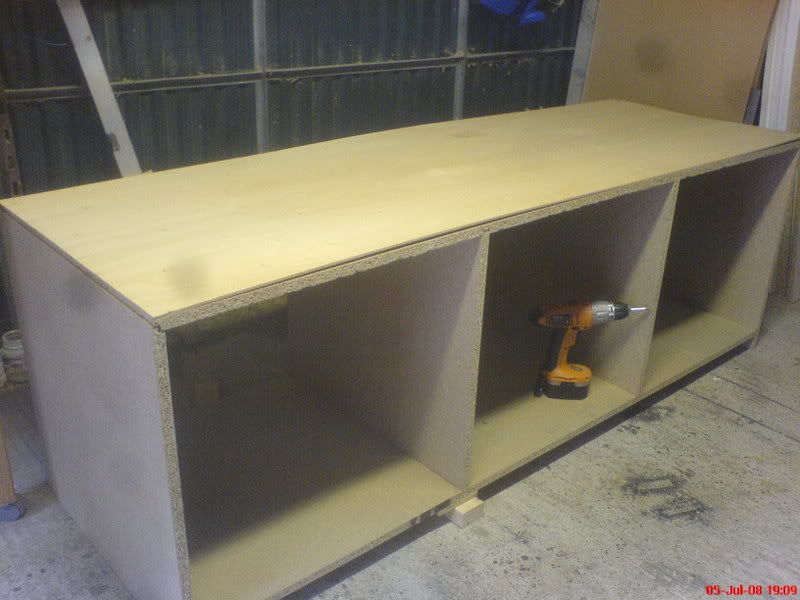
Final dry assembly with 4mm ply placed on top. The first two bays will hold 3, 200 x 580 x 570mm drawers each (that's alot of baby socks!!) with the right hand bay being for two shelves.
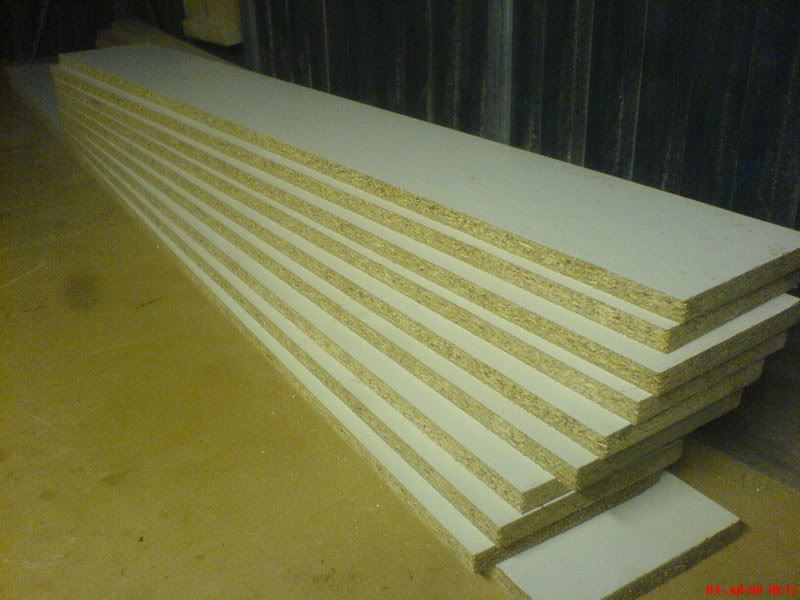
MFC ripped to width for the drawer sides. This was salvaged from work as it was destined for the scrap heap.
That's all for now. Hopefully tomorrow will see most of the drawers made up and possibly some of the ply trim fixed to the front of the carcass. I also indend to fix some feet to the undersides of the two internal drawer support panels to prevent saggage.
TTFN for now.
Bryn.