Inspired by Tenpins curved cupboard I thought I'd do one for my boat, this was the front of the existing cupboard which fits into a corner.
First job was to make a former, for this I used some left over bits of floorboard that I'd used in the workshop, this glued together made the ideal former.
I then resawed some oak on the bandsaw into thin strips 3/16" thick and place two together on the former.
I then repearted this with another two pieces, then the two double pieces were laminated over the former, the result being a curved section 3/4" thick.
Once cut to size I was amazed that they were both a perfect match, remember I've never done this before.
Next job was to cut the mortices in the curved sections, I wasn't to sure how this was going to turn out using the morticer, but in the end it went pretty well.
Today I'm going to put the uprights in that will form the small panels each side of the door, hope this goes as well as the bits so far.
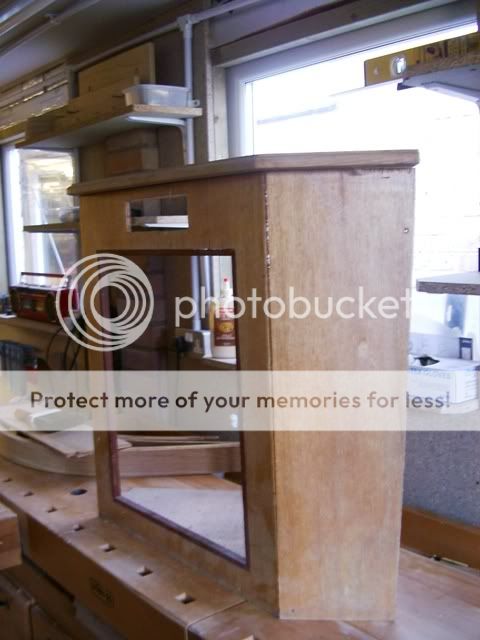
First job was to make a former, for this I used some left over bits of floorboard that I'd used in the workshop, this glued together made the ideal former.
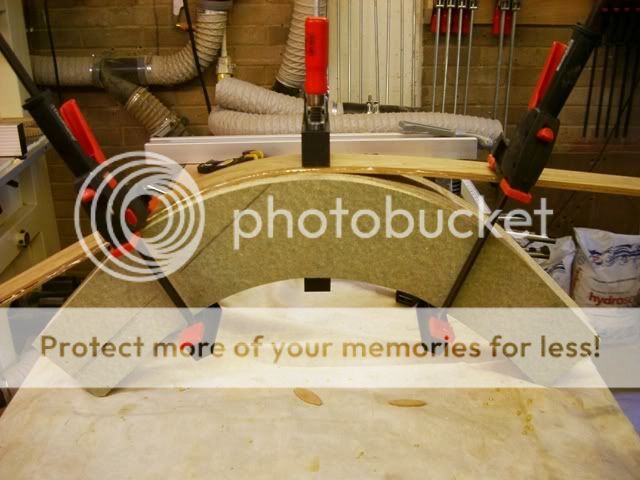
I then resawed some oak on the bandsaw into thin strips 3/16" thick and place two together on the former.
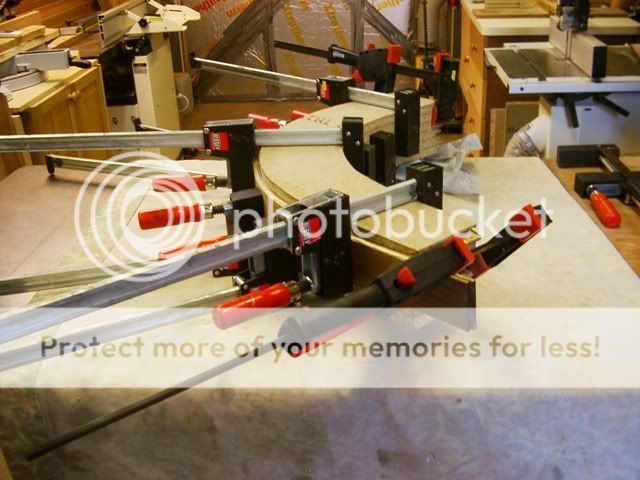
I then repearted this with another two pieces, then the two double pieces were laminated over the former, the result being a curved section 3/4" thick.
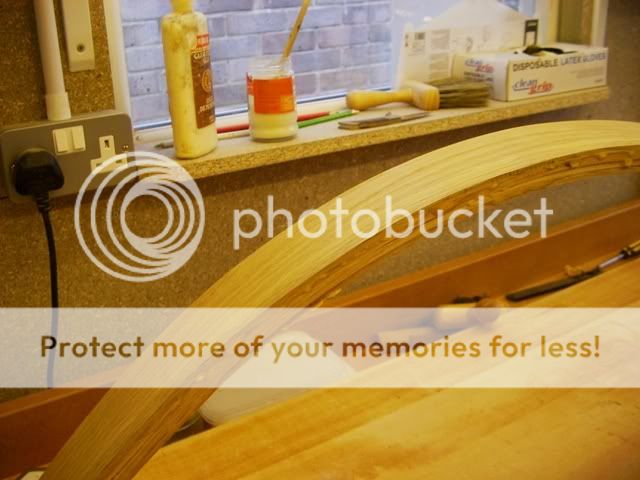
Once cut to size I was amazed that they were both a perfect match, remember I've never done this before.
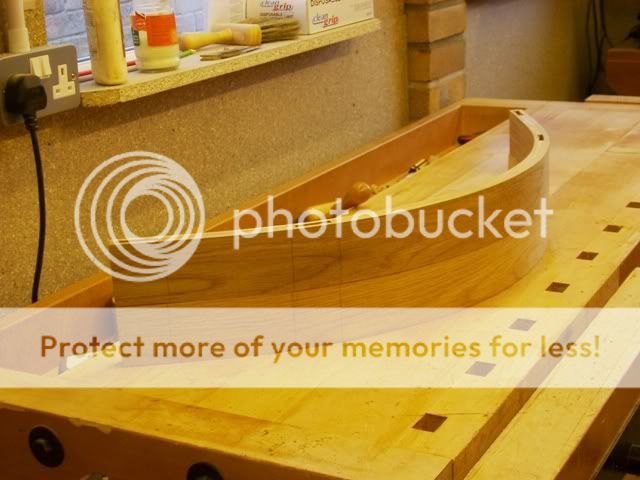
Next job was to cut the mortices in the curved sections, I wasn't to sure how this was going to turn out using the morticer, but in the end it went pretty well.
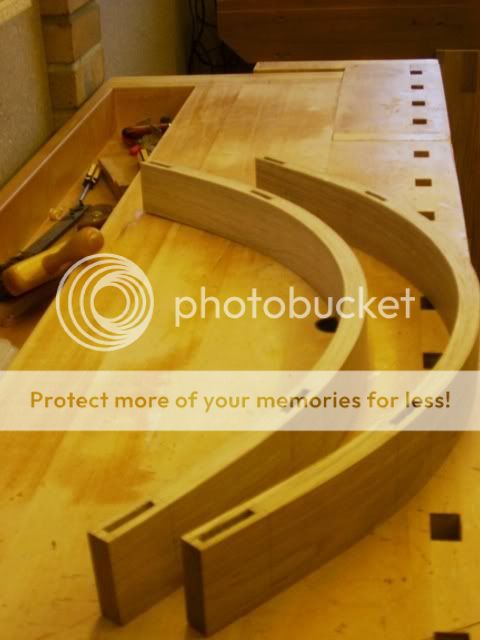
Today I'm going to put the uprights in that will form the small panels each side of the door, hope this goes as well as the bits so far.