This is an odd duck. These guitars were designed to be mass produced so there is one or two things in the process that is better done with power tools for aesthetics (that's not a requirement, but my eyes are trained for strat things and I will later make a guitar entirely with hand tools that has aesthetics almost impossible to do with power tools, but not on this one).
I start with a rosewood blank that's quartersawn for the neck. I would like to take the fingerboard from the same blanks, so hand resawing is necessary (i no longer have a bandsaw, but I wouldn't have trusted it for this). I have about a 16th of wiggle room, which is plenty). Quality of the grain orientation on guitars is critical - on a neck, doubly so, but there's not that much wood in a guitar, so the cost of quality wood vs. junk is perhaps about $150 different. It's worth it. Rosewood necks are not standard on fender guitars, but I have built a telecaster in standard scale of this type (the pickups are seymour duncan p-rails, an unusual type) and the result in terms of sound is fantastic.
It takes about 10 minutes to do this resaw relatively accurately with a typical carpenter's saw. One of the nice things about guitars is that the bulk work really isn't much, and it's often harder to do the nuance (neck profiling, etc) properly if you use power tools instead of hand tools. It's not a break even for production, but for individual guitars, it's probably close.
And the resulting offcut to be set aside to make a fingerboard later.
The body blank that I got for this guitar is khaya, quartered. It's fairly low density and the ribboning is strong. Planing results in no tearout with the cap iron, but grain direction does leave a tiny bit of difference in surface texture. I will leave this as is, but if I round the guitar over on the back, I may be forced to sand just to get uniform finish absorption (french polish). I will not sand out all of the plane nuance, though, just the very surface (mixing planing and sanding on a softer blank like this, even with un-tinted shellac will lead to different wood color in finish areas, looking like the wood was burnished in places and not others, etc).
Cutting the blank - relatives are important working with hand tools, but absolutes are not. I have a general center line to help with alignment, but since I'm not using a CNC machine or any such thing, I can use the center line to aid initial work and then set hardware relative to the neck later. I cut relatively far from the line not for accuracy (it's not that important), but because khaya can blow out on the back and I don't have that much thickness to spare on this blank. I'll remove the excess with a combination of spokeshave and the oscillating spindle/belt sander in the background.
I start with a rosewood blank that's quartersawn for the neck. I would like to take the fingerboard from the same blanks, so hand resawing is necessary (i no longer have a bandsaw, but I wouldn't have trusted it for this). I have about a 16th of wiggle room, which is plenty). Quality of the grain orientation on guitars is critical - on a neck, doubly so, but there's not that much wood in a guitar, so the cost of quality wood vs. junk is perhaps about $150 different. It's worth it. Rosewood necks are not standard on fender guitars, but I have built a telecaster in standard scale of this type (the pickups are seymour duncan p-rails, an unusual type) and the result in terms of sound is fantastic.
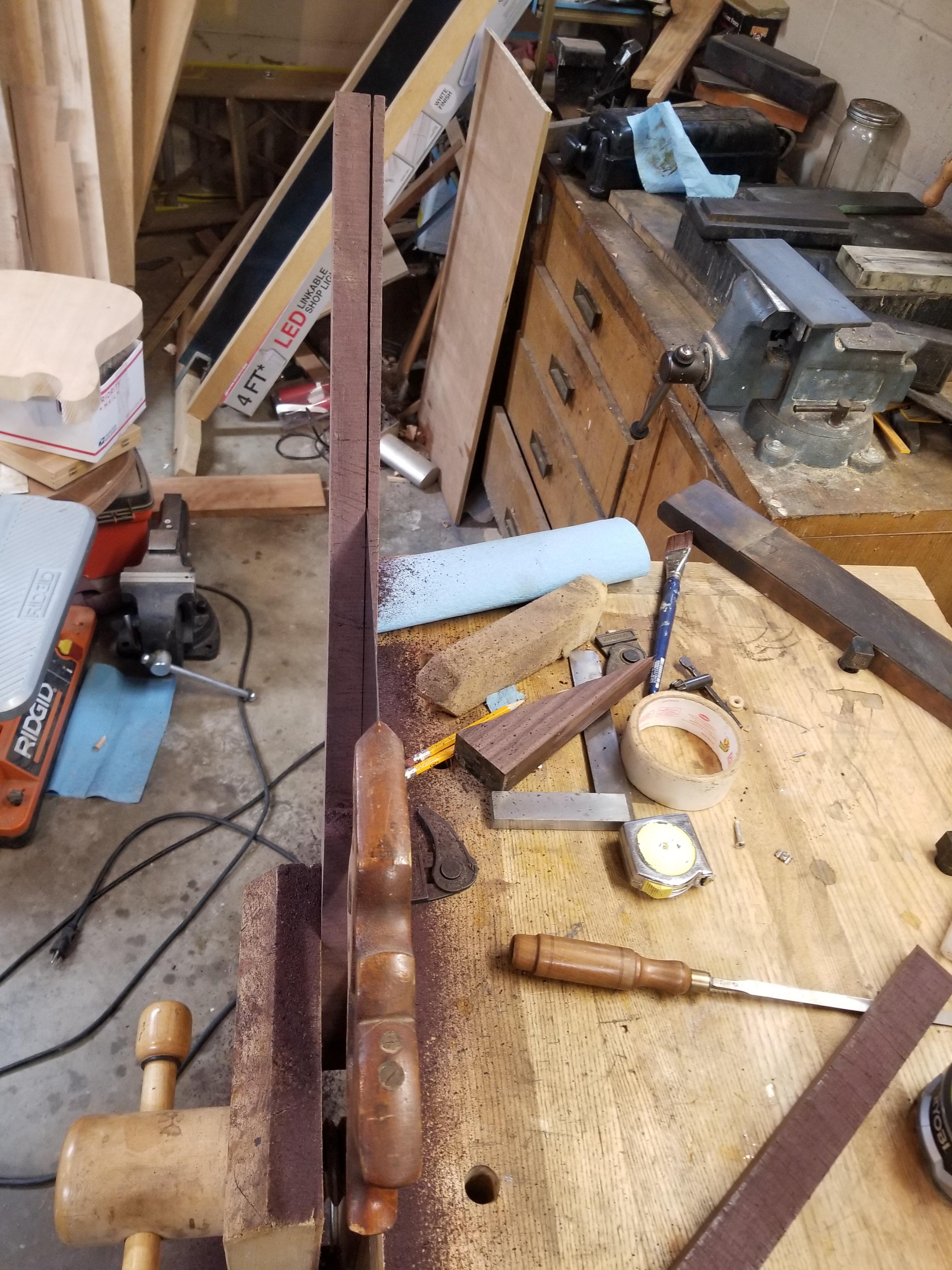
It takes about 10 minutes to do this resaw relatively accurately with a typical carpenter's saw. One of the nice things about guitars is that the bulk work really isn't much, and it's often harder to do the nuance (neck profiling, etc) properly if you use power tools instead of hand tools. It's not a break even for production, but for individual guitars, it's probably close.
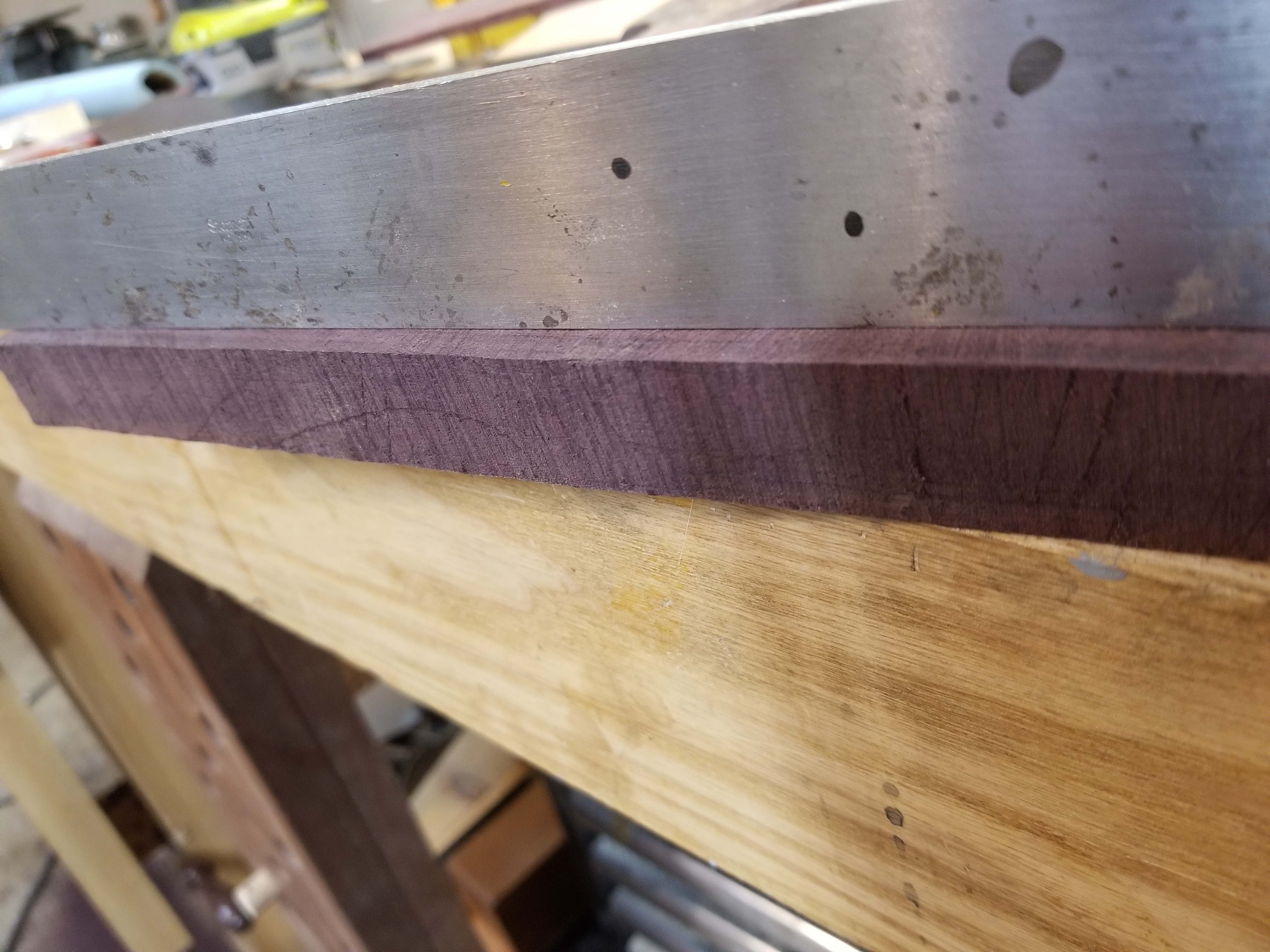
And the resulting offcut to be set aside to make a fingerboard later.
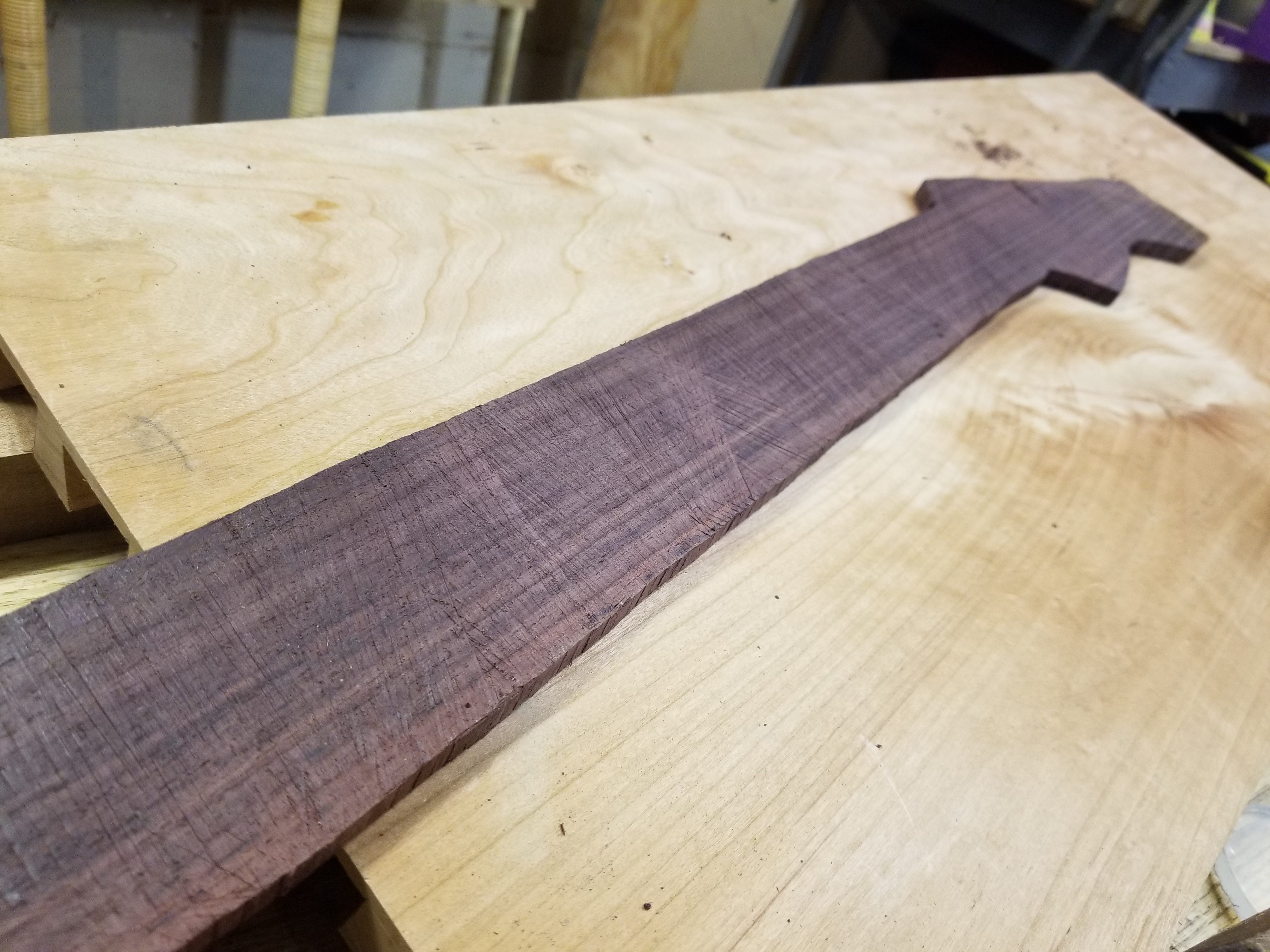
The body blank that I got for this guitar is khaya, quartered. It's fairly low density and the ribboning is strong. Planing results in no tearout with the cap iron, but grain direction does leave a tiny bit of difference in surface texture. I will leave this as is, but if I round the guitar over on the back, I may be forced to sand just to get uniform finish absorption (french polish). I will not sand out all of the plane nuance, though, just the very surface (mixing planing and sanding on a softer blank like this, even with un-tinted shellac will lead to different wood color in finish areas, looking like the wood was burnished in places and not others, etc).
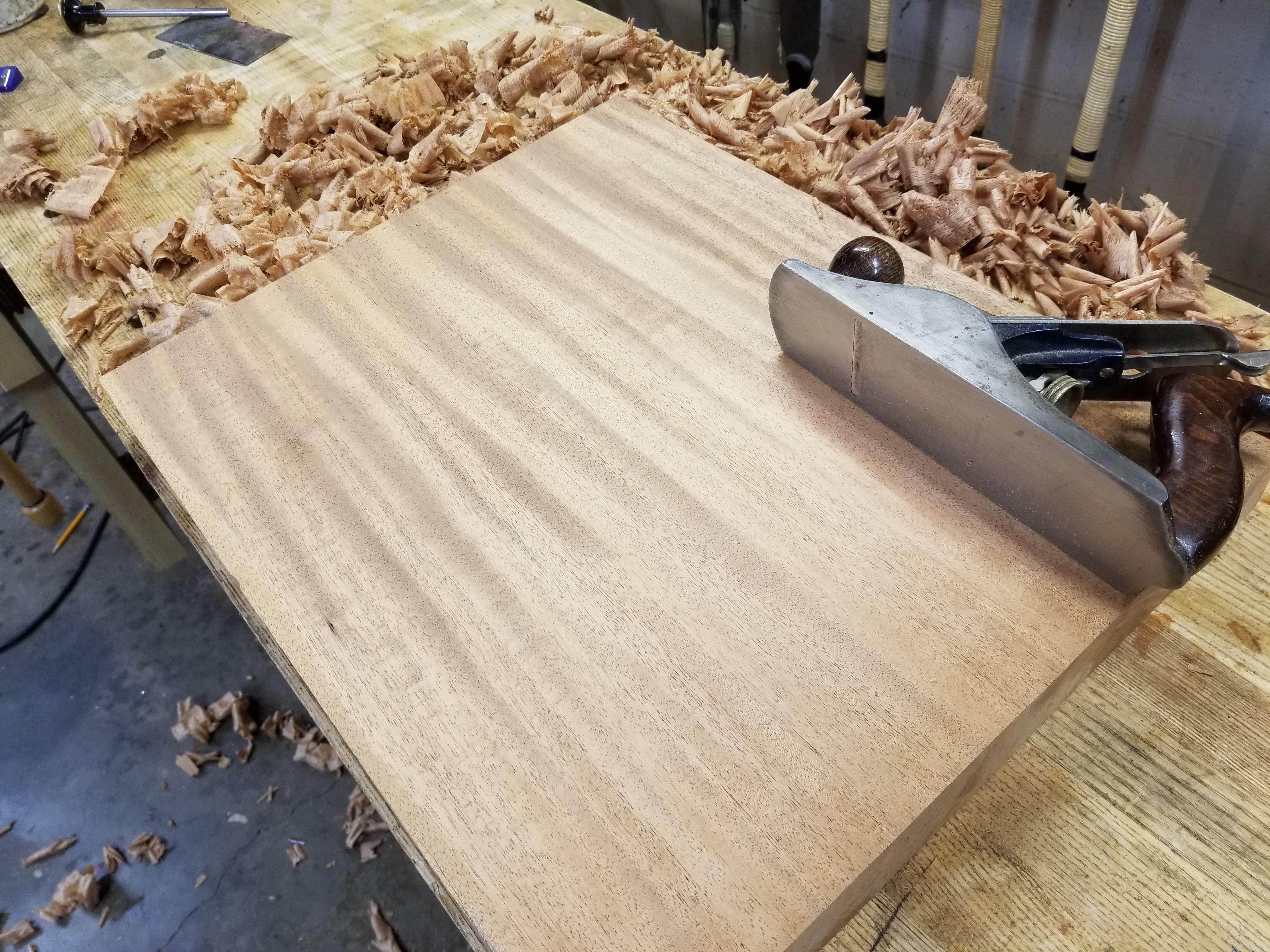
Cutting the blank - relatives are important working with hand tools, but absolutes are not. I have a general center line to help with alignment, but since I'm not using a CNC machine or any such thing, I can use the center line to aid initial work and then set hardware relative to the neck later. I cut relatively far from the line not for accuracy (it's not that important), but because khaya can blow out on the back and I don't have that much thickness to spare on this blank. I'll remove the excess with a combination of spokeshave and the oscillating spindle/belt sander in the background.
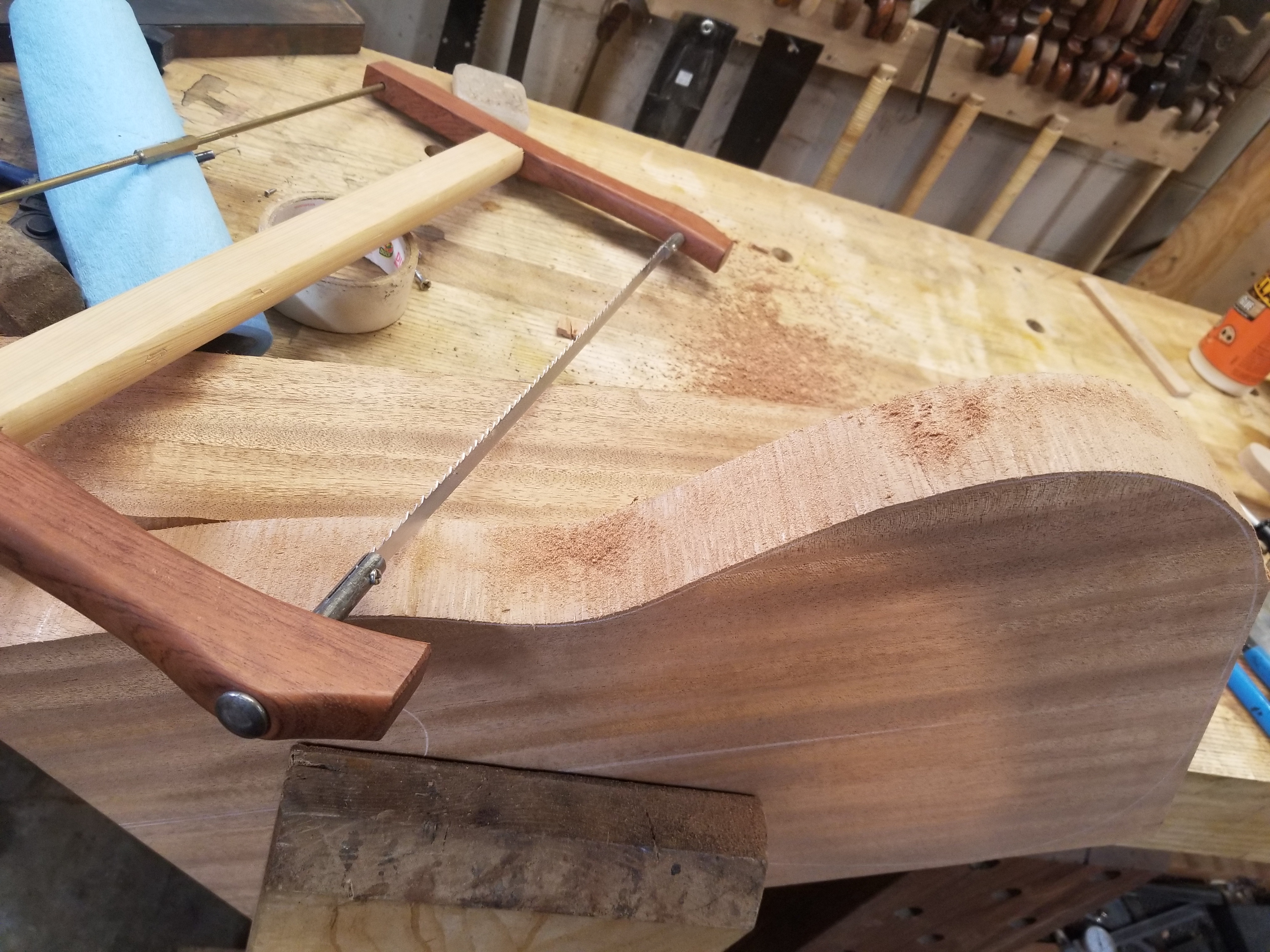