delaney001
Established Member
Hi,
Can anyone reccomend a finish to apply to the attached ash live edge table. The table will have a small amount of epoxy (probably clear) into the two cavities at the end. The legs are going to be a black steel trapezoid shape.
I have been reading about BLO and Danish oil and i also saw Mike's 1/3 mix suggested as well. Can anyone provide any suggestions. Hoping for something not too shiny or anything that will 'yellow' the timber.
Thanks
Can anyone reccomend a finish to apply to the attached ash live edge table. The table will have a small amount of epoxy (probably clear) into the two cavities at the end. The legs are going to be a black steel trapezoid shape.
I have been reading about BLO and Danish oil and i also saw Mike's 1/3 mix suggested as well. Can anyone provide any suggestions. Hoping for something not too shiny or anything that will 'yellow' the timber.
Thanks
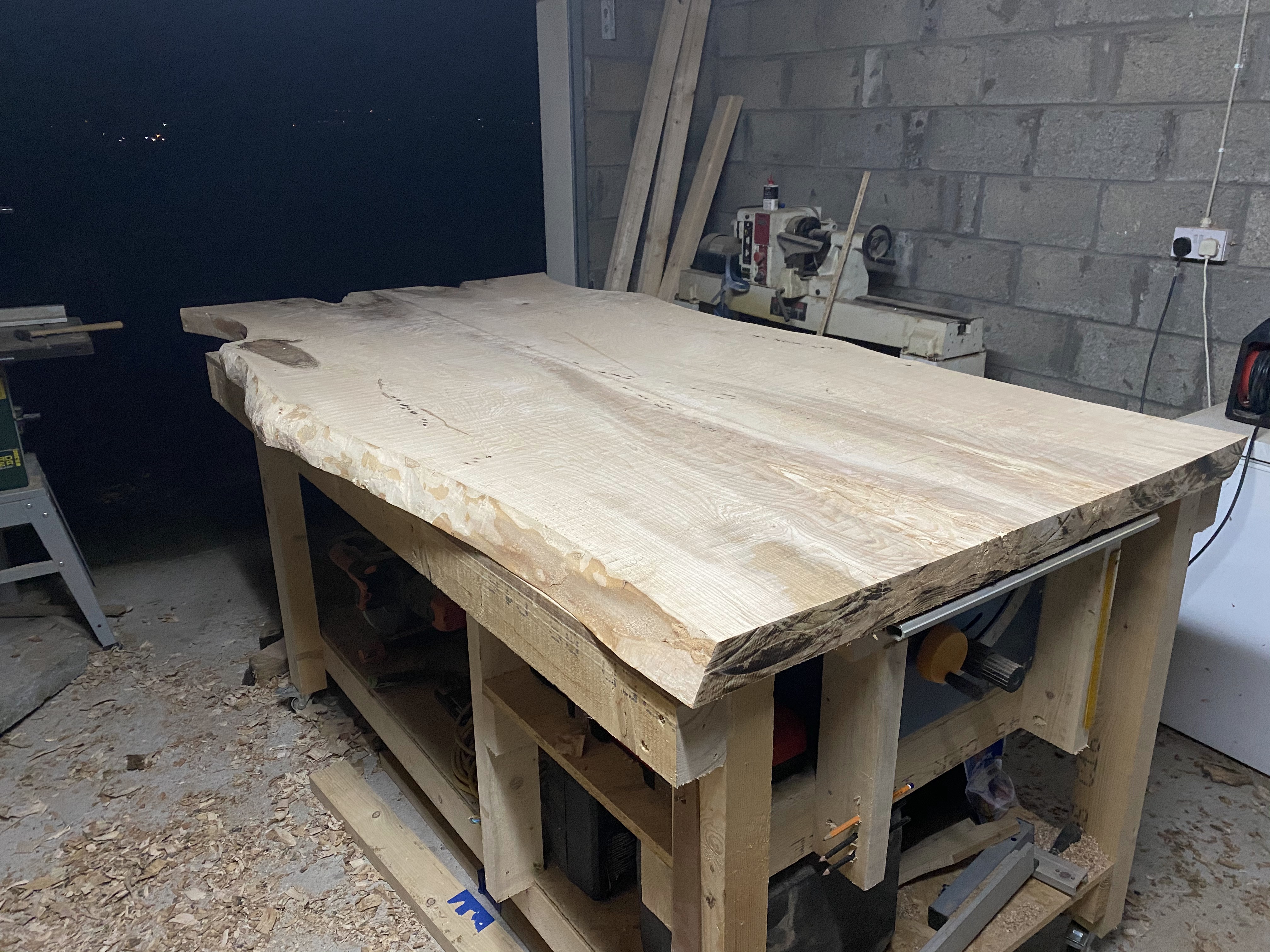
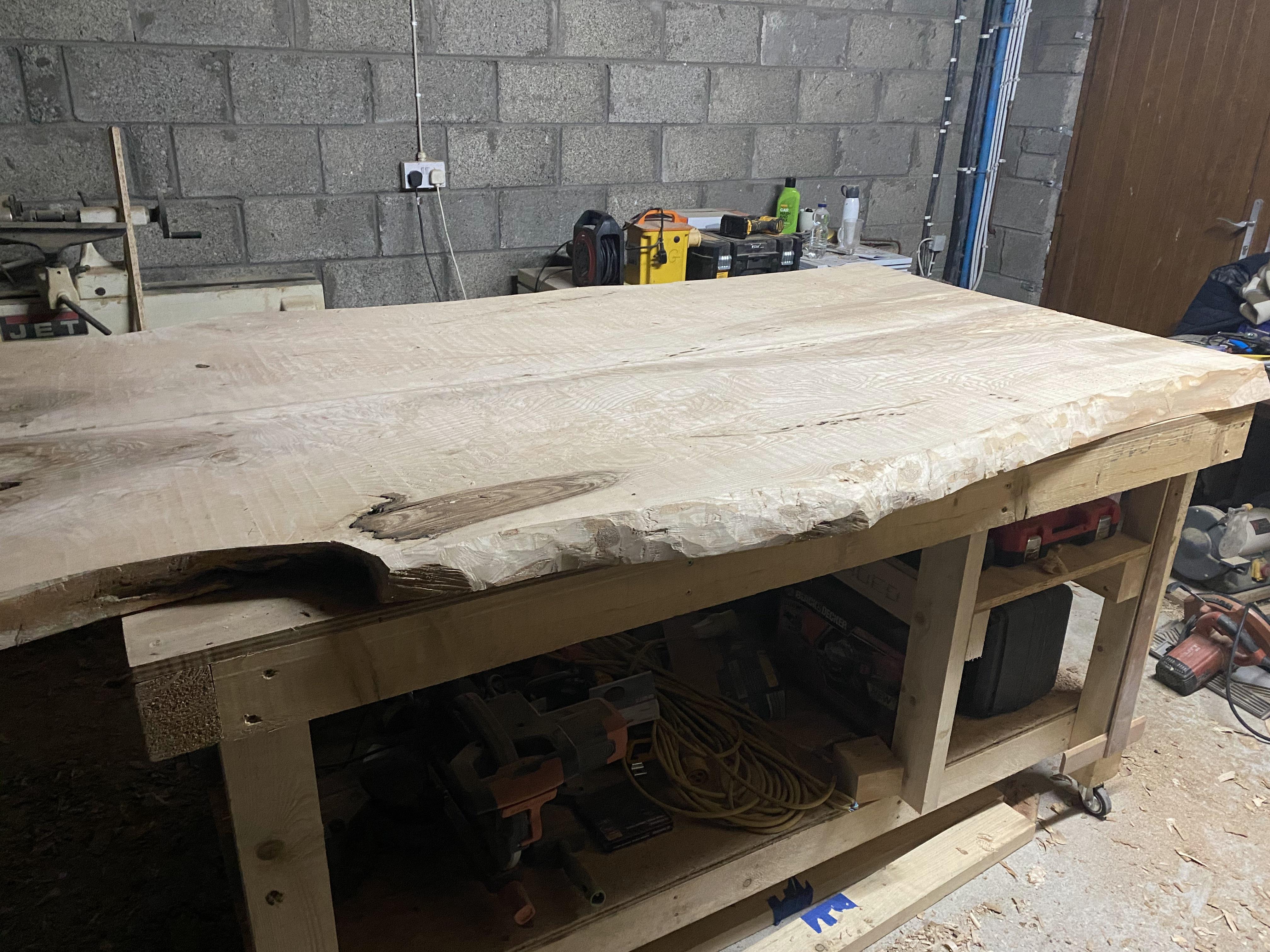
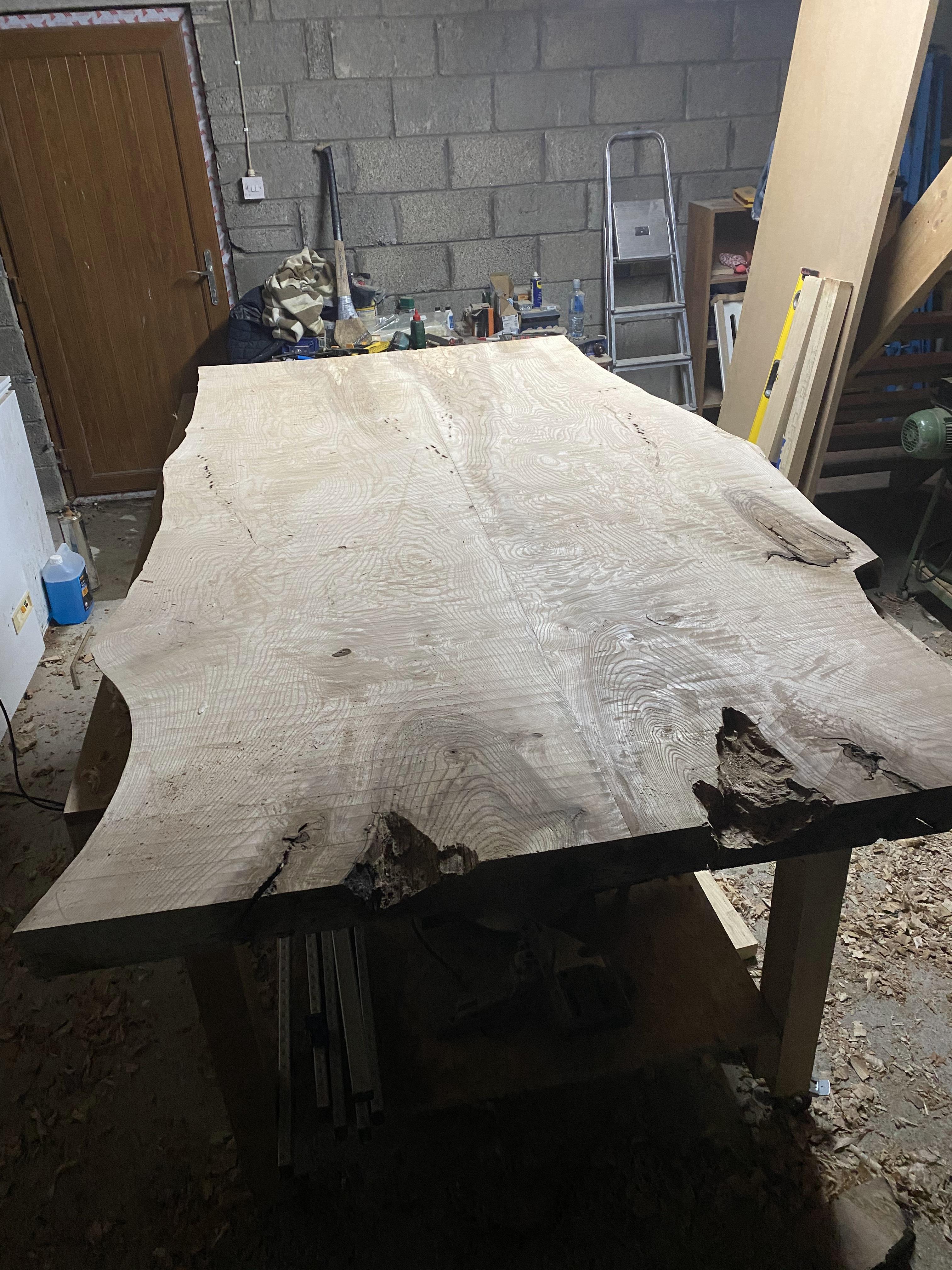
