This is the latest job to come out of my workshop. The brief was a bench that could seat three people with some storage and to go at the end of a kitchen & breakfast room. The client wanted some steel or chrome and the wood was to match the kitchen units which were predominantly solid ash.
I presented the client with sketches (side elevation and half front elevation @ 1:20) of four possible designs with a budget figure. She went for this design but was happy to leave the details to me which avoided the need to make a model.
Here are some views of the finished piece, the cushion is only covered for the photo, client is having it upholstered.
After planning & thicknessing the timber to 73mm finished thickness it was rough cut on the bandsaw to within 2-3mm of the template. I then removed the bottom bearing from the multi-trim bit shown in the router and used the top bearing to follow the shape of the template, the bearing was then replaced and used from the other side running the bearing against the previously routed surface. The holes for the arm rods were plunge cut using a guide bush & 12mm dia cutter. The template is screwed to the arm where the tennon will be cut with a bit odd DS tape at each end for good measure.
Simple jig used with guide bush to route the mortises. The holes in the back rest were plunge cut before the back was bandsawn to the angle thus keeping them aligned horizontally.
Completed legs and side rails ready for assembly
All clamped up. Actual clamping done with them laid on a flat bench
I hot melt glued an 8x4 sheet of MDF to the workshop floor to do a full size layout. The curves for the back rest were plotted with a 5.0m long trammel from a pivot glued to the opposite end of the workshop floor. However I could not swing a big enough radius to get the underside of the seat rails. For these I sprung a strip of MDF and tacked it in place with more hot melt glue then ran the base of my laminate trimmer against this with a ¼” bit to give a 4mm deep groove. I then bandsawed off the waste and ran the bearing of the multi-trim against the remaining side of the groove.
All the parts of the back rest ready for assembly. The 30 odd stainless steel spindles were all spun in the lath while holding 320 grit silicon carbide paper to them this gave a nice “brushed “ finish to the surface. I used grade 304 stainless as this had the smoothest surface to start with, total of 18.0m went into the job.
After a slightly hectic glue up it looked like this, the slats and inner edges were lacquered before assembly.
Hope you like it as much as the client did, all comments and criticisms welcomed
Jason
PS stay tuned for the matching table which has just been commissioned, I’ve just spent £750.00 on the glass & stainless steel fittings alone!
I presented the client with sketches (side elevation and half front elevation @ 1:20) of four possible designs with a budget figure. She went for this design but was happy to leave the details to me which avoided the need to make a model.
Here are some views of the finished piece, the cushion is only covered for the photo, client is having it upholstered.
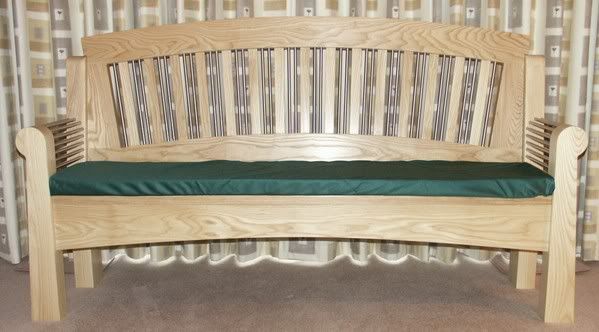
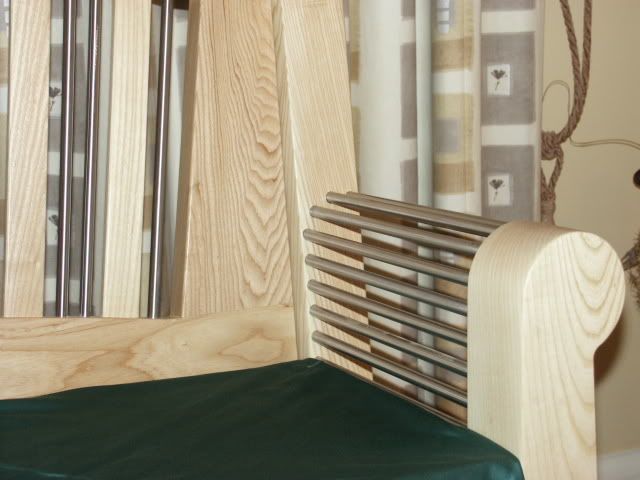
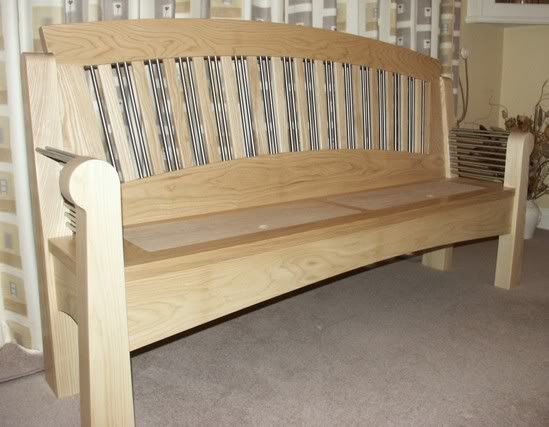
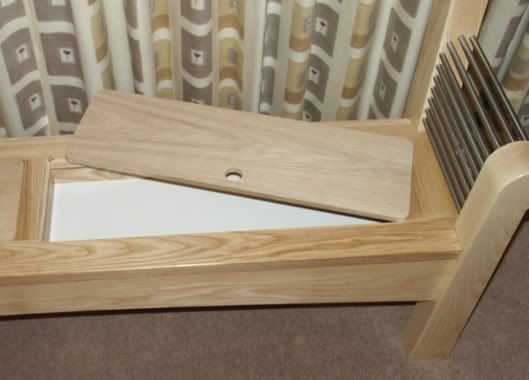
After planning & thicknessing the timber to 73mm finished thickness it was rough cut on the bandsaw to within 2-3mm of the template. I then removed the bottom bearing from the multi-trim bit shown in the router and used the top bearing to follow the shape of the template, the bearing was then replaced and used from the other side running the bearing against the previously routed surface. The holes for the arm rods were plunge cut using a guide bush & 12mm dia cutter. The template is screwed to the arm where the tennon will be cut with a bit odd DS tape at each end for good measure.
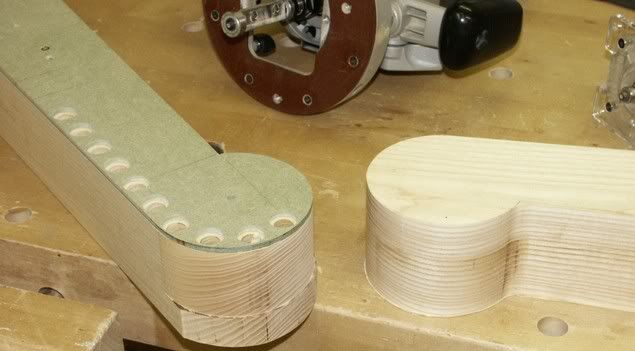
Simple jig used with guide bush to route the mortises. The holes in the back rest were plunge cut before the back was bandsawn to the angle thus keeping them aligned horizontally.
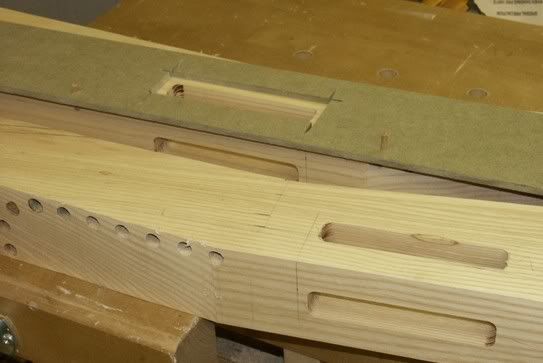
Completed legs and side rails ready for assembly
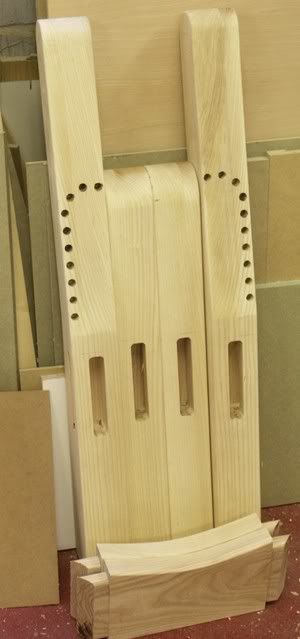
All clamped up. Actual clamping done with them laid on a flat bench
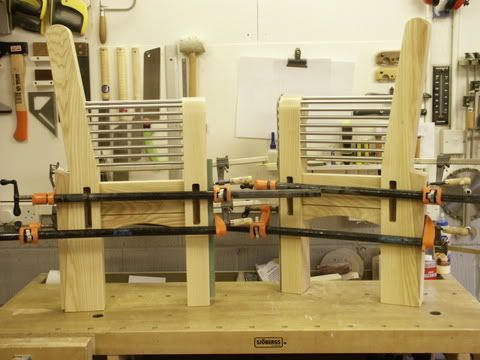
I hot melt glued an 8x4 sheet of MDF to the workshop floor to do a full size layout. The curves for the back rest were plotted with a 5.0m long trammel from a pivot glued to the opposite end of the workshop floor. However I could not swing a big enough radius to get the underside of the seat rails. For these I sprung a strip of MDF and tacked it in place with more hot melt glue then ran the base of my laminate trimmer against this with a ¼” bit to give a 4mm deep groove. I then bandsawed off the waste and ran the bearing of the multi-trim against the remaining side of the groove.
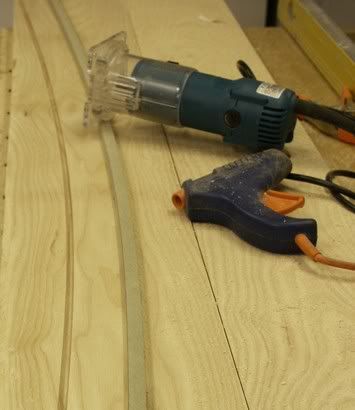
All the parts of the back rest ready for assembly. The 30 odd stainless steel spindles were all spun in the lath while holding 320 grit silicon carbide paper to them this gave a nice “brushed “ finish to the surface. I used grade 304 stainless as this had the smoothest surface to start with, total of 18.0m went into the job.
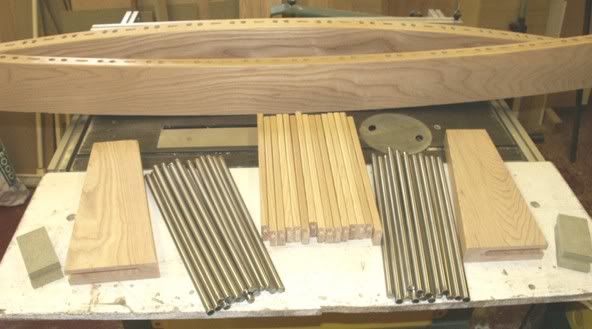
After a slightly hectic glue up it looked like this, the slats and inner edges were lacquered before assembly.
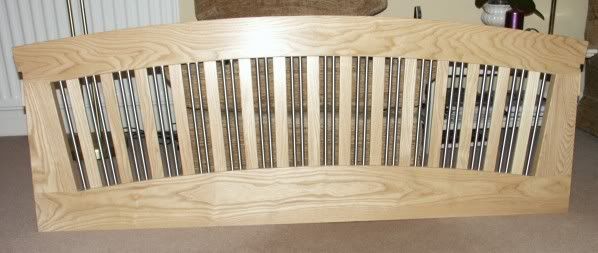
Hope you like it as much as the client did, all comments and criticisms welcomed
Jason
PS stay tuned for the matching table which has just been commissioned, I’ve just spent £750.00 on the glass & stainless steel fittings alone!