gasman
Established Member
The brief was for a traditional cheval mirror with some modern touches. So I thought I would continue my ash/ebony line which has had favourable reception previously.
I looked very hard at Steve Maskery's beautiful oval Cheval mirror in bubinga as I thought an oval mirror would be great. I have the smaller trend ellipse cutting jig (which would have been hopeless as it is too small) - and the problem with those ellipse cutting jigs is that you are constrained by the design of the jig so that there can only be about an 8" difference between the major and minor axes of the ellipse. I made my own version of it which enables about a 12 inch difference - but it would still be too fat a mirror overall.
The other problem I had with an ellipse is that unless I was going to veneer the front, it would be not possible to get a continuous flow of grain around the ellipse - there would have to be joints which, from previous experience have always opened a fraction sometime later on.
Anyway a long-winded way of explaining why I am copping out on the whole ellipse idea - instead I decided to make it a rectangle, but with curved sides so that it is fatter in the middle than the top and bottom... sort of like a coffin but rounded. I made a template and dropped it off at the glaziers - will pick up the mirror from them today
The legs are going to be fairly traditional, with the 'arms' that support the mirror curved.
This is about as good as my plans get I am afraid
So I started with the legs - made a template from ply, then roughly cut with a bandsaw, then a flush trim router bit then a roundover bit then sanding to get the basic leg shape:
To these I glued a 5mm thick ebony 'sole'
I could not really start the sides until I actually had the mirror in my hands (although I have found a 2" ash board with a curve which should be good for the sides), so I turned 2 of 35mm spheres on the lathe which will be the decoration for the top of the arms
Hopefully will be able to start on the frame later today
I looked very hard at Steve Maskery's beautiful oval Cheval mirror in bubinga as I thought an oval mirror would be great. I have the smaller trend ellipse cutting jig (which would have been hopeless as it is too small) - and the problem with those ellipse cutting jigs is that you are constrained by the design of the jig so that there can only be about an 8" difference between the major and minor axes of the ellipse. I made my own version of it which enables about a 12 inch difference - but it would still be too fat a mirror overall.
The other problem I had with an ellipse is that unless I was going to veneer the front, it would be not possible to get a continuous flow of grain around the ellipse - there would have to be joints which, from previous experience have always opened a fraction sometime later on.
Anyway a long-winded way of explaining why I am copping out on the whole ellipse idea - instead I decided to make it a rectangle, but with curved sides so that it is fatter in the middle than the top and bottom... sort of like a coffin but rounded. I made a template and dropped it off at the glaziers - will pick up the mirror from them today
The legs are going to be fairly traditional, with the 'arms' that support the mirror curved.
This is about as good as my plans get I am afraid
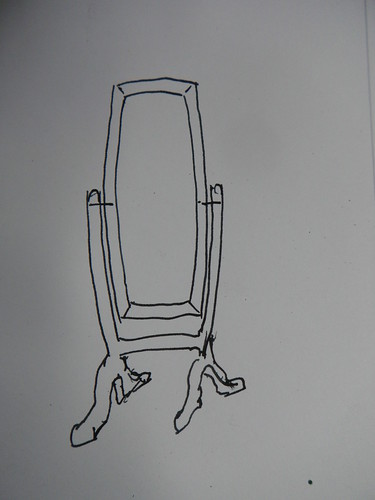
So I started with the legs - made a template from ply, then roughly cut with a bandsaw, then a flush trim router bit then a roundover bit then sanding to get the basic leg shape:
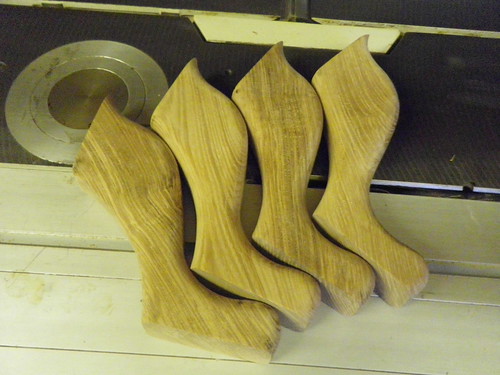
To these I glued a 5mm thick ebony 'sole'
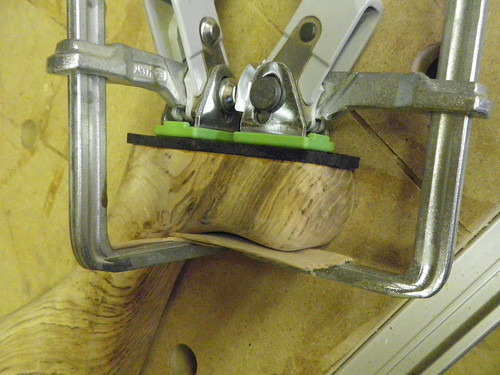
I could not really start the sides until I actually had the mirror in my hands (although I have found a 2" ash board with a curve which should be good for the sides), so I turned 2 of 35mm spheres on the lathe which will be the decoration for the top of the arms
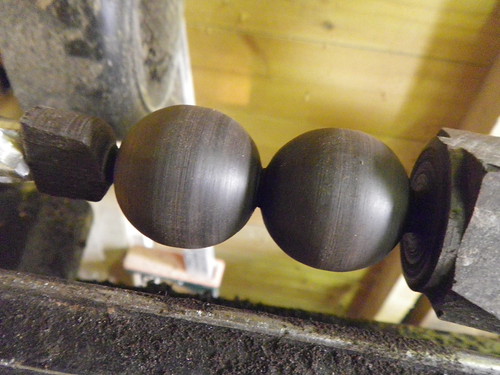
Hopefully will be able to start on the frame later today