Squarethumbs
Established Member
Hi Guys
Nice forum!
We moved into our new house in August and realised my dream of having my own decent sized workshop I was over the moon. Being from a long line of carpenters (not one myself I hasten to add) and a Radio Controlled Plane enthusuast the existing 20ft x 11 ft workshop looked just the ticket.
All was well until Autumn set in. The corrigated steel roof sweat so bad all my tools, equipment and models may aswell have been sat outside so I proceeded in replacing it with external ply and felt. Ideally I want to build an apex roof with insulation for extra storage etc but that will have to wait for now.
Over the last couple of months the ply has got quite damp and started to mould badly. Ive bought a can of decking treatment for preventing mould and then plan to paint it matt white. Is there anything else I can do? At the moment I have one of the double glazed windows slightly open for electric to my temporary Koi pond outside. Is this my main problem?
Workshop is block built on concrete base. I need to get this WS organised ready for the renovation of our three bedrooms before a new arrival end of March but dont have a large cash flow at the minute to get it exactly how I want it.
Any suggestions are very welcome.
Thanks
Guy
Nice forum!
We moved into our new house in August and realised my dream of having my own decent sized workshop I was over the moon. Being from a long line of carpenters (not one myself I hasten to add) and a Radio Controlled Plane enthusuast the existing 20ft x 11 ft workshop looked just the ticket.
All was well until Autumn set in. The corrigated steel roof sweat so bad all my tools, equipment and models may aswell have been sat outside so I proceeded in replacing it with external ply and felt. Ideally I want to build an apex roof with insulation for extra storage etc but that will have to wait for now.
Over the last couple of months the ply has got quite damp and started to mould badly. Ive bought a can of decking treatment for preventing mould and then plan to paint it matt white. Is there anything else I can do? At the moment I have one of the double glazed windows slightly open for electric to my temporary Koi pond outside. Is this my main problem?
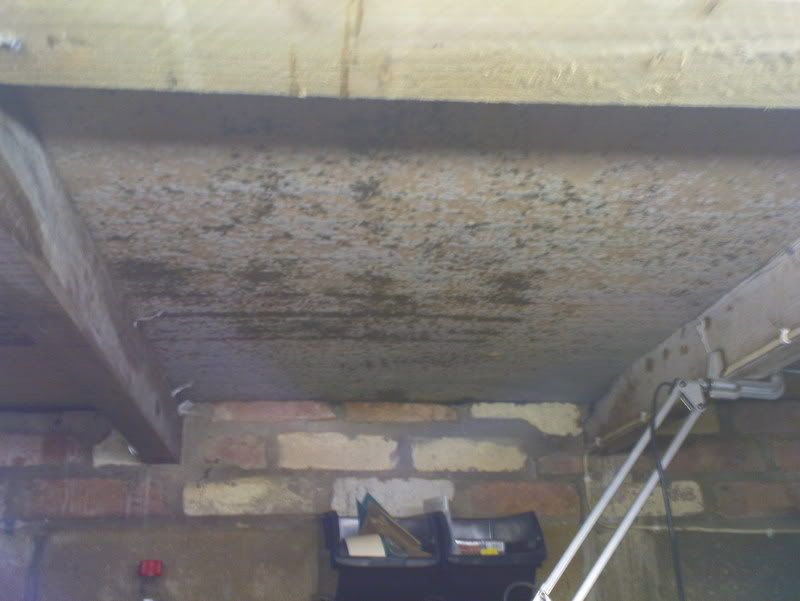
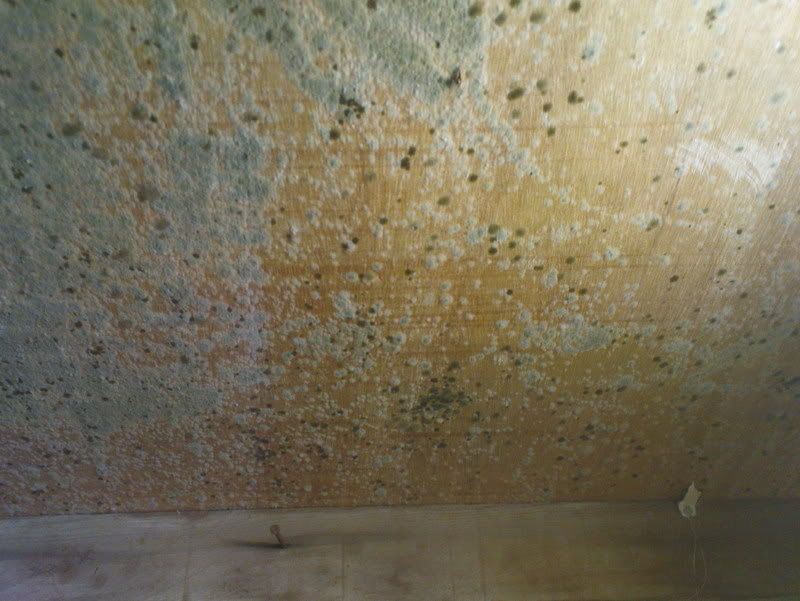
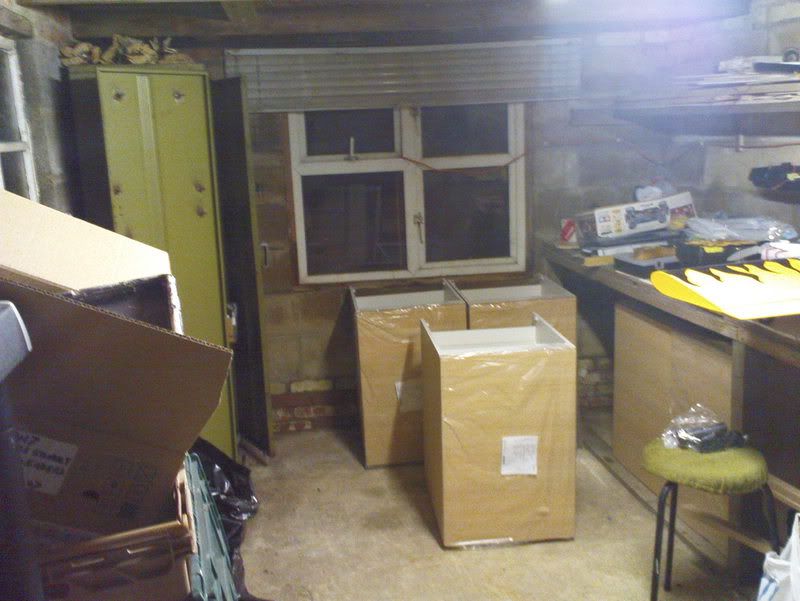
Workshop is block built on concrete base. I need to get this WS organised ready for the renovation of our three bedrooms before a new arrival end of March but dont have a large cash flow at the minute to get it exactly how I want it.
Any suggestions are very welcome.
Thanks
Guy