Derek Cohen (Perth Oz)
Established Member
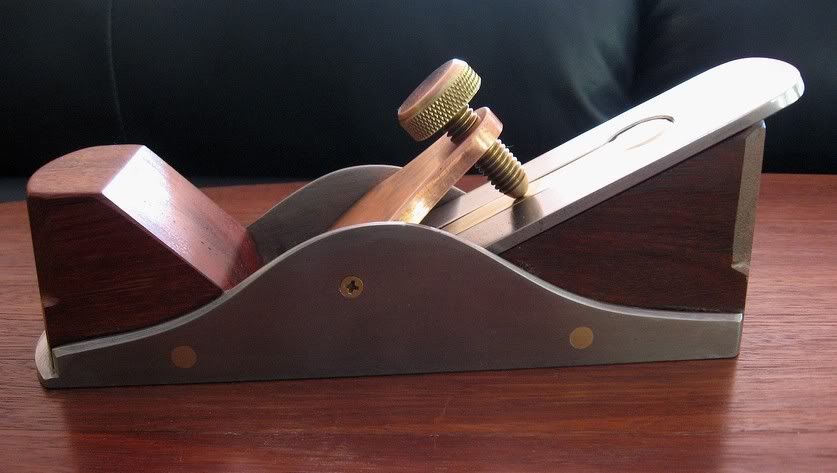
It is several years since I last built a “Stanley infill”, my previous effort based on a #4. This time I decided to use the shell of a derelict #3 Stanley to create a small smoother – the final length is just 7 ½”. I also wanted to incorporate a few ideas. So what we have here is a bevel up configuration with a 25 degree bed.
The reason for the high bed (the standard at present – from LN and LV – is 12 degrees, while Karl Holtey’s #98 is 22 ½ degrees) is to reduce the primary/secondary bevel angle. The bevel here comprises a 30 degree primary with a 35 degree micro, creating a 60 degree cutting angle.
The blade is 1 ¾” wide and 5/32” (about 4mm) thick. It came out of a Danish Langeskov woodie. No cap iron is needed. Since a solid surface was needed, I filledthe blade slot with a piece of brass. This was filed fractionally too large, then left in the freezer to shrink, before force-fitting it (a big hammer!). After it thawed the brass expanded and the whole piece became one solid affair.
The lever cap was carved (!) from a block of phosphor bronze (as I was informed) since I had nothing else to hand that was the desired thickness. This stuff is incredibly hard (I believe that it is used for bearings). It has a warm pink tone. I have used a combination of this and yellow brass throughout.
I lack metal machining tools, unless you include a drill press and an angle grinder. So the task of building a lever cap screw would be well beyond me – if I did not cheat a little. What I do is raid the local Borg’s gardening section for solid brass hose fittings and weld these together. The cap cover was a copper (Australian) 2c piece, so as to match the colour of the lever cap.
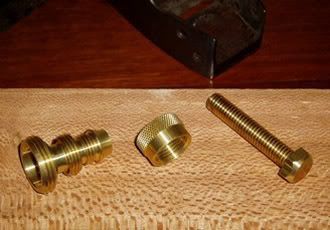
The infill is just scrap Jarrah, well seasoned but I did not have the desired thickness and had to laminate two pieces. This was shaped, then epoxied into place. For additional strength and a “a look”, brass screws were added, then filed flush.
I must admit to having ambivalent feelings about the final shape. I much prefer round to straight sides, and the result here seemed to evolve as if it had a life of its own.
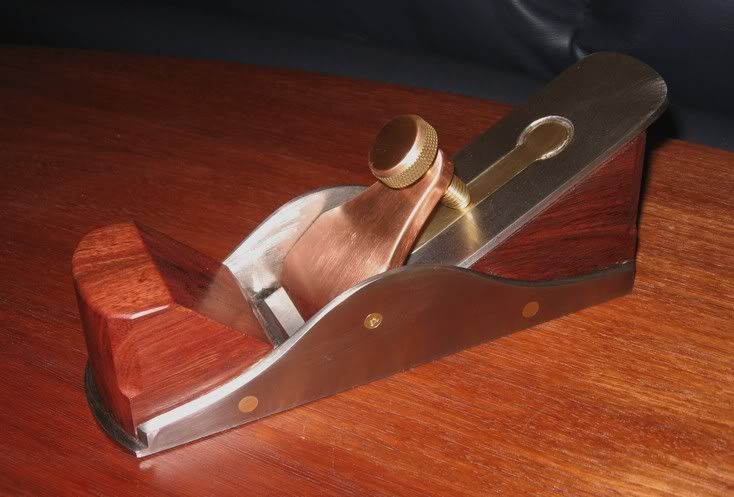
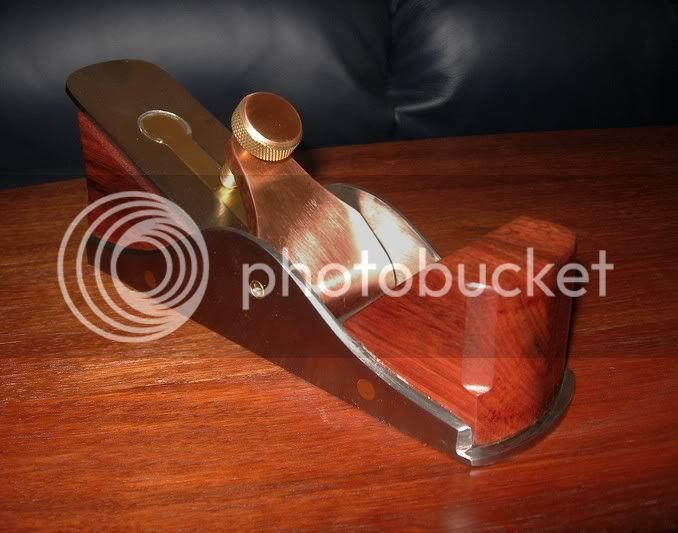
The mouth was completed last of all, deliberately made too small, and opened up gradually with files. The end result is a very fine mouth.
How well does it work?
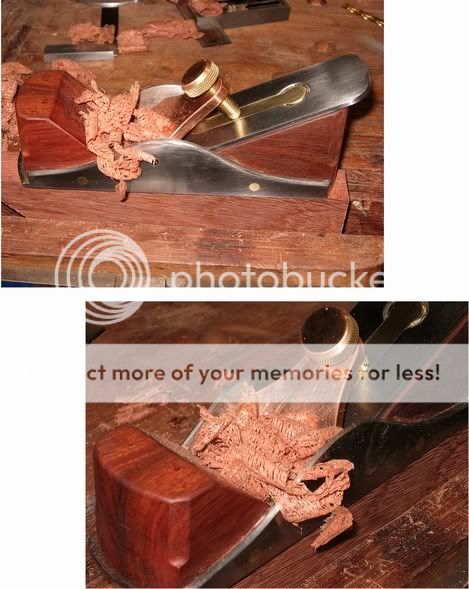
I hope this effort might inspire a few more Stanley infills!
Regards from Perth
Derek
December 2006