tekno.mage
Established Member
My partner & I have just built a prototype thread-cutting jig for use on a wood lathe. This prototype assumes you have access to woodworking equipment only (ie no metal working lathe to turn bits & bobs) and have to make do with easily available chuck adpaters and threaded rods etc. You will also need some scraps of MDF and box wood (or similar).
Currently it cuts 16tpi threads using a length of 3/4" UNF mild steel rod as the leadscrew. I chose this thread size for a number of reasons - firstly, it is suitable for use on turned boxes, secondly I was able to easily source a cheap chuck adapter for my chuck to fit this size rod (it's the same size as the common 3/4" x 16tpi lathe spindle), and thirdly I found a source of the threaded rod & nuts at a reasonable cost at www.ironmongeryonline.co.uk
The most expensive thing I had to buy was the cutter. This is a 3/4" 60 degree double angle milling cutter with 3/8" shank. The only UK supplier I could find of double angle milling cutters was MSC/J&L Industrial Supply www.mscjlindustrial.co.uk
They stock two sizes of cutter, a 1" and a 3/4". The 3/4" will let you thread the inside of smaller items than the 1". They supply the cutters in a variety of materials, the cheapest are the carbon steel variety and even this was £30.00 inc delivery.
I fit the cutter into a 3/8" collet that goes directly into the MT2 taper in my lathe spindle and is secured by a drawbar. Suitable collets can be had from www.chestermachinetools.com at around £6.00 each. You could hold the cutter in a jacobs chuck, by this will stick out further and may introduce "waggle" to the cutter.
We mounted the whole thing on an X-Y cross slide which gives very precise side to side and back & front adjustments. It also made it easy to set the jig up so the cutter was cutting at centre height. However, it is a nice to have feature, and not essential. You could build your own sidewas cross-slide mechanism using another bit of threaded rod!
Here's an annoted photo of the jig as it stands at present
And one from the other side
And a close up of the cutter
If you are dead keen, you can find a PDF diagram (not to scale) here www.teknomage.co.uk/photos/threads/diagram.pdf
Now all we have to do is make a minor adjustment to take some sloppiness out of it (you have to turn the handwheel rather carefully at the moment) and learn to use the thing properly!
From reading Richard Raffan's book on box-making he suggests that 16tpi threads are cut 1.5mm deep, and my first rough attempts on boxwood look ok to me - and just about fitted together!!! The thread in the photo was cut in holly, and was ok until we reversed the thing back over the cutter - which cracked off the crests of the threads :-(
Will have some more practise tomorrow. I am hoping I'll be able to cut threads in somewhat softer woods than boxwood with this system... we shall see.
tekno.mage
Currently it cuts 16tpi threads using a length of 3/4" UNF mild steel rod as the leadscrew. I chose this thread size for a number of reasons - firstly, it is suitable for use on turned boxes, secondly I was able to easily source a cheap chuck adapter for my chuck to fit this size rod (it's the same size as the common 3/4" x 16tpi lathe spindle), and thirdly I found a source of the threaded rod & nuts at a reasonable cost at www.ironmongeryonline.co.uk
The most expensive thing I had to buy was the cutter. This is a 3/4" 60 degree double angle milling cutter with 3/8" shank. The only UK supplier I could find of double angle milling cutters was MSC/J&L Industrial Supply www.mscjlindustrial.co.uk
They stock two sizes of cutter, a 1" and a 3/4". The 3/4" will let you thread the inside of smaller items than the 1". They supply the cutters in a variety of materials, the cheapest are the carbon steel variety and even this was £30.00 inc delivery.
I fit the cutter into a 3/8" collet that goes directly into the MT2 taper in my lathe spindle and is secured by a drawbar. Suitable collets can be had from www.chestermachinetools.com at around £6.00 each. You could hold the cutter in a jacobs chuck, by this will stick out further and may introduce "waggle" to the cutter.
We mounted the whole thing on an X-Y cross slide which gives very precise side to side and back & front adjustments. It also made it easy to set the jig up so the cutter was cutting at centre height. However, it is a nice to have feature, and not essential. You could build your own sidewas cross-slide mechanism using another bit of threaded rod!
Here's an annoted photo of the jig as it stands at present
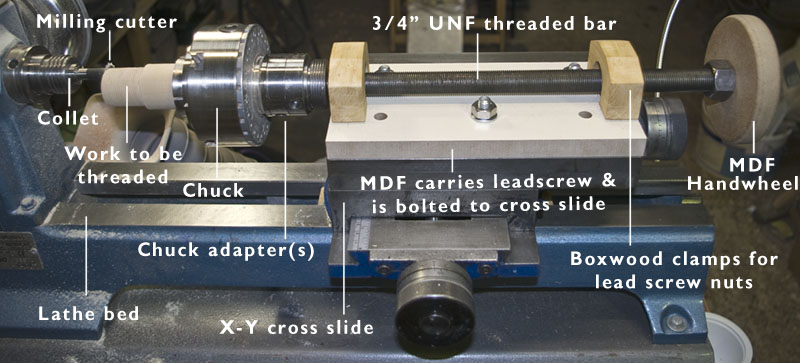
And one from the other side
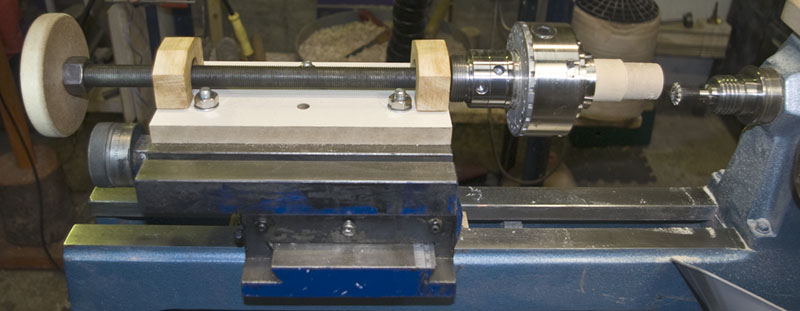
And a close up of the cutter
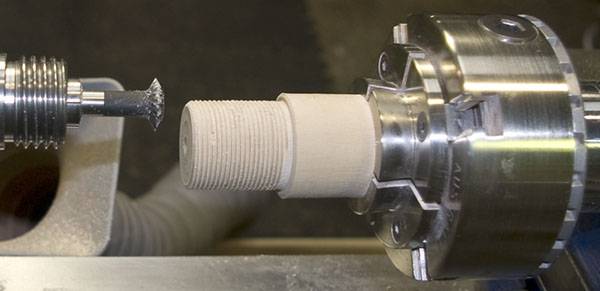
If you are dead keen, you can find a PDF diagram (not to scale) here www.teknomage.co.uk/photos/threads/diagram.pdf
Now all we have to do is make a minor adjustment to take some sloppiness out of it (you have to turn the handwheel rather carefully at the moment) and learn to use the thing properly!
From reading Richard Raffan's book on box-making he suggests that 16tpi threads are cut 1.5mm deep, and my first rough attempts on boxwood look ok to me - and just about fitted together!!! The thread in the photo was cut in holly, and was ok until we reversed the thing back over the cutter - which cracked off the crests of the threads :-(
Will have some more practise tomorrow. I am hoping I'll be able to cut threads in somewhat softer woods than boxwood with this system... we shall see.
tekno.mage