I recently posted some pictures of a late model Norris smoother that I was cleaning up for a friend:
It has the nice traditional curved shape, like its wooden equivalent.
I was reading about these planes in an old Christie's Collectors Guide to Woodworking Tools, published in 1984 by Christopher Proudfoot and Philip Walker. They wrote:
"Norris carried on into the 1940s and was revived after the war years as Norris Planes and Tools Ltd; planes were made by this firm until 1952. These late planes were not dovetailed, but made from solid channel-section rolled steel (how this was achieved in the case of coffin-sided planes has yet to be explained to me). The sides were often finished with a pattern of rotary lapping."
So, has this question been answered? How did they take a chunk of this stuff
and give it those nice curved sides?
It's maybe worth noting that both ends are open, (as I think the were on some of the dovetailed planes?) but this really does seem a surprising statement to me.

It has the nice traditional curved shape, like its wooden equivalent.
I was reading about these planes in an old Christie's Collectors Guide to Woodworking Tools, published in 1984 by Christopher Proudfoot and Philip Walker. They wrote:
"Norris carried on into the 1940s and was revived after the war years as Norris Planes and Tools Ltd; planes were made by this firm until 1952. These late planes were not dovetailed, but made from solid channel-section rolled steel (how this was achieved in the case of coffin-sided planes has yet to be explained to me). The sides were often finished with a pattern of rotary lapping."
So, has this question been answered? How did they take a chunk of this stuff
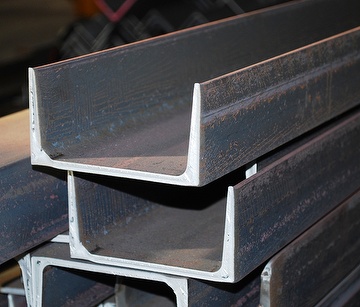
and give it those nice curved sides?
It's maybe worth noting that both ends are open, (as I think the were on some of the dovetailed planes?) but this really does seem a surprising statement to me.