I did some controlled testing to compare a bunch of irons because nobody has been considerate enough to plane to failure in a controlled test, and also because nobody knew how well V11 stacked up against its claims. Some of us (me included) were suspicious and thought that we could get new data and probably knock down the advertising claims of V11 a little at the same time. My specific issue was that I didn't think MDF was a good proxy for what would happen in clean wood that wasn't as abrasive. I still don't know that MDF is a good test bed (it seems like a really lazy way to test things to me), but the results held.
One of the other participants (I tested everything, but a few people provided ideas regarding what to test) wanted to know if he could go to a simplified more coarse sharpening setup, and if he did, what would the compromise be?
Steve Elliot tested this long ago and charted information, but it never hurts to do it a second time. Steve's conclusion was surprising not that finer edge finishes make for longer planing, but how much they do, and he found at the time that edges all the way down to fraction of a micron diamonds did better than coarser abrasives, measurably so.
I didn't go to sub micron, but I did test a 1200 grit ezelap plate (which is finer than the number would suggest), a 5 micron diamond powder (which is quite coarse for an edge), 2.5, and 1 micron, as well as a dan's black finish stone (the best arkansas stone I know of, and most consistent from one to the next) as well as my favorite washita.
These tests were controlled using a guide for angle, the same test piece of wood, and wire edges were stropped off with confirmation of a clean edge under a metallurgical microscope.
The wood used is beech heart, the iron used is O1 (this is after testing the other alloys, and I had no interest in potentially planing 2000 feet to dull each time with V11 or M4). Shavings until failure are approximately 2 1/2 thousandth thick, something a typical user might work with on a smoothing plane until the last pass. Here's the footage planed:
* 1200 ezelap on the bevel, back bevel with 1 micron diamond powder on cast iron - 527 feet (dull surface from the start and high planing resistance)
* 1 micron diamond on both sides of the bevel - 840 feet
* 5 micron diamond on both sides of the bevel - 568 feet (dull feeling and resistant, like the ezelap and back bevel combination)
* dan's black stone front and back - 700 feet
Those results were done with a 35 degree final bevel, and a request was made to run some at 30 degrees. I see quality issues with small chips on some irons below about 32/33, so I generally freehand around that. 35 was chosen for other testing because it's easy on a hard-to-hone iron to prescribe three bevels to ensure that the last stone actually works the very edge (grind, 32, 35 are the steps). I learned that from a charlesworth video when I started, and figured anyone who didn't like the results I posted could very easily run the test on their own
At 30 degrees final bevel, the additional longevity in a hand plane showed a little bit as follows:3
* 1 micron diamond on both sides of the bevel - 908 feet
* dan's black stone front and back - 738 feet
I threw out the 2 1/2 micron results, as i recall, they were unexpectedly short and I didn't feel like redoing them. But I can't remember for sure what the reason was other than something didn't work out right. The sharpness was also unimpressive.
It was a pain to do all of these with a microscope and a guide (to set everything identically and then confirm everything visually under a scope. about half of the irons had some kind of edge issue after sharpening with a guide that one would never see with the naked eye. I don't think they would affect much in longevity, but part of the testing was to judge surface quality, and it's not quite fair to put an iron with a defect on wood and then comment about the lines that it leaves behind).
The perfectly white reflective smooth pictures of one micron diamond are shown on other posts. There's some sentiment that natural stones create a longer lasting edge, but I'd suspect that they generally do not as there are no natural stones that leave an edge as fine. It's easy to get a good edge on an oilstone. It's quite hard to get one visually perfect with no defects after stropping.
Here is a finished black arkansas stone edge (you can see that the stropping moves the edge around a little bit):
5 micron diamond (it actually looks great, but the edge itself is rounded over after stropping on bare leather - the toothy bits left by 5 micron diamonds just round off on a bare leather strop)
While i also thought that this was worth looking at, I have to admit that the cycle time freehand for finishing with a finer abrasive is probably 20 seconds longer at the most (1:20 vs 1 minute), so there's no great reason once you master freehand to use coarse abrasives to finish. Doing all of these tests at the same time gives you a much better feel for the difference in cut resistance and surface quality - it's stark. 1 micron diamonds also do a nice job of prepping an edge for the strop - there just isn't much there to have to strop off - noticeably less even than a black arkansas of the finest quality).
A fine washita makes for results very similar to those of the black arkansas stone (washitas work fine with V11, but not M4 and 3V - I'm beginning to think that vanadium carbides burnish novaculite too much. V11 slows the washita down a little bit, but the edge is actually finer off of a washita with V11 than it is with O1 - not a horrible side effect for finishing).
One of the other participants (I tested everything, but a few people provided ideas regarding what to test) wanted to know if he could go to a simplified more coarse sharpening setup, and if he did, what would the compromise be?
Steve Elliot tested this long ago and charted information, but it never hurts to do it a second time. Steve's conclusion was surprising not that finer edge finishes make for longer planing, but how much they do, and he found at the time that edges all the way down to fraction of a micron diamonds did better than coarser abrasives, measurably so.
I didn't go to sub micron, but I did test a 1200 grit ezelap plate (which is finer than the number would suggest), a 5 micron diamond powder (which is quite coarse for an edge), 2.5, and 1 micron, as well as a dan's black finish stone (the best arkansas stone I know of, and most consistent from one to the next) as well as my favorite washita.
These tests were controlled using a guide for angle, the same test piece of wood, and wire edges were stropped off with confirmation of a clean edge under a metallurgical microscope.
The wood used is beech heart, the iron used is O1 (this is after testing the other alloys, and I had no interest in potentially planing 2000 feet to dull each time with V11 or M4). Shavings until failure are approximately 2 1/2 thousandth thick, something a typical user might work with on a smoothing plane until the last pass. Here's the footage planed:
* 1200 ezelap on the bevel, back bevel with 1 micron diamond powder on cast iron - 527 feet (dull surface from the start and high planing resistance)
* 1 micron diamond on both sides of the bevel - 840 feet
* 5 micron diamond on both sides of the bevel - 568 feet (dull feeling and resistant, like the ezelap and back bevel combination)
* dan's black stone front and back - 700 feet
Those results were done with a 35 degree final bevel, and a request was made to run some at 30 degrees. I see quality issues with small chips on some irons below about 32/33, so I generally freehand around that. 35 was chosen for other testing because it's easy on a hard-to-hone iron to prescribe three bevels to ensure that the last stone actually works the very edge (grind, 32, 35 are the steps). I learned that from a charlesworth video when I started, and figured anyone who didn't like the results I posted could very easily run the test on their own
At 30 degrees final bevel, the additional longevity in a hand plane showed a little bit as follows:3
* 1 micron diamond on both sides of the bevel - 908 feet
* dan's black stone front and back - 738 feet
I threw out the 2 1/2 micron results, as i recall, they were unexpectedly short and I didn't feel like redoing them. But I can't remember for sure what the reason was other than something didn't work out right. The sharpness was also unimpressive.
It was a pain to do all of these with a microscope and a guide (to set everything identically and then confirm everything visually under a scope. about half of the irons had some kind of edge issue after sharpening with a guide that one would never see with the naked eye. I don't think they would affect much in longevity, but part of the testing was to judge surface quality, and it's not quite fair to put an iron with a defect on wood and then comment about the lines that it leaves behind).
The perfectly white reflective smooth pictures of one micron diamond are shown on other posts. There's some sentiment that natural stones create a longer lasting edge, but I'd suspect that they generally do not as there are no natural stones that leave an edge as fine. It's easy to get a good edge on an oilstone. It's quite hard to get one visually perfect with no defects after stropping.
Here is a finished black arkansas stone edge (you can see that the stropping moves the edge around a little bit):
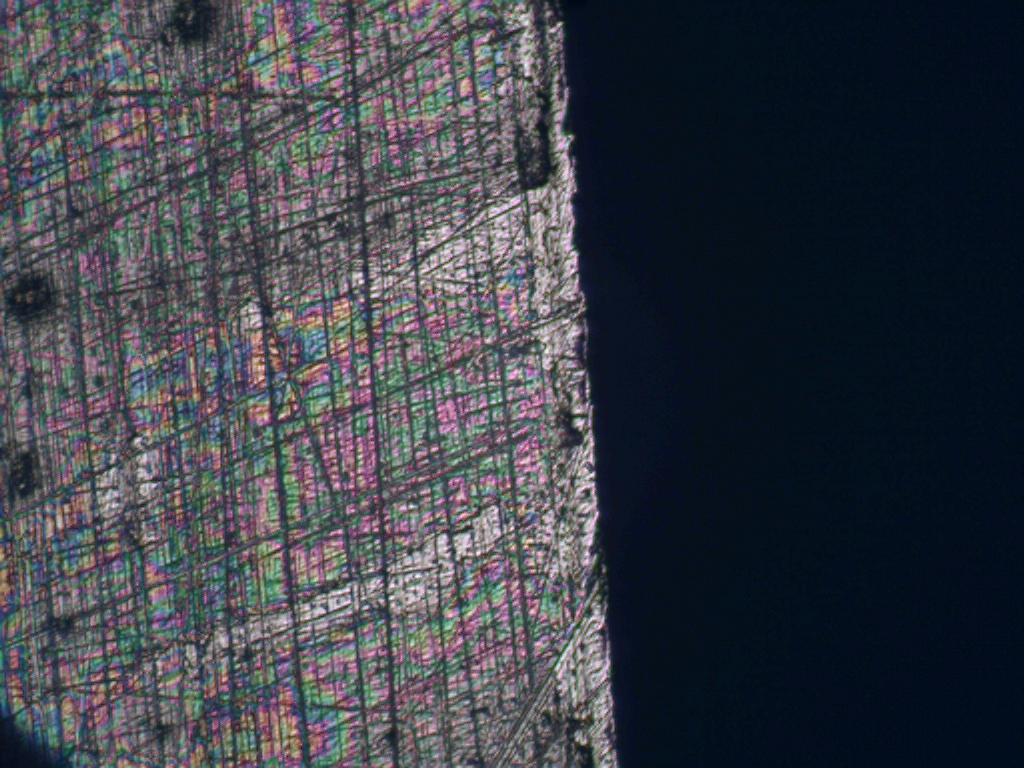
5 micron diamond (it actually looks great, but the edge itself is rounded over after stropping on bare leather - the toothy bits left by 5 micron diamonds just round off on a bare leather strop)
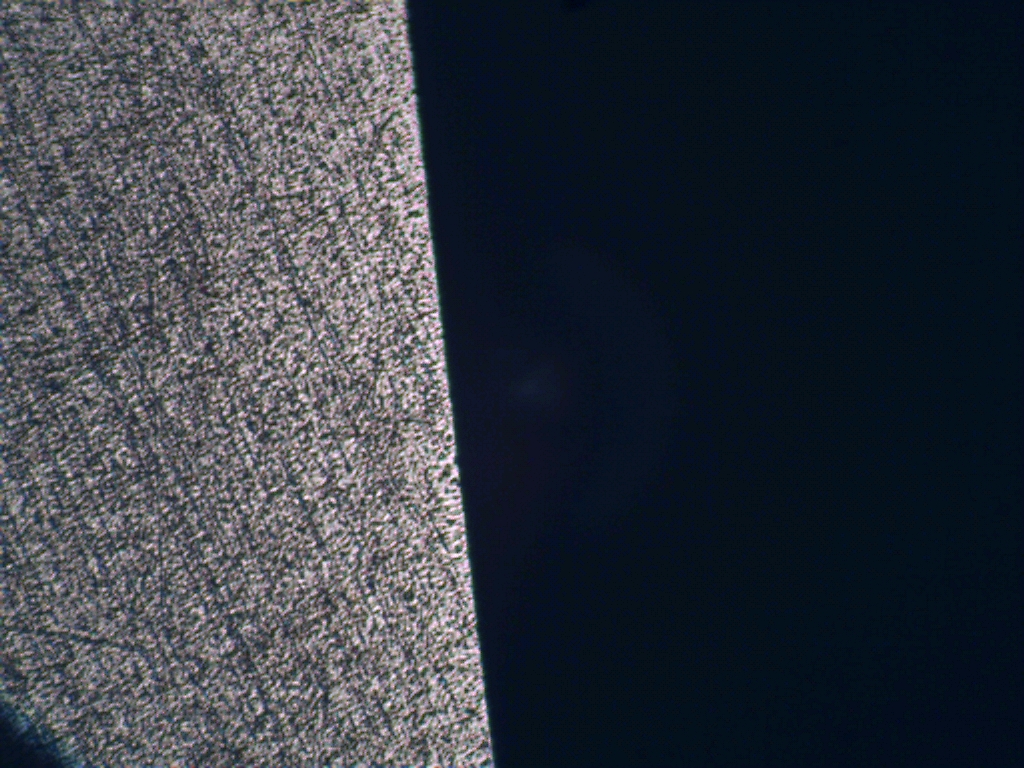
While i also thought that this was worth looking at, I have to admit that the cycle time freehand for finishing with a finer abrasive is probably 20 seconds longer at the most (1:20 vs 1 minute), so there's no great reason once you master freehand to use coarse abrasives to finish. Doing all of these tests at the same time gives you a much better feel for the difference in cut resistance and surface quality - it's stark. 1 micron diamonds also do a nice job of prepping an edge for the strop - there just isn't much there to have to strop off - noticeably less even than a black arkansas of the finest quality).
A fine washita makes for results very similar to those of the black arkansas stone (washitas work fine with V11, but not M4 and 3V - I'm beginning to think that vanadium carbides burnish novaculite too much. V11 slows the washita down a little bit, but the edge is actually finer off of a washita with V11 than it is with O1 - not a horrible side effect for finishing).