I'm trying out a few ideas with my proposed dual extractor system.
I'm thinking I've made a prize cock up here........
turning the yellow motor on results in a pleasing amount of suction and a good exhaust strength.
However turning the blue motor on results in a reduction of suck from the yellow one by about 80-90% i.e. hardly any suck down the flex pipe.
Now I think I can explain it, from my distant past physics day I can remember that " an increase in fluid flow results in a reduction of pressure AT THAT POINT", SO at the "y" piece the yellow extractor is effectively sucking vacuum........
My question is this:
if you exagerate this effect, say connect both extractors together end-2-end then both will be trying to suck vacuum (from the other motor).
If we bring the junction round to 90 degrees, then past to where we are in the picture then we see the effect observed. If we continue round and reduce the angle to 0 degrees using a true "Y" piece i.e. a junction where the 2 air flows join exactly parallel:
would this solve my problem?
Steve
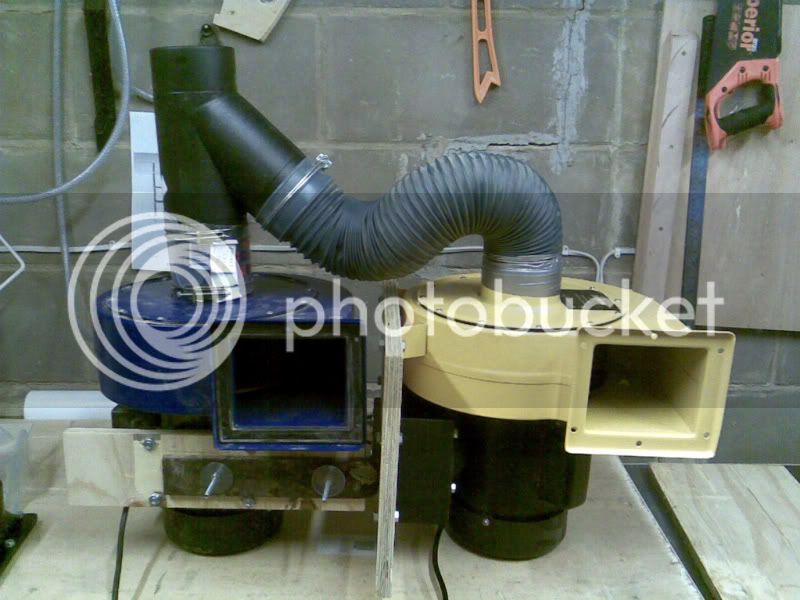
I'm thinking I've made a prize cock up here........
turning the yellow motor on results in a pleasing amount of suction and a good exhaust strength.
However turning the blue motor on results in a reduction of suck from the yellow one by about 80-90% i.e. hardly any suck down the flex pipe.
Now I think I can explain it, from my distant past physics day I can remember that " an increase in fluid flow results in a reduction of pressure AT THAT POINT", SO at the "y" piece the yellow extractor is effectively sucking vacuum........
My question is this:
if you exagerate this effect, say connect both extractors together end-2-end then both will be trying to suck vacuum (from the other motor).
If we bring the junction round to 90 degrees, then past to where we are in the picture then we see the effect observed. If we continue round and reduce the angle to 0 degrees using a true "Y" piece i.e. a junction where the 2 air flows join exactly parallel:
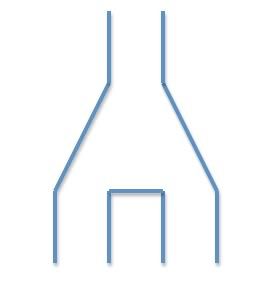
would this solve my problem?
Steve