PaulO
Established Member
Just took delivery today of 1/4 tonne of three inch beech
It is going to be turned into a whole pile of shavings and hopefully a Charlesworth style bench.
I have selected a few boards from the crown, that will be ripped into 4 inch strips and joined to make a quarter sawn top.
Tommorows job is cutting it into rough sizes and planing/thicknessing to about 4mm from final dimensions. Then it will be left in the house for a few weeks / months.
Should be fun as my handheld circular saw that I use for breaking down rough stock only has a 2.5 inch depth of cut, and the boards are currently 3.25 inches.
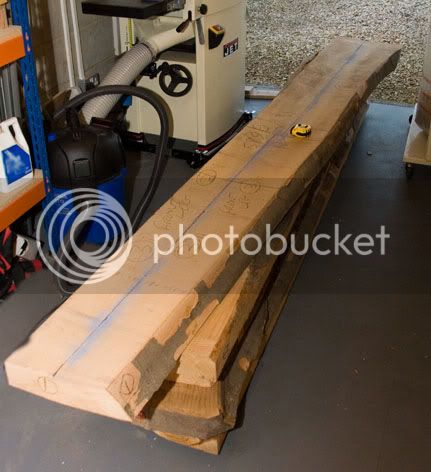
It is going to be turned into a whole pile of shavings and hopefully a Charlesworth style bench.
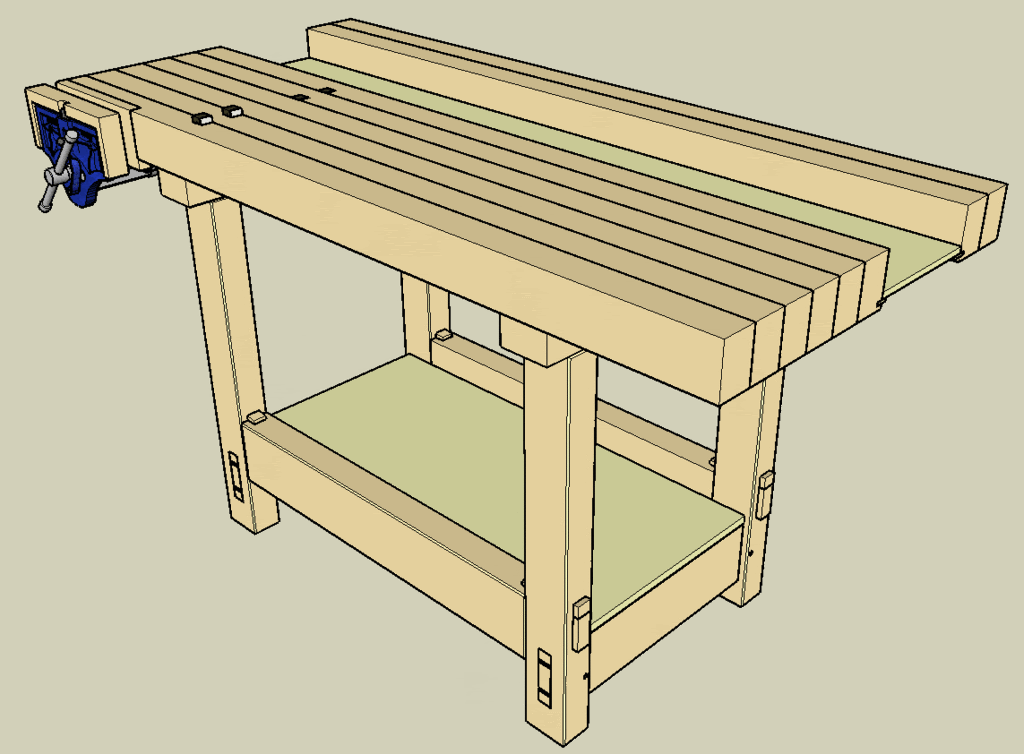
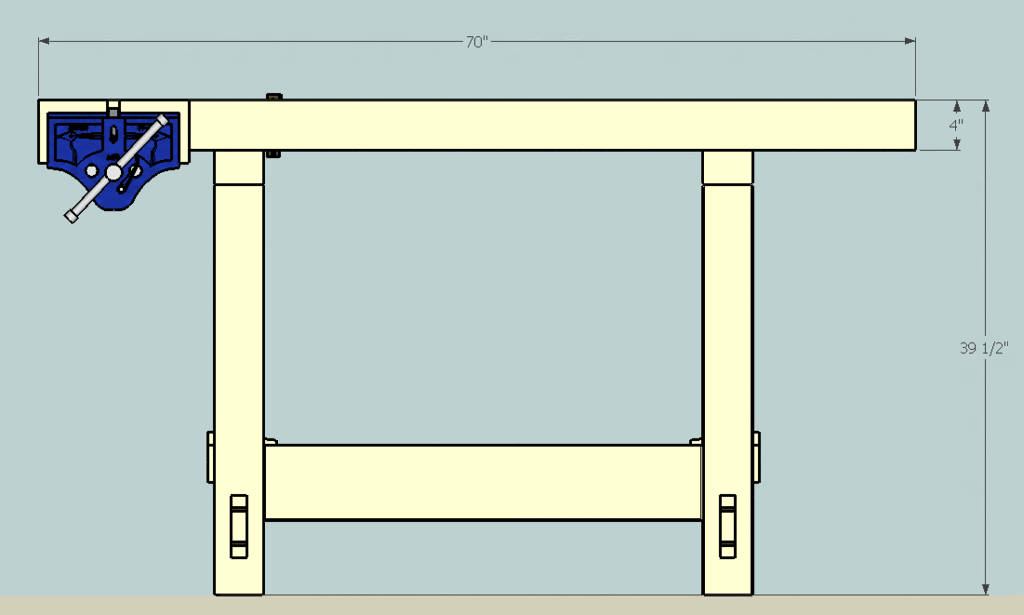
I have selected a few boards from the crown, that will be ripped into 4 inch strips and joined to make a quarter sawn top.
Tommorows job is cutting it into rough sizes and planing/thicknessing to about 4mm from final dimensions. Then it will be left in the house for a few weeks / months.
Should be fun as my handheld circular saw that I use for breaking down rough stock only has a 2.5 inch depth of cut, and the boards are currently 3.25 inches.