RobertMP
Established Member
After getting some help with the design I thought I'd better post some work in progress pictures.
The design is -
Now made out of 3/4 inch white oak veneered MDF and White oak trims and doors.
All pieces cut with a jigsaw slightly oversize and then machined to size on 3 sides. Last side may need cutting once I allow for the trim.
Until that one day when I make a router table I've mounted my nice new Triton router (from B & Q) in the el cheapo B & Q table. There is a steel plate holding the router rock solid in place. The plastic fence has been thrown and a batten clamped across instead. A 0.5mm thick piece of white sheet metal gives me a stepped fence when I need it
Table top edge cutter profile.
Sawing off the trim.
The odd bit of damage but nothing deep and plenty of good lengths
Making more trim for the vertical edges
Flat trims and some triangles for the back that I think I might need.
The top and bottom shapes and shelf blanks.
Seem to be making reasonable progress but then it is all easy stuff. No doubt the drawer and doors will take me months!
Need to experiment with joins on some offcuts. Decided against pocket holes as I'm a bit put off by all the holes. Going to try some of those flat pack fixings with pegs and cams as I quite like the idea of it coming apart for handling and I'm sitting at a desk made that way which is very strong. Glue and biscuit joins if all else fails.
The design is -
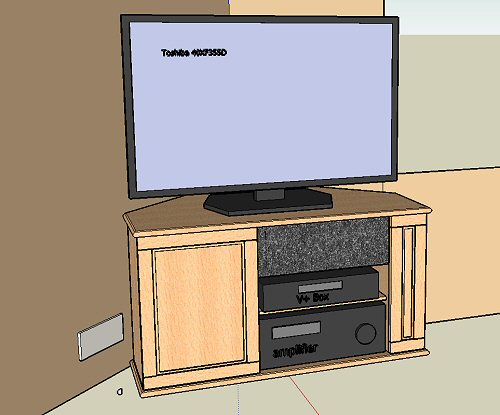
Now made out of 3/4 inch white oak veneered MDF and White oak trims and doors.
All pieces cut with a jigsaw slightly oversize and then machined to size on 3 sides. Last side may need cutting once I allow for the trim.
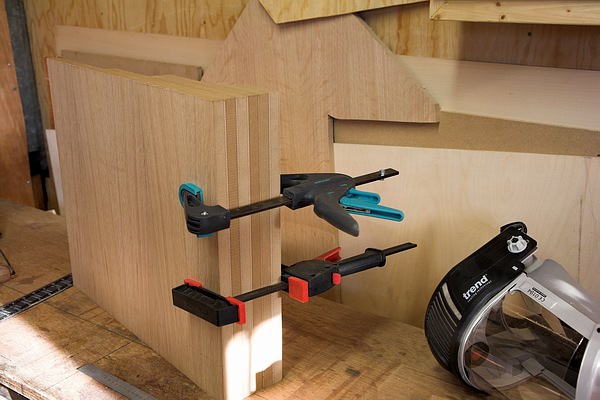
Until that one day when I make a router table I've mounted my nice new Triton router (from B & Q) in the el cheapo B & Q table. There is a steel plate holding the router rock solid in place. The plastic fence has been thrown and a batten clamped across instead. A 0.5mm thick piece of white sheet metal gives me a stepped fence when I need it
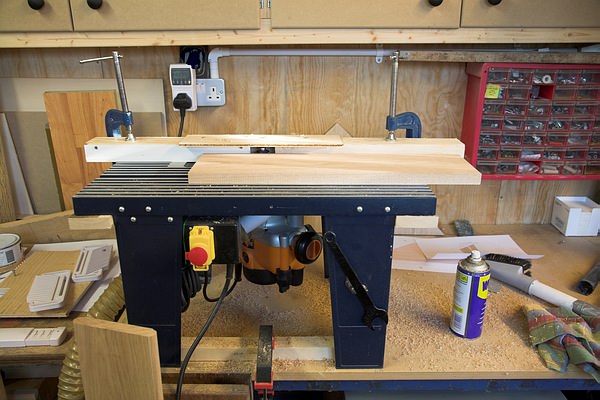
Table top edge cutter profile.
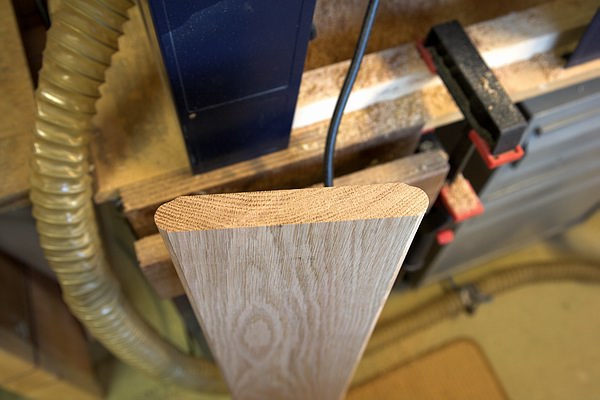
Sawing off the trim.
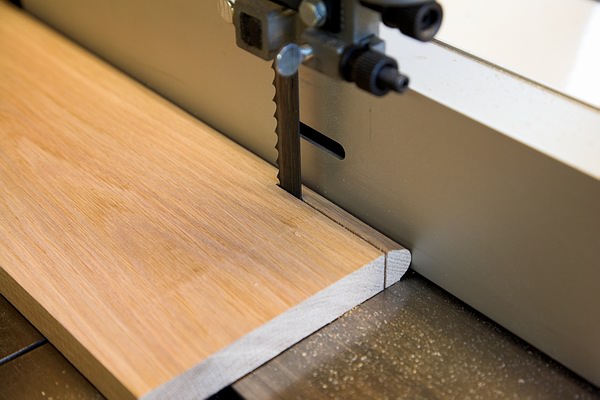
The odd bit of damage but nothing deep and plenty of good lengths
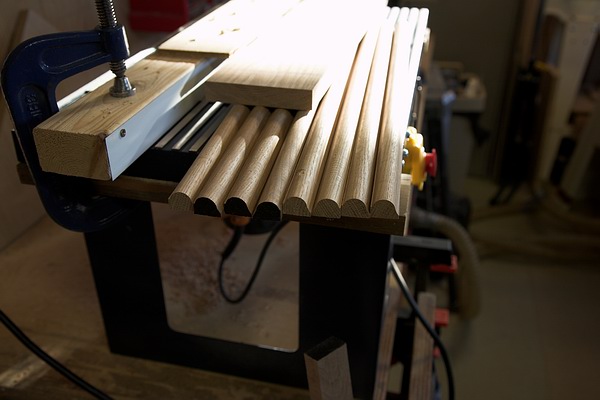
Making more trim for the vertical edges
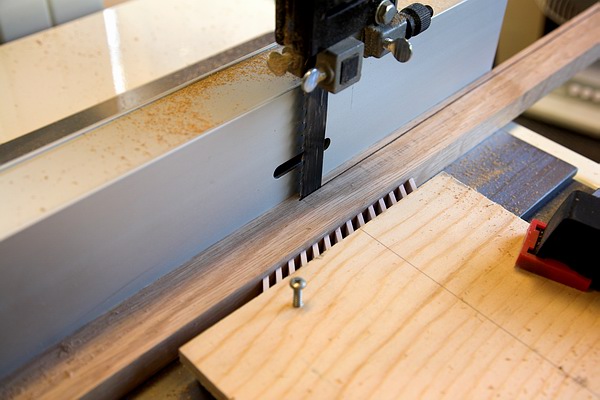
Flat trims and some triangles for the back that I think I might need.
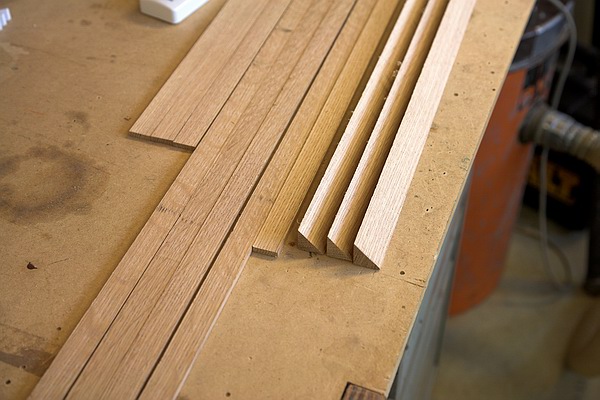
The top and bottom shapes and shelf blanks.
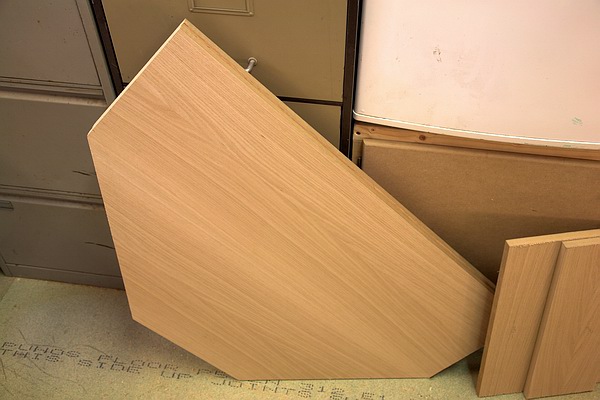
Seem to be making reasonable progress but then it is all easy stuff. No doubt the drawer and doors will take me months!
Need to experiment with joins on some offcuts. Decided against pocket holes as I'm a bit put off by all the holes. Going to try some of those flat pack fixings with pegs and cams as I quite like the idea of it coming apart for handling and I'm sitting at a desk made that way which is very strong. Glue and biscuit joins if all else fails.