tombo
Established Member
wada ya think about these dovetails, pretty nice aye?
Sadly i did not cut them, they were made by some pushy canadian who forced me into buying some lie neilsen tools :roll: you may have heard of him Rob Cosman
I have not had much experience cutting DT's but how hard can it be? RC made it look so easy I can copy his demo piece and I have this DT saw
and this is the result, dont think Rob Cosman has anything to worry about just yet :?
As you can be seen the cut left by my saw is ragged, the final photo shows a staight ripcut made by my saw compared to Rob's LN. The difference is pretty clear.
so what is the opinion? is it my technique or is it the saw?
Tom
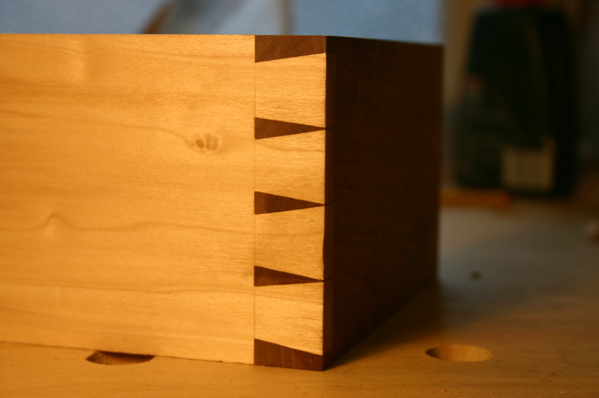
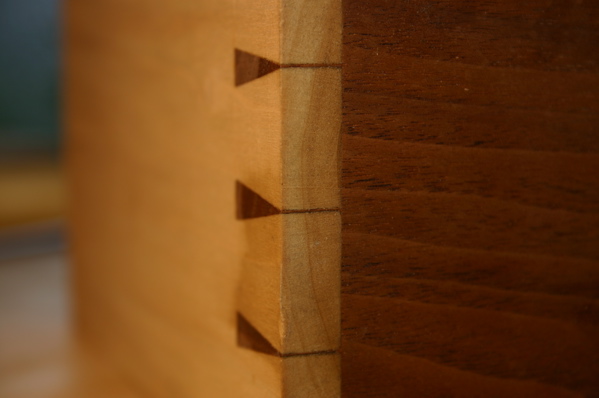
Sadly i did not cut them, they were made by some pushy canadian who forced me into buying some lie neilsen tools :roll: you may have heard of him Rob Cosman
I have not had much experience cutting DT's but how hard can it be? RC made it look so easy I can copy his demo piece and I have this DT saw
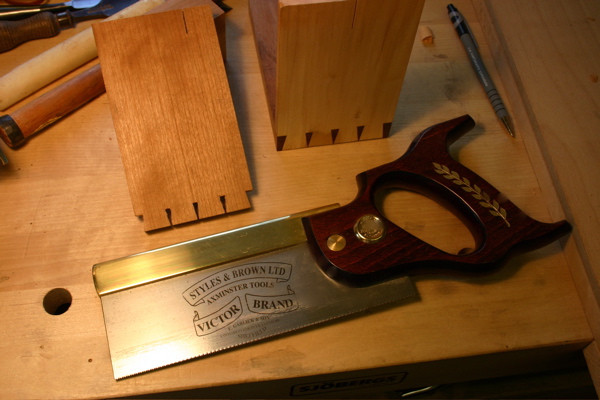
and this is the result, dont think Rob Cosman has anything to worry about just yet :?
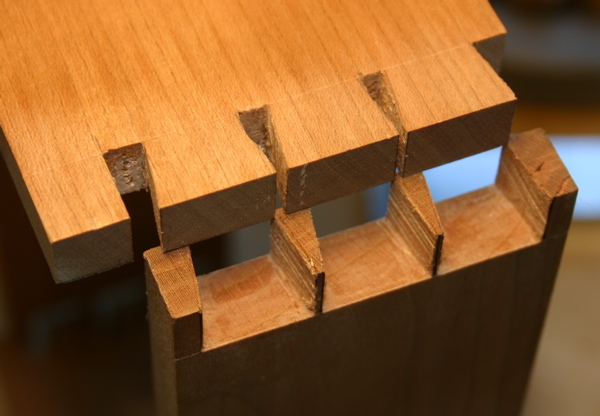
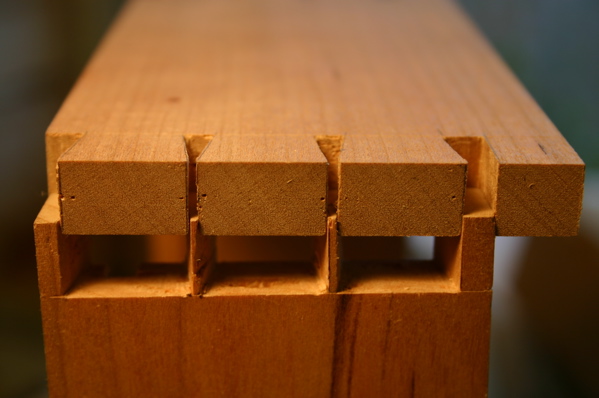
As you can be seen the cut left by my saw is ragged, the final photo shows a staight ripcut made by my saw compared to Rob's LN. The difference is pretty clear.
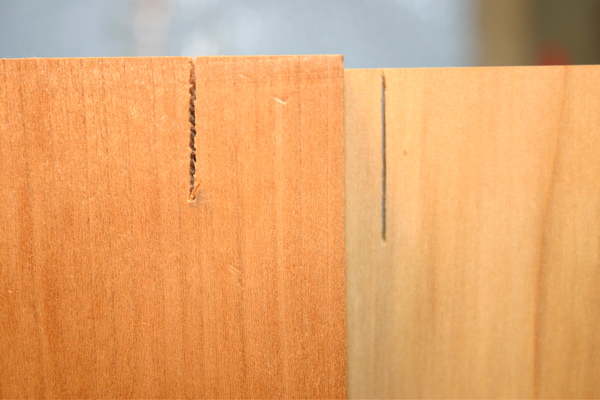
so what is the opinion? is it my technique or is it the saw?
Tom