Richard T
Established Member
When I made Jimi his panel plane shell and exaggerated the top of the cupid bow (Japanese wave style) I did so because I had already cut out the sides for this smoother in that way and couldn't bare to return to the accepted 'norm'.
It is 9 - 1/2" long (sole) and made to take a 2" iron, though it's a bit narrow for much lateral movement. 50 degree pitch.
The sides are 3mm and the sole is 6mm. It has the same size frog block as does Jim's 15 - 1/2 incher so it seems even more big and solid in this little plane.
I made a cap iron after the style (loosely) of Karl H. 3mm mild steel bend cold over the curved area of the side of the anvil. I don't think I will bother with trying to build up the female thread with brass - 3mm should be plenty thick enough.
The iron is the only true parallel I have yet found although it develops a bit of extra thickness toward the end. This I will file down instead of opening the mouth that last smidgeon.
It's by Richard Ibbotson and appears to have had its top clipped and have "L C C" stamped cold underneath the hot stamped maker's mark. Any thoughts on either of these things?
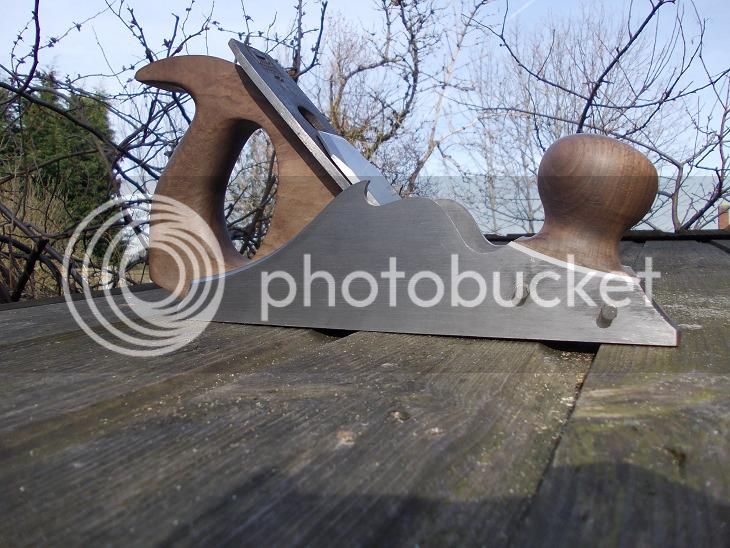
It is 9 - 1/2" long (sole) and made to take a 2" iron, though it's a bit narrow for much lateral movement. 50 degree pitch.
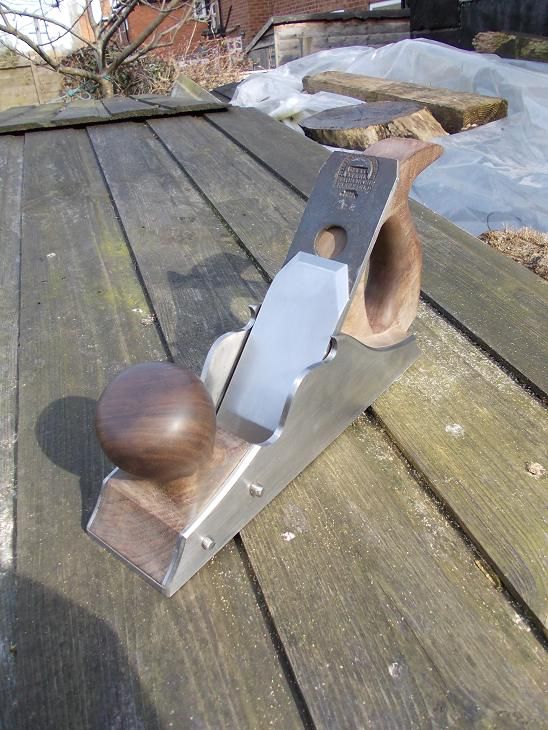
The sides are 3mm and the sole is 6mm. It has the same size frog block as does Jim's 15 - 1/2 incher so it seems even more big and solid in this little plane.
I made a cap iron after the style (loosely) of Karl H. 3mm mild steel bend cold over the curved area of the side of the anvil. I don't think I will bother with trying to build up the female thread with brass - 3mm should be plenty thick enough.
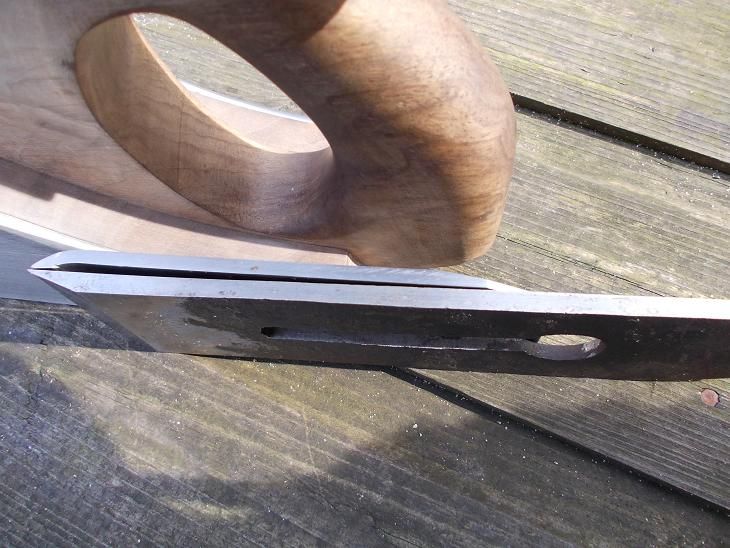
The iron is the only true parallel I have yet found although it develops a bit of extra thickness toward the end. This I will file down instead of opening the mouth that last smidgeon.
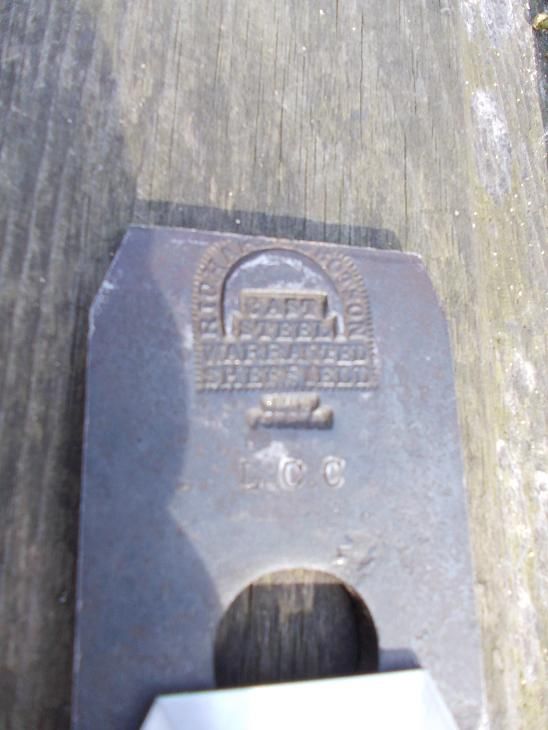
It's by Richard Ibbotson and appears to have had its top clipped and have "L C C" stamped cold underneath the hot stamped maker's mark. Any thoughts on either of these things?