I've decided to try and do something about the dx on my Xcalibur ts.
First off, some pics
Dust is currently extracted via a 4" outlet at the very bottom of the machine
You can see the cavernous area around the motor and blade for dust to fly around before being extracted.
One problem comes when swinging the cradle for angled cuts.
My initial thought was to block up the existing d/x hole and put a new 5" one right behind the blade on the back of the machine
Also find some way of blocking up all the silly gaps between the cabinet and the cast iron top (those are my fingers in the pic).
Anybody got any good ideas on how to treat the swinging cradle - I want to reduce the internal volume of the cabinet by fitting a false floor/blade shroud.
Any comments welcome.
Cheers
Karl
First off, some pics
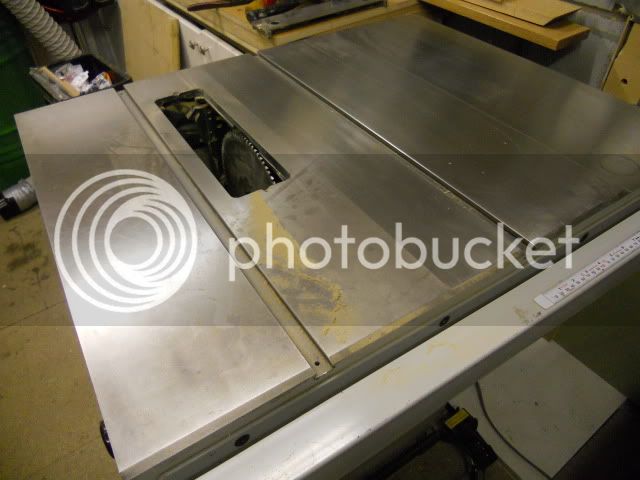
Dust is currently extracted via a 4" outlet at the very bottom of the machine
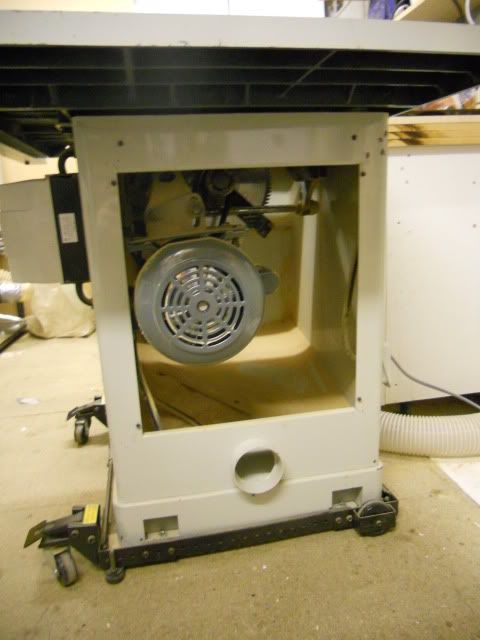
You can see the cavernous area around the motor and blade for dust to fly around before being extracted.
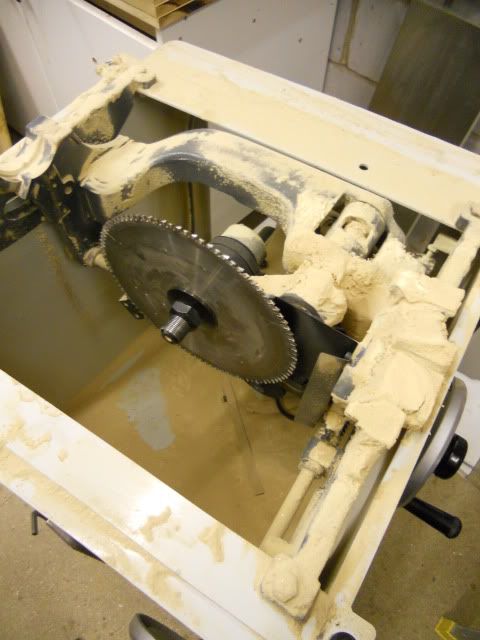
One problem comes when swinging the cradle for angled cuts.
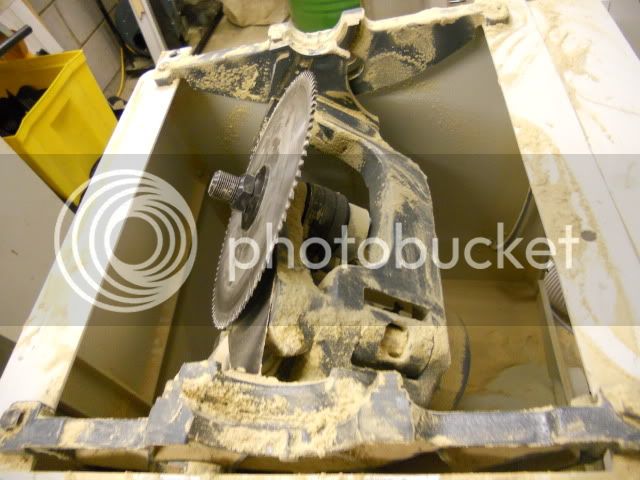
My initial thought was to block up the existing d/x hole and put a new 5" one right behind the blade on the back of the machine
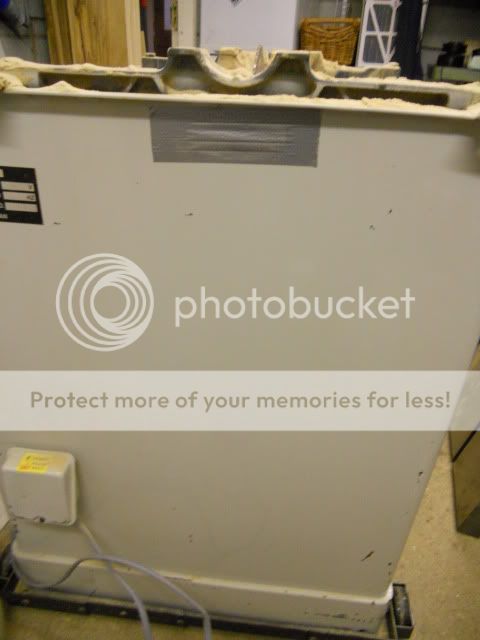
Also find some way of blocking up all the silly gaps between the cabinet and the cast iron top (those are my fingers in the pic).
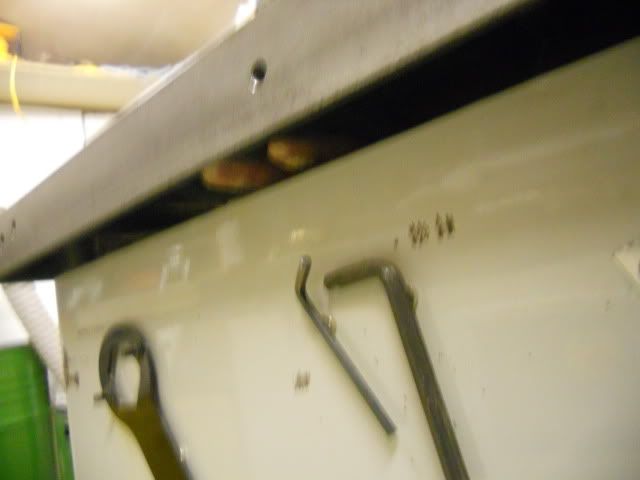
Anybody got any good ideas on how to treat the swinging cradle - I want to reduce the internal volume of the cabinet by fitting a false floor/blade shroud.
Any comments welcome.
Cheers
Karl